Automatic pallet shuttle system (PSS) for fully automatic pallet warehouse shuttle rack storage system (SRL)
Language selection 📢
Published on: July 3, 2023 / update from: July 4, 2023 - Author: Konrad Wolfenstein
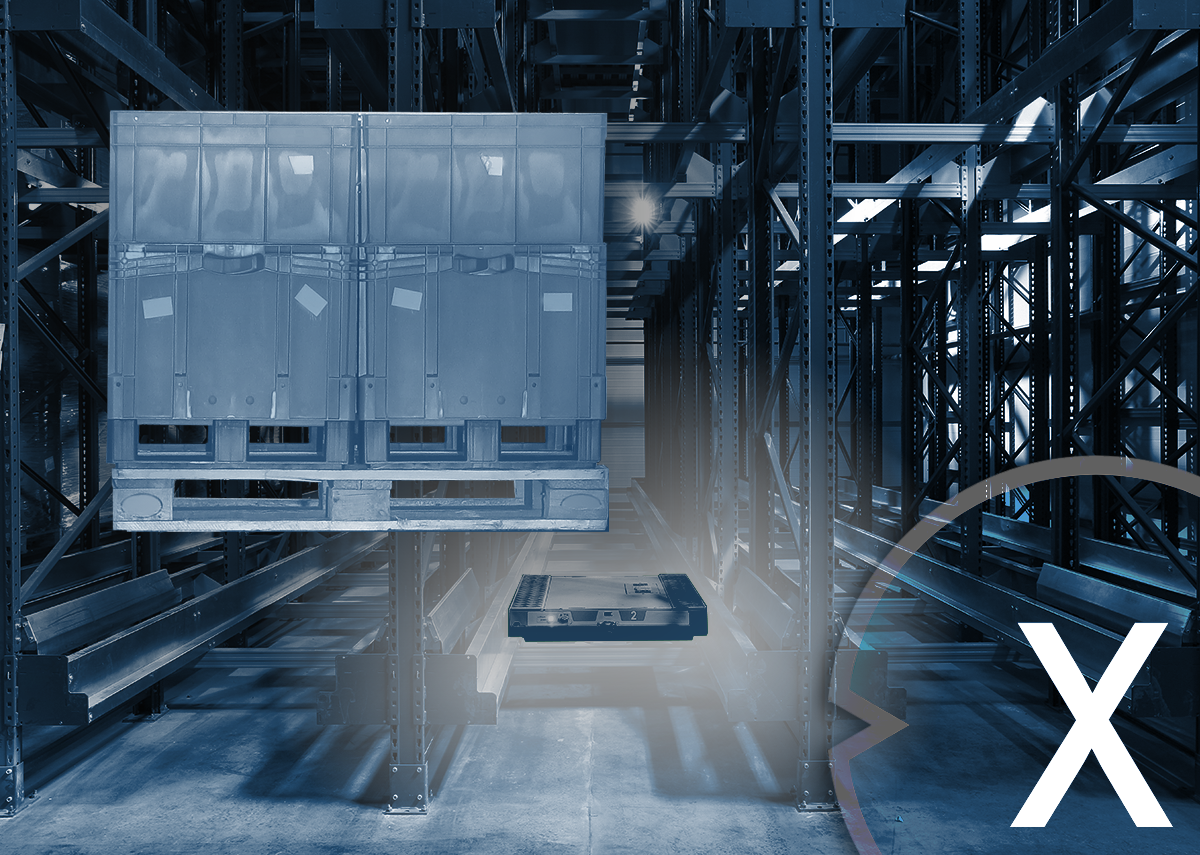
Automatic pallet shuttle system for fully automatic pallet warehouse shelf storage system - Image: Xpert.Digital
Efficient and innovative automatic pallet shuttle system for fully automatic pallet warehouse racking system
An automatic pallet shuttle system is an efficient solution for storing pallets in a fully automated pallet storage racking system. This state-of-the-art system revolutionizes the way pallets are stored and transported.
The automatic pallet shuttle system consists of specially developed shuttles that operate independently in the rack aisles. These shuttles are able to transport pallets horizontally and place them in the designated shelves. They work in closely coordinated interaction with a warehouse management system (LVS), which controls and monitors the shuttles.
The shuttles are equipped with sensors that allow them to detect the position of the pallets and move them precisely to the desired shelf position. This ensures optimal use of space and maximum storage capacity. In addition, the shuttles can transport the pallets at a high speed, which leads to efficient storage and retrieval.
Another big advantage of the automatic pallet shuttle system is its flexibility. It can be integrated into existing storage systems and is scalable to meet the needs of different warehouse sizes and types. The system also enables high throughput because several shuttles can work in the rack aisles at the same time.
The automatic pallet shuttle system also offers significant benefits in terms of worker safety. Because the pallets are stored and transported automatically, the need for employees to manually move heavy loads is eliminated. This reduces the risk of injury and improves health and safety in the workplace.
In addition, the automatic pallet shuttle system enables improved warehouse management and control. The LVS ensures precise inventory tracking and enables quick and accurate identification of pallets. This allows inventory to be managed more efficiently, inventory overstocks or bottlenecks to be avoided, and inventory control to be optimized.
Another interesting detail of the automatic pallet shuttle system is its energy efficiency. The shuttles are equipped with powerful batteries that enable long operating times. The shuttles can also recover kinetic energy when braking and descending and feed it into the batteries. This leads to a reduction in energy consumption and contributes to sustainability.
➡️ The automatic pallet shuttle system is a state-of-the-art and efficient storage system that optimizes the storage and transport of pallets. With its numerous advantages, such as high throughput, flexibility, occupational safety, improved warehouse management and -
control as well as energy efficiency, it is an ideal solution for companies that want to automate and optimize their warehouse processes.
The difference between an Automatic Pallet Shuttle System (PSS) and an Automated Guided Vehicle (AGV)
An automated pallet shuttle system (PSS) and an automated guided vehicle (AGV) are two different solutions for automating warehouse and logistics processes. Although they share similar goals, there are some important differences between the two systems.
An automatic pallet shuttle system (PSS) is specifically designed for the efficient storage of pallets in a fully automated pallet storage racking system. It consists of shuttles that operate independently in the rack aisles and transport pallets horizontally. The shuttles are controlled and monitored by a warehouse management system (LVS). They are designed to work in a closely coordinated interaction and to ensure optimal use of space. The PSS offers high throughput performance, flexibility and improved warehouse management and control.
On the other hand, Automated Guided Vehicles (AGVs) are autonomous vehicles used to transport goods and materials in warehouse and production environments. AGVs can transport both pallets and other forms of load carriers. Unlike the PSS, AGVs move on the ground and can cover different routes and areas. They are equipped with sensors and navigation devices to avoid obstacles and carry out their tasks efficiently. AGVs tend to be more versatile and can be used in different areas of a business.
An important difference between PSS and AGV lies in their application. The automatic pallet shuttle system specifically focuses on the efficient storage of pallets in racking systems. It optimizes space, increases throughput and improves inventory control. AGVs, on the other hand, are more flexible and can be used for different transport tasks in different areas of a company. They can support the flow of materials in warehouses, production lines or even in the shipping area.
Another difference lies in the way the two systems work. The automatic pallet shuttle system is designed for the specific rack structures and uses specialized shuttles to transport the pallets horizontally. AGVs, on the other hand, move freely on the ground and can adapt to different environments and tasks. They can be equipped with different grippers or modules to handle different types of load carriers.
➡️ Both the automatic pallet shuttle system and AGVs offer advantages in terms of efficiency, worker safety and automation. The choice between the two systems depends on the specific requirements and circumstances of a company. When efficient pallet storage is required in an automated racking system, the PSS is the optimal choice. On the other hand, when flexible transport is required in different areas of the operation, AGVs offer a versatile solution.
The difference between an automatic pallet shuttle system (PSS) and an automated guided vehicle system (AGV)
High-bay warehouses with driverless transport systems (AGVs) are widespread – Image: Xpert.Digital / vanitjan|Shutterstock.com
An automatic pallet shuttle system (PSS) and an automated guided vehicle system (AGV) are two different approaches to automating warehouse and logistics processes. Although they share similar goals, there are some important differences between the two systems.
An automatic pallet shuttle system (PSS) is specifically designed for the efficient storage of pallets in a fully automated pallet storage racking system. It consists of specially developed shuttles that operate independently in the rack aisles and transport the pallets horizontally. The PSS works in close coordination with a warehouse management system (LVS), which controls and monitors the shuttles. These shuttles are designed to ensure optimal space utilization and maximize storage capacity. The PSS offers high throughput performance, flexibility and improved warehouse management and control.
On the other hand, driverless transport systems (AGVs) are mobile platforms that can transport goods and materials autonomously and without human interaction. Unlike PSS, AGVs move on the ground and can be used over a wider range, both within warehouses and in production or shipping areas. AGVs are equipped with sensors, navigation devices and intelligent controls to avoid obstacles and navigate efficiently. They can transport pallets, containers or other load carriers and can also be equipped with lifting devices or grippers to handle the load.
An important difference between the PSS and FTS lies in their application and flexibility. The automatic pallet shuttle system focuses on the efficient storage and transport of pallets in racking systems. It is specifically optimized for this environment and offers high capacity and throughput. AGVs, on the other hand, can be used in different areas of a company and are more flexible. They can handle different load carriers and perform various tasks such as transporting goods between production lines, storing and retrieving warehouses or shipping products.
Another difference lies in the type of transport. The automatic pallet shuttle system moves on fixed rails or guide rails in the rack aisles and is specialized in the horizontal transport of pallets. AGVs, on the other hand, move freely on the ground and can take different routes to meet the needs of the operation. They can avoid obstacles and adapt to the conditions of the environment.
➡️ The automatic pallet shuttle system and AGVs offer advantages in terms of efficiency, work safety and automation. The choice between the two systems depends on the specific requirements and circumstances of a company. When efficient pallet storage and transport is required in an automated racking system, the PSS is the optimal choice. However, if flexible transport is necessary in different areas of the company, AGVs offer a versatile solution.
The difference between an automated guided vehicle (AGV) and an automated guided vehicle (AGV)
A driverless transport system (AGV) and an Automated Guided Vehicle (AGV) are two different solutions for automating transport and logistics processes. Although they share similar goals, there are some important differences between the two systems.
A driverless transport system (AGV) is an autonomous mobile platform that can transport goods and materials without human interaction. It consists of vehicles equipped with sensors, navigation devices and intelligent control. AGVs can be used in a wide range of applications, from production to warehouse to shipping. You can transport different load carriers, such as pallets, containers or other means of transport. AGVs are designed to avoid obstacles and navigate efficiently to complete their tasks autonomously.
On the other hand, Automated Guided Vehicles (AGVs) are also autonomous vehicles used to transport goods and materials. AGVs can transport various forms of load carriers, including pallets, containers or rolls. Like AGVs, AGVs are also equipped with sensors, navigation devices and intelligent controls. You can recognize obstacles and carry out routine tasks autonomously.
An important difference between AGVs and AGVs lies in their application and flexibility. AGVs can be used in various areas of a company, such as production, warehouse or shipping. They are more versatile and can fulfill different transport tasks. AGVs, on the other hand, are often tailored to specific applications or tasks. They are often used in a specific area or for a specific task, such as moving pallets in a warehouse or moving goods on a production line.
Another difference lies in the type of transport. AGVs usually move on wheels and can travel in all directions. You can take turns and navigate tight spaces. AGVs, on the other hand, can have different types of propulsion, such as wheels, tracks or even tracks. The choice of drive type depends on the specific application and environment in which the AGV will be used.
Both AGVs and AGVs offer advantages in terms of efficiency, automation and worker safety. The choice between the two systems depends on the specific requirements and circumstances of a company. AGVs can be used more flexibly and can fulfill different tasks in different areas. AGVs, on the other hand, are often more specialized and are well suited to specific applications or tasks that require high accuracy or specialized vehicle design.
➡️ AGVs and AGVs are innovative technologies that help companies automate and optimize their transport and logistics processes. Depending on a company's individual needs and goals, both AGVs and AGVs can be a valuable addition.
Isn't an AGV and an AGV the same thing?
In fact, the terms “automated guided vehicles” (AGV) and “driverless transport system” (FTS) are often used synonymously and can mean the same in practice. There is no uniform definition or clear distinction between the two terms. Both refer to autonomous vehicles that are used for the transport of goods and materials without human interaction.
The use of the terms AGV and AGV may vary depending on the context and industry. Some companies use the term AGV to describe autonomous vehicles that perform specific tasks or applications in a limited area, such as transporting pallets in a warehouse. Other companies use the term AGVs to describe autonomous vehicles that can be used in a broader area and can transport different load carriers.
It is important to note that the distinction between AGV and AGV is more semantic than functional. Both types of vehicles are based on similar technology and have the common goal of automating and optimizing transportation.
In practice, the terms AGV and FTS may be used interchangeably and do not really differ from each other. The exact definition and application depends on the individual interpretation of the company or industry. For specific projects or requirements, it is advisable to consider the specific features and functions of an autonomous vehicle, regardless of the name used.
Fully automatic pallet warehouse shuttle rack storage system (SRL)
A fully automated pallet warehouse shuttle rack storage system (SRL) is an innovative solution for the efficient storage and management of pallets in large warehouses or distribution centers. It combines state-of-the-art technology with intelligent design to ensure optimal space utilization, fast access times and high throughput performance.
The SRL consists of special shelves arranged vertically, providing multiple levels for storing pallets. Each shelf is equipped with shuttles that operate autonomously in the shelf aisles. These shuttles move horizontally along the rows of racks and allow the pallets to be transported to the desired positions. You can pick up and place pallets and navigate between the different levels of the racking system.
A central control system, often integrated with a warehouse management system (LVS), monitors and controls the activities of the shuttles in the SRL. It optimizes the use of storage space, plans the routes of the shuttles and manages the storage and retrieval process of the pallets. The control system can also support inventory management, pallet movement tracking, and report generation.
One of the outstanding features of the SRL is the high efficiency it offers. By storing pallets vertically and using the entire height of the warehouse, companies can significantly increase their storage capacity. The SRL also allows for quick and precise access to the pallets as the shuttles are specifically designed for quick storage and retrieval cycles. This leads to reduced lead times and an increase in overall warehouse performance.
In addition, the SRL offers improved safety and workplace safety. Because the shuttles operate autonomously, there is no need for manual forklifts or other equipment, reducing the risk of accidents or collisions. The shuttles are equipped with sensors and safety devices to detect obstacles and navigate safely.
Another advantage of the SRL is flexibility. It can be adapted to the specific needs of a company, both in terms of storage capacity and the type of pallets. The SRL can handle various pallet sizes and weights and can be expanded or reconfigured as needed.
➡️ The fully automatic pallet warehouse shuttle shelf storage system is an efficient, flexible and safe solution for storing and managing pallets. Companies that have a high storage volume and want to optimize their storage capacity can benefit from the advantages of the SRL. It enables smooth handling of warehouse processes, reduces labor costs and improves warehouse productivity. As automation technologies continue to develop, the SRL is becoming an increasingly popular choice for companies looking to improve their warehousing and logistics processes.
Xpert.Plus warehouse optimization - high-bay warehouses such as pallet warehouses consulting and planning
Xpert.plus-logistics advice and logistics optimization-industry expert, here with its own 'Xpert.digital Industrie-Hub' of over 1,000 specialist contributions
Xpert.Plus is a project from Xpert.Digital. We have many years of experience in supporting and advising on storage solutions and in warehouse optimization, which we bundle in a large network under Xpert.Plus.
I would be happy to serve as your personal advisor.
You can contact me by filling out the contact form below or simply call me on +49 89 89 674 804 (Munich) .
I'm looking forward to our joint project.
Xpert.Digital – Konrad Wolfenstein
Xpert.Digital is a hub for industry with a focus on digitalization, mechanical engineering, logistics/intralogistics and photovoltaics.
With our 360° business development solution, we support well-known companies from new business to after sales.
Market intelligence, smarketing, marketing automation, content development, PR, mail campaigns, personalized social media and lead nurturing are part of our digital tools.
You can find out more at: www.xpert.digital – www.xpert.solar – www.xpert.plus