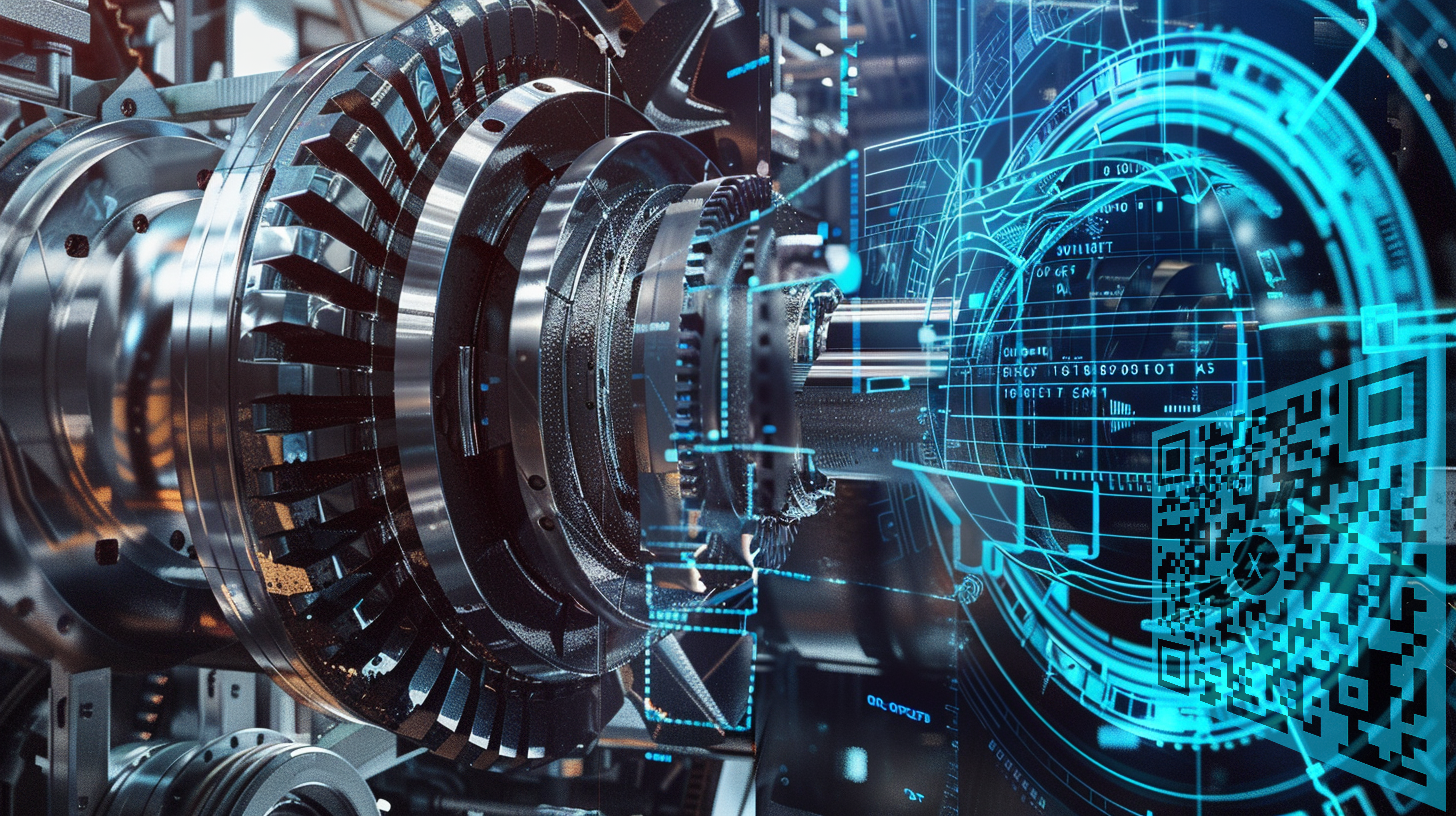
Safety -relevant components in mechanical engineering: rolling bearing with digital twin and GS1 Datamatix for optimized maintenance and reliability – creative image: xpert.digital
From trains to space travel: The central role of rolling bearings in technology and everyday life
Rolling bearings play a central role in numerous industrial and everyday applications. Their importance ranges from ensuring passenger traffic and ensuring smooth system operation to precision in aerospace. The modern world would hardly be conceivable without them, as they make a crucial contribution to making movement low in wear and friction.
Rolling bearings as safety-relevant components
In security-critical applications- – example in rail traffic, aviation or the oil and gas – the perfect function of rolling bearing components is indispensable. A defective roller bearing can have serious consequences, including:
- Unforeseen maintenance costs: An unplanned replacement of components can tie up significant financial and time resources.
- Production downtime: A plant shutdown can cause enormous costs and delivery delays.
- Personal injury and safety risks: In applications such as rail or aviation, sudden failures can cause accidents with fatal consequences.
Rolling bearings can be found wherever there is movement. They are irreplaceable for:
- Trains and cars: They ensure smooth passenger transport.
- Industrial systems: They guarantee reliability and efficiency.
- High-tech applications: From wind turbines to aircraft engines, they enable precise and reliable movements.
Schaeffler: A world-leading manufacturer of rolling bearing technology
With over 40,000 standard rolling bearing products as well as numerous customer-specific solutions, Schaeffler one of the world's largest and most innovative providers in this area. The product range extends from millimeter-sized miniature bearings for dental drills to high-temperature bearings for space travel.
Each rolling bearing has specific properties that are tailored to the respective application. This makes it all the more important that customers receive precise information about the specifications and condition of the bearings they use. This is where Schaeffler uses digital technologies to create a completely new level of transparency and maintenance efficiency.
Digitization through the GS1 DataMatrix code
A central component of Schaeffler's digital strategy is the use of the GS1 DataMatrix code. This code is engraved directly on the inner and outer ring of the rolling bearings and provides access to a digital twin of the product. The digital twin links the physical warehouse with a digital database that provides comprehensive information.
The GS1 DataMatrix code: structure and function
- Serialized GTIN: The code contains a serialized Global Trade Item Number (GTIN) that is encrypted and machine readable.
- Individual identification: Every rolling bearing can be uniquely identified worldwide.
- Data access: Customers receive access to a variety of product-related data via the code.
This technology creates complete transparency throughout the entire life cycle of a rolling bearing and enables numerous innovative applications.
Scope of data provided
The GS1 DataMatrix code gives customers access to a wide range of information, including:
1. Manufacturing data
- Place of production
- Date of manufacture
- Technical specifications
2. Operating data
- mileage
- Vibration data
- Fat analysis
3. Maintenance data
- History of maintenance performed
- Recommendations for future maintenance intervals
4. Logistics data
- Location tracking
- Supply chain information
GS1 standards and IoT
The use of GS1 standards such as the DataMatrix Code is crucial for implementing IoT solutions:
- Uniform identification: GS1 identification numbers enable objects, machines and people to be clearly identified.
- Interoperability: GS1 standards act as a common language for data exchange between different systems and companies.
- Linking to digital twins: The GS1 Digital Link allows physical objects to be connected to their digital representations.
Advantages of the digital twin
Linking physical products with a digital twin offers numerous advantages for manufacturers, operators and maintenance service providers. Key benefits include:
- Complete traceability: Every rolling bearing can be seamlessly tracked from the manufacturing process to the end of its life cycle.
- Predictive maintenance: Using the operational data collected, potential problems can be identified and resolved before failures occur.
- Optimized maintenance intervals: Using the collected data, maintenance cycles can be precisely adjusted to the actual load.
- Cost reduction: Significant savings can be achieved by avoiding unplanned downtime and making maintenance processes more efficient.
- Greater reliability: Improved monitoring options contribute to safety, particularly in rail transport and other safety-critical areas.
Innovative service offerings
By using the digital twin, Schaeffler has created the basis for a range of innovative services. An example of this is the so-called 100% return service. This service enables professional reconditioning of rolling bearing components, which regain their full performance thanks to comprehensive data documentation.
Digitalization in the railway industry: A pioneer
An outstanding example of the use of these technologies is the railway industry. Here, Schaeffler is pushing ahead with digitalization and creating significant advantages for operators and manufacturers. “We are setting new standards for transparency and efficiency in the maintenance of rail vehicles,” emphasizes a company spokesman. Networking the physical components with digital data not only increases operational safety, but also increases the reliability of the entire fleet.
Data Matrix Code (DMC): Sustainability and Efficiency
The integration of digital technologies such as the GS1 DataMatrix code and the digital twin also supports the industry's sustainability goals. Through the precise control of maintenance processes and the possibility of remanufacturing components, the service life of products is extended, which conserves resources and reduces environmental impact.
In addition, the use of data-based solutions sets new standards in the industry. The continuous analysis of operational data makes it possible to optimize existing processes and drive innovation. In this way, Schaeffler not only creates added value for its customers, but also positions itself as a pioneer in digital transformation.
Schaeffler impressively shows how traditional technologies such as rolling bearings can be redefined through the use of digital solutions. With the GS1 DataMatrix code and digital twin, the company is setting new standards in reliability, efficiency and sustainability. The connection between the physical and digital worlds not only creates advantages for manufacturers and operators, but also increases security and reliability in safety-critical applications.
Digitalization not only offers technological advantages, but is also an important step towards a more sustainable and efficient industry. With innovative approaches and a clear vision for the future, Schaeffler remains an indispensable partner for companies in all areas where movement plays a role.
Suitable for:
Our recommendation: 🌍 Limitless reach 🔗 Networked 🌐 Multilingual 💪 Strong sales: 💡 Authentic with strategy 🚀 Innovation meets 🧠 Intuition
From the bars to global: SMEs conquer the world market with a clever strategy – Image: Xpert.digital
At a time when a company's digital presence determines its success, the challenge is how to make this presence authentic, individual and far-reaching. Xpert.Digital offers an innovative solution that positions itself as an intersection between an industry hub, a blog and a brand ambassador. It combines the advantages of communication and sales channels in a single platform and enables publication in 18 different languages. The cooperation with partner portals and the possibility of publishing articles on Google News and a press distribution list with around 8,000 journalists and readers maximize the reach and visibility of the content. This represents an essential factor in external sales & marketing (SMarketing).
More about it here:
Safety-relevant components and their importance for mechanical engineering
The role of safety components and rolling bearings
Safety-relevant components play a crucial role in mechanical engineering, as their failure can have devastating consequences. Rolling bearings in particular are of great importance in almost all areas of industry because they enable movements and are installed in both small precision devices and powerful industrial systems. In this context, the Schaeffler company comes into focus because it is one of the leading rolling bearing manufacturers in the world. With its wide product range, the use of modern digitalization approaches and the use of the GS1 DataMatrix code, Schaeffler offers a comprehensive solution for optimized maintenance strategies as well as higher reliability and availability of machines and systems. The following explains the relevance of rolling bearings in safety-critical applications, examines the digitalization approach through the so-called digital twin in more detail and explains to what extent the introduction of the GS1 DataMatrix Code is revolutionizing maintenance.
Areas of application and relevance of rolling bearings
Roll bearings – also known as a ball bearing, cylinder roller warehouse, bowling roller warehouse or needle bearing – can be found in a variety of areas of application. They serve to reduce friction on rotating or oscillating components and at the same time absorb high loads. These properties are essential for safe and smooth traffic: trains, cars and aircraft are just a few examples of means of transport that rely on reliable rolling bearings. In addition, the camps have an important role in industrial plants in which they ensure the uninterrupted operation of production lines, robots and other machines. Experts always point out: "A defective roller bearing can have serious consequences." The effects include prematurely maintenance, expensive still stands in production and possible accidents when systems suddenly fail.
Rolling bearings in safety-critical applications
The use of rolling bearings is particularly sensitive in safety-relevant environments such as the railway industry, the oil and gas industry and in aerospace. There are often extreme conditions that demand maximum performance from the bearings: “In rail vehicles, the axlebox bearings are largely responsible for the safety of passengers,” it is often said. Failure could have a direct impact on stability and steerability. The situation is similar in aircraft turbines, where continuous monitoring is essential so that they can permanently withstand the enormous loads and speeds. The highest level of operational safety is also required in drilling rigs or production systems in the oil and gas industry, where pressures, temperatures and corrosion are unusually high. Only if all components, including the rolling bearings, function reliably can undisturbed operation be guaranteed.
Advances and challenges in rolling bearing technology
Against this background, it is not surprising that billions of rolling bearings are in service worldwide and drive a wide variety of machines. At the same time, the requirements for quality and efficiency have become ever more stringent. Advances in materials research, lubricants and production logistics are ensuring constantly increasing performance properties, but at the same time, Industry 4.0 is increasingly relying on data collection and real-time monitoring. Therefore, one sentence is a guiding principle for many engineers: “Without rolling bearings, no robot arm, no wind turbine, no aircraft engine or no train can move today.” Wherever there is movement, reliable and efficient bearings are needed.
Schaeffler: A global market leader in rolling bearing production
Schaeffler has established itself as one of the largest rolling bearing manufacturers in the world in this market segment. The company offers a diverse portfolio, ranging from tiny miniature bearings for dental drills to special designs for mining. In addition, high-temperature bearings are being developed for use in aerospace that can withstand large temperature fluctuations or aggressive environmental conditions. According to internal information, the standard program includes around 40,000 different types of rolling bearings. But that's not all: “Every rolling bearing has individual properties,” emphasize experts. Customer-specific special solutions are often designed to precisely meet the requirements of individual industries or customers.
Data acquisition and sensors for rolling bearings
Schaeffler provides extensive data so that customers always know what special specifications the rolling bearings they have installed have. Since rolling bearings are always mounted in places where movement occurs, they are particularly suitable as measuring points for relevant operating parameters. Sensor technology and data recordings make it possible to examine bearing behavior under real conditions. This allows information from the areas of engineering, production and logistics to be collected. For this purpose, Schaeffler has created a data interface through which customers can access data on mileage, vibration values or temperatures. It is emphasized: “Rolling bearings are perfect data suppliers.”
Digitization through the digital twin
In the wake of digitalization, which is increasingly finding its way into all areas, Schaeffler has developed the digital twin approach. The physical rolling bearing is coupled with a virtual counterpart in the cloud or in a data platform. The basis is the GS1 DataMatrix code, which is attached directly to the inner and outer ring of the bearing using laser engraving. This code is a machine-readable mark that contains, among other things, the serialized Global Trade Item Number (GTIN). Each code is unique and allows the physical warehouse to be clearly identified. This creates the prerequisites for mapping all information about this warehouse in a digital twin and tracking it throughout the entire life cycle.
Advantages of the GS1 DataMatrix Code and the digital twin
The advantages of this digital connection are manifold. First of all, it offers complete traceability. From the time of production to disposal, it can be clearly determined when and where the bearing was manufactured, what materials were used and what specific characteristics it has. This is a significant advantage, especially in safety-critical areas, because only a transparent and documented product life allows quick reactions in the event of a recall or malfunction. Maintenance also benefits from this data collection, because maintenance intervals can no longer be based solely on statistical empirical values, but can be individually adapted to the actual condition of the bearing. A sentence that operators emphasize again and again is: “Predictive maintenance reduces costs and increases availability.”
The key role of predictive maintenance in industry
Predictive maintenance and digital diagnostics are now key elements of modern maintenance. They are based on detailed real-time data and algorithms that detect irregularities in bearing stress. This technology-driven process makes it possible to identify wear at an early stage and initiate countermeasures in a timely manner so that downtimes are minimized. In industries with high production rates or with safety-critical requirements, such as rail transport, preventative replacements can prevent damage before it has serious consequences. In addition, digital data is the basis for application-specific services. Schaeffler, for example, offers a 100% return service for bearing preparation. This means customers can rely on their bearings being professionally inspected, cleaned and, if necessary, repaired. It is always checked which factors were particularly stressful during previous operation and how they need to be taken into account when used again.
Optimizations through the GS1 DataMatrix Code
Thanks to the GS1 DataMatrix code, the company can bundle production and logistics data in a central database and make it accessible to both the customer and other authorized partners. This also results in optimizations in the supply chain, as the clear identification enables consistent tracking in logistics and service. One person responsible sums it up like this: “The GS1 DataMatrix Code is the bridge between the real and digital worlds.”
Digital rolling bearings in the railway industry
This approach is now seen as a pioneer and role model in the railway industry. Rail operators are faced with the challenge of keeping their fleets available around the clock with as little maintenance as possible. The rail network in many regions of the world is already heavily utilized, meaning failures can significantly disrupt operations. The solution developed by Schaeffler to digitally monitor rolling bearings throughout their entire life cycle makes a significant contribution to keeping the infrastructure stable. In addition to increasing safety, the costs for maintenance and spare parts can be reduced because planning is based on real data and not based on purely time-based intervals. Future trains could report in real time if bearing damage is imminent, and a maintenance team can provide the necessary components and specialists in a timely manner.
Sustainable maintenance and resource conservation
Another important topic is sustainability. When used properly, rolling bearings can last a very long time and can sometimes be reconditioned several times. Digitalization enables precise documentation of such processes and can promote resource-saving circular models. Since all repair and maintenance steps are stored in the digital twin, the history of the bearing is always traceable. This also makes it easier to make decisions about whether a bearing should be remanufactured or replaced. Operators can see at a glance how many operating hours the bearing has already completed, what peak loads occurred and what the results of lubricant analyzes looked like. This transparency not only supports the reduction of waste, but also leads to a more efficient use of personnel and materials.
New business models thanks to digital solutions
The interlinking of digital twins, sensors and big data analyzes also opens up new business models. Some operators are already switching from buying rolling bearings to purchasing their functionality as a service. In such a model, the manufacturer retains full responsibility for maintenance and replacement, ensuring that the bearings perform at their target performance at all times. This includes the fact that data is continuously collected, evaluated and used for planning. As one insider describes it: “We are no longer just selling stock, but guaranteed availability.”
The GS1 DataMatrix Code as an identification anchor
The GS1 DataMatrix Code acts as a secure identification anchor. It allows clear identification, which minimizes sources of errors in the documentation and improves clarity. The transition from manual lists or error-prone barcode scans to laser-engraved serialized GTIN also reduces the risk of installing the wrong bearing during maintenance work. In locations with high levels of automation, robots can read the code and transfer the corresponding data directly to the systems. This reduces human errors and further speeds up the process of stocking and assembling warehouses.
The future of industry with Schaeffler
In summary, it turns out that Schaeffler with his innovative rolling stores is up to date and addresses the requirements of modern industrial sectors. More and more companies realize that it is no longer sufficient to select components exclusively from mechanical aspects. Rather, information about the origin, the condition and the expected useful life are part of a holistic product life cycle. This trend goes beyond the classic state monitoring and ends in comprehensive, networked solutions. This is exactly where the concept of the digital twin comes into play, which Schaeffler implements using the GS1 Datamatrix Codes. "We think the rolling bearing new – and digital," the motto could be.
Perspectives for other industries
In the future, other industries will adopt this approach, be it manufacturing, energy or construction. The principle of predictive maintenance can be used profitably wherever rotating or pivoting components are used that are subject to high stress. Digitalization is the central element that increases both the safety and the cost-effectiveness of the systems. And it is companies like Schaeffler that are pushing this path forward with vigor.
Rolling bearings: data sources for modern industry
This makes it clear that rolling bearings are much more than just mechanical components. They are data carriers and data generators at the same time and form the foundation for modern maintenance concepts. Thanks to their key position in mobile systems and openness to advanced technologies, they are ideally suited to enable the step into the fully connected industry. This shows: “Where there is movement, Schaeffler is involved, and where Schaeffler is involved, there is a new quality and quantity of data.” This applies to mechanical and plant engineering, the railway industry, aviation or any other industry that Safety, reliability and efficiency are equally prioritized.
We are there for you – advice – planning – implementation – project management
☑️ SME support in strategy, consulting, planning and implementation
☑️ Creation or realignment of the digital strategy and digitalization
☑️ Expansion and optimization of international sales processes
☑️ Global & Digital B2B trading platforms
☑️ Pioneer Business Development
I would be happy to serve as your personal advisor.
You can contact me by filling out the contact form below or simply call me on +49 89 89 674 804 (Munich) .
I'm looking forward to our joint project.
Xpert.digital – Konrad Wolfenstein
Xpert.Digital is a hub for industry with a focus on digitalization, mechanical engineering, logistics/intralogistics and photovoltaics.
With our 360° business development solution, we support well-known companies from new business to after sales.
Market intelligence, smarketing, marketing automation, content development, PR, mail campaigns, personalized social media and lead nurturing are part of our digital tools.
You can find more at: www.xpert.digital – www.xpert.solar – www.xpert.plus