Siemens Lighthouse Factory of Digital Transformation – A guide in the era of intelligent manufacturing
Xpert pre-release
Language selection 📢
Published on: January 9, 2025 / Update from: January 9, 2025 - Author: Konrad Wolfenstein
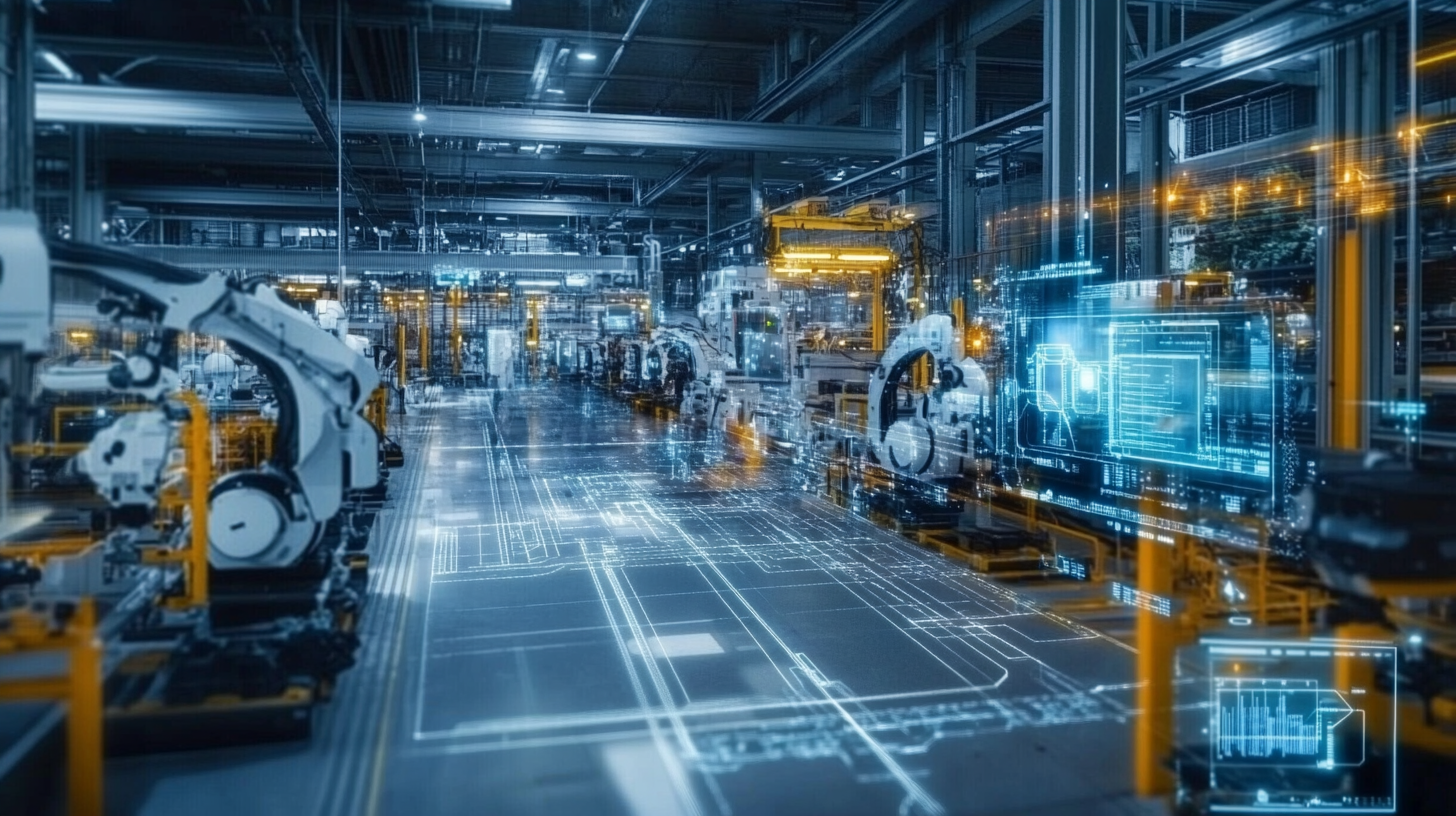
Siemens Lighthouse Factory of Digital Transformation – A Guide in the Era of Intelligent Manufacturing – Creative Image: Xpert.Digital
Siemens equipment factory in Erlangen: A beacon of digital transformation
The Siemens equipment factory in Erlangen (GWE) is an example of the modern industrial revolution. As a pioneer in the application of digital technologies in manufacturing, the factory combines innovative concepts such as digital twins, artificial intelligence (AI) and automation with advanced IT technologies. The goal is to seamlessly connect the physical and digital worlds to significantly increase both productivity and sustainability.
The GWE as a “digital lighthouse factory”
A “lighthouse factory” is a production facility that uses pioneering technologies of the fourth industrial revolution (Industry 4.0) and has an exemplary character for other companies. The Siemens device work has earned this status through the strategic use of digital technologies and demonstrates impressively how digitization can be used to improve efficiency, sustainability and operational excellence.
The integration of digital twin technology is an essential part of the digital transformation in GWE. Digital twins provide a virtual representation of physical objects, processes or systems, enabling continuous monitoring and optimization. They provide data that can be used to make informed decisions. For example, maintenance cycles can be better predicted, production processes can be simulated and operating costs can be reduced.
In the context of the industrial metaverse, the GWE merges physical and digital reality. This not only allows for a profound optimization of work processes, but also helps reduce energy consumption and waste. For example, possible bottlenecks and problems can be identified and resolved at an early stage using simulations in virtual space. This reduces the need for real resources and the entire manufacturing process becomes more sustainable.
Suitable for:
The advantages of digital transformation in GWE
The Siemens equipment plant in Erlangen benefits from digitalization in many ways. The most important advantages include:
- Increase in efficiency and productivity: Through the use of automation technologies and optimized processes, production times can be shortened and resources can be used more efficiently.
- Informed decision-making: Data from sensors and connected production systems enable informed decisions to be made based on real-time data.
- Sustainability: Through optimized use of energy and reduced waste production, the plant contributes to achieving environmental goals.
- Flexibility and agility: Digital technologies make it possible to react more quickly to changes in market demand or customer requests.
- Improved customer experience: Customization and personalized products increase customer satisfaction.
- Better data analysis: By using modern analysis tools, valuable insights can be gained that influence both production and business strategy.
- Optimized collaboration: Digital platforms facilitate communication and coordination between different departments and locations.
- Cost efficiency: Automated processes and reduced error rates lead to a reduction in operating costs.
How the GWE uses technologies
A look at the specific applications shows how the Siemens equipment plant in Erlangen successfully integrates digital technologies:
- Digital twins: In GWE, digital twins are used to simulate and optimize production processes. For example, simulations of production lines can highlight bottlenecks and provide suggestions for improvement. This saves time and costs and increases productivity.
- Artificial Intelligence: AI-based algorithms analyze massive amounts of data to detect anomalies in real-time and initiate proactive maintenance actions. This maximizes machine availability and minimizes production downtimes.
- Industrial Metaverse: By creating a digital image of the entire plant in the industrial metaverse, various scenarios can be played out and optimized before physical resources are deployed. This enables an enormous increase in efficiency and conservation of resources.
Examples from other industries
Other companies are also using technologies such as digital twins, AI and the industrial metaverse to improve their production processes:
- BMW: The company has created a digital image of its production facilities to simulate processes and increase efficiency. Before building new factories, they are virtually “pre -constructed” in order to identify and remedy potential problems.
- A Chinese electronics manufacturer: AI-driven automation reduced energy consumption per unit of production by 24% and reduced production waste by 50%.
- Siemens gas turbine production: Digital twins are used here to simulate and optimize the performance and service life of turbines. This improves efficiency and reduces operating costs.
Suitable for:
Future visions for the GWE
Digital transformation is not a one-time project, but a continuous process. The Siemens equipment plant in Erlangen is expected to continue to play a pioneering role by evaluating and integrating new technologies. Developments in the areas of:
- 5G networks: These enable highly networked production with extremely low latency.
- Robotics and automation: Advanced robots could be used even more flexibly in the future to handle complex tasks.
- Sustainability technologies: Technologies such as CO2 optimization through digital twins could be further developed to further reduce the ecological footprint.
- Quantum computing: In the future, quantum computing could help solve extremely complex optimization problems in manufacturing.
The possibilities of digital transformation
The Siemens device plant Erlangen is an impressive example of the possibilities of digital transformation. With the integration of innovative technologies such as digital twins, AI and the industrial meta person, the work shows how companies can become more sustainable, more efficient and flexible. As a “digital lighthouse factory”, the GWE sets standards for Industry 4.0 and inspires other companies worldwide.
The continuous development and integration of new technologies will help to consolidate GWE's position as an innovation leader while at the same time making an important contribution to sustainable industrial production. In a rapidly changing world, the Siemens equipment plant in Erlangen remains a beacon of innovation, showing how digitalization and sustainability can successfully go hand in hand.
🗒️ Xpert.Digital: A pioneer in the field of extended and augmented reality
Find the right Metaverse agency and planning office such as a consulting firm - Image: Xpert.Digital
🗒️ Find the right Metaverse agency and planning office such as a consulting firm - search and search for top ten tips for consulting & planning
In the age of digitalization, where technologies such as Extended Reality (XR) and the Metaverse are constantly becoming more relevant, Xpert.Digital positions itself as an opinion leader and pioneer. With over 1,500 specialist articles, Xpert.Digital has established itself as a central point of contact for the industry.
🌌 Extended Reality (XR): The best of both worlds
Extended Reality is a collective term that includes virtual reality (VR), mixed reality (MR) and augmented reality (AR). Xpert.Digital is committed to creating immersive XR experiences that are both informative and entertaining.
- Interactive Experiences: XR allows users to immerse themselves in virtual worlds and interact with their surroundings in ways previously unimaginable.
- Education and Training: XR can be used for educational purposes to convey complex topics and concepts in an understandable and tangible way.
- Entertainment: Whether games, films or art – XR opens new horizons in digital entertainment.
🔮 Augmented Reality (AR): See the world through digital eyes
Augmented Reality, a particular focus of Xpert.Digital, makes it possible to integrate digital information or graphics into the real world. The possibilities are nearly unlimited.
- Marketing and Advertising: AR can be used to create interactive advertising campaigns that engage customers in a whole new way.
- Everyday help: From navigation apps that project the route directly onto the street to furniture apps that show what a new sofa would look like in the living room - AR makes it possible.
🌐 The Metaverse: The Next Big Thing
The Metaverse is a virtual world where people can interact through avatars and create shared experiences. Xpert.Digital recognizes the enormous potential of the Metaverse and is working to translate this potential into usable products and services.
- Social Interaction: The Metaverse offers the opportunity to connect with people from all over the world and share common experiences.
- Economy and trade: Virtual goods and services can be traded in the metaverse, which opens up completely new business models and sources of income.
- Creative Freedom: From building your own worlds to designing custom avatars, the Metaverse is a place of endless creative possibilities.
🚀 Xpert.Digital at the forefront of innovation
Xpert.Digital shows how a company can be at the forefront of the technological revolution. With their focus on XR, AR and the Metaverse, they are well positioned to shape and define the future of digital interaction.
More about it here:
Artificial intelligence and digital twins: This is how Siemens is building the intelligent factory of tomorrow
Industrial Revolution 4.0: How the Siemens equipment factory unites digital and physical worlds
The Siemens Gerätewerk Erlangen (GWE) is at the forefront of an industrial revolution in which the boundaries between the physical and digital worlds are increasingly blurring. Driven by the vision of a fully connected and intelligent factory, the GWE integrates advanced technologies such as digital twins, artificial intelligence (AI) and the industrial metaverse to usher in a new era of manufacturing. This integration is not an end in itself, but a strategic step to create sustainable added value, raise productivity to a new level and at the same time assume ecological responsibility.
The GWE has established itself as a so-called “lighthouse factory”. This term describes production facilities that are at the forefront of implementing technologies from the fourth industrial revolution – also known as Industry 4.0. Such factories serve as an inspiration and blueprint for other companies by demonstrating how digital technologies can be successfully deployed at scale. The focus is on achieving measurable improvements in financial, operational and environmental terms. The GWE ideally embodies this concept by actively driving digital transformation in the manufacturing industry through the use of innovative technologies and demonstrating the concrete advantages of these technologies in practice. By acting as a role model, the GWE encourages other manufacturers to recognize and use the potential of Industry 4.0.
A central component of the digital transformation at GWE is the seamless integration of digital twin technology with advanced data analysis processes. Continuously collecting and analyzing data from a variety of sources - including manufacturing assets, smart sensors and IoT devices - creates a foundation for more informed and accurate decisions. Digital twins form the foundation of this data-driven decision-making. They are essentially virtual replicas of the physical factory, replicating all relevant elements and processes in a dynamic, digital environment. These virtual representations make it possible to simulate complex scenarios, detect potential problems at an early stage and identify optimization potential without having to intervene in ongoing operations.
The Industrial Metaverse, another cornerstone of GWE's digital strategy, represents a fusion of the real and digital worlds that goes far beyond traditional visualizations. In this immersive environment, employees, engineers and managers can interact in real time, collaborate on projects and experience complex production processes in a three-dimensional, interactive environment. This merger opens up completely new possibilities for process optimization, more efficient use of resources and reduction of environmental impact. For example, production processes can be simulated and analyzed in the Metaverse to identify bottlenecks, optimize material flows and improve the arrangement of machines and workstations. Early detection and resolution of potential problems in the virtual world leads to fewer production downtimes, reduces material consumption and lowers energy requirements.
The diverse advantages of digital transformation in GWE
The consistent implementation of digital transformation in GWE generates a variety of significant benefits that have a positive impact on various aspects of operations:
Increase efficiency and productivity
By automating repetitive tasks and optimizing complex processes, significant efficiency gains can be achieved and overall productivity increased. Intelligent algorithms and networked systems enable more precise planning and control of production, shortening throughput times and minimizing idle time.
More informed decision making
The ability to collect, analyze and visualize large amounts of data from multiple sources in real-time enables leaders to make data-driven decisions based on facts rather than guesswork. This leads to greater accuracy in strategic and operational decisions.
Sustainability as an integral component
Digital transformation enables detailed monitoring and optimization of energy consumption and resource use. By reducing waste, optimizing material flows and using energy-efficient technologies, GWE makes an important contribution to environmental protection and resource conservation.
Increased flexibility and agility
In a rapidly changing market environment, the ability to quickly adapt to new requirements is crucial. Digital technologies enable GWE to react more flexibly to changing customer needs, new product variants or unforeseen events in the supply chain. Production can be quickly changed and adjusted if necessary.
Improved customer experience through customization
By using digital technologies, GWE is able to personalize products and services more closely and tailor them to the individual needs of customers. This ranges from configuring products according to customer requirements to tailor-made service offerings.
Deeper data analysis and valuable insights: Modern digital technologies enable the collection and analysis of vast amounts of data that would remain unused in traditional environments. By using big data analysis and machine learning algorithms, valuable insights into production processes, customer behavior and market trends can be gained, which serve as the basis for continuous improvements.
Optimized collaboration and communication
Digital tools and platforms facilitate collaboration and communication between employees, teams and even across company boundaries. Real-time information and transparent communication channels help break down silos and promote more effective collaboration.
Increased cost efficiency
Significant cost savings can be achieved by automating processes, reducing errors and scrap, optimizing energy consumption and using resources more efficiently. Predictive maintenance enabled by digital technologies also helps reduce costs by reducing unplanned downtime.
The diverse advantages of digital transformation make a significant contribution to securing GWE's long-term competitiveness and preparing the company for the challenges and opportunities of the future. In a dynamically evolving industrial landscape, these improvements enable GWE to remain agile, drive innovation and achieve sustainable growth.
Concrete application examples of digital technologies in similar production environments
Although the information provided does not provide detailed insights into the specific applications of digital twins, AI and the industrial metaverse in GWE, examples from other companies can clearly illustrate the diverse possibilities of these technologies in an industrial context:
Digital twins in practice
Siemens itself is making extensive use of the potential of digital twins in various areas. In product development, digital twins enable virtual testing and optimization of new products before a physical prototype is built. In manufacturing, digital twins are used to simulate production processes to identify bottlenecks and increase efficiency. Additionally, digital twins are used to monitor performance of products and systems in the field. An illustrative example is the use of digital twins in gas turbine manufacturing, where they are used to precisely predict and optimize the lifespan and efficiency of turbines under various operating conditions. By virtually replicating the turbine and its operating environment, engineers can simulate various scenarios, improving turbine performance and reliability.
Suitable for:
Artificial intelligence is revolutionizing manufacturing
A leading electronics manufacturer in China has impressively demonstrated how AI-driven automation can help reduce production waste. By using intelligent image recognition systems and algorithms, the company is able to automatically identify up to 16 different categories of production waste and route it to the correct recycling process. This initiative resulted in a significant reduction in energy consumption per unit of production by 24% and a reduction in production waste by almost 50%. In addition, AI is being used in manufacturing for predictive maintenance. By analyzing sensor data and historical patterns, AI systems can predict potential machine failures before they occur, minimizing unplanned downtime and reducing maintenance costs.
The industrial metaverse as an innovation platform
BMW recognized the possibilities of industrial meta verse at an early stage and uses digital twins to create detailed virtual replicas of its production facilities. These virtual factories serve as a platform for optimizing various aspects of the business processes. A particularly remarkable example is the “previous construction” of a complete factory in industrial meta verse. Before the physical building began, the factory was completely simulated and optimized. This made it possible to identify and remedy potential problems in the planning process at an early stage, which led to significant cost savings and faster commissioning. In addition, industrial meta verse enables improved cooperation across geographical borders. In the virtual environment, engineers, designers and production planners can work together on projects, develop prototypes and optimize production processes as if they were physically in the same place.
In addition to these core technologies, infrastructure technologies such as the 5G mobile network and advanced robotics systems also play a crucial role in the industrial metaverse. 5G networks enable extremely fast and reliable data communication with low latency, which is essential for real-time applications and connecting a wide range of devices and sensors. Advanced robot systems equipped with AI and sensors are taking on increasingly complex tasks in production and logistics, thereby contributing to automation and increasing efficiency. These technologies are also of great importance for the future operation of the GWE as they have the potential to further improve the efficiency, flexibility and agility of production.
Suitable for:
GWE's future vision: Continuous innovation and adaptation
Even if the available sources do not contain specific details about GWE's future visions in the area of digital transformation, it can be assumed that the plant will continue to expand its pioneering role in the implementation of new technologies. Digital transformation is not a one-time project, but a continuous process of innovation and adaptation. Companies must constantly adapt to new technological developments and changing market conditions in order to maintain and expand their competitiveness. For GWE, this likely means continuous development of the existing digital infrastructure, research and implementation of new technologies such as quantum computing or advanced forms of additive manufacturing, and even stronger networking with partners and customers along the entire value chain. A possible focus could also be on the development of even more intuitive and user-friendly human-machine interfaces to further optimize collaboration between humans and robots and promote the acceptance of new technologies among employees. In addition, cybersecurity will play an increasingly important role as increasing connectivity also opens up new areas of attack. The GWE is therefore expected to continue investing in robust security measures to protect sensitive data and critical infrastructure.
The GWE as a pioneer for the intelligent manufacturing of tomorrow
The Siemens device plant (GWE) impressively demonstrates how the consistent implementation of the digital transformation can fundamentally change the manufacturing industry. Through the targeted use of key technologies such as digital twins, artificial intelligence and industrial metavers, the GWE continuously optimizes its production processes and is consistently working to raise efficiency and sustainability to a new level. As a “digital lighthouse factory”, the GWE not only serves as a model for other companies, but also provides valuable knowledge and best practice for the successful implementation of digital technologies in production. The digital transformation of the GWE is therefore not only of great importance for the company itself, but also serves as pioneering roadmap for other manufacturers who want to use digital technologies to increase their efficiency, strengthen their competitiveness and make a contribution to more sustainable production. The path of the GWE shows that the intelligent factory of the future is no longer a distant vision, but can already become a reality through consistent innovation and the courage to change.
We are there for you - advice - planning - implementation - project management
☑️ SME support in strategy, consulting, planning and implementation
☑️ Creation or realignment of the digital strategy and digitalization
☑️ Expansion and optimization of international sales processes
☑️ Global & Digital B2B trading platforms
☑️ Pioneer Business Development
I would be happy to serve as your personal advisor.
You can contact me by filling out the contact form below or simply call me on +49 89 89 674 804 (Munich) .
I'm looking forward to our joint project.
Xpert.Digital - Konrad Wolfenstein
Xpert.Digital is a hub for industry with a focus on digitalization, mechanical engineering, logistics/intralogistics and photovoltaics.
With our 360° business development solution, we support well-known companies from new business to after sales.
Market intelligence, smarketing, marketing automation, content development, PR, mail campaigns, personalized social media and lead nurturing are part of our digital tools.
You can find out more at: www.xpert.digital - www.xpert.solar - www.xpert.plus