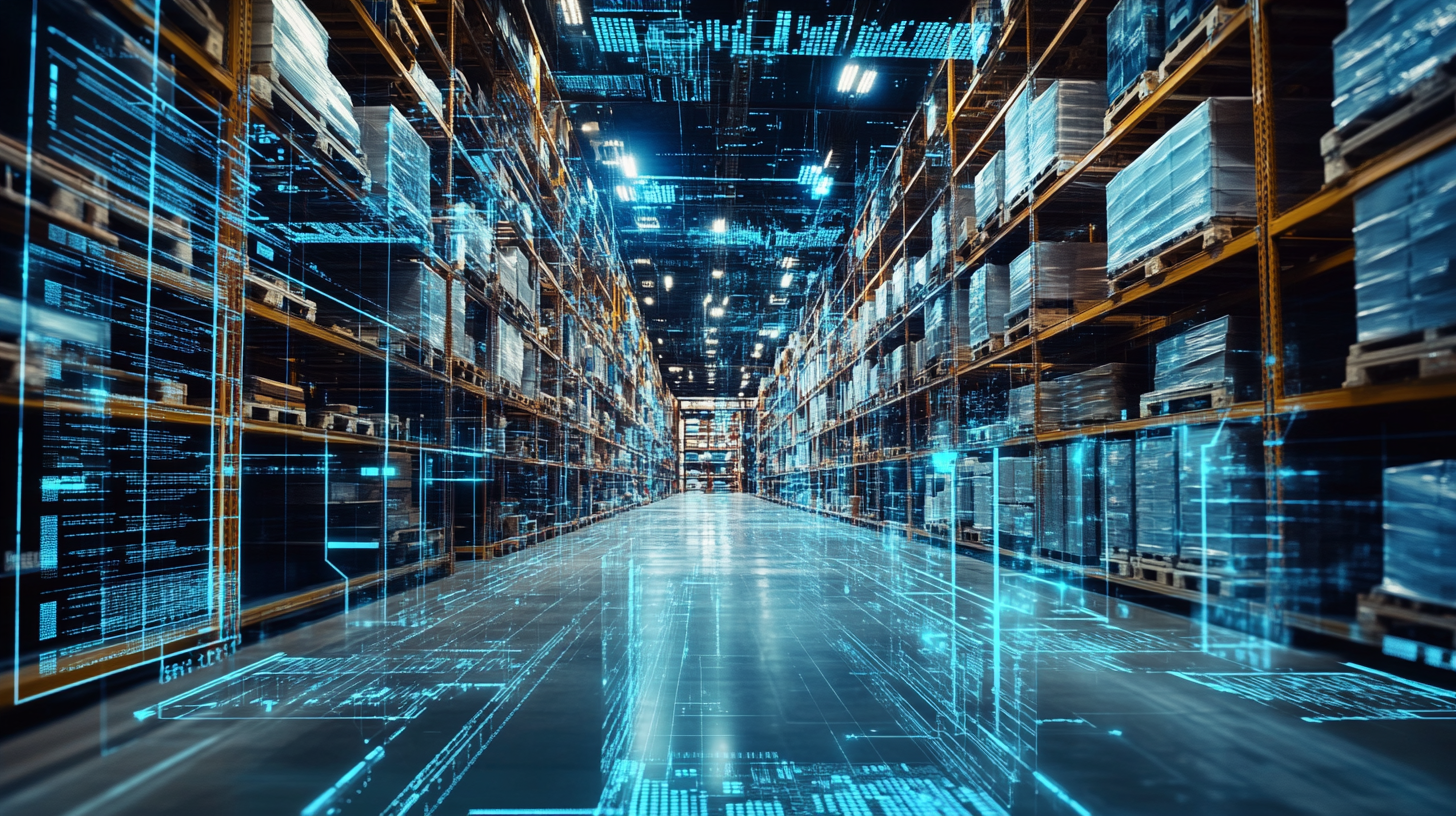
Integration of AI and machine learning in warehouse logistics - global developments in Germany, EU, USA and Japan - Image: Xpert.digital
Artificial intelligence transforms the warehouse logistics: automated efficiency in focus
The future of warehouse logistics: AI-controlled processes for maximum productivity
Artificial intelligence (AI) describes the ability of machines or software to perform tasks that normally require human intelligence - such as logical thinking, learning, planning or creative problem solving. In essence, it is about computer systems from data and can make decisions instead of only following strictly predefined rules. Machine learning (ML) is a sub -area of the AI in which algorithms independently identify patterns and adapt their behavior by analyzing large amounts of data. Put simply, an ML system learns from experience: it is "trained" with historical data and can then predict or make decisions with new, unknown data. As a result, AI is able to continuously improve its own forecasts and services without being explicitly programmed by people for every individual case.
In logistics - and especially in warehouse logistics - AI and ML open enormous opportunities. The logistics industry has extensive networks and generates huge amounts of data, which makes it an ideal field of application for AI. For example, intelligent algorithms can predict future order quantities, calculate optimal routes or control complex warehouse processes. Self -learning systems can make decisions faster and often more precisely than people, especially when it comes to processing large amounts of data in real time. In modern warehouses, AI technologies are therefore used in different areas-from inventory management to picking (the compilation of orders) to transport control within the warehouse.
Overall, the following applies: AI in the camp imitates the "thinking" of a very experienced camp manager, only that she can access a lot more data. For example, AI systems can recognize which items sell well when, how to store goods most efficiently, or which paths a forklift should drive to save time. These automated, data -driven decisions form the basis for the fact that AI and ML is increasingly penetrating warehouse logistics.
Optimization of warehouse processes by AI
One of the greatest advantages of AI in warehouse logistics is the optimization of existing processes. Warehouses are dependent on constant current of information - for example inventory data, order data or location information from goods. However, where people are prone to errors or can only process a limited information, KI provides precision and speed. For example, AI can provide and analyze data in real time, which means that errors are recognized and remedied faster before causing problems. Routine tasks such as checking inventory or the collection of goods inputs can be automated, which relieves employees.
AI systems can also recognize patterns in the warehouse processes that might miss a human eye. Through these data analyzes, the system better understands the current situation in the warehouse, identifies bottlenecks or inefficiencies and suggests improvements. A practical example is way optimization: algorithms can analyze and optimize the walking paths of warehouses or industrial trucks (e.g. forklifts). For example, picking lists are sorted in such a way that employees take the shortest possible route through the warehouse. This reduces terms and the orders are put together faster. Likewise, AI functions can determine the best storage space for each product- based on its size, coverage and other factors- to make the deposit and outsourcing more efficient.
Another important aspect is to reduce errors and improve quality. AI-supported image identification systems can, for example, scan packages and check their condition and dimensions when they are receipt. This recognizes immediately if there is damage or an article has been incorrectly labeled. Such automated quality controls ensure that problems are resolved early in the process and do not run through the entire supply chain. In addition, the AI learns over time: initially mistakes can still occur, but through machine learning techniques, image recognition continuously improves itself and further reduces the error rate.
All of these optimizations ultimately lead to more productivity and lower costs in warehouse operations. Robots and AI systems can do some tasks much faster and more precisely than people, which increases productivity. At the same time, the algorithmic evaluation of warehouse data enables better strategic decisions- for example in personnel and resource planning- which makes overarching processes more efficient. AI solutions can continuously monitor the processes, analyze risks and act proactively (e.g. recognize and counteract a threatening bottleneck). Overall, the transparency in the warehouse improves, and problems are often recognized before they even arise. All of this contributes to reducing costs, because a more efficient warehouse causes less waste, less error costs and optimally uses working hours. According to expert forecasts, AI technologies could increase efficiency in the logistics industry in the coming years by significant magnitude-accenture, for example, estimates an efficiency increase of over 40 % to 2035.
In summary, AI increases the speed, accuracy and flexibility of warehouse processes. This ranges from the faster finding and sending of products, minimizing inventory differences, to better coordination with other areas of the supply chain. For companies, this means a higher performance of their warehouse while relieving the employees of monotonics or complex tasks.
Suitable for:
- Stock at the limit? Warehouse automation: warehouse optimization vs. retrofit – the right decision for your warehouse
Demand forecast and inventory management with ML
A central field of application of machine learning in warehouse logistics is the requirement forecast. This means the forecast of future demand - the question: which product is needed when and in what amount? The precise answer to this question is worth gold because it enables inventory to be optimally controlled. Too much goods in stock bind capital and storage space unnecessary, too little goods lead to delivery bottlenecks and dissatisfied customers. AI-based systems can defuse this dilemma by making very precise predictions based on large amounts of data.
Modern machine learning models analyze historical sales, seasonal fluctuations, current orders, marketing campaigns, trends on social media and many other influencing factors. From this they learn patterns and relationships. Such a system can, for example, recognize that the paragraph increases certain items as soon as a certain event is imminent (for example, demand for grill carbon increases before summer weekends). Based on such patterns, the AI automates which goods quantities should be delivered at which location at what time. These predictions help companies to adapt their inventory to their inventory. Specifically, this means that if a product will be increasingly in demand, the AI ensures that supplies ordered in time and is available in the warehouse. Conversely, she warns if a product is likely to be in demand, so that excess stocks and overproduction are avoided.
The German online retailer Otto provides a practical example. The company has been using a self-developed AI-based system for sales forecast since 2019. This system looks into the future of sales, so to speak, and supports all processes involved - from purchasing to warehousing to delivery. The AI forecasts show Otto exactly which items arrive in the warehouse and how high the expected paragraph will be at a certain point in time. On this basis, Otto decides whether and in what amount an article is bought and how it should be sold. For example, the AI determines whether a product is kept in stock as an in stock or, if necessary, sent directly to the customer by the manufacturer. The forecast has a direct impact on purchasing, warehouse and distribution. The result: there is always only the goods in stock, which is really needed, which reduces expensive excess stocks and later references with discounts. At the same time, the forecasts ensure that items are available as soon as the demand attracts demand not to miss sales opportunities. With Otto, thanks to this AI, 35 % of the range is now automatically reordered without having to manually trigger orders - a proof of how well the predictions work.
Other companies also use such AI-based inventory optimizations. DHL reports that AI systems can compare demand and existing in real time and can automatically arrange reorder. They are even able to calculate demand tips in advance in order not to create any wrong stocks (out-of-stock) or excess stands. This guarantees a rapid delivery to customers because there is always enough goods in stock, but there are no unnecessary buffers in the warehouse that would cause costs.
The demand forecast via ML not only affects your own warehouse, but the entire supply chain (supply chain). For example, good forecasts make it possible to send in regional distribution centers in advance before orders were even received. Otto, for example, creates regional forecasts to predict which products are ordered in which number. Accordingly, these items are already delivered to a nearby depot as a precaution. This shortens delivery times and reduces transport routes, which also lowers CO₂ emissions.
In summary, AI-supported demand planning leads to more efficient warehousing: Always the right product at the right time in a suitable amount in the warehouse. This enables companies to avoid delivery bottlenecks, increase customer satisfaction and at the same time reduce storage costs. For warehouse logistics, this means less "fire brigade inserts" in order to fix sudden bottlenecks because the AI recognizes and likes such situations early on. In times more and more volatile customer behavior (keyword e-commerce boom, seasonal peaks through online actions, etc.), this forward-looking control is becoming a decisive competitive factor.
Automation and robotics in the warehouse
A particularly eye-catching area of AI integration is automation through robotics in warehouses. Modern bearings are increasingly relying on smart machines that can move, lift, sort or pack - often controlled or supported by AI. These warehouse robots relieve human employees, especially in physically exhausting, monotonous or time -critical tasks.
One example is autonomous vehicles in the warehouse, also known as FTS (driverless transport systems) or AMR (autonomous mobile robot). Such vehicles - from small, flat transport robots to automated forklifts - can transport pallets, boxes or individual articles from A to B completely independently. This is made possible by sensors, cameras and navigation systems, combined with AI algorithms for route planning. The robots “see” their surroundings, recognize obstacles and look for the best way to the goal. AI enables these vehicles to react to changes in real time - such as bypassing an obstacle that is suddenly in the corridor - and still keeping the optimal route. Such autonomous load carriers are already reality in many camps: they transport goods between storage spaces, bring supplies to the shelf, collect articles for customer orders (automated picking) or promote finished orders to the shipping station. This relieves human employees from long walking routes and transport tasks and can concentrate on more demanding activities.
Another robotic application are AI-controlled picking robots. These are inpatient or mobile robots with arms that can be found from shelves. With the help of image processing (cameras and AI software), such a robot identifies the correct article and packs the required amount. There are already plants in which robots pick individual parts: the robot receives the order from the warehouse management system, e.g. 5 pieces of an Article X. He navigates (if mobile) to the corresponding subject, visually recognizes the article and accesses precisely. Weight sensors check whether the correct quantity has been removed and the AI confirms the article identity again via image recognition. Such systems often work in separate areas or during the night to be able to prepare orders around the clock. Also more complex automation systems such as picking machines (automatic stores) are also used - there are various articles in containers or shafts, and on request, the system automatically transports the desired item into an output container.
In this context, Amazon has become famous: The company has been massively on warehouse robots for around a decade. In the Amazon camps, thousands of small orange robots (formerly from Kiva Systems) transport entire shelf modules across the warehouse directly to the human pickers. An intelligent AI control coordinates this robot shelves so efficiently that the paths of the employees are minimized. An internal Amazon study has shown that this AI-optimized coordination leads to enormous savings-around half a billion US dollars a year saves Amazon by bringing the robots to the employees faster and more efficiently. The AI always calculates which shelf modules next to the employee will have to be brought to which employee in order to optimally process the orders. The result: faster execution of customer orders at the same time.
Sorting and packaging robots are also moving in. In some DHL packaging centers, for example, robots already take packages from the conveyor belt and sort them into subjects for the respective delivery routes. Thanks to AI, these so-called DHLBots are capable of learning and flexible-equipped with 3D cameras, you can see the size and shape of programs, scan barcodes and autonomously decide which subject includes a package. So they are much more than rigid industrial robots; You can handle a wide variety of packet sizes and adapt to changed processes. In practice, this means that packages are pre -sorted faster and more error -free, which accelerates the delivery on the "last mile".
There are numerous exciting examples internationally. In the logistics center of the Chinese e-commerce giant Alibaba (more precisely its logistics daughter Cainiao), a highly automated warehouse was set up, in which robots do around 70 % of the work. Around 60 mobile robots - also called “ZHU Que” locally - transport in a 3,000 m² camp to the packing stations and have tripled productivity. A human warehouse worker usually creates 1500 picked items per shift - with the support of the robots there are 3000 articles, with significantly fewer walking. The AI ensures that the robots work together efficiently, do not get in the way and always bring the next goods to the withdrawal point at the right moment. This alibaba warehouse demonstrates what is technically possible if you almost fully automate warehouse logistics: employees hardly have to walk through the shelf series because the robots bring the shelves or goods directly, and the throughput increases enormously.
Such smart warehouses often integrate several technologies: autonomous vehicles, robot gymnastics, automated conveyor belts, IoT sensors for monitoring environmental conditions and stocks, as well as AI systems as "brain" that controls everything. The goal is a highly automated warehouse that works efficiently, safely and transparently. In these environments, human employees often work hand in hand with collaborative robots (cobots), which they support in severe lifting processes or bring them to them. The introduction of this robotic leads to a changed task profile for the employees, but overall increases the performance of the warehouse.
There are still many camps at the beginning of this development - according to estimates, around 20 % of warehouses are only automated in Germany and the United States, the rest is still largely operated manually. But the big players such as Amazon, Alibaba or DHL set it off and gradually equip their camps with AI technologies and robots. In the coming years, more and more warehouse processes will be expected - be it through driverless transport systems, automated sorting systems or intelligent assistance systems for employees.
Suitable for:
- Efficient warehouse automation: 25 important questions and answers for your optimization – tips on warehouse optimization and retrofitting
AI in supply chain and enterprise software (SCM, DCM, ERP)
Not only individual robots, but also the software in the background plays a crucial role in AI integration in warehouse logistics. Modern supply chain management (SCM) systems and enterprise resource planning (ERP) solutions are increasingly equipped with AI functions to improve planning, control and administration along the supply chain. The term demand-chain management (DCM) also appears in this context-here the focus is especially on customer demand and the supply chain based on it. In all of these systems, AI can serve as a kind of intelligent layer that significantly enhances the classic functions.
A central example is the Warehouse Management System (WMS)-the software that manages all processes in the warehouse (from receipt of goods to storage and picking to goods output). In the past, a WMS worked according to firmly programmed rules. In the meantime, however, manufacturers integrate AI modules that make the WMS "smarter". For example, the Polish fashion retailer LPP has implemented a AI solution (PSIWMS AI) in its warehouse management system that uses machine learning mechanisms for process optimization. The result was significantly shorter picking trails and overall a higher efficiency in the warehouse. This shows: AI can add existing logistics software in such a way that it learns from its own operating data and improves processes independently. A AI-based WMS can, for example, recognize which items are often ordered together and whose storage spaces move closer together (automated layout optimization). Or it prioritizes orders dynamically according to available resources, traffic conditions or shipping dates.
Supply chain management systems
Supply chain management systems with AI support go one step further by looking at the entire supply chain beyond the individual bearing. They use AI to make end-to-end optimizations: to compensate for the stocks across several storage locations, to optimally utilize transport capacities and to react flexibly to disorders. AI-based SCM tools can bring large amounts of data from different sources-e.g. weather data, traffic information, supplier information-and thus adapt delivery plans in real time. Oracle, for example, describes that companies use AI to balance stocks and find fuel -efficient delivery routes, far more efficient than it would be possible with conventional software. For example, such a system could automatically calculate an alternative route for subsequent trucks in the event of a suddenly blocked traffic route and the affected deliveries. Or it notices quality problems with a certain supplier and warns in time before faulty parts get into the camp.
Demand-Chain management (DCM)
Demand-Chain management (DCM), which focuses on the demand side, also benefits from AI. This is about optimal use of customer needs - basically a integration of marketing/sales with the supply chain. In DCM, for example, AI can analyze customer orders and improve forecasts in order to adapt production and warehousing even more precisely to the actual demand. In practice, SCM and DCM often blur, but both aim to reconcile supply and demand with AI as efficiently as possible.
Large ERP providers such as SAP or Oracle have already integrated AI functions in their products. SAP speaks of "Business AI" within the ERP modules, which should optimize warehousing, order processing and transport with AI-supported knowledge. Oracle emphasizes that AI systems can recognize patterns in supply chains that remain hidden for humans, for example to predict customer demand more precisely and thus enable more economically efficient inventory management. Microsoft and specialized logistics software providers also offer AI modules that are clinking into existing processes. Standard interfaces are often provided with ERP systems, so that AI models (for example for forecasts) can work relatively quickly with the company data. For example, a AI model for sales forecast can be integrated directly into the ERP order processing: the system then automatically creates order suggestions for supplies in purchasing, based on the ML forecast.
A easily understandable software use are AI chatbots for logistics. These digital assistants can be integrated into warehouse management systems or transport management systems and help employees such as external partners to quickly get information. In the storage context, chatbots could answer questions, for example, à la “Where is Article XY?” or "How high is the current existence of product z?" - And in a matter of seconds, around the clock. You can accept order inquiries or predict delivery times. Internally, such assistants relieve the staff of time -consuming research work, externally improve customer service (e.g. information on the warehouse status of an order).
In summary, AI penetrates the software landscape in logistics at all levels. From WMS to SCM/DCM to ERP, classic systems are supplemented by AI to enable automated decisions. Integration is important: the AI solutions must fit seamlessly into existing processes. Thanks to cloud technology and standardized interfaces, this is getting easier. Today, companies can often add AI functions to their existing systems as an extension. Nevertheless, successful implementation remains a task that requires know-how-the correct data must be available, the models trained and continuously monitored. Once this has been mastered, AI-based software systems offer considerable added value: transparency, speed and proactive control become new normality in warehouse logistics.
Xpert partner in warehouse planning and construction
Challenges of AI implementation: This is how companies master investments and IT hurdles
Challenges of AI implementation: This is how companies master investments and IT hurdles-Image: Xpert.digital
Practical examples from companies
Many companies worldwide already use AI successfully in their warehouse and logistics processes. Here are some practical examples that show how diverse the applications are:
Amazon (USA)
As one of the pioneers, Amazon uses AI and robotics on a large scale. In the fulfillment centers (logistics centers) of the e-commerce giant, tens of thousands of robots move to the employees. A AI permanently optimizes the process - which shelf drives to which employee in order to have an article removed. This intelligent picking control has increased Amazon's efficiency enormously. Studies put the savings from Amazon's AI-based “picking” optimization at around 470 million euros per year. In addition, Amazon Ki uses in many other areas, for example in route planning for delivery vehicles, dynamic personnel planning depending on the order volume or for the predictive maintenance (predictive maintenance) of its facilities in the warehouse.
Alibaba (China)
Alibaba operates high -automated warehouse with his logistics daughter Cainiao, in which robots do the majority of physical work. In a well -known camp in Guangdong, smart transport robots do 70 % of the storage work and increase productivity by triple. The robots - controlled by AI - bring to human colleagues, who mainly only take on packaging. Due to the AI coordination, an employee sorts up to 3000 packages per shift, instead of ~ 1500 without support. Alibaba also uses KI for delivery drones and autonomous delivery vehicles in local transport and, with ML, optimizes the allocation of stocks to its numerous distribution centers. The result is lightning-fast deliveries (sometimes seed-day or within a few hours) despite huge order quantities-enabled by AI-optimized processes.
Deutsche Post DHL (Germany)
As a global logistics service provider, DHL is investing in various business areas in AI. In the parcel delivery, DHL tests, for example, autonomous delivery drones and street bots, but AI solutions are also used in the warehouse itself. In some DHL camps or parcel centers, AI-based robots sort packages fully automatically by target region. These robot arms recognize every show using a 3D camera and AI, grab and put them in the right shipping subject-much faster than a person could. DHL also uses AI tools for the route optimization of the truck fleets, for the forward-looking maintenance of its funding systems and for inventory management for contract customers. An example of the latter: DHL KI uses in contract logistics (warehouse logistics for industrial customers) to monitor stocks of its customers and trigger automatic supply orders before a bottleneck is created. In this way, DHL increases delivery reliability and binds customers more closely.
Otto (Germany)
As mentioned above, Otto Ki successfully uses for sales forecast and storage control. The system ordered autonomously and optimizes the inventory. As a result, Otto was able to reduce excess stands and at the same time improve the ability to deliver. Otto is an example of how a German company develops AI internally and uses productively to remain competitive in a highly competitive market (online trade).
Hitachi (Japan)
In Japan, where many processes traditionally run manually, the wide integration of AI in warehouse logistics is now also beginning. An example is Hitachi who researches AI to improve picking in his distribution centers. The aging workforce is to be supported with image recognition and gripper. Other Japanese companies - for example in the automotive supply industry - are also increasingly relying on automated warehouse systems with AI. The Japanese government promotes such projects as part of "Society 5.0" and special programs to cushion the shortage of skilled workers in the logistics sector. In general, robotics in Japan enjoy a high level of acceptance, and new strategies aim to automate warehouses and supply chains.
Walmart (USA)
The world's largest retail chain is also investing in AI for her supply chain. Walmart uses AI analysis to pursue the inventory in real time in its distribution centers and to predict when branches need replenishment. In addition, Walmart tested inventory robots in some branches that drive along the shelf and recognize which products need to be refilled. Automated sorting systems are used in the large e-commerce logistics centers of the group, and AI optimizes the allocation of packages on truck routes. Together with companies like Walmart, the US trade giants are driving the AI adoption in logistics.
The examples mentioned show that both technology groups and classic logistics service providers AI use productively in their camps. Amazon and Alibaba in particular set standards on which others are oriented. But also in Germany and elsewhere, AI projects-partly developed in-house (as with Otto), partly in cooperation with technology partners or by purchasing startups. It is important that these successes make school: Many small and medium-sized logistics companies observe exactly what the big ones do and now also begin to pilot AI solutions in some areas.
Economic effects of AI in the warehouse
The introduction of AI and ML in warehouse logistics is not only a technical, but also an economic decision. Companies hope for tangible business advantages, but must also invest and take possible side effects into account.
First to the positive economic effects
As already explained, AI significantly increases efficiency in the warehouse - processes run faster and with fewer errors. This affects the costs directly. For example, through AI-optimized route planning for warehouse workers or robots, the time to peck an order can be drastically reduced, which means that more orders can be processed per layer (higher throughput). Personnel costs can be saved or better used because employees are relieved by automation and more productive elsewhere can be used elsewhere. AI-supported inventory management reduces inventory costs because less capital is bound into unnecessary goods and depreciation due to spoilage or outdated products decrease. A survey showed that many logistics companies in AI see the opportunity to significantly increase quality and productivity - even as a pioneering industry of digitization, over half of the companies rated logistics. This means that the industry expects AI to contribute to added value.
Specific numbers underpin the savings potential
Accenture analyzes predict that the use of AI could increase logistics efficiency by 2035 by over 40 %. This would mean enormous cost reductions, since increase in efficiency usually means more output (operation of orders) with the same or less input (time, personnel, area). Already today, a return on investment (ROI) is often relatively quick in concrete projects. AI systems that optimize transports or truck loads, for example, can save fuel costs and avoid empty trips, so that the investment in the software pays for itself within a few years. Ki also contributes to saving costs by avoiding downtime (disorders that lead to delivery delays), for example if Predictive Mainness prevents systems from preventing expensive machine light stands in the warehouse.
Pilot projects and business cases: When AI pays off in warehouse logistics
However, investment costs and challenges are also offset by the opportunities. The purchase of warehouse robots, sensors and AI software is initially expensive. Not every company has Amazon's financial strength to put hundreds of million in automation. Many logistics decision-makers hesitate due to the high investment costs or a lack of IT infrastructure. Especially in small and medium -sized stores, the digital basics (e.g. continuous data acquisition) are often missing in order to fully exploit AI. In addition, implementation requires know-how: experts in AI and data analysis are in demand, but rare and expensive. Initially, AI projects can increase the complexity of what makes employee training and change management necessary.
In the short term, there may also be shifts in the costs. For example, with more IT use, the effort for data security and maintenance of the systems increases. Budgets for regular software updates, model neut training (in the case of ML) or backup systems must be planned. The integration costs-i.e. to integrate AI solutions into existing system landscapes-should not be underestimated. Oracle, for example, emphasizes that implementation can often be difficult and expensive, especially when tailor-made ML models have to be trained on its own data.
In the long term, however, most experts expect the savings potential to outweigh the investments. If a company has overcome the initial hurdles, a AI-supported warehouse usually runs significantly more economically. There are also soft factors: a modern, automated warehouse can react more scalable to growth (cope with more orders without having to top up linear personnel). It increases competitiveness - you remain competitive with the delivery times and costs or can even differentiate yourself by particularly fast service. In addition, AI-optimized processes help to shorten delivery times, which in turn can increase customer loyalty and sales (please order satisfied customers again).
An interesting aspect is sustainability, which is also economically relevant. Ki helps to operate more environmentally friendly (e.g. by optimal use of truck capacities, which saves journeys, or by avoiding excess stands, which lowers overproduction). Since sustainability is now also rewarded by investors and customers, this can indirectly bring financial benefits (keyword "green logistics" as a sales argument).
In summary, AI influences the storage costs in many ways: personnel costs, inventory costs, error costs, loss costs - all of these can be reduced by AI. This faces investment and operating costs for AI systems. Companies have to weigh up when and where AI pays off for them. In practice, we experience that pilot projects are often started at first to get concrete figures. These usually show whether scaling is worthwhile. Since the technology is becoming increasingly accessible and cheaper (cloud services, standard solutions), the entrance threshold drops.
In total, one can say: AI is a competitive factor in logistics. If you invest early and sensibly, you can obtain cost leadership or achieve a service lead. Companies that wait, on the other hand, risk working more inefficient in the long term and losing market shares. Nevertheless, the introduction is not trivial-it takes a convincing business case, good planning and often also the backing of management because it is about strategic course.
Suitable for:
Regional differences: Germany, EU, USA and Japan
The development and spread of AI in warehouse logistics is different regionally, influenced by economic conditions, technological pioneer and political framework. A look at important regions:
Germany and the EU
In Germany, the logistics industry is traditionally very important and is considered comparatively innovative. Studies show that 22 % of German logistics companies are already using AI and another 26 % have concrete plans for this. German companies see German companies Ki as helpful, especially in the area of demand forecast, sales planning and transport optimization. However, around 20 % of the warehouse in Germany are currently largely automated. This means that the majority still works with predominantly manual processes. The challenges often lie in the system complexity and the shortage of skilled workers, which inhibits the implementation of new technologies. Nevertheless, German companies invest strongly in AI in order to optimize processes and remain competitive.
Politically, both Germany and the European Union are massively promoting AI technologies. Germany has launched a AI strategy and provided billions in research. Institutions such as Fraunhofer Institutes (e.g. IML in Dortmund) are targeting AI solutions for logistics. Terms such as Industry 4.0 and Logistics 4.0 frame the vision in which AI also plays a key role. The EU plans to advance with programs such as Horizon Europe and special support projects, AI and robotics in industry. At the same time, in Europe you pay attention to ethical guidelines and regulation-keyword EU Commission and European AI regulation project (AI Act). This is intended to ensure that AI is used trustworthy and safely, which is also important in logistics (e.g. data protection for employee data, safety standards for autonomous systems).
USA
The United States were long leaders in automation and AI research and accommodate tech giants such as Google, Amazon, IBM, Microsoft, which drive AI strongly. In the practice of warehouse logistics, however, the United States is not much further automated than Europe. It is estimated that only about 20 % of the US warehouses are highly automated. However, the high labor costs and the increasing shortage of labor in the United States are now heavily increasing the investments in automation. Large companies such as Amazon, Walmart or UPS implement AI-based systems and serve as draft horses. The United States realizes that AI technology is necessary so as not to fall behind in global competition (especially compared to Asia).
Politically, there are other priorities in the United States - here private investments and initiatives dominate. State funding is less central than in the EU or China, but there are programs by the Ministry of Defense or the Department of Energy indirectly support AI research (e.g. for autonomous vehicles, which also benefits logistics). More recently, however, AI strategies are also discussed nationally, in particular to strengthen the industrial basis. Overall, one can say: American companies drive AI pragmatically in logistics, while politics is slowly trying to create a framework to catch up internationally.
Japan
Japan is one of the pioneers in robotics and automation - in industry (e.g. automotive production), Japan has a robot density of 399 robots per 10,000 workers and is at the top worldwide. In warehouse logistics, however, Japan has so far been more reserved. Traditional working methods and high appreciation of human work have long led to the fact that the warehouse automation remained comparatively low. But that is now changing rapidly, because Japan is faced with acute demographic problems: there are fewer and fewer young workers, and statutory working time limits force companies to install automation solutions in order to maintain productivity. More and more Japanese companies are therefore turning to modern AI bearing solutions. The government is actively promoting this - there is the "New Robot Strategy" that targets the use of robots in service sectors such as logistics.
In addition, Japan propagates the concept of Society 5.0, a super-networked society in which AI is omnipresent to mastering social challenges (such as the aging society). In this context, for example, automated delivery trucks, robot-based charging and unloading systems and AI-optimized supply chains are worked. We already see Japanese logistics centers that are equipped with driverless forklifts and AI-controlled conveyor systems. So while Japan has started a little later, the automation in camps and AI use should increase suddenly there in the next few years. Culturally, the acceptance of robots is very high, which makes change easier.
China and South Korea (for comparison)
Even if it is not explicitly demanded in the question, a quick glance is worthwhile: China aggressively invests in robotics and AI and is now the world's largest market for industrial robots. Over 50 % of all new robots worldwide are installed in China. The Chinese government subsidizes this development to modernize its supply chains. Especially through the e-commerce boom (Alibaba, jd.com etc.) China has experienced a large thrust in automated warehouse solutions. South Korea, on the other hand, is considered a secret leader in the warehouse automation: over 40 % of the camps there are automated, thanks to high tech affinity and companies such as Coupang, which rely on AI. Such countries serve as a benchmark for what is possible if you consistently introduce technology.
Europe (EU) overall
Europe is moving - with exceptions - at the level of the USA. Within Europe, countries such as Germany, the Netherlands or Scandinavia are well positioned in terms of logistics IT, while others have some catching up to do. With joint projects (e.g. GAIA-X for data infrastructure) and grants, the EU tries to promote progress uniformly. In addition, there are EU-wide research projects in the field of AI for transport and logistics (e.g. to autonomous truck platoons, delivery drone regulation, etc.), which of course also have an impact on the camps, since everything interlocks.
In summary: Germany/EU and the USA are still relatively equal in practical AI use in camps-a lot of potential recognized, but still large parts of the industry without AI. Asia is heterogeneous: China and South Korea very far ahead through forced use, Japan in the catch -up process. Regional politics and funding programs play a major role: While China and sometimes Europe push strongly from the state, the private sector is driving in the United States. In the end, everyone observes: good solutions are taken up internationally. Therefore, a certain convergence can be expected-warehouse logistics are global, and successful AI concepts (whether the “Amazon Way” or the Alibaba robots) will spread worldwide.
Automated warehouse 2050: A vision becomes a reality
A look into the future of warehouse logistics with AI and machine learning promises further exciting developments. A term that falls again and again is the "smart warehouse" - the almost completely digitized and intelligent camp. In such future scenarios, all systems and machines communicate with each other (keyword Internet of Things, IoT). AI forms the brain that controls these networked devices. You can imagine a warehouse in 2050, in which almost all routine activities are automated: Autonomous vehicles were promoted, robots picking, inventory (e.g. recognizing shelf pieces by camera), AI systems monitor everything in real time.
Suitable for:
- The further development and re-optimization of warehouse logistics: warehouses, automation, robotics and AI for a new era of efficiency
Potential developments
We are only at the beginning of what AI can do in logistics. In the future, self -learning algorithms could optimize entire storage complexes in real time - dynamically adapt to the product mix, order situation or even unforeseen events (such as a sudden border closure or raw material shortage). Generative AI (known by Chatgpt & Co.) could help in planning processes, for example designing alternative scenarios for supply chains failures. Robotics is probably more versatile: Today we have specialized robots for certain tasks; In the future, humanoid robots or extremely flexible robot systems could work in the warehouse that take on a wide variety of tasks (gripping, carrying, driving). The first approaches (two -legged robots as warehouse helpers) are already being tested.
The human-machine collaboration is also further refined. Cobots could work closely with people without protective cages, and AI could serve as a personal assistant for every warehouse work - for example through data glasses with augmented reality, which show the employee in real time all relevant information (storage space, next step, warnings). AI-supported wearables could also monitor security (e.g. a bracelet vibrates when a forklift is nearby). All of this serves to improve working conditions and further reduce errors or accidents.
Of course there are also challenges and ethical questions on the way there. A frequently discussed concern is the job question: If more and more is automated in the warehouse, what happens to the warehouse workers? In the short term, certain activities can be omitted - for example, you need fewer manual pickers if robots take on this task. Studies predict a decline in human jobs, especially in simple, repetitive activities. But there are also new roles: AI also creates new jobs - just others. In the future, experts for robotics maintenance, data analysis or AI system support will be increasingly being needed in the future. So while physical routine work decreases, the requirements for technical know-how increase. Companies are required to train and train their employees so that they can make sense in the AI-based environment. Interestingly, some companies even report that automation has enabled them to expand and hire more staff because their business grew. The machine does not necessarily take the job as a whole, but often only the monotonous and stressful parts of it - people can then take on more qualified tasks.
Man against machine? Why hybrid solutions will dominate in the warehouse
Ethical aspects also affect data protection and transparency. AI in the warehouse collects a lot of data, such as the performance of employees (pick -up rates, movement pattern) or for monitoring the environment. Here, personal data must be handled carefully in order to maintain privacy and to keep surveillance at the workplace in the framework. Decisions that AI makes should be understandable - for example, if an algorithm specifies how much an employee should make, transparent criteria are needed to ensure fairness. In this context, the EU emphasizes Trustworthy Ai - Algorithms that are explainable, fair and reliable.
Another topic is security: autonomous robots and AI systems must be designed in such a way that there is no danger to humans. This requires technical standards and tests (e.g. a self -driving forklift must stop 100 % reliably if a person is in the way). Cybersecurity is also becoming more important: a networked camp could be the goal of hacker attacks, so AI systems must be protected against manipulation.
In the future vision you could even imagine completely autonomous camps that work without lighting at night because only machines are active. People would rather take over the control functions. However, people remain a central component for the foreseeable future - if only to ensure flexibility and problem -solving ability in unforeseen situations. The hybrid solution (human + AI) should therefore be the way of the next decades.
Future of warehouse logistics: Why AI is now indispensable
There are also challenges in the practical implementation: Many companies face the question of how to introduce AI. Standards are missing, there is a jungle of providers and success depends on good data quality. If you have bad or incomplete data, you don't get good results with AI ("Garbage in, Garbage Out"). The interoperability between different systems (e.g. the AI of the warehouse and the AI of transport management) must be guaranteed so that a continuous intelligent supply chain is really created.
Nevertheless, the trend is clear: AI is becoming increasingly important in warehouse logistics. In ten years, a lot of what is a pilot project today will of course be part of everyday life. Companies that start today gain valuable experiences and can scale their solutions. Politics in many countries promote this development because it has been recognized that logistics is a key area for the overall economy - and AI The lever to make this key industry more efficient and crisis.
The integration of AI and machine learning in warehouse logistics has already started with visible success in efficiency and speed. It requires investments and swings, but offers enormous opportunities - from cost savings to better customer service to new business models. Regional differences will become smaller over time because Best Practices are adopted globally. The future promises an even more intelligent, largely automated warehouse logistics in which people and machine cooperate closely. At the same time, we have to deal responsibly with the changes - take employees with us, design technology safely and comply with ethical guardrails. If this succeeds, we are facing a logistics world that is much more efficient, more flexible and more resistant than anything we know from the past.
Xpert.Plus warehouse optimization - high-bay warehouses such as pallet warehouses consulting and planning
We are there for you - advice - planning - implementation - project management
☑️ SME support in strategy, consulting, planning and implementation
☑️ Creation or realignment of the digital strategy and digitalization
☑️ Expansion and optimization of international sales processes
☑️ Global & Digital B2B trading platforms
☑️ Pioneer Business Development
I would be happy to serve as your personal advisor.
You can contact me by filling out the contact form below or simply call me on +49 89 89 674 804 (Munich) .
I'm looking forward to our joint project.
Xpert.Digital - Konrad Wolfenstein
Xpert.Digital is a hub for industry with a focus on digitalization, mechanical engineering, logistics/intralogistics and photovoltaics.
With our 360° business development solution, we support well-known companies from new business to after sales.
Market intelligence, smarketing, marketing automation, content development, PR, mail campaigns, personalized social media and lead nurturing are part of our digital tools.
You can find out more at: www.xpert.digital - www.xpert.solar - www.xpert.plus