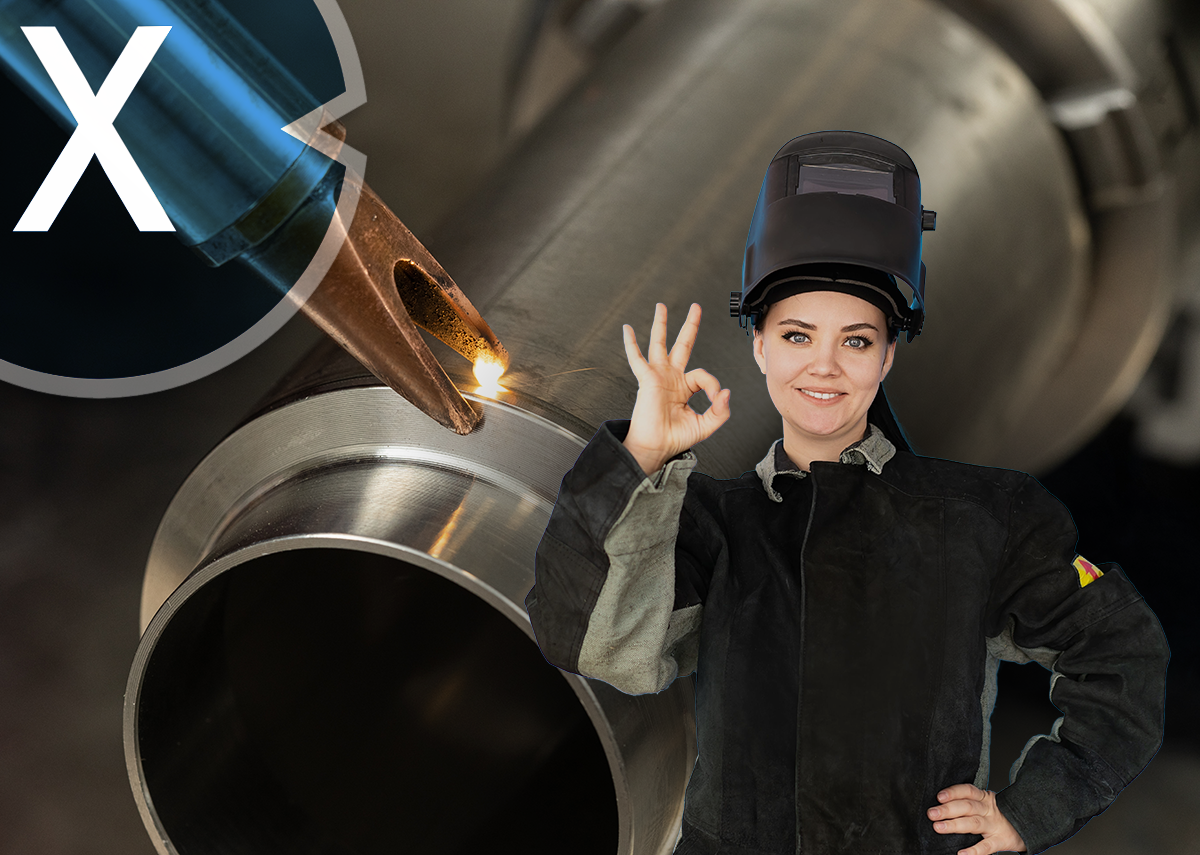
Laser welding machine and laser welding systems of the future: innovations and potential – Image: Xpert.Digital
Laser welding machine and laser welding system: precision and quality in joining technology
Laser technology has made amazing advances in the last few decades, enabling a wide range of applications in various industries. Laser welding in particular has established itself as one of the most efficient and precise methods in joining technology. Laser welding machines and laser welding systems play a crucial role in manufacturing products in industries such as automotive, aerospace, electronics, medical technology and many more.
Functionality and technology
Laser welding machines use high-energy laser beams to join metals, plastics or other materials together. The process is based on the precise concentration of laser light, which is focused on the parts to be welded. This creates an extremely high energy density that melts and bonds the material.
Modern laser welding systems offer different types of lasers, including fiber lasers, CO₂ lasers and diode lasers. Each type has specific advantages and disadvantages that must be taken into account depending on the use case. For example, fiber lasers are known for their high beam quality and energy efficiency, while CO₂ lasers offer a greater depth of penetration.
Advantages of laser welding
1. Precision and quality
Laser welding machines enable extremely precise welds with minimal distortion or deformation of the workpiece. This leads to high quality welded connections.
2. Speed and efficiency
The welding process is often faster compared to traditional methods. The automated laser systems can speed up the production process and increase efficiency.
3. Versatility
Laser welding can join a variety of materials together, including various metals, plastics and even mixed compounds.
4. Minimum material consumption
Because the laser beam is so focused, only a limited amount of material is melted, reducing material consumption.
5. No additives
Unlike some traditional welding processes, laser welding typically does not require additional fillers, minimizing costs and post-processing.
Applications in industry
1. Automotive industry
In automotive manufacturing, laser welding machines are used to produce body parts, seat frames, exhaust systems, and more. The high-precision welded connections contribute to the safety and longevity of the vehicles.
2. Aerospace
In the aerospace industry, component weight is critical. Laser welding machines provide lightweight yet strong connections for structural elements of aircraft and spacecraft.
3. Electronics industry
The miniaturization of electronic components requires precise and reliable connection techniques. Laser welding systems enable the creation of tiny connections in electronic components.
4. Medical technology
In medical technology, laser welding machines are used for the production of implants, medical instruments and devices where hygiene and precision are of utmost importance.
News and current developments
1. Additive manufacturing (3D printing) and laser welding
The integration of laser welding technologies into the 3D printing process has opened up new possibilities. This enables the production of complex components with high-strength welded connections.
2. Collaborative robotics
Automation and Robotics: Advances in robotics have led to collaborative laser welding systems where robots and human workers can work together safely. This flexibility enables more efficient production and use in small and medium-sized companies.
3. Higher power fiber laser
The development of higher power fiber lasers has further increased welding speeds and enabled the processing of thicker materials.
4. Inline quality control
Modern laser welding systems are often equipped with inline quality controls that can monitor welds in real time and detect possible defects, increasing production quality.
5. Innovative materials
Advances in materials science and technology have enabled the development of new materials that are specifically optimized for specific joining processes. These materials offer improved strength, flexibility and resistance to environmental influences.
6. Lightweight construction and hybrid construction
Lightweight structures are important in many industries to reduce the weight of products and improve energy efficiency. Hybrid processes, in which different joining techniques are combined, offer a wide range of possibilities for innovative lightweight construction concepts.
outlook
Laser welding machines and laser welding systems have revolutionized joining technology and offer a wide range of advantages in terms of precision, speed, versatility and quality. With continued research and innovation, these technologies are expected to evolve to conquer even more industries and improve industrial manufacturing.
Welding and cutting: precision and quality in joining technology
Joining technology plays a crucial role in the modern manufacturing industry, and welding and cutting are two of the most important processes in this area. The precision and quality of these techniques are crucial for producing high-quality products in various industries such as automotive, aviation, shipbuilding, mechanical engineering, and many others. In this text we will take a closer look at welding and cutting technologies and examine their importance and current developments.
Welding: creating connections that last
The importance of welding
Welding is a process in which two or more workpieces are permanently joined together by a weld. It is one of the oldest joining techniques and has evolved significantly over time. Welding is used in a variety of industries to produce complex structures and components that must withstand high loads.
Welding processes and their features
- Arc Welding: Arc welding is one of the most commonly used welding processes. Here, an arc is created between an electrode and the workpiece, which melts the material and creates a bond. There are different subcategories such as metal active gas welding (MAG) and tungsten inert gas welding (TIG).
- Laser Welding: Laser welding is known for its exceptional precision and quality. It uses high-energy laser beams to connect materials together. The low heat-affected zone minimizes deformation and enables use on sensitive workpieces.
- Electron beam welding: Electron beam welding involves shining a focused beam of electrons onto the workpiece, melting and welding the material. This process is used for materials with high density and in vacuum.
Cutting: precise shaping for efficient production
The Importance of Cutting
Cutting is an essential step in manufacturing to shape raw materials into the desired shape and size. Precise cuts are crucial for producing parts and components with tight tolerances.
Cutting technologies and their properties
- Laser Beam Cutting: Laser beam cutting is known for its high precision and speed. A high-energy laser beam is directed at the material, causing it to melt or vaporize. This allows cutting thin and thick materials with great accuracy.
- Plasma Cutting: Plasma cutting is mainly used for cutting metals. A plasma jet generated by the ionized gas melts the material, allowing thicker sheets to be cut.
- Water Cutting: Water cutting uses a fine jet of water laced with abrasive particles to cut materials. This method is ideal for soft materials or those that could be damaged by high temperatures.
News and current developments
Industry 4.0 and automation
Joining technology has benefited from advances in automation and Industry 4.0. Robot-based welding and cutting systems are increasingly being used to increase productivity and make manufacturing processes more efficient.
Artificial intelligence and machine learning
Integrating artificial intelligence into welding and cutting systems enables better process control and error detection. The technology can automatically adjust parameters to achieve optimal results and minimize waste.
Material innovations
Advances in materials science and technologies have produced new materials specifically optimized for welding and cutting. These materials provide improved strength, corrosion resistance and other properties important for specific applications.
Hybrid systems
The combination of different joining and cutting technologies makes it possible to take advantage of multiple processes and meet specific requirements. Hybrid welding and cutting systems are increasingly being used in industry.
The two pillars of joining technology
Welding and cutting are two essential pillars of joining technology and play a crucial role in the modern manufacturing industry. The precision and quality of these processes are essential for producing high-quality products. Through continuous research and innovation, welding and cutting technologies are expected to continue to improve to meet the increasing demands of the industry and open up new opportunities in manufacturing.
Welding, soldering, gluing and more: the variety of joining techniques
Joining technology is an important area in manufacturing and is concerned with connecting workpieces in order to produce finished products. Various methods are used to connect the workpieces permanently or temporarily, depending on the requirements of the respective application. The quality and reliability of the joining technology are crucial for the performance and functionality of the end product. In this text we will look at the basics of joining technology and give some examples of different joining processes.
Types of joining technology
There are a variety of joining processes that can be selected depending on materials, applications and specific requirements. Here are some of the most common types of joining techniques:
- Welding: Welding is one of the oldest and most commonly used joining processes. It includes various techniques such as arc welding, laser welding, electron beam welding and more. Welding involves permanently joining workpieces together with a weld, melting the material at the joint.
- Soldering: Soldering is a process in which a solder is applied to the workpieces to be joined. Heating the solder causes it to melt and join the workpieces. Unlike welding, soldering does not melt the base material.
- Gluing: When gluing, the workpieces are connected to each other using a layer of adhesive. Bonding is particularly suitable for materials that are difficult to weld or are sensitive to high temperatures.
- Riveting: When riveting, rivets or pins are inserted through the workpieces to be connected and then deformed or welded at the ends. This creates a permanent connection.
- Mechanical Connections: Mechanical connections include techniques such as bolting, clamping or press fitting. These methods do not require permanent changes to the material and enable non-destructive dismantling.
Examples of the application of joining technology
- Automotive industry: In the automotive industry, joining technology plays a central role in the manufacture of vehicles. Welding is used for body assembly, while bonding is used in vehicle glazing or composite materials.
- Aerospace: Aerospace requires high-strength and reliable connections. Welding and bonding are used here for structural parts, engines and aircraft components.
- Electronics industry: In the electronics industry, soldering processes are used to produce circuit boards and electronic components. Gluing is used in the assembly of displays, touchscreens and housings.
- Medical technology: Medical technology uses adhesives and welding processes to produce medical devices, implants and prostheses. A precise and reliable connection is of utmost importance here.
- Shipbuilding: Shipbuilding uses welding techniques to create ship hulls and components, while riveting has traditionally been used to join plates and sheets.
Laser welding on large, sensitive components where TIG welding is problematic
ALPHA LASER, a leading provider of laser welding solutions, is presenting its latest 1200 W laser welding system during the Welding and Cutting trade fair in Essen (September 11th to September 15th, 2023) , which was specially developed for welding on large and sensitive components where the conventional Welding reaches its limits. The powerful systems enable welding tasks that were previously only possible in the TIG / TIG and MIG areas, but with the advantages of laser welding.
Advantages of the ALPHA LASER 1200 W laser welding system
- Due to the low heat input into the material, preheating is no longer necessary, which saves time and costs.
- Minimal deformation and cracking, allowing welding of critical and delicate metals without cracking.
- Flexible welding: The systems enable both pulsed and continuous welding depending on the application.
Areas of application of the 1200 W laser welding systems
The powerful 1200W laser welding systems are ideal for various applications including:
- Shaft repair
- Hard cladding with wire and powder
- Casting repairs in hydroelectric power plants
- Welding large and sensitive components where TIG welding is problematic
- With these systems, wires with a diameter of 1.6 mm can be melted.
Expansion options and automation
The ALPHA LASER 1200 W systems offer numerous expansion options, such as rotary axes, heavy-duty rotary axes and tilt-swivel lenses for quick positioning of the laser beam. The Mabotic software with scanner kit allows complex component geometries to be scanned, programmed and welded, enabling the automation of welding tasks.
Innovative systems
The introduction of the powerful ALPHA LASER 1200 W laser welding systems marks an important step in welding technology for sensitive components. With these innovative systems, demanding welding tasks can be carried out precisely and efficiently, while avoiding the disadvantages of conventional welding processes.
For further information about the ALPHA LASER laser welding systems and their possible applications, visit our exhibition stand 5C10 or www.alphalaser.eu
Source: press release dated July 31, 23
What is TIG welding?
TIG welding (tungsten inert gas welding) is an arc welding process that uses a non-melting tungsten electrode to create the weld. It is one of the inert gas welding processes because an inert gas, usually argon or helium, is used during the welding process to protect the molten metal from reacting with oxygen and nitrogen in the air.
TIG welding process
- Preparation: The workpieces to be welded are first cleaned and positioned precisely. The weld seam and electrode position are carefully determined.
- Structure of the welding machine: The welding machine is adjusted according to the requirements. The welding current, gas flow rate and other parameters are adjusted.
- Tungsten electrode and gas: The non-melting tungsten electrode is inserted into the welding gun. The inert gas is supplied to protect the weld zone from oxidation and contamination.
- Welding process: The welder starts the arc by bringing the tungsten electrode close to the workpiece and then removing it again. The arc is created and the material is melted.
- Additional material: If additional welding material is required, it is manually introduced into the welding zone. The addition of filler material can be precisely controlled and in some cases is not necessary depending on the welding task.
- Weld: The tungsten electrode and the weld pool create the weld. The quality of the seam depends on the welding speed, the welding current and the precision of the welder.
Features of TIG welding
- TIG welding enables extremely precise and clean weld seams.
- Because the tungsten electrode does not melt, it is not incorporated into the weld and does not contribute to the weld material.
- The use of inert gas as protection creates a pure weld zone with minimal risk of contamination.
- The process can be used on various metals such as aluminum, stainless steel, copper and nickel.
- Due to its precision and control, TIG welding requires a certain level of experience and skill on the part of the welder.
Applications of TIG welding
TIG welding is used in many industries, especially when high demands are placed on welding quality. Examples of applications are:
- Manufacturing aircraft parts and spacecraft where high strength and reliable welds are required.
- Food and pharmaceutical industries, where clean and uncontaminated welds are essential for hygiene and safety.
- Manufacture of stainless steel containers and pipelines where precise and tight welds are required.
- Ironwork and metalworking where precise welds are required for aesthetic and decorative purposes.
Precision and versatility
Due to its precision and versatility, TIG welding is a widely used welding process used in many demanding applications. It enables high-quality and durable welds and is valued by experienced welders in various industries.