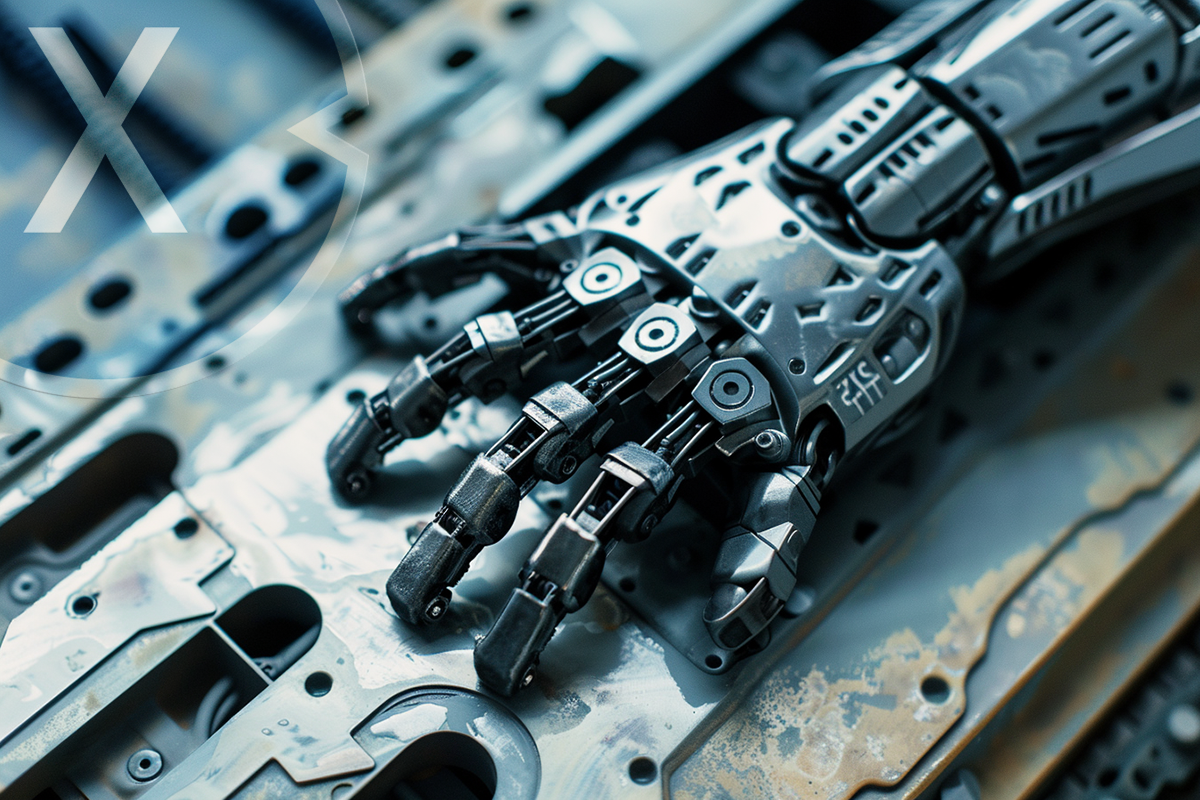
The future of manufacturing in mechanical engineering: punching, bending, welding, and assembly – AI and robot-assisted – Image: Xpert.Digital
Efficient manufacturing processes: The change in automotive, electrical and medical technology
The automotive industry, the electrical/electronics industry, and medical technology – three sectors that could hardly be more different, yet share one thing in common: They all depend on efficient and precise manufacturing processes in the areas of stamping, bending, welding, and assembly technology. However, these processes are undergoing rapid change. Modern technologies and automation solutions are gaining ground and transforming the way products are developed and manufactured. This change is not just a matter of progress, but simply essential for survival in the face of global competition.
Automotive industry: On the fast track towards the future
The automotive industry is facing fundamental change. The era of the internal combustion engine is coming to an end, electromobility and autonomous driving are dominating the headlines. But this change brings with it enormous challenges. In addition to developing new drive technologies, automobile manufacturers also have to adapt production processes to the new requirements. Added to this is increasing international competition, particularly from Asia, which is putting the industry under pressure.
In this dynamic environment, stamping, bending, welding and assembly technology plays a crucial role. In order to remain competitive, automobile manufacturers must optimize their production processes while ensuring the quality of their vehicles. Modern technologies pave the way into the future:
AI-supported image processing systems
The days of manual quality controls are over. Intelligent image processing systems detect even the smallest errors in real time, enabling seamless quality control. The result: less waste, lower costs and higher customer satisfaction.
Robot-based automation
Robots are taking on more and more tasks in assembly. They assemble, weld, and paint components – all with a precision and speed unattainable by humans. The advantages are obvious: greater efficiency, lower error rates, and increased productivity.
But automating production is only part of the solution. The networking of the individual production steps is just as important. This is where the concept of Industry 4.0 comes into play. By networking machines and systems, a smart factory is created in which data can be exchanged in real time and processes can be dynamically adjusted. The result: flexible and efficient production that can be individually tailored to customer needs.
Electrical/electronics industry: precision on a microscale
The electrical/electronic industry is characterized by a constant trend towards miniaturization. Smartphones, tablets and laptops are becoming smaller and more powerful. This development places the highest demands on precision in production. Micro sheet metal parts used in these devices must be manufactured with the highest precision to ensure the functionality of the devices.
Modern punching and laser cutting technologies enable the production of highly complex components with tolerances in the micrometer range. These technologies are at the heart of modern electronics manufacturing:
Laser cutting
Using laser beams, even the most complex geometries can be cut from sheet metal with the highest precision. The advantages: burr-free cutting edges, high flexibility and enormous speed.
Stamping bending technology
This technology makes it possible to shape sheets into almost any desired shape. Precise punching and bending operations create complex three-dimensional components that are used in a variety of ways in the electronics industry.
But the production of the individual micro-sheet metal parts is only the first step. The precise assembly of the individual components into complex assemblies is just as important. Here, too, automated systems are increasingly being used, which assemble the tiny components with the utmost precision.
Medical technology: Where precision saves lives
Medical technology is a particularly sensitive field. The products manufactured here – from implants and surgical instruments to complex diagnostic devices – have a direct impact on people's health and lives. The demands on manufacturing quality and precision are correspondingly high.
Stamping, bending, welding and assembly technology play a central role in medical technology. Modern technologies enable the production of medical devices and components that meet the highest demands:
Laser welding
This technology enables high-precision joining of metals without causing thermal distortion. This is particularly important in the production of medical implants that are inserted into the patient's body.
Cleanroom technology
In order to avoid contamination of products with particles, medical devices and components are often manufactured under cleanroom conditions. Special clean rooms ensure that the air is free of dust and other contaminants.
The ability to offer customized solutions is another crucial factor in medical technology. Many products are individually adapted to the needs of the patient. Modern manufacturing technologies make it possible to implement these individual requirements quickly and flexibly.
The future of manufacturing is digital, automated and connected
Rapid advances in stamping, welding and assembly technology are changing the way products are developed and manufactured. The automotive industry, the electrical/electronic industry and medical technology benefit greatly from these developments. Modern technologies make it possible to manufacture complex products with the highest precision and efficiency.
The trend is clearly towards automation, digitalization and networking. The smart factory, in which machines and systems communicate with each other and optimize processes independently, is no longer a dream of the future, but a reality. Companies that invest in these areas secure a decisive competitive advantage and actively shape the future of manufacturing.
Suitable for: