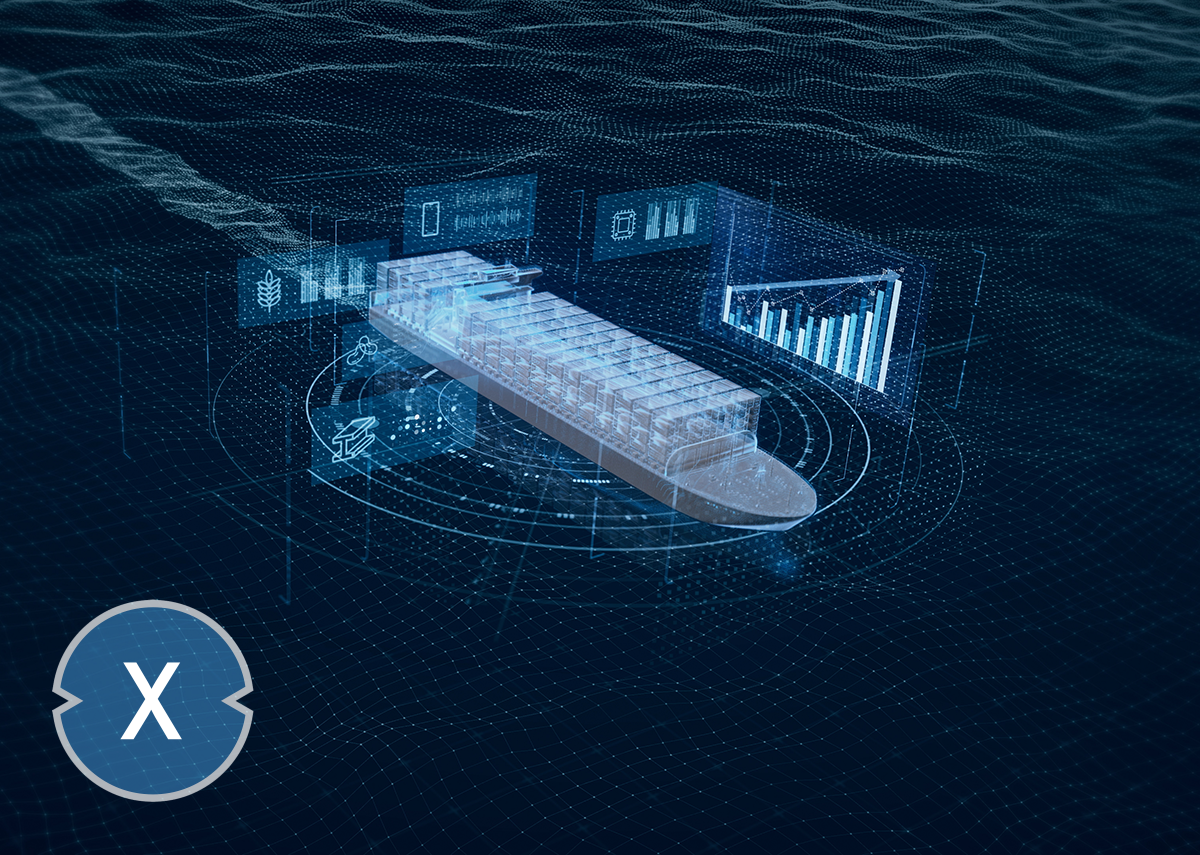
New logistics strategies, among other things with digital twins and artificial intelligence (machine learning) – Image: Xpert.digital / Keyfame | Shutterstock.com
In 2011, “Stres test” was elected by the Society for German Language (GfDS) as the word of the year. It denotes a test that measures the resilience and the associated and growing stress of physical or psychological way of reaction to an event. The media gained greater awareness in relation to the stress tests of nuclear power plants, intermediate storage, but also for banks and the Stuttgart 21 rail project.
A crisis plan for the economy?
What is interesting here is that a so-called national pandemic plan for Germany was first published in 2005 and was last updated in March 2017. It was the response to the 2002/2003 SARS pandemic and the global spread of H5N1. In addition to the measures against the spread of a pandemic pathogen, the country's infrastructure should also be maintained.
With regard to influenza, the World Health Organization (WHO) in its recently revised guidelines for Pandemic Influenza Risk Management determined that the general director of the WHO is calling for a pandemic – i.e. the transition from an epidemic to – .
However, possible scenarios for a collapse of global supply chains and an international catalog of measures aimed at reducing and bridging global consequences have not yet been identified. The corona pandemic stopped the supposedly golden age of globalization that was being pushed forward with the ostrich tactic. Even ecologically contradictory aspects were pushed into the background. Any objective stress test would have highlighted the sensitive supply chains and their ecological weak points.
With growing ecological awareness (reducing greenhouse gas emissions) and the outbreak of the corona pandemic, it is now clear to everyone that things cannot continue like this. While some people still hoped that the pandemic would resolve itself quickly like an annual flu wave, we are now already in the second year of the pandemic and looking beyond the third year, a possible way out is still not in sight.
Example steel and aluminum
Even if the supply chains were temporarily broken here and there and raw materials for further processing were missing, national and international logistics have so far mastered the crisis quite well. However, this was also reflected in the prices. Many goods and raw materials have become expensive or are taking a long time to arrive. For example, B. steel and aluminum prices rose, which, among other things, also had a negative impact on the expansion of renewable energies. In September 2021, the aluminum price reached its highest level in the eight-year observation period.
The steel industry has always been one of the most important key industries on which many industries depend. Steel is therefore an important indicator of economic and economic developments. Even if prices are moving downwards at the moment, further developments and the effects of the Omicron variant of the corona pandemic are still unclear.
A strategy and planning security look different. In short, the pandemic is exposing our fragile global supply chain. It is becoming increasingly obvious that the weakest link in globalization and the global economy is supply chains and we need to consider new logistics strategies. You failed the acute stress test.
Take advantage of the opportunity now and bring the supply chain back to Europe
Ok, production and labor costs are lower in China than in Germany. And that products consist of many individual parts and work steps such as: It is obvious, for example, that smartphones cannot currently be produced competitively in Germany. But what use is this advantage to me if, as is currently the case, transport costs with container ships are skyrocketing and then the goods can either be delivered late or are currently not available?
At the latest when the 400 -meter -long and 59 meter wide freighter “Ever Given” made March 2021 in the Suez Canal, everyone had to be clear that there was a sensitive area in the global supply chain. So a mistake or bug in the system. The after -effects until such a global supply chain management gets rolling again or works somewhat again, because it is time for weeks. In times of Corona pandemic, however, the disorders in the global supply chain increased to adapt the supply chain management to the circumstances and react accordingly flexibly.
On the other hand, possible risks for a “disorder in the supply chain” were not entirely unknown. Already in 2015 there was the “Risk & Resilience” study (from DHL) for resistant logistics . A possible pandemic has not been mentioned, but there is talk of cyber attacks, protectionism or political escalations, which represent an additional and real disruptive potential in the same or greater extent to the current corona pandemic.
Around 12% of global cargo and approximately 30% of the world's containers pass through the Suez Canal. The Suez Canal is the most important waterway in the world, ahead of the Panama Canal.
Now the prices of containers have risen sharply, in some cases by 500% or more compared to the previous year. The demand for container deliveries has shot through the roof because there is no longer any passenger air traffic, which was used to transport some of the goods. It is assumed that air freight transport options will not recover any time soon.
This in turn leads to traffic jams in front of American and European ports. In November, 400 to 500 container ships were anchored at their destination, which can only be processed slowly due to the high demand for containers and the lack of port staff capacity. This in turn means that the containers used are needed for longer and thus the container prices have also risen. In short: there is a shortage of containers.
German companies want to change supply chains. 68% of affected companies have already taken appropriate measures to get the situation under control as quickly as possible:
- 47% are looking for new or additional suppliers
- 41% want to increase storage capacity
- 22% distribute suppliers to several countries
- 12% are working on shortening delivery routes
- 11% plan to relocate production in-house
Source: DIHK, Going Global 2021
World logistics – resistant logistics
A March 2020 survey of 2,900 senior management respondents found the following:
- 52% of respondents said changes are being made to global supply chains as a result of global events.
- 40% plan to reassess
- and only 8% see no need for change.
- Almost 40% of companies surveyed also said they were planning changes to their workforce.
- 36% are planning a further approach to automation,
- 41% are considering revising the current speed of their automation.
Industry 4.0 technologies will significantly change the supply chain
The current changes and adjustments to supply chains are based on the ability to deliver. Anyone who cannot deliver is currently not competitive. The price plays a secondary role.
When the market stabilizes again, the costs will be in the foreground again. Then the consideration is in the room to accept the next disorder in the global supply chain or to have switched World logistics – resistant logistics
In order to make this sustainable and competitive, it is important to seize the opportunity and promote the expansion of Industry 4.0 technologies:
Internet of Things (IoT) – The new mobile phone standard 5G only enables the IoT. It opens up new perspectives like investors, especially for the Smart Factory area
Competitive by reducing costs with automation and networking of storage systems
Electricity self-consumption optimization through to autonomous power supply
- Electricity self-consumption optimization
- Background knowledge of oil, CO2 tax and renewable energies – energy transition
Robotics & automation in industry and logistics are already bringing supply chains back to important regional locations. This also includes buffer warehouses, local warehouses, decentralized logistics centers such as micro-hubs.
- Germany is a leader in robotics
- Robotics & automation in the warehouse
- Local decentralized hubs – logistics centers
- Micro hub – the key-genial solution?
- Buffer camp in intralogistics – the solution to secure the supplies
Use of digital twins
Another important form of the Industry 4.0 world is the use of digital twins.
A digital twin is part of process automation (and belongs to the broader and emerging category of “hyperautomation”).
The digital twin is changing the entire product lifecycle management, from design to manufacturing to service and operations. Product lifecycle management is very time-consuming in terms of efficiency, manufacturing, intelligence, service phases and sustainability in product design. A digital twin can bring together the physical and virtual space of the product and extremely shorten the time required.
The digital twin enables companies to create a digital footprint of all their products, from design to development and throughout the product lifecycle.
In the manufacturing process, the digital twin is a virtual replica of real-time processes in the factory. Thousands of sensors are placed throughout the physical manufacturing process, all collecting data from different dimensions, such as: B. Environmental conditions, behavioral characteristics of the machine and work carried out. All of this data is continuously transmitted and collected by the digital twin. Thanks to the Internet of Things, digital twins have become more affordable and could determine the future of manufacturing.
As a result, digital twins offer great business potential as they predict the future instead of analyzing the past of the manufacturing process.
Another example comes from the healthcare industry: “Healthy” used to be considered the absence of signs of illness. With a digital twin, “healthy” patients can be compared to the rest of the population to define truly healthy.
3-D Visualization: Digital Zwilling – Digital Twin – Image: Xpert.digital / Chesky | Shutterstock.com
Suitable for:
Digital transformation – numbers from Italy
The question was formulated as follows: "If you look at all areas of your company, in which of the following innovative digital projects have you already invested in 2019 / will you invest 2020?"
Projects for digital transformation carried out by companies in Italy in 2019 – according to areas
Projects for digital transformation – Image: Xpert.digital carried out by companies in Italy in 2019
In 2019, 40 percent of companies surveyed in Italy implemented digital marketing or social media campaigns, while 35 percent of companies launched projects using big data technologies. Virtual and augmented reality still seem to be a niche area for Italian companies, as only seven percent of them implement projects in this area.
Have you carried out projects in any of the following areas in the past year?
- Digital marketing/social media/digital marketing/social media – 40 %
- Big Data Technologies / Big Data Technologies – 35 %
- Cloud Computing (SaaS) / Cloud Computing (SaaS) – 33 %
- Software development innovation (Agile, DevOps) / Software Dev Innovation (Agile, DevOps) – %
- Cloud Computing (IAAS, PAAS) / Cloud Computing (IAAS, PAAS) – 28 %
- Artificial intelligence / machine learning / Artificial Intelligence / Machine Learning – 26 %
- Multi -channel customer loyalty / multichannel customer commitment – 21 %
- Extended / predicting analysis / advanced / predictive analytics – 18 %
- RPA (robot -based process automation) / RPA (Robotic Proces Automation) – 18 %
- Internet of Things (IoT, M2M) / Internet of Things (IoT, M2M) – 17 %
- Enterprise app store, MDM, MAM / Enterprise Appstore, MDM, MAM – 15 %
- Blockchain / Blockchain – 11 %
- Wearable technology / Wearable Tech – 8 %
- Extended / virtual reality / augmented / virtual reality – 7 %
- Digital twin / digital twin – 3 %
Companies that implement digital transformation processes in Italy in 2020 – according to areas
According to a 2019 survey, 32 percent of companies surveyed will undertake software development innovation projects in 2020. Digital marketing and big data appear to be more attractive areas, with 50 and 36 percent of companies planning projects in these areas, respectively. Finally, 39 percent of Italian companies planned to invest resources in cloud computing.
Will you be doing projects in any of the following areas this year?
- Digital marketing / social media / digital marketing / social media – 50 %
- Big data technologies / big data technology – 36 %
- Cloud Computing (SaaS) / Cloud Computing (SaaS) – 39 %
- Software development innovation (Agile, DevOps) / Software Dev Innovation (Agile, DevOps) – %
- Cloud Computing (IAAS, PAAS) / Cloud Computing (IAAS, PAAS) – 31 %
- Artificial intelligence / machine learning / Artificial Intelligence / Machine Learning – 44 %
- Multi -channel customer loyalty / multichannel customer commitment – 30 %
- Extended / predicting analysis / advanced / predictive analytics – 29 %
- RPA (robot -based process automation) / RPA (Robotic Proces Automation) – 25 %
- Internet of Things (IoT, M2M) / Internet of Things (IoT, M2M) – 27 %
- Enterprise app store, MDM, MAM / Enterprise Appstore, MDM, MAM – 17 %
- Blockchain / Blockchain – 18 %
- Wearable technology / Wearable Tech – 8 %
- Extended / virtual reality / augmented / virtual reality – 12 %
- Digital twin / digital twin – 7 %
Smart Factory – Implementation in German companies
In 2019, 48 percent of the companies surveyed, which are predominantly active in mechanical and plant engineering as well as in the electrical and automotive industries, stated that they were pursuing individual operational projects related to Industry 4.0. Four years earlier it was 31 percent.
Around 70 percent of the companies surveyed are in the mechanical and plant engineering, electrical and automotive industries.
2015: How far is your company on the way to the “smart factory”?
- We pursue operational individual projects in terms of industry 4.0 – 31 %
- The topic is in our observation and analysis – 36 %
- The topic is with us in the planning and test – 5 %
- We have not yet dealt with it in concrete terms – 19 %
- Industry 4.0 is fully operated by us – 4 %
- No answer – 5 %
2017: How far is your company on the way to the “smart factory”?
- We pursue operational individual projects in terms of industry 4.0 – 41 %
- The topic is with us in the observation and analysis – 24 %
- The topic is with us in the planning and test – 14 %
- We have not yet dealt with it in concrete terms – 8 %
- Industry 4.0 is fully operated by us – 7 %
- No answer – 6 %
2019: How far is your company on the way to the “smart factory”?
- We pursue operational individual projects in terms of industry 4.0 – 48 %
- The topic is in our observation and analysis – 21 %
- The topic is with us in the planning and test – 11 %
- We have not yet dealt with it in concrete terms – 9 %
- Industry 4.0 is fully operated by us – 8 %
- No answer – 3 %
Smart Factory – implementation of processes worldwide
In 2019, 68 percent of manufacturing companies surveyed worldwide said they were ready to implement a smart factory initiative. Two years earlier it was 43 percent. Survey of manufacturing companies from 13 countries worldwide.
2019: Are you already pursuing smart factory initiatives?
- Yes, smart factory initiatives are already running – 68 %
- No, the introduction is planned for the next year – 6 %
- No, not yet – 26 %
2017: Are you already pursuing smart factory initiatives?
- Yes, smart factory initiatives are already running – 43 %
- No, the introduction is planned for next year – 33 %
- No, not yet – 24 %
Have you already introduced smart factory processes in your company?
Have you already introduced processes in the area of the intelligent factory in your company? – Image: Xpert.digital
The graphic shows the results of a global survey conducted in 2017 on processes in the area of intelligent factories. 67 percent of respondents from the industrial manufacturing sector stated that they had already introduced processes in the area of intelligent factories.
Smart Factory – introduced processes worldwide according to industries
- Industrial production – 67 %
- Aviation and defense – 62 %
- Automation and transportation – 50 %
- Energy and supply industry – 42 %
- Consumer goods – 40 %
- Bioscientific, biotech industry, pharmacy – 37 %
According to the source, the survey was conducted in eight countries (US, UK, France, Germany, Italy, Sweden, China and India).
What are the biggest challenges in smart factory strategy planning?
What are the biggest challenges in strategy planning in the field of intelligent factories? – Image: Xpert.digital
The graphic shows the results of a global survey conducted in 2017 on the biggest challenges in strategic planning in the area of intelligent factories. 32 percent of respondents said the lack of coordination between different organizational units was the biggest challenge in smart factory strategy planning.
Smart Factory – greatest challenges in strategy planning
- Lack of coordination between different organizational units – 32 %
- Lack of unity in the management team – 28 %
- A lack of clarity about business scenarios – 28 %
- Lack of ownership – 23 %
- Lack of imagination – 21 %
What are the biggest challenges in implementing smart factory strategies?
The graphic shows the results of a global survey conducted in 2017 on the biggest challenges in introducing strategies in the area of smart factories. 29 percent of respondents said lack of investment was the biggest challenge in adopting smart factory strategies.
Smart Factory – greatest challenges in the introduction of strategies
- Lack of investments – 29 %
- A lack of maturity in automated manufacturing processes – 22 %
- Organizational inertia – 21 %
- Challenges in the identification and prioritization of opportunities – 21 %
- Missing strategies – 20 %
Which of the following predictive maintenance applications do you already use?
In 2019, 37 percent of the companies surveyed, which are predominantly active in mechanical and plant engineering as well as in the electrical and automotive industries, stated that they use automated tracking and display of the due dates of regular maintenance work. Around 70 percent of the companies surveyed are in the mechanical and plant engineering, electrical and automotive industries.
Smart Factory – Use of Predictive Maintenance applications in Germany
- Automated persecution and display of the due date of regular maintenance work – 37 %
- Optimize the quality of the manufactured products in a targeted manner – 28 %
- Recognize wear in good time and automatically (predictive maintenance) – 28 %
- Optimize setting processes – 25 %
- Avoid incorrect operation – 25 %
- Recognize bad processing processes – 23 %
- Show armor errors – 13 %
- We do not use predictive maintenance applications – 38 %
Use of connectivity technologies and analytics in manufacturing 2017-2022
In 2017, the most used connectivity and analytics technology in manufacturing was data-driven resource optimization. It was predicted that this technology will also be the most used technology by 2022. However, the fastest growing technology between 2017 and 2022 will be predictive maintenance. It is predicted that by 2022, approximately 66 percent of manufacturers will have implemented predictive maintenance in their operations.
Use of connectivity technologies and analytics by manufacturers in 2017
- Data-based resource optimization / data-enabled resource optimization – 77 %
- Integrated planning / Integrated Planning – 61 %
- Big-Data controlled process and quality optimization / big data-driven process and quality optimization – 65 %
- Modular production facilities / modular production assets – 36 %
- Networked factory / connected factory – 60 %
- Forward -looking maintenance / predictive maintenance – 66 %
- Process visualization/ automation/ process visualization/ automation – 62 %
- Digital twin of the product / digital twin of the product – 43 %
- Digital twin of the factory / digital twin of the factory – 44 %
- Digital twin of the production system / digital twin of the production asset – 39 %
- Flexible production methods / flexible production methods – 34 %
- Autonomous internal logistics / autonomous intra-plant Logistics – 35 %
- Transfer of production parameters / transfer of production parameters – 32 %
- Completely autonomous digital factory / fully autonomous digital factory – 11 %
Use of connectivity technologies and analytics by manufacturers in 2022
- Data-based resource optimization / data-enabled resource optimization – 52 %
- Integrated planning / Integrated Planning – 32 %
- Big-Data controlled process and quality optimization / big data-driven process and quality optimization – 30 %
- Modular production facilities / modular production assets – 29 %
- Networked factory / connected factory – 29 %
- Forward -looking maintenance / predictive maintenance – 28 %
- Process visualization/ automation/ process visualization/ automation – 28 %
- Digital twin of the product / digital twin of the product – 23 %
- Digital twin of the Fabrik / Digital Twin of the Factory – 19 %
- Digital twin of the production system / digital twin of the production asset – 18 %
- Flexible production methods / flexible production methods – 18 %
- Autonomous internal logistics / autonomous intra-plant Logistics – 17 %
- Transfer of production parameters / transfer of production parameters – 16 %
- Completely autonomous digital factory / fully autonomous digital factory – 5 %
Where will business-to-business (B2B) technology buyers spend more or less in 2021?
The majority of business-to-business (B2B) technology buyers surveyed believe that spending on web and video conferencing, online collaboration and project management will increase in 2021. As the coronavirus (COVID-19) pandemic continues into the new year and vaccines are slow to roll out, remote working will remain the norm for the foreseeable future.
Forecasting B2B technology spending in 2021, by product and service
Additional expenses for:
- Web and video conferences / Web & Video – 64 %
- Online cooperation and project management / online collaboration & project management – 53 %
- Marketing / marketing – 41 %
- Business Intelligence / Business Intelligence – 38 %
- Customer support / customer support – 36 %
- Network solutions / Network Solutions – 33 %
- Sales / sales – 33 %
- Database management / database management – 32 %
- Product development and management / product development & management – %
- Other IT / other IT – 27 %
- Other hardware / other hardware – 23 %
- Professional services / professionally services – 21 %
- Router and switch / routers and Switches – 20 %
- Financial and accounting / finance and – 18 %
- Human resources / human resources – 18 %
- Vertical industry / vertical industry – 14 %
Expenses remain the same
- Web and video conferences / Web & Video – 26 %
- Online cooperation and project management / online collaboration & project management – 35 %
- Marketing / marketing – 40 %
- Business Intelligence / Business Intelligence – 43 %
- Customer support / customer support – 45 %
- Network solutions / Network Solutions – 45 %
- Sales / sales – 42 %
- Database management / database management – 52 %
- Product development and management / product development & management – %
- Other IT / other IT – 46 %
- Other hardware / other hardware – 43 %
- Professional services / professionally services – 50 %
- Router and switch / routers and Switches – 46 %
- Financial and accounting / finance and – 62 %
- Human resources / human resources – 55 %
- Vertical industry / vertical industry – 40 %
Spend less on:
- Web and video conferences / Web & Video – 7 %
- Online cooperation and project management / online collaboration & project management – 8 %
- Marketing / marketing – 15 %
- Business Intelligence / Business Intelligence – 12 %
- Customer support / customer support – 14 %
- Network solutions / Network Solutions – 14 %
- Sales / sales – 14 %
- Database management / database management – 11 %
- Product development and management / product development & management – %
- Other IT / other IT – 18 %
- Other hardware / other hardware – 25 %
- Professional services / professionally services – 22 %
- Router and switch / routers and Switches – 22 %
- Financial and accounting / finance and – 15 %
- Human resources / human resources – 20 %
- Vertical industry / vertical industry – 22 %
Not specified)
- Web and video conferences / Web & Video – 3 %
- Online cooperation and project management / online collaboration & project management – 3 %
- Marketing / marketing – 4 %
- Business Intelligence / Business Intelligence – 7 %
- Customer support / customer support – 6 %
- Network solutions / Network Solutions – 6 %
- Sales / sales – 11 %
- Database management / database management – 6 %
- Product development and management / product development & management – %
- Other IT / other IT – 9 %
- Other hardware / other hardware – 10 %
- Professional services / professionally services – 6 %
- Router and switch / routers and Switches – 12 %
- Financial and accounting / finance and – 5 %
- Human resources / human resources – 7 %
- Vertical industry / vertical industry – 23 %
If you think about the next few years, in which areas do you expect the shipping industry to receive the most stimulus from increasing digitalization in the next few years?
In 2021, the suppliers, shipowners, ship operators and shipyards surveyed expect that the areas of maintenance and fleet management will be most affected by increasing digitalization in the shipping industry. While 28 percent of suppliers and 27 percent of shipyards believe that digitalization will impact the use of remotely controlled unmanned ships, shipowners and ship operators are more skeptical.
Areas affected by digitalization in the shipping industry 2021
Provider – suppliers
- Maintenance/remote monitoring/maintenance/remote survey – 54 %
- Fleet management/performance/fleet management/performance – 49 %
- Assistance systems for optimized ship operations / Assistance Systems for Optimized Ship Operation – 45 %
- Communication (e.g. crew, logistics chain) / Communication (EG Crew, Logistics Chain) – 33 %
- Navigation/bridge management/navigation/bridge management – 33 %
- Use of unmanned ships (remote control) / use of unmanned ships (remote controlled) – 28 %
- Use of unmanned ships (completely autonomous) / use of Unmanned Ships (Completely Autonomous) – 18 %
- Digital twin / digital twin – 13 %
- Other areas / other areas – 2 %
- Do not know / do not know – 14 %
Ship owner/ship operator – Shipowners/Ship operators
- Maintenance/remote monitoring/maintenance/remote survey – 56 %
- Fleet management/performance/fleet management/performance – 63 %
- Assistance systems for optimized ship operations / Assistance Systems for Optimized Ship Operation – 57 %
- Communication (e.g. crew, logistics chain) / Communication (EG Crew, Logistics Chain) – 49 %
- Navigation/bridge management/navigation/bridge management – 40 %
- Use of unmanned ships (remote control) / use of unmanned ships (remote controlled) – 7 %
- Use of unmanned ships (completely autonomous) / use of Unmanned Ships (Completely Autonomous) – 7 %
- Digital twin / digital twin – 8 %
- Other areas / other areas – 1 %
- Do not know / do not know – 6 %
Shipping – Shipyards
- Maintenance/remote monitoring/maintenance/remote survey – 49 %
- Fleet management/performance/fleet management/performance – 43 %
- Assistance systems for optimized ship operations / Assistance Systems for Optimized Ship Operation – 55 %
- Communication (e.g. crew, logistics chain) / Communication (EG Crew, Logistics Chain) – 39 %
- Navigation/bridge management/navigation/bridge management – 33 %
- Use of unmanned ships (remote control) / use of unmanned ships (remote controlled) – 27 %
- Use of unmanned ships (completely autonomous) / use of Unmanned Ships (Completely Autonomous) – 16 %
- Digital twin / digital twin – 10 %
- Other areas / other areas – 2 %
- Do not know / do not know – 14 %
Are you looking for technical and strategic advice for supply chain optimization or warehouse optimization ? Xpert.Digital supports you!
I would be happy to serve as your personal consultant for supply chain & warehouse solutions.
You can contact me by filling out the contact form below or simply call me on +49 89 89 674 804 (Munich) .
I'm looking forward to our joint project.
Xpert.digital – Konrad Wolfenstein
Xpert.Digital is a hub for industry with a focus on digitalization, mechanical engineering, logistics/intralogistics and photovoltaics.
With our 360° business development solution, we support well-known companies from new business to after sales.
Market intelligence, smarketing, marketing automation, content development, PR, mail campaigns, personalized social media and lead nurturing are part of our digital tools.
You can find more at: www.xpert.digital – www.xpert.solar – www.xpert.plus