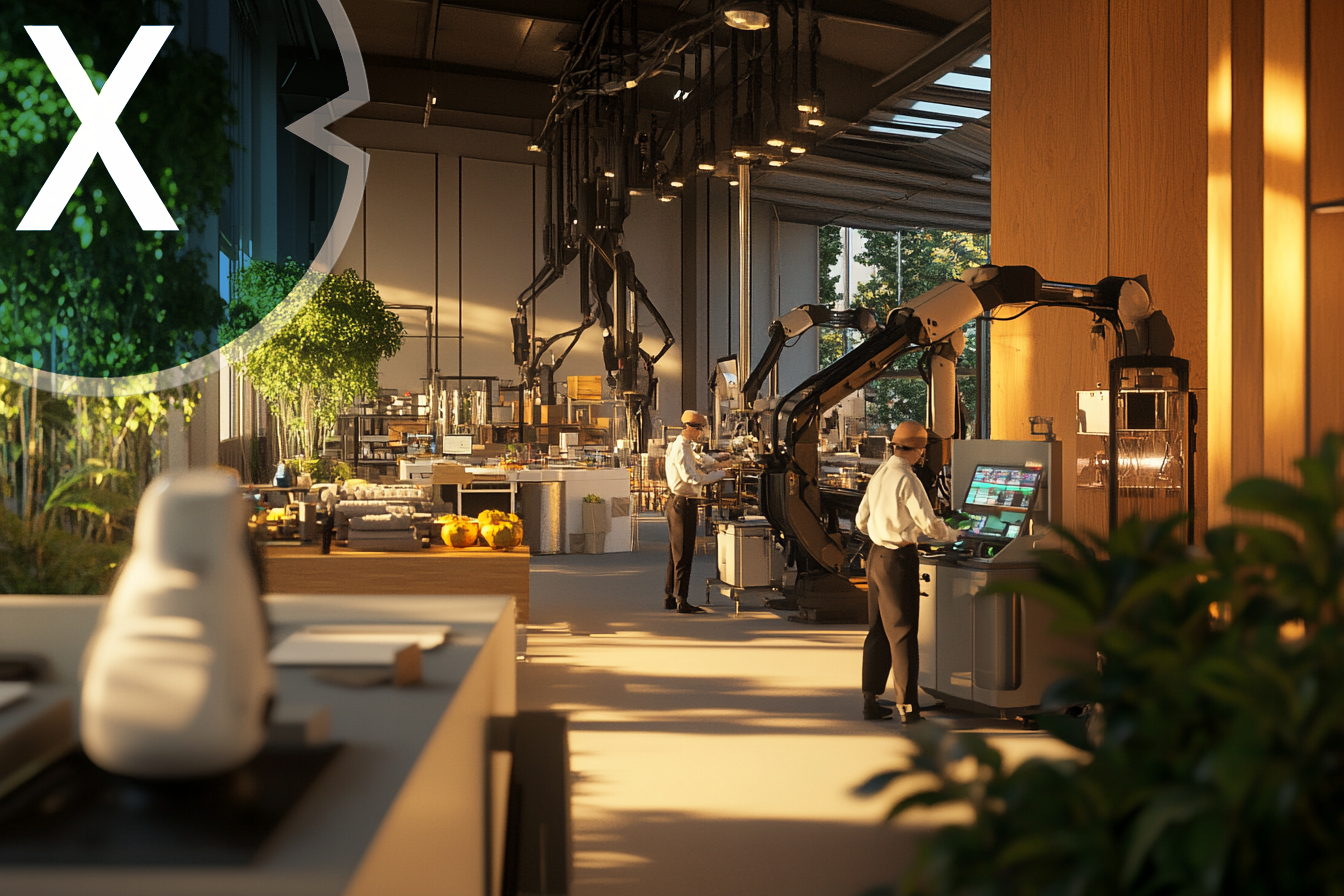
Industry 5.0: Origin, meaning and further development compared to Industry 4.0 – Image: Xpert.Digital
Technology meets people: The revolution of Industry 5.0 compared to Industry 4.0
The human-centeredness of the future: How Industry 5.0 is replacing Industry 4.0
Industrial development has accelerated rapidly in recent decades. While Industry 4.0 advanced the digitalization and automation of production processes, Industry 5.0 is now the focus of a new phase that puts people more at the center again. But what exactly does Industry 5.0 mean, who initiated the concept and how does it differ from its predecessor?
Who initiated the topic of Industry 5.0?
The term Industry 4.0 was first publicly presented at the Hannover Messe 2011 and goes back to Henning Kagermann (former SAP board spokesman), Wolfgang Wahlster (former CEO of the German Research Center for Artificial Intelligence) and Wolf-Dieter Lukas (later State Secretary in the Federal Ministry of Research). This fourth industrial revolution was characterized by the integration of automation, digitalization and the Internet of Things (IoT) into manufacturing.
The concept of Industry 5.0, on the other hand, was significantly advanced by scientists such as Birgit Vogel-Heuser and Klaus Bengler from the Technical University of Munich. They emphasized that industrial automation is facing a paradigm shift in which collaborative work between humans and machines is at the forefront. The European Commission has also adopted the term and recorded it in a document entitled “Industry 5.0: Towards a Sustainable, Human-centric, and Resilient European Industry”. This means that Industry 5.0 is increasingly being anchored at the political level.
What does Industry 5.0 mean?
Industry 5.0 builds on the achievements of Industry 4.0, but goes one step further by putting people more at the center of the production process. While Industry 4.0 focused on automation through technologies such as the Internet of Things (IoT), artificial intelligence (AI) and big data, Industry 5.0 aims to create symbiotic collaboration between humans and machines.
A central aspect of Industry 5.0 is human-machine interaction. This involves humans and robots working together in a collaborative environment to combine human skills such as creativity, decision-making and problem solving with the precision and efficiency of machines. This collaboration takes place, for example, via so-called cobots (collaborative robots), which can interact directly with people.
Another important goal of Industry 5.0 is sustainability. In contrast to Industry 4.0, which focused primarily on increasing efficiency through automation, Industry 5.0 places great emphasis on environmentally friendly production processes and the use of renewable energy. This helps reduce the carbon footprint and promote more sustainable production.
Differences between Industry 4.0 and Industry 5.0
More about it here:
Further development: From automation to collaboration
A key difference between the two concepts lies in the type of interaction between humans and machines:
- Industry 4.0 was primarily about automating processes using technologies such as robotics or IoT. Although humans continued to play a role in the production process, many repetitive or dangerous tasks were delegated to machines.
- In Industry 5.0, on the other hand, people are viewed as creative partners who not only monitor or control machines, but also actively work with them. This collaboration is supported by technologies such as cobots or exoskeletons, which enable humans to perform physically demanding tasks more easily.
In addition, personalization plays a larger role in the new industrial era: While individualized mass production was optimized in Industry 4.0, Industry 5.0 is about adapting products even more closely to the individual needs of customers.
Sustainability as a core principle
Another important aspect of Industry 5.0 is the pursuit of sustainable production processes. While Industry 4.0 focused on increasing efficiency – often without considering ecological aspects – Industry 5.0 aims to integrate environmentally friendly technologies and utilize renewable energies.
This is reflected in the development of energy-efficient systems and in the reduction of CO₂ emissions through optimized production processes. Companies are encouraged not only to pursue economic goals, but also to assume social responsibility.
Resilience: robustness to external disturbances
In addition to sustainability, Industry 5.0 also places great value on resilience, i.e. the ability of a company or a production system to be robust against external disruptions. This includes, for example, delivery bottlenecks or fluctuations in demand.
Through close cooperation between humans and machines, companies can respond more flexibly to such challenges: While machines can ensure consistent quality, humans contribute their ability to quickly adapt to changing conditions.
A paradigm shift in industrial production
Industry 5.0 does not completely replace Industry 4.0 – rather, it is a further development of the existing concept. The technological foundations remain: IoT, AI, and Big Data continue to play a central role in production.
The key difference, however, is that humans are once again taking center stage: instead of simply monitoring machines or performing simple tasks, they are actively collaborating with them – supported by advanced technologies such as cobots or exoskeletons.
This development offers enormous opportunities for both companies and employees: companies can increase their efficiency and at the same time establish more sustainable production processes; Employees benefit from more attractive jobs and a better integration of their creative skills into the production process.
Overall, Industry 5.0 marks an important step towards a human-centered future of industrial production – a future in which technology not only serves to increase efficiency but also promotes human well-being.
Industry 5.0: The fusion of robotic precision and human flexibility
Industry 5.0 marks the next evolutionary stage of industrial development and goes beyond Industry 4.0. While Industry 4.0 relies on digitalization and the networking of machines through the Internet of Things (IoT), Industry 5.0 focuses on collaboration between humans and machines. Technologies such as artificial intelligence (AI), robotics, machine learning and big data are combined with human creativity, flexibility and problem-solving skills to enable even more efficient and personalized production.
Core aspects of Industry 5.0 for industry, production and mechanical engineering
1. Human-machine collaboration
The machines and robots no longer only work independently or in rigid processes, but interact directly with people. As a result, employees can be integrated into the production process as “cobots” (collaborative robots), which enables complex and personalized production processes. This promotes flexibility and adaptability, so that individual customer needs can be better met.
2. Personalized production
Industry 5.0 promotes a “Mass Customization”, ie mass production with the simultaneous possibility of individual adjustment. This development is particularly possible by the use of advanced AI algorithms and the processing of huge amounts of data (big data). Companies can adapt products exactly according to customer requirements and still produce efficiently and inexpensively.
3. Sustainability and resource efficiency
In production, the focus is increasingly on sustainability and the efficient use of resources. Industry 5.0 plays an essential role here by using digital twins and intelligent energy management systems to optimize resource consumption. The circular economy, in which resources are recycled and reused, is also promoted through intelligent systems that minimize waste and conserve raw materials.
4. Artificial intelligence and machine learning
AI and machine learning play a central role in Industry 5.0 by optimizing production processes in real time. These technologies enable proactive maintenance and detection of failures before they occur. The machines can learn from data and adapt to changes, further increasing the efficiency and productivity of production facilities.
5. Ethics and social issues
Another central aspect of Industry 5.0 is the human and ethical factor. People should be at the heart of developments by creating jobs and improving working conditions through collaborative technologies. Ethics plays a major role here, as human-centered production aims to provide fair, safe and pleasant working conditions for employees.
Advantages for companies in industry, production and mechanical engineering
Increased flexibility
Through the collaboration of people and machines, production becomes more adaptable and can react more quickly to changes in the market and customer requests.
Increased productivity
Using AI and automation reduces downtime and increases efficiency, thereby increasing productivity.
Cost reduction
Production costs are reduced by using resources more precisely and avoiding errors and failures.
Better working conditions
Collaboration with intelligent machines relieves employees of dangerous and monotonous tasks, which increases safety and satisfaction in the workplace.
Competitive advantage
Companies that rely on Industry 5.0 at an early stage can position themselves as innovation leaders and assert themselves in the market.
Industry 5.0 brings significant advantages for the industrial, production and mechanical engineering sectors and represents a decisive step towards a human-centered, sustainable and efficient production method.
Suitable for: