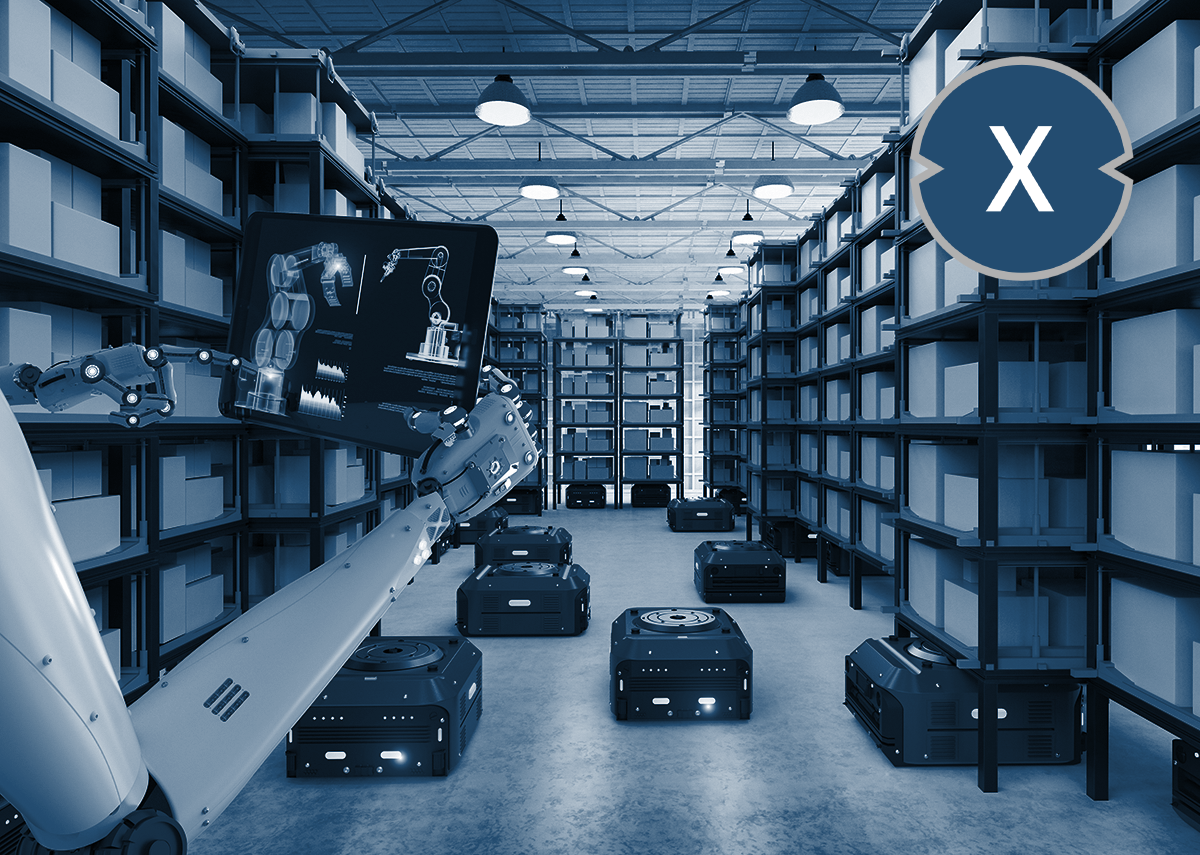
Smart Storage: Warehouse Robots – Logistik Roboter in der Fabrik bzw. im Lager – Phonlamai Photo|Shutterstock.com
Die Optimierung der eigenen Lagerlogistik gehört nicht nur im Versandhandel für die meisten Unternehmen zum Kerngeschäft – und dabei gleichzeitig meist ebenfalls zu den größten Kostenfaktoren. Aufgrund seiner Komplexität sind Verbesserungen in diesem Bereich mit die schwierigsten und oft auch kostenintensivsten Aufgaben, denen sich die Unternehmen stellen müssen. Um die Abläufe auf Effizienz zu trimmen ist eine Automatisierung des Lagers mithilfe automatischer Materialfluss- und Fördersysteme, bei denen die Waren in modernsten Regallagern untergebracht werden, eine Option.
Wie allerdings kommt die Ware von dort aus zur Pick-Station?
Oftmals werden an dieser Stelle Lagerarbeiter eingesetzt, die mit mobilen Scannern auf die Reise geschickt werden, um die Artikel für die Kommissionierung einzusammeln. Eine Lösung, die neben hohen Personalkosten Einschränkungen hinsichtlich der zeitlichen Flexibilität (Stichwort Rund-um-die-Uhr-Kommissionierung) und trotz Einsatzes modernster Scannertechnik Nachteile bei der Pickgenauigkeit nach sich zieht.
Intralogistkanbieter haben darüber hinaus Lösungen entwickelt, um die Pickraten und damit die Kommissionierungsgeschwindigkeit zu erhöhen. So setzen sie bei den Versandlogistikern auf den Einsatz horizontaler Karusselllager. Diese transportieren die benötigten Artikel direkt zum Kommissionierungsort. Durch die automatisch gesteuerte Bereitstellung der Produkte am Arbeitsplatz können sich die Mitarbeiter auf weitere Tätigkeiten, wie beispielsweise die Verpackung der Waren konzentrieren, was bereits zu einer höheren Geschwindigkeit und Genauigkeit führt. Darüber hinaus bleibt den Lagermitarbeitern der langwierige Gang zu den verstreut liegenden Waren erspart, was die Laufwege verkürzt und dazu auch die Ergonomie am Arbeitsplatz erhöht.
Selbstverständlich macht die technische Entwicklung an dieser Stelle nicht halt, sondern schreitet permanent fort. So sind bereits mehrere Systeme auf dem Markt, welche eine dynamische Lagerhaltung und Kommissionierung mithilfe autonomer Kleinroboter-Systeme ermöglichen, die die anfallenden Arbeiten ressourcenschonend übernehmen.
Kiva-Robotics – der Vorreiter
Vorreiter auf dem Gebiet ist das US-Unternehmen Kiva, welches im Jahr 2003 gegründet wurde und aufgrund seiner bahnbrechenden Neuentwicklung in der US-Logistikbranche schnell auf sich aufmerksam machte; kam ihre Version doch gänzlich ohne Förderbänder, automatisierte Hochregallager oder neuartige Transportwagen aus, sondern konzentrierte sich auf kleine, autonom agierende Roboter, welche durch das Lager rollten und an jeder Stelle Kleinregale aufnahmen, um diese zu den Packplätzen zu transportieren. Nach Entnahme der Artikel ging es für die Regale automatisch wieder zurück und der Roboter suchte sich sein nächstes Ziel.
Statt also Lagermitarbeiter samt ihren Picklisten oder mobilen Scannern loszuschicken, übernahm diese Aufgabe der kleine, orangefarbene Roboter, der mit Hilfe seiner integrierten Hebetechnik das gesamte (Klein)regal transportierte, in welchem sich die benötigte Ware befand. Anstatt den einzelnen Artikel aufzunehmen, wird einfach das gesamte Regal genommen und an die entsprechende Stelle transportiert. Somit befindet sich das Lager quasi permanent in Bewegung, während den fix an den Pickplätzen postierten Lagerarbeitern die Aufgabe zukommt, den herbeigeschafften Regalen bloß noch die benötigten Produkte zu entnehmen.
Wie überall im Zeitalter elektronisch gesteuerter Lagerlogistiksysteme liegt die Kunst in der Software des Gesamtsystems, welche die Roboter zur richtigen Zeit an den richtigen Ort lenkt. Es ist augenscheinlich kein leichtes Unterfangen, beim Einsatz von Hunderten von Robotern in Lagern, die bis zu mehreren tausend Regale fassen, den drohenden Stau zu vermeiden. Und es ist eben jene annähernd unbegrenzte Skalierbarkeit und Flexibilität, die dieses System für Anwender so interessant macht.
Neben ausreichend Strom und der Investition in die passenden Roboter und Regale sowie ebene Flächen benötigt die Kiva-Lösung kaum weitere Voraussetzungen. Im Gegenteil, fallen dafür doch zahlreiche, heutzutage beim Einsatz von Lagerarbeitern unverzichtbare Faktoren weg. So müssen die genutzten Lagerflächen nicht beleuchtet oder beheizt werden; arbeitet der Roboter doch auch bei völliger Dunkelheit und weit unterhalb jeglicher, aus arbeitsrechtlichen Gründen vorgeschriebener Temperatur. Außer zur Entnahme und Kommissionierung ist menschliche Arbeitskraft hier nicht mehr notwendig; was gleichbedeutend mit der Reduzierung der physikalischen Beschränkungen alleinig auf die Akku-Laufzeit der Roboter ist. Gesetzlich vorgeschriebene Arbeits- und Pausenzeiten sowie Faktoren wie Ermüdung oder Ablenkung fallen beim Lagervorgang kaum mehr ins Gewicht. Laut Kiva steigert das System die Produktivität der Lagermitarbeiter um das Drei- bis Vierfache.
All diese Vorteile sind sicher ein Grund dafür, dass das Kiva System bereits bei vielen der top US-Versandhändler im Einsatz ist. Für einen, den mit Abstand größten von ihnen – Amazon – war das Unternehmenskonzept derart interessant, dass es die Firma 2012, kurz nach Vorstellung der Technik auf dem deutschen Markt, erwarb.
Nach dem Kauf von Kiva hat Amazon die Produktion stark angezogen, denn allein der eigene Roboterbedarf – Schätzungsweise 18.000 Stück für die weltweiten Amazon-Lager – ist etwa dreimal höher als die Gesamtproduktion der Firma seit ihrer Gründung. Der Verkauf des Systems an interessierte Dritte wird somit zunächst zurückstehen müssen.
Und was tut sich in Deutschland?
Inzwischen gibt es auch eine Reihe deutsche Maschinenbauer, die an einer vergleichbaren Lösung arbeiten. Einer der Vorreiter ist hier die Firma Grenzebach, die mit ihrem neuentwickelten System G-Com nach eigener Aussage den Kommissionierungsaufwand um bis zu 70 Prozent reduzieren kann.
Auch die G-Com-Lösung des bayerischen Maschinenbauers basiert auf mobilen, wendigen Robotern – den sogenannten Carrys – die selbstständig durch die Lagerhalle manövrieren. Da sich die Motoren der kleinen Roboter per Induktion aufladen, können diese durchgängig operieren, wodurch Zeitverluste durch Verweildauern an den Ladestationen entfallen. Gesteuert durch die von Grenzebach entwickelte Software, fahren die Carrys zu den vorgesehenen Regalen, heben diese an und bewegen die Waren zu den ergonomisch und flexibel konfigurierbaren Pick-Stationen, an denen die Lagerarbeiter die Artikel entnehmen und für den Versand vorbereiten. Dabei sind die Regale von ihrer Aufteilung her vollkommen variabel konstruiert und können von daher Artikel unterschiedlichster Abmessungen und Gewichte lagern. Folglich eignen sie sich hervorragend für die Lagerung heterogener Produkte und für Anbieter, die mit einem breiten Sortiment operieren.
Doch die Automatisierung hat auch andere Vorteile: Müssen Lagerarbeiter bei herkömmlichen Systemen oft 15 oder gar 18 Kilometer am Tag zurücklegen, so können sie bei den Roboter-Lösungen ohne große körperliche Belastung stationär an den Pickstationen verbleiben, wodurch das Ware-zur-Person-System die Wegezeiten der Beschäftigten eklatant reduziert. Grenzebach zufolge vermindert sich die Pickzeit gegenüber herkömmlichen Lösungen um etwa 55 %. Hinzu kommen etwa 15 % der Orientierungs- und Suchzeit am Regal, was zu der Effizienzsteigerung von 70 % führt. Dadurch, dass nur noch der reine Pick- und Ablagevorgang der Artikel manuell gehandhabt wird, werden die Personalkosten signifikant reduziert. Dazu kommt, dass sich aufgrund der Vereinfachung der Abläufe die Einarbeitungszeit der Beschäftigten auf nur noch ein bis zwei Tage verringert.
Auch bei G-Com muss der Lagerbereich nicht mehr beleuchtet, belüftet oder beheizt werden. Hier muss allein der Bereich der Pickplätze den gesetzlichen Anforderungen gerecht werden; was in der Regel nur etwa 10 % des gesamten Lagerbereiches betrifft und folglich zu deutlichen Einsparungen beim Energieverbrauch führt.
Für die Steuerung der Carrys werden keine Induktionsschleifen benötigt, was die Anwendung extrem flexibel einsetzbar macht und darüber hinaus Umzüge der Lagersysteme kostengünstig und unkompliziert gestalten dürfte.
Der deutsche Anlagenbauer Eisenmann stellt Kiva und G-Com sein auf einem Doppelkufensystem operierendes, gerade mal 60 kg schweres Flurfördermittel Logimover entgegen. Ausgestattet mit einem leistungsstarken Lithium-Ionen-Batteriekonzept befördert das fahrerlose und extrem wendige Gefährt auf kleinstem Raum Lasten von bis zu einer Tonne mit einer Geschwindigkeit von einem Meter in der Sekunde und hilft so, Abläufe in der Transport- und Lagerlogistik zu optimieren. Der fahrende Roboter besteht aus zwei parallel operierenden Kufen, welche selbständig unter Norm-Paletten manövrieren, diese anheben und über ein optisches Spurführungssystem bis an ein definiertes Ziel befördern. Für die Synchronisation der beiden unabhängigen Kufen sorgt eine ausgeklügelte Software, die den gesamten Weg des Gefährts überwacht und steuert.
Laut Aussage des Unternehmens ist der Logimover für vielfältige Aufgaben in der Intralogistik, von der Materialbereitstellung für Maschinen, über die Ein- und Auslagerung von Waren jeder Art bis hin zu komplexen Kommissionieraufgaben geeignet. Das Kufen-Konzept sowie das innovative Steuerungs- und Antriebssystem des Logimovers sind inzwischen patentrechtlich in Europa geschützt.
Einen zusätzlichen Schritt ging Neobotix: Mit dem MT-400 präsentierte die Firma auf der Automatica 2014 einen weiteren autonomen mobilen Roboter, welcher als kostengünstiges, hoch flexibles Transportsystem entwickelt wurde. Dank seines kompakten Aufbaus kann sich der MT-400 auch durch sehr schmale Gänge bewegen, in denen weder Bodenmarkierungen noch andere Installationen zwecks Orientierung des Gefährts notwendig sind. Stattdessen verlässt sich das Navigationssystem auf die Informationen eines installierten Laserscanners, der es dem Roboter ermöglicht, Hindernisse selbstständig zu umfahren und auf unvorhersehbare Situationen zu reagieren.
Ein sich selbst steuernder, denkender Lagerroboter? Von hier aus erscheint der Schritt zu einer autonom agierenden Gesamtlösung, die den Einsatz des Menschen im Lager irgendwann vollkommen überflüssig macht, nicht mehr weit.
Logistik-Roboter? Wer braucht sowas?
Bei all ihren individuellen Unterschieden sind die Systeme von Kiva und den deutschen Anbietern aufgrund ihrer hohen Automatisierung und Flexibilität speziell auf die Bedürfnisse des rasant wachsenden E-Commerce- und Multi-Channel-Marktes ausgerichtet.
Dafür sprechen vor allem folgende Gründe:
Optimales Handling breiter Sortimentspaletten
Die mobilen Helfer eignen sich aufgrund ihrer flexiblen und skalierbaren Bauart in erster Linie für Lager- und Kommissionierbetriebe, die aus einem breiten Sortiment eine Vielzahl unterschiedlicher Sendungen zusammenstellen. Von daher sind sie geradezu prädestiniert für Logistiklösungen von Unternehmen des Versand- und Multi-Channel-Handels sowie Fulfillment-Dienstleister, die in der E-Commerce-Branche aktiv sind. Hier können sie ihre Effizienzvorteile ausspielen und den ständig steigenden Anforderungen der Händler an immer kürzere Auslieferungszeiten und bei dauerhaften Kostenreduzierungen gerecht werden.
Flexibler Einsatz
Mit den vorgestellten Systemen ist nahezu jeder Artikel lagerfähig, sofern er nicht die maximalen Abmessungen ihrer Chassis überschreitet. Auch können die Regale je nach Bedarf mit Wannen, Schubladen, Hängestangen etc. ausgestattet werden und passen sich auf diese Weise flexibel den Sortimentsanforderungen an. So helfen sie, die verfügbare Lagerflächen effektiver auszunutzen, da jeder Bereich als Abstellfläche für die mobilen Regale genutzt werden kann. Aufgrund ihrer geringen Ansprüche hinsichtlich technischer Installationen ist eine problemlose Integration in bestehende Lagergebäude möglich.
Schnelle Bereitstellungszeiten
Durch die sofortige Bereitstellung der Waren an der Pickstation reduziert sich Durchlaufzeit eines Auftrags auf nur noch wenige Minuten. Ein Zeitvorteil, welcher der zunehmend verlangten extrem schnelle Lieferung – Stichworte Next und Same Day-Delivery – Rechnung trägt.
Fazit
Natürlich sind dem Einsatz der kleinen Helfer – noch! – Grenzen gesetzt. So werden schnelldrehende Artikel sicher weiterhin am effizientesten auf Paletten in Griffweite der Pickstationen gelagert werden. Auch die Bedienung hochmoderner Lagerliftsysteme, von Hoch- und Karussellregalen oder der Transport sehr schwerer oder großvolumiger Waren kann von Kiva & Co. vorerst nicht übernommen werden. So werden sich auf mittlere Sicht vor allem Mischlösungen anbieten, bei denen die unterschiedlichen Systeme nebeneinander und sich gegenseitig ergänzend betrieben werden. Doch bereits jetzt können die Geräte einen großen Beitrag dazu leisten, die Effizienz der Lagerlogistik bedeutend zu steigern.