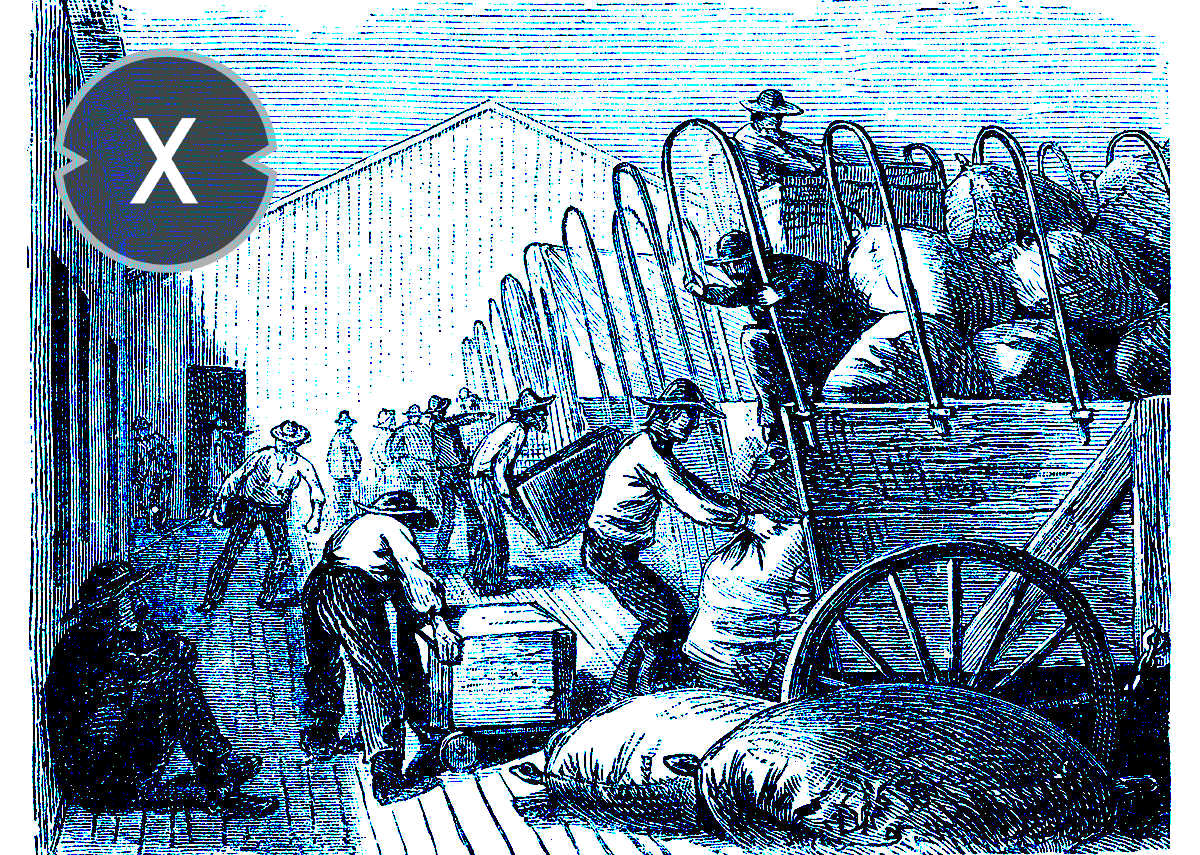
Logistik in den 1850ern / Geschichte der Intralogistik – Bild: Xpert.Digital / Stocksnapper|Shutterstock.com
Obwohl bei der Bereitstellung der Steinquader für den Bau der Pyramiden bestimmt noch nicht von Materialfluss und Intralogistik gesprochen wurde, werden die mit den Begriffen zusammenhängenden Aufgaben doch seit Jahrtausenden erledigt. Anfänglich noch ohne jeglichen Automatisierungsgrad, doch bereits mit Erfindung des Rads wurde ein erstes technisches Hilfsmittel eingesetzt, um logistische Prozesse zu bewältigen. Quelle logistischer Aufgaben war zumeist das Militär, welches seit der Antike den funktionierenden Transport von Material und Soldaten einforderte. Größere bauliche Vorhaben mit logistischem Anspruch wie eben der Bau der Pyramiden waren da eher noch die Ausnahme. An der eingesetzten Technik änderte sich über die folgenden Jahrhunderte wenig, und erst mit der aufkommenden Industrialisierung bahnte sich auch in der Logistik der Fortschritt seinen Weg.
Anfänge nach dem Krieg
Ihren Aufschwung nahm die zivile Logistik nach dem zweiten Weltkrieg. Im Zuge der wirtschaftlichen Erholung trat die Ausrichtung der Logistik auf militärische Belange nach und nach zugunsten wirtschaftlicher Aspekte zurück. Jedoch wurde auch zu dieser Zeit bei Beschreibung der innerbetrieblichen Abläufe noch lange nicht von Intralogistik gesprochen.
Dazu kam, dass zu Zeiten des Wirtschaftswunders in den 50er Jahren der Fokus von Unternehmen primär auf der Produktion und der optimalen Nutzung der oft knappen Ressourcen lag. Wenn von innerbetrieblicher Logistik gesprochen wurde, dann eher von Fördertechnik. Dabei ging es allerdings weniger um Prozessoptimierung bei Lagerung und Kommissionierung, sondern vielmehr um Fragen des Förderns oder Transportierens von Waren. Auch beim Thema Lagerung ging es mehr um die adäquate Aufstellung von Lagerregalen als um effizienzsteigernde intralogistische Maßnahmen.
Jedoch kam es in dieser Zeit zu einer Erfindung, die zu einem enormen Anschwellen der globalen Warenströme und damit einer zunehmenden Bedeutung der Logistik führen sollte: Der Frachtcontainer, der 1956 vom Amerikaner Malcom P. McLean entwickelt wurde und der in den folgenden Jahren den gesamten Transportsektor umkrempeln sollte.
Jetzt, mit zunehmender Globalisierung und stetig steigendem Wettbewerbsdruck wurden die Potentiale der allgemeinen und innerbetrieblichen Logistik erkannt, mit der sich beträchtliche Kosteneinsparungen erzielen ließen.
Der Fortschritt erreichte Deutschland 1962, als Bertelsmann das erste automatische Hochregallager in Gütersloh vorstellte. Geschuldet war der Bau gestiegenen Anforderungen der Kunden hinsichtlich Lieferservice und -geschwindigkeit.
Ein Anfang war gemacht, doch trotz der wachsenden Bedeutung von Lagertechnik für Effizienz und Produktivität wurde die Intralogistik in den 70er und 80er Jahren weiter als klassischer Teil einer Gesamtlogistik, die aus Transport, Umschlag und Lagerung bestand, gesehen.
Definition der Intralogistik erst in 2003
Während der sich in den 90er Jahren durchsetzenden ganzheitlichen Betrachtung der Wertschöpfungskette logistischer Aufgaben wurde die Definition der Supply Chain geboren. Bei dieser ging es um die Analyse und Optimierung des kompletten Wertschöpfungszyklus’ vom Rohmaterial bis zur Übergabe des Fertigproduktes an den Endabnehmer. Auch machten im Zuge des sich verschärfenden globalen Wettbewerbs Begriffe wie Lean Production oder Lean Logistics die Runde. Und eben in diesem Bereich wurde der Teil, den die innerbetrieblichen Aktivitäten einnahmen, als immer wichtiger betrachtet. So wichtig, dass im Jahr 2003 von Branchen- und Marketingfachleuten schließlich der eigentliche Begriff der Intralogistik festgelegt wurde. Per Definition repräsentiert die Intralogistik-Branche “sämtliche Anbieter von Hebezeugen, Förder- und Lagertechnik, Logistik-Software, Dienstleistungen und Komplettsystemen. Die Intralogistik umfasst die Organisation, Steuerung, Durchführung und Optimierung des innerbetrieblichen Materialflusses, der Informationsströme sowie des Warenumschlags in Industrie, Handel und öffentlichen Einrichtungen.”
In 2015 betrug der Umsatz der Branche knapp 19 Milliarden Euro. Nicht eingerechnet sind Aufwendungen für den Betrieb der logistischen Anlagen, der Lagerhäuser, Vertriebszentren und weiterer Intralogistiklösungen. Dabei ist Deutschland nach den USA der wichtigste Produzent von Intralogistikanlagen.
Seitdem sich in vielen Bereichen von Industrie und Produktion das ursprünglich von Toyota entwickelte Just-In-Time-Konzept durchgesetzt hat, wird dies auch vermehrt in der Intralogistik angewendet. Kein Wunder, minimieren doch Anlieferung und Bereitstellung auf Bestellung an Produktionslinien oder Kommissionierstationen Lagerflächen und -kosten. Ein Teil dieses Konzepts ist die Kanban-Methode.
Kanban in der Intralogistik
In zentral gesteuerten Planungssystemen wird eine vergleichsweise hohe Vorratshaltung benötigt, was hohe Lagerhaltungskosten zur Folge hat. Im Gegensatz dazu wird der Nachschub im Kanban-System auf Grundlage der am Verarbeitungsort verwendeten Güter gesteuert. Die aus Japan stammende Methode orientiert sich somit ausschließlich am tatsächlichen Materialverbrauch und ermöglicht so die Reduktion der vorzuhaltenden Bestände in Lager, Vormontage und nachgelagerter Produktion. Eine Verringerung der Lagerraten und -flächen sind die Folge dieser Art der Bereitstellung auf Abruf.
Dazu werden über die Produktionskette hinweg den jeweiligen Bereitstellungsorten dezentrale Pufferlager beigeordnet, sodass die benötigten Waren stets auf kurzen Transportwegen zum Ziel gelangen. Um die aufgrund der kurzen Strecken erreichten Zeitvorteile effektiv nutzen zu können, ist ein hohes Maß an Präzision und Bereitstellungsleistung bei den Lagersystemen gefragt. Am besten funktionieren hier kompakt bauende und platzsparende automatisierte Geräte, deren Steuerung über eine zentrale, auf die Lagerbedingungen und -anforderungen abgestimmte Lagerverwaltungssoftware erfolgt.
Die Zukunft – ein kleiner Ausblick
Anzunehmen ist, dass einer weiteren Automatisierung der Lagerprozesse die Zukunft gehört. Im Zuge der technischen Weiterentwicklung werden Hard- und Software permanent leistungsfähiger und schlauer. So ist es nicht mehr weit, bis autonom agierende und untereinander in Form einer Schwarmintelligenz kommunizierende Transportsysteme die Ein-, Auslagerung und Kommissionierung von Artikeln übernehmen werden. Im Vergleich zum Menschen sind sie einfach zu präzise, schnell, ermüdungsfrei und rund um die Uhr einsetzbar, als dass sich ihr Einsatz über kurz oder lang nicht durchsetzen würde.
Dazu fließen in die Planung intralogistischer Aktivitäten immer stärker Umweltgedanken mit ein. Kein Wunder, gilt die Intralogistik doch als Segment mit nennenswerten Einsparmöglichkeiten im energetischen Bereich. Unter dem Stichwort Green Logistics wird die Energieeffizienz damit zu einem weiteren treibendem Moment in der Weiterentwicklung der Intralogistik.