Intralogistics & Logistics – Disrupted supply chains: With relocation and buffer storage for more security
Language selection 📢
Published on: July 3, 2022 / update from: November 6, 2024 - Author: Konrad Wolfenstein
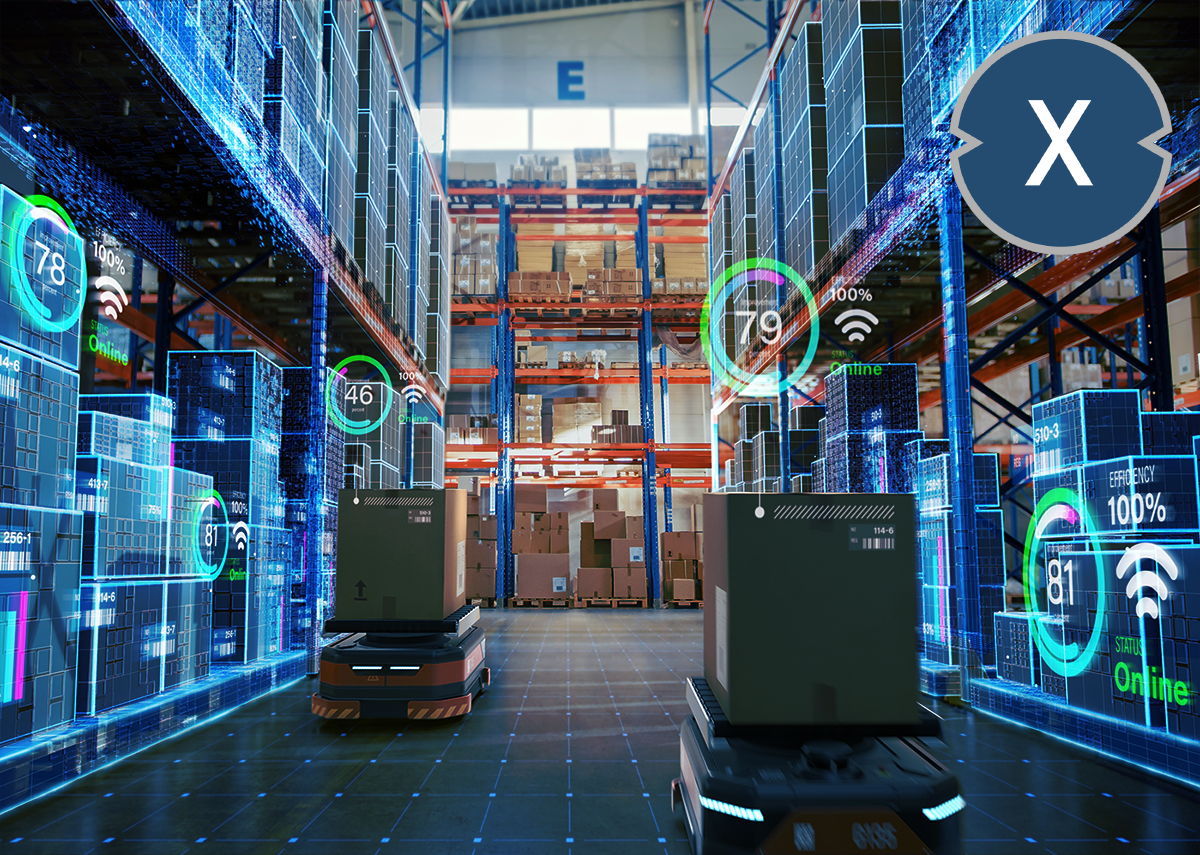
Supply chains: With relocation and buffer storage for more security – Image: Xpert.Digital / Gorodenkoff|Shutterstock.com
Disrupted supply chains. What to do?
For over two and a half years, logisticians and companies around the world have been faced with disrupted supply chains. Especially since the beginning of the global corona pandemic, there have been repeated production downtimes and spontaneous delays in the handling of ships, which can lead to months of waiting for the corresponding products or components in Europe. The war in Ukraine has added another risk factor, which also leads to serious failures and delays in the supply chain.
For logistics companies, given this uncertainty, it is hardly possible for them to operate a strategically plannable business. Companies, on the other hand, cannot produce and deliver sufficiently, which is why they lose valuable sales in view of the sometimes high demand. The traffic jam in the supply chains ultimately means that many companies are skeptical about the future or even see their existence at risk, even though their order books are full to the brim.
Massive sales losses due to supply chain chaos
In fact, delivery problems can lead to significant cash flow problems, especially for seasonal items. A retailer who sells summer goods will have difficulty getting rid of them and at great discounts if he does not receive them until autumn or winter. There is hardly any way for him to compensate for the negative consequences of the current chaotic supply chains, meaning that once lost business cannot be made up again.
The fashion trade in particular is suffering from current developments. According to a study by the Textile Shoes Leather Goods Trade Association (BTE), only 5% of the retailers surveyed stated that they experienced no or only minimal problems with the delivery of goods. On the other hand, 37% complained about failures of up to 10 and 20% respectively. The affected companies must already be in a very good economic position in order to be able to cushion the resulting shortfall in income.
But the supply chain crisis affects companies of all industries and sizes. This also applies to the local photovoltaic industry, because it also imports important raw materials and preliminary products from all over the world. In this area in particular, the conditions for flourishing sales are met. The energy transition and the increased pressure to move away from fossil energies due to the Russia conflict are leading to a significant revival in demand for renewable energies. Solar installations are booming across the country, but the numbers could be even better if companies could meet the immense demand.
How sales can be secured
But what should be done to avoid falling into the vicious circle of impending delivery bottlenecks, material shortages, production downtime, supply shortages and massive loss of sales? Since the beginning of 2020 at the latest, there has been increasing discussion about relocating parts of the production, which was partly outsourced to the Far East decades ago, closer to the domestic sales market and the company's own location. In addition, more and more company managers are placing greater emphasis on the safety of production instead of just looking at superficial efficiency when it comes to choosing a location.
Relocation is a very productive step, particularly in highly automated manufacturing processes, because countries with lower wages can hardly exploit their cost advantages. In addition, manufacturers are moving closer to the processes, which gives them significantly better control and control options than if production took place tens of thousands of kilometers away. In addition, companies that take back production will have a better handle on the possible withdrawal of know-how and sensitive data.
Buffer storage offers another option for cushioning fluctuations in the supply chain . Forward-looking companies have long relied on sufficient inventory. In doing so, they say goodbye to the just-in-time principle that has characterized production in recent years. Here too, security and a warehouse that may be a little too full from a purely business perspective are preferable in these times to logistics that may collapse if the first required part is missing.
Supply chain on the brink? The delivery difficulties and solutions
Is the global supply chain torn apart by ongoing problems and regional crises? – Image: Xpert.Digital / Iaroslav Neliubov|Shutterstock.com
We recently wrote about it: “As has already been described countless times, globalization has put a lot of strain on the supply chain structure and made it vulnerable to unexpected and unexpected crises beyond its control. But also in the relatively short time there was no strategic awareness. This means that there is no relaxation in sight along the supply chain in logistics or intralogistics in the future either.”
Now it's time to act. Anyone who does it now is late - and there are quite a few of them! As early as 2012, 16.2% of the companies surveyed stated in a survey that they had no solutions or strategies for supply chain risk management. A reaction should be made now at the latest, because the current situation will continue. And what many people don't even consider: the danger of a chain reaction and the possible consequences of further crises resulting from it are real. Can anyone seriously say this is it?
Need for action to ensure supply chains continue to function
Fragile supply chains: Supply chain under pressure – Image: Xpert.Digital / Travel mania|Shutterstock.com
Global supply chains are still strained by the pandemic. Many countries have introduced numerous anti-pandemic measures, which have caused severe delays in value and supply chains. For example, control and quarantine zones in logistical hubs have led to delivery backlogs of goods. As a result, many supplier companies were hindered in their production and were no longer able to fully meet their delivery obligations. And missing supplier parts can quickly have a massive impact on production processes. Added to this are the absence of workers due to illness or travel restrictions.
In-house competence: The example of GridParity
The relocation requires that the companies have the expertise to produce the required materials or parts themselves. However, many companies have lost the know-how for this in recent years. Instead, they have become problematically dependent on their suppliers.
The PV manufacturer GridParity AG shows how it can be done efficiently and differently. The solar specialists from Karlsfeld near Munich have been relying on self-sufficient methods for some time now when it comes to producing their PV systems. GridParity works closely with Agora Solar as in Slovakia in the production of modules. In this way, the company, in which GridParity owns a third, takes over the production of many important parts that would otherwise have to be sent by ship halfway around the world to be available to GridParity. This also helps to minimize uncertainties in the supply chain. At the same time, it shows that strategic decisions such as investing in a local producer like Agora can make a significant contribution to securing the future of GridParity.
📦 Logistics consulting for industry and mechanical engineering - for logistics managers and warehouse managers
Do you need competent support in implementing your requirements? Do you have questions about Smart Factory, Smart Logistics or digitalization?
🏬 Warehouse optimization and automation for industry, production and trade
The automation of warehouses and supply chains is an essential element of warehouse optimization. We support you in this.
🛒 E-commerce storage solutions for returns, fast shipping (same day delivery) and error-free picking
E-commerce has special requirements and competition is becoming ever stronger. It is not for nothing that e-commerce is considered the driver of changes in the market. With our digital know-how, innovative solutions and implementations are our strength.
Logistics consultant for secure supply chains and buffer warehouses: Use our Xpert.Plus service for your logistics consulting, warehouse planning or warehouse consulting
Xpert.Plus is a project from Xpert.Digital. We have many years of experience in supporting and advising on storage solutions and in logistics optimization, which we bundle in a large network Xpert.Plus
I would be happy to serve as your personal advisor.
You can contact me by filling out the contact form below or simply call me on +49 89 89 674 804 (Munich) .
I'm looking forward to our joint project.
Xpert.Digital – Konrad Wolfenstein
Xpert.Digital is a hub for industry with a focus on digitalization, mechanical engineering, logistics/intralogistics and photovoltaics.
With our 360° business development solution, we support well-known companies from new business to after sales.
Market intelligence, smarketing, marketing automation, content development, PR, mail campaigns, personalized social media and lead nurturing are part of our digital tools.
You can find out more at: www.xpert.digital – www.xpert.solar – www.xpert.plus