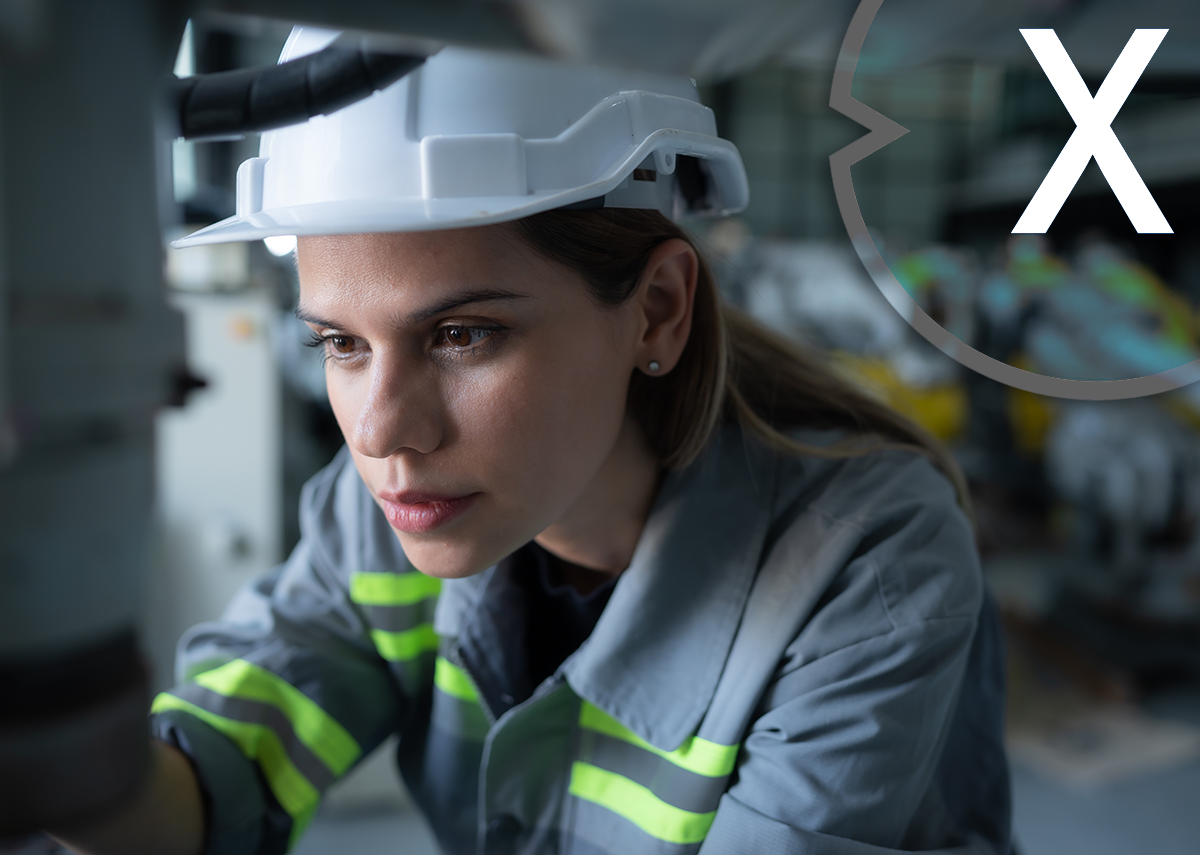
Systems for testing agent calibration, test equipment for product measurement, thread drive and positioning tables – Image: Xpert.digital
Test equipment calibration: Accuracy through calibration systems 📏
Calibration of test equipment, product measurement and the use of screw drives and positioning tables are essential aspects in various industrial areas. They play a key role in ensuring product quality, accuracy of measurements and precise positioning of components. In this section, we will delve into these topics in depth and highlight the importance and current developments in these areas.
🛠️ Systems for test equipment calibration
Calibration of test equipment is a fundamental step in ensuring the accuracy of measurements. It ensures that measuring instruments such as calipers, micrometers and other testing equipment deliver correct results. Measuring deviations can be detected and corrected through regular calibration. This is particularly important in industries such as manufacturing, medical technology and aviation.
Current developments in calibration technology enable automated calibration processes that increase efficiency and minimize human error. Companies rely on advanced software solutions that store calibration data and provide analytics for better process optimization. These systems increase quality control and reduce waste.
📏 Test equipment for product measurement
The precision of product measurements is critical to ensuring products meet established specifications. Testing equipment such as coordinate measuring machines (CMMs) enable highly precise measurements of three-dimensional components. This technology is used in the automotive industry, aerospace and electronics production.
Modern testing equipment is equipped with non-contact measuring technology, which enables quick and accurate measurements. The integration of optical sensors and laser technology enables the measurement of complex shapes and geometries. By using advanced software, measurement data can be analyzed and visualized in real time, improving quality control.
🔩 Screw drives and positioning tables
Screw drives and positioning tables are widely used in machines and systems to enable precise movements and positioning. They find application in CNC machines, robots, optical systems and more. Choosing the correct thread type and the design of the positioning table are crucial for the accuracy and repeatability of the movements.
Modern screw drives use advanced materials and manufacturing techniques to minimize friction and wear. This increases the service life of the components and contributes to the consistency of the movements. By using stepper motors or servo motors, precise motion profiles can be created, which is of great importance in applications such as automated manufacturing.
📝 Highest quality and precision
In today's highly competitive industrial world, systems for test equipment calibration, test equipment for product measurement as well as screw drives and positioning tables are indispensable to ensure the highest quality and precision. Automated calibration processes, non-contact measurement technology and advanced thread technologies help to optimize production processes and minimize waste.
The constant development of these technologies opens up new opportunities for companies to improve their products and develop innovative solutions. The precise control of measurements and movements makes it possible to meet the highest standards even in demanding applications.
📣 Similar topics
- Test equipment calibration: Accuracy through calibration systems
- Product measurement: precision in quality control
- Screw drives and positioning tables: precise movements for automation
- Automated calibration processes: increasing efficiency through technology
- Optical measurement technology: Non-contact precision in product measurement
- Materials and manufacturing techniques: Longevity and consistency in screw drives
- Industrial applications: Areas of application for positioning tables and screw drives
- Future prospects: innovation potential in measurement technology and positioning
- Man vs. Machine: The Role of Automation in Calibration
- Increasing quality in production: technological developments in focus
#️⃣ Hashtags: #Precision Technology #Industrial Measurement #AutomatedCalibration #Quality Control #InnovativeManufacturing Technologies
Coordinate measuring machines (CMMS) – precision in every dimension 📏
Coordinate measuring machines (CMMS – Coordinate Measuring Machines) are essential tools in the modern manufacturing industry, which are indispensable for precise measurements and quality control. These highly developed machines make it possible to measure complex components three -dimensionally and ensure that they meet the specified specifications. Let us take a closer look at this fascinating technology and find out how it revolutionized the industry.
🌐 The importance of CMMs in the industry
Coordinate measuring machines (CMMs) are crucial in numerous industries. From the automotive to aerospace industries to medical technology, CMMs are used to ensure the precision and quality of products. They enable the precise measurement of complex geometries, which is indispensable in many applications.
⚙️ How CMMs work
The way CMMs work is based on a sophisticated system of sensors, movement units and software. The component is placed on the measuring machine and high-precision sensors take measurements in three dimensions. The software processes the measurement data and creates an accurate digital model of the component. This model can then be compared with the CAD data to identify deviations.
🔍 Areas of application of CMMs
CMMs are used in a variety of applications:
- Automotive industry: CMMs are used in vehicle manufacturing to ensure that components such as engines, body panels and transmissions adhere to specified tolerances.
- Aerospace: Here CMMs play a crucial role in the production of aircraft components. They ensure that these parts can withstand the extreme stresses of flight.
- Medical technology: Precision is essential in medical technology. CMMs are used to secure implants, prostheses and medical devices.
- Electronics industry: CMMs are used in the production of circuit boards and electronic components to ensure accurate placement of components.
📈 The future of CMM technology
CMM technology is constantly evolving. New sensors, improved software and automation functions make CMMs even more powerful and efficient. The integration of artificial intelligence makes it possible to carry out measurements faster and more precisely and to minimize errors.
🌟 Highest quality standards – precision and versatility
Coordinate measuring machines (CMMs) are without a doubt a cornerstone of the modern manufacturing industry. They ensure that the products that shape our everyday lives meet the highest quality standards. With their precision and versatility, CMMs help drive innovation and increase efficiency in production.
📣 Similar topics
- The evolution of measurement technology: coordinate measuring machines through the ages
- How CMMs are shaping the automotive industry: precision from engines to body parts
- Aerospace: CMMs as guarantees for safe flights
- Medical technology and CMMs: precision for a better life
- Electronics production: How CMMs ensure the quality of circuit boards
- Artificial intelligence and CMMs: The future of precise measurement technology
- Increased efficiency through CMM automation: faster measurements, fewer errors
- Cross-application precision: CMMs in various industrial sectors
- Practical insights: How CMMs are used in manufacturing
- On the way to perfection: The continuous development of CMMs**
#️⃣ Hashtags: #measurement technology #quality control #industrial precision #manufacturing innovation #future technology
Test equipment calibration
Gauge calibration is an important process in various industries to ensure that the measuring devices or gauges used in a company provide accurate and reliable results. Test equipment can be anything from simple hand tools to highly specialized measuring devices used in production, laboratory or quality control environments.
Calibration of test equipment involves comparing a measuring instrument with a known standard reference or calibration standard. This comparison serves to check the accuracy and reliability of the instrument being calibrated and to adjust it if necessary. The goal of calibration is to ensure that the measurements made with a particular test equipment are as close as possible to the actual physical properties or magnitudes.
The calibration process can include various steps:
- Selection of calibration standards: Selection of reference standards or devices that have a higher accuracy than the test equipment to be calibrated.
- Carrying out the calibration: The test equipment to be calibrated is compared with the calibration standard and deviations are measured.
- Adjustment or adjustment: If the test equipment has deviations, it may be necessary to adjust or adjust it to make it more accurate.
- Calibration certificate: After successfully completed calibration, the test equipment receives a calibration certificate. This document contains information about the test equipment tested, the calibration standards used, the measured deviations and the validity period of the calibration.
- Periodic Repetition: Test equipment should be calibrated regularly to ensure that its accuracy is maintained over time. The frequency of calibration depends on various factors such as the type of test equipment, frequency of use and industry standards.
Gauge calibration is particularly important in industries such as manufacturing, automotive, aerospace, healthcare, environmental protection and many others where accurate measurements contribute to quality assurance, product compliance or safety. Calibrated test equipment ensures that manufactured products meet the required standards and prevents potential problems caused by inaccurate measurements.
Screw drives and positioning tables
Screw drives and positioning tables are mechanical systems used in many industrial applications to provide precise linear movement or positioning. They play an important role in areas such as manufacturing automation, measurement technology, the semiconductor industry, medical technology and many others.
Screw drives
A screw drive is a mechanism that converts rotary motion into linear motion or vice versa. It usually consists of a threaded spindle and a nut. The lead screw is an elongated rod with a spiral thread, while the nut is a component with a matching internal thread. As the spindle is rotated, the nut moves along the spindle, creating linear motion. The pitch of the thread determines the distance the nut moves per revolution of the spindle, which is called mechanical advantage.
There are different types of screw drives including:
- Spindle screw drives: Here the spindle and nut are separate components. They are particularly suitable for applications where high precision is required.
- Trapezoidal screws: These have a trapezoidal thread profile and are often used in higher load applications.
- Ball screws: Here the thread is rolled by balls, resulting in lower friction loss and higher efficiency. They are used for high-precision and fast positioning.
Positioning tables
A positioning stage, also known as a linear positioning stage or positioning platform, is a mechanical device that allows objects to move along a straight line. It consists of a frame on which one or more movable axes are mounted. Each axis can be driven by a screw, ball screw or other mechanisms. Positioning tables can be controlled manually, motorized or even automated depending on the requirements of the application.
Positioning tables are often combined with precision measurement systems to ensure accurate positioning and repeatability. They find application in areas such as:
- Manufacturing: In the manufacturing industry, positioning tables are used to precisely machine, assemble or inspect workpieces.
- Optics and microscopy: Positioning stages are used in optical systems, microscopes and telescopes to precisely align samples or lenses.
- Semiconductor manufacturing: Microchip manufacturing uses positioning tables to precisely position and move wafers and components.
- Medical technology: In medical imaging devices and robotic systems, positioning tables are important to enable precise movements of instruments or sensors.
Screw drives and positioning tables play a crucial role in precision and automation technology and help various industries to work efficiently and accurately.
Test equipment for product measurement
Product measurement test equipment is an instrument or device used in various sectors and industries to check the precise dimensions, properties and quality of manufactured products. These test tools are crucial to ensure that products meet established specifications and quality standards. Here are some examples of test equipment for product measurement:
- Caliper: A measuring tool used to precisely measure lengths, diameters, widths and depths of objects.
- Dial Indicator: An instrument used to measure small variations or tolerances in a product. It is often used in quality control.
- Micrometer: Also called a caliper, a micrometer takes very precise length and thickness measurements.
- Coordinate Measuring Machine (CMM): An automated system that measures the 3D coordinates of a product to ensure it meets design specifications.
- Surface roughness measuring device: Used to measure the surface roughness of a product and ensure that it meets the requirements.
- Hardness tester: Determines the hardness of a material, which indicates its mechanical strength.
- Ultrasonic flaw detector: Uses ultrasonic waves to detect internal defects or inaccuracies in materials.
- X-ray inspection device: Uses X-rays to see inside products and detect irregularities, cracks or defects.
- Visual Inspection Device: A visual inspection tool that can be used to inspect surface features, colors, shapes and other external aspects.
- Mass spectrometer: Used in laboratories to analyze the chemical composition of materials to ensure they meet requirements.
- Colorimeter: Measures the color of a product and compares it to a set color standard.
- Volumetric Test Equipment: Used in the food industry to accurately measure the volume of liquids or granules.
These test tools are used to ensure the quality of products, minimize defects and ensure that they meet customer requirements or industry standards. Choosing the right test equipment depends on the type of product, the specific requirements and the quality standards that apply in a particular industry.
Systems for test equipment calibration
Test equipment calibration systems are important components in various industries to ensure that measuring instruments and test equipment deliver accurate and reliable results. Calibration refers to the process by which the accuracy and reliability of measuring instruments and test equipment are checked and, if necessary, adjusted to ensure that they meet established standards. Here are some key aspects of equipment calibration systems:
- Calibration standards: Test equipment calibration systems are based on international or industry-specific standards. These standards define the precise requirements for measurement accuracy, procedures and tolerances.
- Calibration Laboratories: In many cases, calibrations are performed by specialized laboratories that have the necessary equipment, expertise, and reference standards to perform accurate calibrations.
- Calibration procedure: Calibration is carried out by comparing the measuring instrument or test equipment with a reliable reference standard. Measured values are recorded and deviations are analyzed.
- Calibration intervals: Depending on the requirements and area of application of the measuring instrument or test equipment, specific calibration intervals are specified. Some instruments require frequent calibrations, while others require calibration less frequently.
- Documentation: During the calibration process, accurate records are created of the steps taken, measurements, deviations and adjustments. This ensures the traceability and traceability of the calibration results.
- Certificates: A calibration certificate is often issued after successful calibration. This certificate contains information about the instrument tested, the procedures used, the reference standards and the accuracy achieved.
- Automation: Modern technologies enable the automation of calibration processes. Automated calibration systems can make the process more efficient and minimize human errors.
- Traceability: An important property of calibrations is the traceability of the results to national or international standards. This ensures that the accuracy of the calibration can be verified.
- Software support: There are specialized software solutions that make it easier to plan, perform and manage calibrations. This software can manage calibration intervals, send reminders when calibrations are due, and store data for later analysis.
- Quality Control: Calibrations are an integral part of quality control systems. They ensure that the products manufactured or measurements carried out meet the required standards.
The requirements for test equipment calibration systems vary depending on the industry, area of application and legal regulations. However, calibrations are crucial in many areas to ensure accurate and reliable measurements.