Entwicklung der Container-Terminals: Von Container Yards zu vollautomatisierten vertikalen Container-Hochregallager
Xpert Pre-Release
Sprachauswahl 📢
Veröffentlicht am: 25. Juli 2025 / Update vom: 25. Juli 2025 – Verfasser: Konrad Wolfenstein
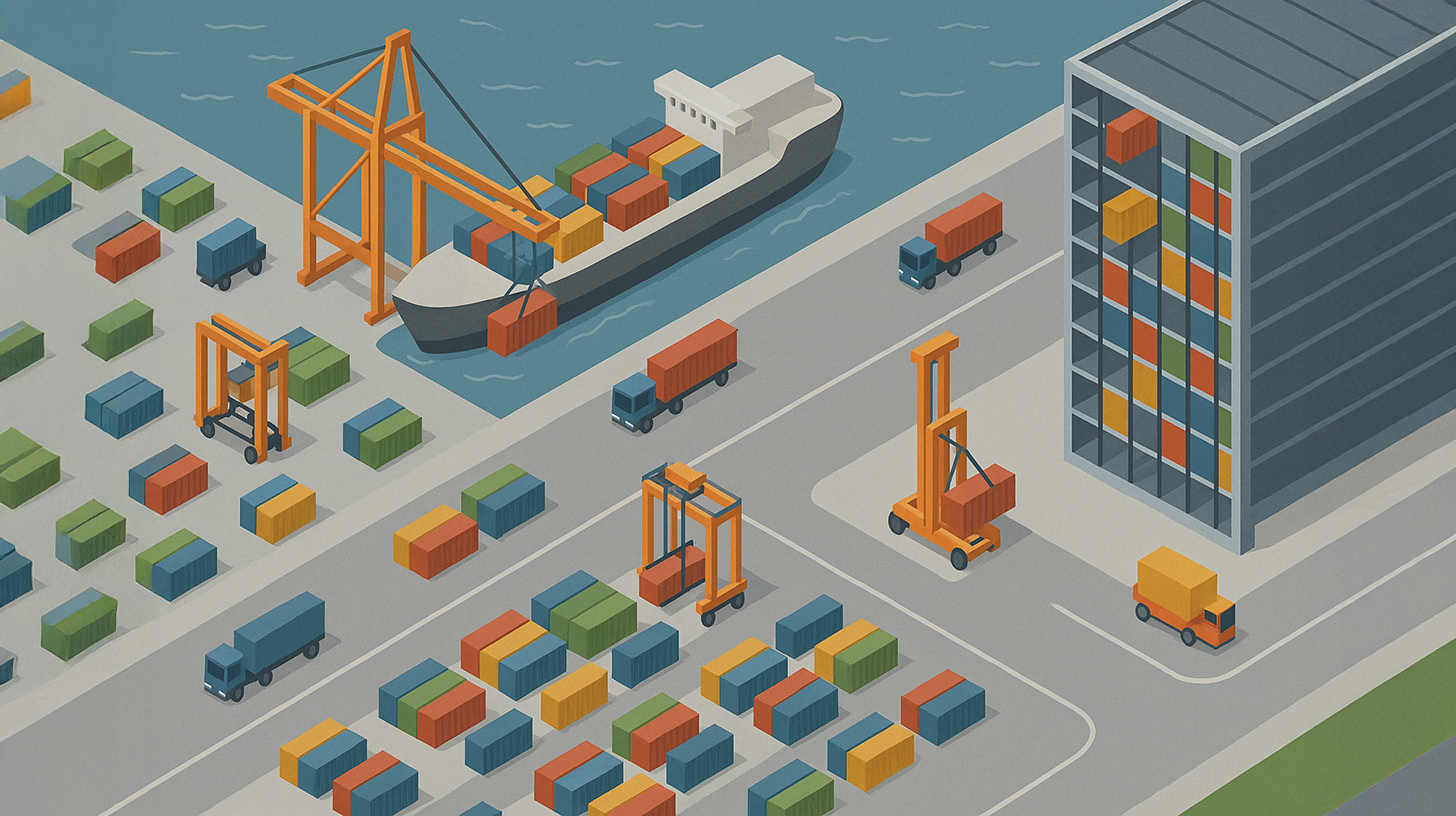
Entwicklung der Container-Terminals: Von Container Yards zu vollautomatisierten vertikalen Container-Hochregallagern – Bild: Xpert.Digital
Raum als Strategie: Die Neuerfindung der globalen Containerlogistik
Platzwunder der Logistik: Intelligente Lagersysteme verändern den Welthandel
Weiterentwicklung der Container-Terminals von Container Yards (Containerstellfläche), hin zu platzoptimierten, vollautomatisierten und KI-gestützten vertikalen Container-Hochregallagern der KV-Terminals (Kombinierter Verkehr aus Straße, Schiene und Seefahrt) des globalen Güterverkehrs.
Der Wendepunkt der globalen Logistik – Wenn der Raum zur strategischen Ressource wird
Das globale Logistiknetzwerk, das Rückgrat des modernen Welthandels, ächzt unter der Last seines eigenen Erfolgs. Ein unaufhaltsames Wachstum des Handelsvolumens, gepaart mit einer dramatischen Zunahme der Schiffsgrößen – insbesondere der Ultra Large Container Ships (ULCS), die bis zu 24.000 TEU (Twenty-Foot Equivalent Unit) transportieren können – hat das traditionelle Modell des Containerterminals an seine absoluten physischen und operativen Grenzen gebracht. An den Schnittstellen der globalen Warenströme, in den Häfen, manifestiert sich eine Krise, die die gesamte Lieferkette zu lähmen droht.
Diese Entwicklung hat einen zentralen Zielkonflikt der modernen Hafenlogistik offengelegt: das unlösbar scheinende Paradoxon zwischen der Notwendigkeit einer immer höheren Lagerdichte auf knappen, teuren Flächen und dem daraus resultierenden katastrophalen Verlust an betrieblicher Effizienz in konventionellen Systemen. Der Containerterminal, einst ein reiner Transitpunkt, ist zum kritischen Flaschenhals geworden, der das Tempo der gesamten globalen Lieferkette diktiert. Die Weiterentwicklung von weitläufigen Containerstellflächen, den sogenannten Container Yards, hin zu platzoptimierten, vollautomatisierten und KI-gestützten vertikalen Container-Hochregallagern ist daher keine bloße technologische Aufrüstung. Sie ist vielmehr eine notwendige, paradigmenwechselnde Antwort auf eine systemische Krise, die eine grundlegende Neudefinition der Funktionsweise von Umschlagterminals im Kombinierten Verkehr (KV) aus Straße, Schiene und Seefahrt erzwingt.
Passend dazu:
- Die Top Ten der Container-Hochregallager-Hersteller und Leitfaden: Technologie, Hersteller und Zukunft der Hafenlogistik
Das Zeitalter der Grenzen – Traditionelle Containerterminals am Scheideweg
Anatomie eines konventionellen Containerterminals: Ein Ökosystem unter Druck
Um die Tragweite der bevorstehenden Revolution zu verstehen, ist ein Blick auf die Anatomie und die Funktionsweise eines traditionellen Containerterminals unerlässlich. Ein solcher Terminal ist ein komplexes Ökosystem, das aus mehreren klar definierten physischen Komponenten und operativen Zonen besteht. An vorderster Front liegt die Kaianlage mit den Liegeplätzen (Berths), an denen die riesigen Containerschiffe festmachen. Hier dominieren die gewaltigen Ship-to-Shore (STS) Krane, deren Ausleger sich über die gesamte Breite der Schiffe erstrecken, um Container zu laden und zu löschen.Das Herzstück des Terminals ist jedoch das weitläufige Container Yard (CY), eine riesige, befestigte Fläche, die als temporäres Pufferlager für Tausende von vollen und leeren Containern dient. Innerhalb dieses Yards operiert eine Flotte von spezialisierten Umschlag- und Transportgeräten. Dazu gehören gummibereifte Portalkrane (Rubber-Tired Gantry Cranes, RTGs), schienengebundene Portalkrane (Rail-Mounted Gantry Cranes, RMGs), Portalhubwagen (Straddle Carriers) und Greifstapler (Reach Stackers), die für die Stapelung und den Transport der Container innerhalb des Yards zuständig sind. Das dritte wesentliche Element ist der Gate-Komplex, das Nadelöhr für den landseitigen Verkehr, an dem Lkw abgefertigt, Container registriert und Sicherheitskontrollen durchgeführt werden. Ergänzt wird dies oft durch eine Bahnanlage für den intermodalen Weitertransport ins Hinterland.Die betrieblichen Abläufe folgen einer klaren Logik: Schiffsoperationen umfassen das schnelle Be- und Entladen der Schiffe durch die STS-Krane. Die Yard-Operationen beinhalten die Lagerung, Organisation und Bereitstellung der Container. Die Gate- und Bahnoperationen stellen die nahtlose Anbindung an die landseitigen Verkehrsträger sicher. In der Theorie ist dies ein fließender Prozess. In der Praxis jedoch hat die schiere Masse an Containern, die von einem einzigen ULCS gelöscht wird, dieses System an den Rand des Zusammenbruchs gebracht.
Der Teufelskreis der Ineffizienz: Das Paradigma des Blockstapelns
Die Achillesferse jedes konventionellen Containerterminals liegt in seiner fundamentalen Designphilosophie: dem Blockstapeln. Unabhängig davon, ob ein Terminal ein lineares oder ein Block-Layout verwendet, beruht das Prinzip darauf, Container direkt übereinander zu stapeln, um die begrenzte Fläche maximal auszunutzen. Was auf den ersten Blick logisch erscheint, ist in Wahrheit die Quelle einer tiefgreifenden und systemischen Ineffizienz.Das Kernproblem sind die sogenannten “unproduktiven Umstapelvorgänge”, auch als “Reshuffling” oder “Shuffle-Moves” bekannt. Um auf einen Container zuzugreifen, der sich am Boden eines Stapels befindet, müssen alle darüber liegenden Container zunächst angehoben und an anderer Stelle zwischengelagert werden. Erst dann kann der Zielcontainer entnommen werden, woraufhin die zwischengelagerten Container oft erneut bewegt werden müssen. Analysen zeigen, dass diese unproduktiven Bewegungen, die weder Zeit noch Wert schaffen, zwischen 30 % und 60 % aller Kranbewegungen in einem herkömmlichen Yard ausmachen. Das bedeutet, dass im schlimmsten Fall mehr als die Hälfte der gesamten Kranaktivität reiner Verschwendung dient.Dieser Umstand erzeugt einen Teufelskreis: Um die Kapazität auf begrenztem Raum zu erhöhen, sind die Terminalbetreiber gezwungen, die Container höher zu stapeln. Doch mit jeder zusätzlichen Ebene steigt die Wahrscheinlichkeit und Komplexität von Umstapelvorgängen exponentiell an. Ab einem Füllgrad von 70-80 % bricht die Leistung eines Lagerblocks dramatisch ein. Das Ergebnis sind unvorhersehbare Abfertigungszeiten, massive Staus innerhalb des Terminals und eine operative Leistung, die nicht mehr planbar ist. Die Größenvorteile der Megaschiffe auf See werden durch massive Ineffizienzen an Land zunichtegemacht.
Der Imperativ des Kombinierten Verkehrs (KV): Wenn der Flaschenhals die Kette lähmt
Für die Terminals des Kombinierten Verkehrs (KV), die als kritische Schnittstelle zwischen den Verkehrsträgern Schiff, Bahn und Lkw fungieren, sind diese Ineffizienzen fatal. Die Leistungsfähigkeit des gesamten intermodalen Netzwerks hängt von der Effizienz und Zuverlässigkeit dieser Umschlagpunkte ab. Ein konventioneller Terminal, der von unplanbaren Umstapelvorgängen und internen Staus geplagt wird, wirkt wie eine Bremse für die gesamte Logistikkette.Lange und unvorhersehbare Wartezeiten für Lkw an den Gates und für Güterzüge an den Bahnterminals sind die direkte Folge. Ein verspäteter Container kann die Abfahrt eines ganzen Güterzuges verzögern, was wiederum Fahrpläne im gesamten Schienennetz durcheinanderbringt und Anschlussverbindungen gefährdet. Die ökonomischen und ökologischen Vorteile des Kombinierten Verkehrs – die Bündelung von Transporten und die Verlagerung von der Straße auf die Schiene – werden durch den Flaschenhals im Hafen untergraben. Die Unberechenbarkeit des Terminals pflanzt sich wellenartig durch die gesamte Lieferkette fort und macht eine zuverlässige Just-in-Time-Logistik nahezu unmöglich. Es wird deutlich, dass die Ineffizienz traditioneller Terminals kein Managementproblem ist, sondern ein systemischer Fehler, der in ihrer physischen Architektur wurzelt. Dieses einst adäquate Modell ist durch die Skalierung und Geschwindigkeit des modernen globalen Handels obsolet geworden und hat die Terminals zur Hauptquelle von Reibung und Unvorhersehbarkeit in den Lieferketten gemacht.
Die Vertikale Revolution – Das Hochregallager als neues Paradigma
Von horizontaler Ausdehnung zu vertikaler Dichte: Das HRL-Konzept
Als Antwort auf die systemische Krise der konventionellen Terminals entsteht ein radikal neuer Ansatz: das vollautomatisierte Container-Hochregallager (HRL), international als High-Bay Storage (HBS) bekannt. Statt sich weiter horizontal auszudehnen, was in den meisten Hafenstädten geografisch unmöglich und ökologisch bedenklich ist, verlagert das HRL-Konzept die Lagerung in die Vertikale. Es ist eine Strategie, die die Gleichung der Flächennutzung fundamental verändert.Dieses Konzept ist keine reine Fiktion, sondern basiert auf bewährter und robuster Technologie, die aus einem unerwarteten Sektor stammt: der Schwerindustrie. Führende Anbieter wie die deutsche SMS group haben jahrzehntelange Erfahrung mit vollautomatisierten Hochregallagern für extrem schwere Lasten, wie beispielsweise 50 Tonnen schwere Stahlcoils, die unter rauen Industriebedingungen im 24/7-Betrieb zuverlässig gehandhabt werden. Die Adaption dieser erprobten Technologie für die Containerlogistik reduziert das wahrgenommene Risiko für Hafenbetreiber erheblich und verleiht dem Innovationssprung eine solide industrielle Basis.
Passend dazu:
Dekonstruktion der Technologie: Das Prinzip des direkten Einzelzugriffs
Ein HRL ist weit mehr als nur ein hohes Regal. Es ist ein hochkomplexes, vollautomatisiertes System, dessen Genialität in einem einzigen Prinzip liegt: dem direkten Einzelzugriff auf jeden einzelnen Container. Dieses Prinzip wird durch zwei Kernkomponenten ermöglicht.Erstens, die Stahlregalstruktur: Eine massive Stahlkonstruktion, die bis zu elf Container hoch sein kann, bildet das Skelett des Lagers. Jeder Container wird in einem eigenen, individuell adressierbaren Regalfach platziert. Ein entscheidendes Detail ist, dass diese Regale keine durchgehenden Böden benötigen. Die standardisierten ISO-Container sind selbsttragend und werden nur an ihren vier Eckbeschlägen (Twistlocks) gehalten. Dies reduziert den Materialeinsatz, das Gesamtgewicht und die Baukosten erheblich, ohne die Statik zu beeinträchtigen.Zweitens, die automatisierten Regalbediengeräte (RBG), auch Stacker Cranes genannt: Diese schienengeführten, Hochgeschwindigkeitskrane bewegen sich autonom durch die Gänge zwischen den Regalreihen. Sie sind mit verstellbaren Greifarmen (Spreadern) ausgestattet, die sich präzise an den Containern verriegeln. Von einem zentralen Steuerungssystem gelenkt, kann ein RBG jeden beliebigen Container im Lager direkt ansteuern und entnehmen oder einlagern – ohne einen einzigen anderen Container bewegen zu müssen.Genau hier liegt der revolutionäre Kern der Technologie. Der direkte Einzelzugriff eliminiert unproduktive Umstapelvorgänge vollständig. Jede Bewegung eines Krans ist eine produktive Bewegung. Der fundamentale Zielkonflikt zwischen Lagerdichte und Zugriffseffizienz, der traditionelle Terminals lähmt, wird aufgelöst. Die wahre Revolution des HRL ist somit nicht die Vertikalität an sich, sondern der Wechsel von einer lagerzentrierten (Stapeln) zu einer zugriffszentrierten (Regalieren) Philosophie. Das Lager verwandelt sich von einem trägen Warenhaus in einen hochdynamischen Sortier- und Pufferknoten.
Fallstudie: Das BOXBAY-System als “Machbarkeitsnachweis”
Die technologische Machbarkeit und die Leistungsfähigkeit dieses Konzepts sind keine Theorie mehr. Das Joint Venture BOXBAY, eine Kooperation zwischen dem globalen Terminalbetreiber DP World und dem deutschen Anlagenbauer SMS group, hat mit seinem Pilotprojekt im Hafen Jebel Ali in Dubai den eindrucksvollen “Machbarkeitsnachweis” geliefert.Die Testanlage, die über 792 Containerstellplätze (ca. 1.300 TEU) verfügt, wurde unter realen Hafenbedingungen intensiv erprobt. Bis Ende 2024 wurden über 330.000 Containerbewegungen erfolgreich durchgeführt. Die Ergebnisse übertrafen die Erwartungen: Die Umschlagleistung erreichte 19,3 Bewegungen pro Stunde an der Schnittstelle zum Kai und beeindruckende 31,8 Bewegungen pro Stunde an den landseitigen Lkw-Kranen. Diese Zahlen belegen, dass das System nicht nur funktioniert, sondern auch eine bisher unerreichte Performance und Planbarkeit ermöglicht.Der nächste entscheidende Schritt ist bereits getan: Im März 2023 wurde der erste kommerzielle Auftrag für eine “Nachrüstung”-Implementierung im Hafen von Pusan, Südkorea, unterzeichnet. Dort wird das BOXBAY-System in einen bestehenden, hochmodernen Terminal nachgerüstet. Das Ziel: die Eliminierung von 350.000 unproduktiven Umstapelvorgängen pro Jahr und eine Verkürzung der Lkw-Abfertigungszeiten um 20 %. Der Erfolg dieses Projekts wird ein Lackmustest für die Fähigkeit der Technologie sein, die bestehende Infrastruktur der Welthäfen zu modernisieren und wird von der gesamten Branche mit höchster Aufmerksamkeit verfolgt.
Digitale Nervensysteme: Der Container-Terminal der Zukunft zwischen Hightech und Effizienz
Die Triebwerke des Wandels – Automatisierung, Robotik und Digitalisierung
Das automatisierte Terminal: Von der Teil- zur Vollautomatisierung
Automatisierung in Containerterminals ist kein binärer Zustand, sondern ein Spektrum mit unterschiedlichen Reifegraden. Die meisten heute als “automatisiert” bezeichneten Terminals fallen in die Kategorie der Teilautomatisierung. Hier wird typischerweise der Lagerprozess im Yard durch den Einsatz von automatisierten Stapelkranen (Automated Stacking Cranes, ASCs) automatisiert, während der horizontale Transport zwischen Kai und Lagerblock weiterhin mit manuell bedienten Fahrzeugen erfolgt.Die Vollautomatisierung geht einen Schritt weiter und automatisiert auch diesen horizontalen Transport. Anstelle von Lkw-Fahrern übernehmen fahrerlose Transportsysteme (Automated Guided Vehicles, AGVs) oder automatisierte Hubfahrzeuge (Automated Lifting Vehicles, ALVs) den Transfer der Container. Trotz des enormen Interesses an diesen Technologien sind weltweit nur etwa 3-4 % aller Containerterminals teil- oder vollautomatisiert. Dies verdeutlicht, dass die Hürden für die Einführung hoch sind. Das Konzept des Hochregallagers stellt dabei die höchste und am tiefsten integrierte Stufe der Automatisierung dar, bei der Lagerung und Handling zu einem einzigen, geschlossenen Robotiksystem verschmelzen.
Passend dazu:
- Die simple wie evolutionär gewachsene Idee vom Container-Regallager: Ein Paradigmenwechsel in der globalen Logistik
Das digitale Nervensystem: IoT und der “intelligente Hafen”
Damit ein hochautomatisertes System wie ein HRL als kohärentes Ganzes funktionieren kann, benötigt es ein digitales Nervensystem. Diese Rolle übernimmt das Internet der Dinge (Internet of Things, IoT). Durch ein dichtes Netz von Sensoren an Kränen, Fahrzeugen, der Infrastruktur und sogar an den Containern selbst wird der physische Terminal in Echtzeit digital abgebildet.Diese Konnektivität ermöglicht mehrere transformative Anwendungen. Erstens, die Echtzeit-Transparenz: Die Betreiber wissen zu jeder Sekunde, wo sich jeder Container und jedes Gerät befindet und in welchem Zustand es ist. Zweitens, die Zustandsüberwachung und vorausschauende Wartung (Condition Monitoring & Predictive Maintenance): Sensoren an kritischen Komponenten wie Motoren oder Lagern messen kontinuierlich Daten wie Vibrationen, Temperatur und Druck. Algorithmen analysieren diese Datenströme und können potenzielle Ausfälle vorhersagen, bevor sie eintreten. Dies ermöglicht einen Wechsel von einer teuren, reaktiven Reparaturkultur zu einer proaktiven, geplanten Instandhaltung, was die Ausfallzeiten drastisch reduziert und die Wartungskosten um bis zu 50-75 % senken kann. Drittens, die Erstellung von Digitalen Zwillingen: Aus den IoT-Daten lassen sich virtuelle 1:1-Abbilder des physischen Hafens erstellen. In diesen Simulationen können neue Prozesse, Layouts oder Notfallszenarien risikofrei getestet und optimiert werden, bevor sie in der realen Welt implementiert werden.
Der intelligente Kern: KI-gestützte Optimierung und Steuerung
Wenn das IoT das Nervensystem ist, dann sind Künstliche Intelligenz (KI) und Maschinelles Lernen (ML) das Gehirn des modernen Terminals. Die schiere Menge und Geschwindigkeit der von den IoT-Sensoren erzeugten Daten kann von menschlichen Disponenten nicht mehr effektiv verarbeitet werden. Hier setzen KI-Systeme an, die in das zentrale Terminal Operating System (TOS) – die Software-Plattform zur Steuerung aller Abläufe – integriert sind.
Optimierte Entscheidungsfindung: KI-Algorithmen treffen in Sekundenbruchteilen komplexe Entscheidungen. Sie bestimmen den optimalen Lagerplatz für jeden ankommenden Container unter Berücksichtigung von Faktoren wie Gewicht, Zielort und Abholzeit. Sie planen die effizienteste Bewegungssequenz für die Krane und berechnen die idealen Routen für die AGVs, um Staus zu vermeiden und Leerfahrten zu minimieren.
Vorausschauende Analytik (Predictive Analytics): Durch die Analyse historischer und aktueller Daten kann die KI die Ankunftszeiten von Schiffen präziser vorhersagen, drohende Engpässe im Yard prognostizieren und den zukünftigen Bedarf an Personal und Geräten antizipieren. Dies ermöglicht eine proaktive statt reaktive Ressourcenplanung.
Ressourcenmanagement: Die KI optimiert die Zuweisung von Liegeplätzen, Kranen und Fahrzeugen, um den Gesamtdurchsatz zu maximieren und die Wartezeiten für Schiffe und Lkw zu minimieren. Frühe Anwender von KI in der Logistik berichten von signifikanten Erfolgen, wie einer Reduzierung der Logistikkosten um 15 % und einer Steigerung der Service-Effizienz um 65 %.
Es wird deutlich, dass die physische Robotik und die digitale Intelligenz untrennbar miteinander verbunden sind. Die starre, hochkomplexe Struktur eines HRL ist nur durch eine hochentwickelte KI beherrschbar. Umgekehrt kann das Optimierungspotenzial der KI nur in einer vollautomatisierten, datenreichen Umgebung voll ausgeschöpft werden. Dies erzeugt eine positive Rückkopplungsschleife: Bessere Daten ermöglichen eine intelligentere KI, die wiederum effizientere physische Abläufe steuert. Die oft zitierte Beobachtung, dass automatisierte Häfen manchmal sogar weniger produktiv sind als manuelle, findet hier ihre Erklärung: Ohne das intelligente Gehirn (KI) ist der automatisierte Körper nur eine Ansammlung starrer Maschinen. Der Erfolg der Automatisierung hängt entscheidend von der Intelligenz ihres Steuerungssystems ab.
Ein Quantensprung – Die vielschichtigen Vorteile der neuen Terminalgeneration
Neudefinition der Effizienz: Ein Quantensprung bei Durchsatz und Geschwindigkeit
Die Leistungsdaten der neuen Systeme definieren die Maßstäbe für Effizienz neu. An erster Stelle steht die Flächeneffizienz: Ein Hochregallager kann auf der gleichen Grundfläche die dreifache Lagerkapazität eines konventionellen, mit RTGs betriebenen Yards erreichen. In manchen Konfigurationen bedeutet dies eine Reduzierung des benötigten Flächenbedarfs um bis zu 90 %. Für Häfen, die in dichten urbanen Räumen gefangen sind, ist dies ein unschätzbarer Vorteil.Gleichzeitig steigt die Umschlaggeschwindigkeit signifikant. Durch die Eliminierung unproduktiver Bewegungen und den direkten Zugriff auf jeden Container kann die Umschlagleistung am Kai um bis zu 20 % gesteigert werden. Dies verkürzt die Liegezeiten der Schiffe im Hafen – ein enormer wirtschaftlicher Gewinn für die Reedereien, für die jeder Tag im Hafen hohe Kosten verursacht. Landseitig können die Abfertigungszeiten für Lkw um ebenfalls 20 % reduziert werden, was zu weniger Staus an den Toren und einer besseren Auslastung der Transportkapazitäten führt.
Die folgende Tabelle stellt die Leistungskennzahlen der verschiedenen Technologien vergleichend gegenüber und verdeutlicht den Quantensprung, den Hochregallager darstellen.
Vergleich verschiedener Container-Terminal-Lagerungen
In der Logistik und Hafeninfrastruktur spielen Container-Terminal-Lagerungen eine entscheidende Rolle für Effizienz und Nachhaltigkeit. Ein detaillierter Vergleich verschiedener Lagersysteme zeigt signifikante Unterschiede: Der konventionelle RTG-Yard repräsentiert traditionelle Lagermethoden mit einer Lagerdichte von 700-1.000 TEU pro Hektar und hohen Umstapelvorgängen zwischen 30-60%. Im Gegensatz dazu bietet der automatisierte ASC-Yard eine deutlich höhere Lagerdichte von etwa 2.000 TEU und moderate Betriebskosten. Das Hochregallager (HBS) stellt die fortschrittlichste Lösung dar, mit einer beeindruckenden Lagerdichte von über 3.000 TEU, vollständig eliminierten Umstapelvorgängen und minimaler Umweltbelastung.
Die Systeme unterscheiden sich erheblich in Produktivität, Kosten und Umweltauswirkungen. Während konventionelle Systeme hohe lokale Emissionen und Lärmbelastung verursachen, bieten automatisierte und Hochregallager deutlich effizientere und umweltfreundlichere Alternativen mit elektrischem Antrieb und reduzierten Betriebskosten. Die Investitionskosten steigen dabei proportional zur Technologiekomplexität, wobei Hochregallager die höchsten Anfangsinvestitionen, aber auch die niedrigsten Betriebskosten aufweisen.
Die ökonomische Gleichung: Neubewertung von Kosten und Kapitalrendite
Die Einführung hochautomatisierter Systeme führt zu einer fundamentalen Verschiebung der Kostenstruktur. Das traditionelle Modell – geringe Investitionskosten (CAPEX) für Flächen und einfache Geräte, aber hohe laufende Betriebskosten (OPEX) für Personal und Diesel – wird umgekehrt. Ein HRL-Terminal folgt einem CAPEX-intensiven, aber OPEX-leichten Modell.Die hohen Investitionskosten sind die größte Hürde. Projekte können von mehreren hundert Millionen bis über eine Milliarde US-Dollar kosten. Diese Summen sind für viele, insbesondere kleinere Terminalbetreiber, prohibitiv.Der wirtschaftliche Nutzen entfaltet sich jedoch über die drastische Reduzierung der Betriebskosten auf lange Sicht. Die Personalkosten, der größte Posten in manuellen Terminals, können um bis zu 70 % gesenkt werden. Die Energiekosten sinken durch den vollelektrischen Betrieb und die Energierückgewinnung (Rekuperation) erheblich; das BOXBAY-Pilotprojekt zeigte Energiekosten, die 29 % niedriger als erwartet waren. Hinzu kommen signifikante Einsparungen bei der Wartung durch vorausschauende Instandhaltung und robustere, weil automatisierte, Prozesse.Der Return on Investment (Kapitalrendite) ist komplex und standortabhängig. Dennoch ergibt sich ein überzeugendes Geschäftsmodell, wenn man die OPEX-Einsparungen mit dem immensen Wert der eingesparten oder freigewordenen Flächen kombiniert. Bei Grundstückspreisen von 2.000 bis 3.000 Euro pro Quadratmeter kann die Einsparung von nur drei Hektar Land einen Wert von 60 bis 90 Millionen Euro repräsentieren, was die hohen Anfangsinvestitionen erheblich relativiert.
Das grüne Terminal: Ein neuer Standard der Nachhaltigkeit
Die neue Terminalgeneration setzt auch ökologisch neue Maßstäbe und wird zu einem zentralen Baustein für eine nachhaltige Hafenwirtschaft. Der Haupttreiber ist die Elektrifizierung: HRL-Systeme und die zugehörigen fahrerlosen Transportfahrzeuge sind vollelektrisch und eliminieren damit die lokalen Emissionen von CO2, Stickoxiden (NOx) und Feinstaub, die von Dieselmaschinen verursacht werden.Durch die Kombination mit erneuerbaren Energien kann ein CO2-neutraler Betrieb erreicht werden. Die riesige Dachfläche eines Hochregallagers ist ideal für die Installation von Photovoltaikanlagen, die den Terminal mit grünem Strom versorgen und ihn potenziell sogar zu einem Energie-Plus-System machen können.Darüber hinaus wird die Umweltbelastung drastisch reduziert. Da der Betrieb vollautomatisch in einem geschlossenen oder gekapselten System stattfindet, kann auf eine flächendeckende Beleuchtung des Yards verzichtet werden. Dies reduziert nicht nur den Energieverbrauch, sondern minimiert auch die Lichtverschmutzung. Ebenso wird die Lärmbelastung für angrenzende Stadtgebiete erheblich gesenkt – ein entscheidender Vorteil für Häfen in urbaner Lage. Schließlich leistet die immense Flächeneffizienz einen direkten Beitrag zum Umweltschutz, da sie den Bedarf an ökologisch bedenklichen und teuren Landgewinnungsprojekten durch Aufschüttungen reduziert.
Stärkung des Kombinierten Verkehrsnetzes
Für die Terminals des Kombinierten Verkehrs sind diese Vorteile transformativ. Ein mit einem HRL ausgestatteter Terminal wandelt sich von einem unberechenbaren Flaschenhals zu einem hochleistungsfähigen, zuverlässigen und schnellen Umschlagknoten. Die hohe Geschwindigkeit und vor allem die präzise Planbarkeit der Abfertigungsprozesse für Lkw und Züge synchronisieren die Schnittstellen zwischen den Verkehrsträgern.Diese Zuverlässigkeit macht die gesamte intermodale Kette wettbewerbsfähiger gegenüber dem reinen Straßentransport. Wenn Spediteure und Bahnbetreiber sich auf pünktliche und schnelle Übergaben im Hafen verlassen können, steigt der Anreiz, Transporte auf die umweltfreundlichere Schiene oder das Binnenschiff zu verlagern. Das HRL wird so zu einem entscheidenden “Enabler” für einen effizienteren und nachhaltigeren Modal Split im globalen Güterverkehr.
Risiken und Chancen der Hafen-Automatisierung - Was Unternehmen wissen müssen
Der Weg zur Implementierung – Navigation durch die Herausforderungen
Die Investitionshürde: Kapital, Komplexität und Regulatorik
Die primären Hindernisse sind offensichtlich. Die finanzielle Belastung durch die enormen Investitionskosten stellt eine massive Hürde dar, die nur die größten und finanzstärksten Hafenbetreiber und Konzerne stemmen können. Die Komplexität solcher mehrjährigen Großprojekte ist immens und erfordert tiefgreifendes Fachwissen in den Bereichen Anlagenbau, Robotik, IT-Integration und Projektmanagement.Hinzu kommen erhebliche technische Risiken, insbesondere bei der Integration der neuen automatisierten Systeme in bestehende, oft veraltete Infrastrukturen und IT-Landschaften (Legacy-Systeme). Schnittstellenprobleme können zu erheblichen Verzögerungen und Kostensteigerungen führen. Nicht zuletzt stellen langwierige regulatorische Hürden und Genehmigungsverfahren für derart große Bauvorhaben in vielen Ländern eine weitere große Herausforderung dar.
Neubau vs. Nachrüstung: Die zwei Pfade zur Modernisierung
Bei der Implementierung gibt es zwei grundlegend unterschiedliche Szenarien, deren Herausforderungen sich stark unterscheiden. Der Neubau-Ansatz, also der Neubau eines Terminals auf der “grünen Wiese”, ist das Ideal-Szenario. Er bietet vollständige Gestaltungsfreiheit, um Layout, Infrastruktur und Prozesse von Grund auf optimal aufeinander abzustimmen. Das BOXBAY-Pilotprojekt in Dubai ist ein Beispiel für ein solches Quasi-Neubau-Projekt, das die technische Machbarkeit unter idealen Bedingungen demonstrierte.Der Nachrüstungs-Ansatz, die Nachrüstung in einem bestehenden, laufenden Terminal, ist das weitaus häufigere und ungleich schwierigere Szenario. Die neue Technologie muss in einen 24/7-Betrieb integriert werden, ohne die laufenden Prozesse und den Kundenservice übermäßig zu stören. Dies erfordert eine komplexe, schrittweise Implementierung, bei der Teile des Terminals umgebaut werden, während andere weiterarbeiten. Solche Projekte können sich über Jahre ziehen und bergen ein hohes Risiko für unvorhergesehene Kosten und Betriebsstörungen. Der kommerzielle Auftrag für BOXBAY in Pusan ist daher von herausragender Bedeutung: Gelingt diese Nachrüstungs-Implementierung, beweist dies die Praxistauglichkeit des Konzepts für die Mehrheit der Welthäfen und könnte das Signal für eine breitere Marktakzeptanz sein.
Bei der Modernisierung von Infrastruktur und Technologiesystemen stehen Unternehmen grundsätzlich zwei zentrale Wege zur Auswahl: der Neubau oder die Nachrüstung. Beide Ansätze unterscheiden sich fundamental in ihren Charakteristiken und Herausforderungen.
Der Neubau bietet maximale Gestaltungsfreiheit, ermöglicht eine optimale Abstimmung von Layout und Technologie und erlaubt eine komplett neue Infrastrukturarchitektur. Allerdings sind die initialen Investitionskosten sehr hoch, da sämtliche Systeme neu aufgebaut werden müssen. Die Integrationskomplexität ist geringer, da von Beginn an einheitliche Systeme geschaffen werden. Das Projektrisiko bleibt dennoch hoch, primär aufgrund der immensen Investitionssummen.
Im Gegensatz dazu steht die Nachrüstung, die durch stark eingeschränkte Gestaltungsfreiheit gekennzeichnet ist. Hier müssen Anpassungen an bestehende Strukturen vorgenommen werden, was die Integration extrem komplex gestaltet. Die Kosten können zwar potenziell niedriger ausfallen als beim Neubau, jedoch birgt dieser Ansatz ein sehr hohes Risiko von Betriebsstörungen. Unternehmen müssen mit möglichen Kapazitätseinbußen über Jahre rechnen.
Beide Projektansätze haben lange Zeitpläne, wobei der Neubau planbarer erscheint, während Nachrüstungsprojekte anfälliger für unvorhergesehene Verzögerungen sind. Die Entscheidung zwischen diesen beiden Wegen erfordert eine sorgfältige Abwägung der spezifischen Unternehmensanforderungen, technologischen Rahmenbedingungen und finanziellen Ressourcen.
Der Faktor Mensch: Sozioökonomische Auswirkungen und die Zukunft der Hafenarbeit
Die Automatisierung führt unweigerlich zu tiefgreifenden sozioökonomischen Veränderungen. Sie eliminiert nicht einfach nur Arbeitsplätze, sondern transformiert die Anforderungsprofile radikal. Manuelle Tätigkeiten wie die von Kranführern, Lkw-Fahrern im Yard oder Laschern werden stark reduziert oder verschwinden ganz. Gleichzeitig entsteht ein hoher Bedarf an neuen, hochqualifizierten Fachkräften in den Bereichen IT, Robotik, Datenanalyse, Systemüberwachung und Instandhaltung komplexer Anlagen.Dies stellt die bestehende Belegschaft vor eine enorme Herausforderung. Proaktive und umfassende Strategien zur Umschulung und Weiterqualifizierung sind daher nicht nur eine Frage der sozialen Verantwortung, sondern eine wirtschaftliche Notwendigkeit, um den neuen Fachkräftebedarf decken zu können. Ohne qualifiziertes Personal zur Wartung und Steuerung können die teuren Anlagen ihr Potenzial nicht entfalten.Eine entscheidende Rolle spielt dabei die Sozialpartnerschaft. Eine frühzeitige, transparente und ehrliche Kommunikation mit den Gewerkschaften und Arbeitnehmervertretungen ist unerlässlich, um Widerstände abzubauen und den Wandel konstruktiv zu gestalten. Gemeinsam entwickelte Konzepte zur sozialen Abfederung des Übergangs, zur Beteiligung an den Produktivitätsgewinnen und zur Gestaltung der neuen Arbeitsplätze können aus potenziellen Gegnern Partner der Transformation machen und sind ein entscheidender Erfolgsfaktor für eine reibungslose Implementierung.
Digitale Risiken: Cybersicherheit im hypervernetzten Hafen
Mit der zunehmenden Vernetzung und der Abhängigkeit von digitalen Steuerungssystemen entsteht eine neue, kritische Verwundbarkeit: die Gefahr von Cyberangriffen. Ein hochautomatisierter Terminal ist ein attraktives Ziel für Hacker, Saboteure oder staatliche Akteure. Ein erfolgreicher Angriff auf das zentrale Terminal Operating System könnte den gesamten Hafenbetrieb lahmlegen und hätte katastrophale Auswirkungen auf die globalen Lieferketten.Dies erfordert ein fundamentales Umdenken in der Sicherheitsstrategie. Es bedarf robuster, mehrschichtiger Cybersicherheitsarchitekturen, die sowohl die IT- als auch die OT-Systeme (Operational Technology) umfassen. Konzepte wie eine “Collective Defense Strategy”, bei der Hafenbehörden, Terminalbetreiber und Sicherheitsbehörden Informationen austauschen und gemeinsam auf Bedrohungen reagieren, werden zur Notwendigkeit. Kontinuierliche Überwachung, regelmäßige Penetrationstests und die Schulung des Personals im Umgang mit digitalen Bedrohungen sind keine optionalen Extras mehr, sondern integraler Bestandteil des Risikomanagements in einem Hafen 4.0.
Das Container-Terminal als Logistik-Betriebssystem
Die Analyse zeigt, dass die Weiterentwicklung von flachen Container-Yards zu vertikalen, KI-gestützten Hochregallagern keine inkrementelle Verbesserung ist, sondern eine fundamentale Neuarchitektur der Funktion eines Container-Terminals. Die Containerstellfläche wandelt sich von einem physischen Ort zur Lagerung von Gütern zu einem hochleistungsfähigen, datengesteuerten “Logistik-Betriebssystem”. Die traditionellen Wettbewerbsfaktoren wie reiner Umschlagpreis oder maximale Geschwindigkeit treten in den Hintergrund. An ihre Stelle rücken neue, strategische Imperative: Planbarkeit, Zuverlässigkeit, Resilienz und Nachhaltigkeit. Ein Terminal, der eine Lkw-Abfertigung auf die Minute genau garantieren kann, ist für die moderne Logistik wertvoller als einer, der zwar theoretisch schneller, aber in der Praxis unberechenbar ist. Der strategische Ausblick geht sogar noch weiter. Das Hochregallager ist wahrscheinlich nicht der Endpunkt der Entwicklung. Radikalere Konzepte wie die Untergrund-Containerlogistik (Underground Container Logistics, UCL), bei der Container in einem unterirdischen Röhrensystem vollautomatisch zwischen verschiedenen HRL-Knotenpunkten, dem Kai und dem Hinterlandanschluss transportiert werden, sind bereits in der Entwicklung. In einem solchen Szenario würde der Containerverkehr vollständig von der Oberfläche verschwinden. Das HRL wäre dann nicht mehr die Gesamtlösung, sondern ein entscheidender Baustein in einem zukünftigen, dreidimensionalen, vollständig integrierten Logistik-Ökosystem.
Für die beteiligten Akteure ergeben sich daraus klare strategische Handlungsempfehlungen:
Für Hafenbetreiber und Investoren: Der Fokus muss sich von den reinen Investitionskosten (CAPEX) auf die Gesamtbetriebskosten (Total Cost of Ownership, TCO) und den strategischen Wert von Zuverlässigkeit und Flächeneffizienz verlagern. Investitionen in die Standardisierung von Prozessen und die Entwicklung des Personals müssen der technologischen Implementierung vorausgehen.
Für die Politik und Regulierungsbehörden: Die Aufgabe besteht darin, diese Transformation zu ermöglichen und zu beschleunigen. Dies erfordert die Schaffung unterstützender regulatorischer Rahmenbedingungen, die Förderung von Forschung und Entwicklung, die Finanzierung von Qualifizierungsprogrammen und die Etablierung internationaler Standards für den Datenaustausch, um Interoperabilität zu gewährleisten.
Für die Logistikindustrie: Spediteure, Reedereien und Bahnbetreiber müssen sich auf eine neue Ära hyper-effizienter, planbarer und datentransparenter Hafenschnittstellen einstellen. Diese werden neue Geschäftsmodelle ermöglichen, die auf einem bisher unerreichten Niveau der Lieferkettenintegration basieren und die Vision eines nahtlosen, intelligenten und nachhaltigen globalen Güterverkehrs in greifbare Nähe rücken.
Wir sind für Sie da - Beratung - Planung - Umsetzung - Projektmanagement
☑️ Unsere Geschäftssprache ist Englisch oder Deutsch
☑️ NEU: Schriftverkehr in Ihrer Landessprache!
Gerne stehe ich Ihnen und mein Team als persönlicher Berater zur Verfügung.
Sie können mit mir Kontakt aufnehmen, indem Sie hier das Kontaktformular ausfüllen oder rufen Sie mich einfach unter +49 89 89 674 804 (München) an. Meine E-Mail Adresse lautet: wolfenstein∂xpert.digital
Ich freue mich auf unser gemeinsames Projekt.