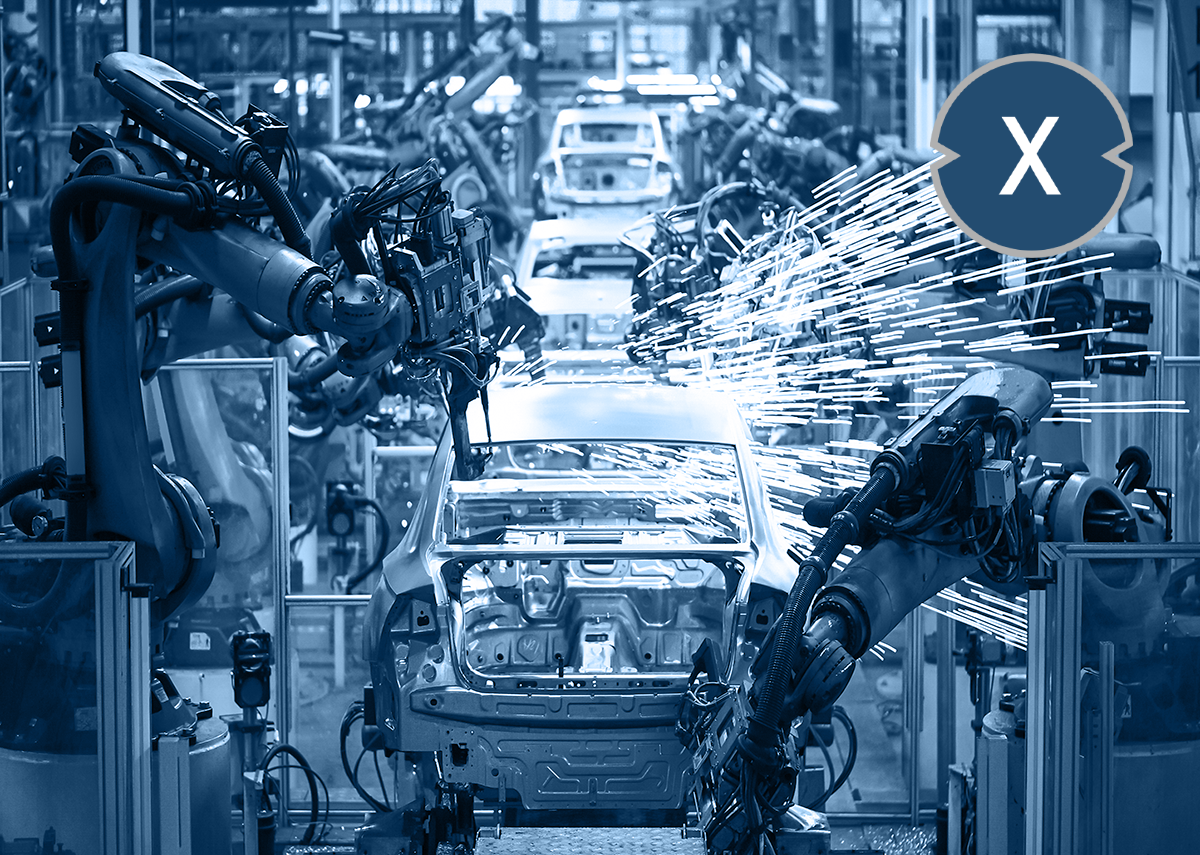
Industrial Automation Engineering (Industrial Automation Technologies) – Image: Xpert.Digital & Jenson|Shutterstock.com
Automation techniques are about the skills to design, create, develop and manage machines and systems, e.g. B. Factory automation, process automation and warehouse automation (e.g. buffer warehouse ).
Automation technology is the integration of standard engineering elements. Automatic control of various control systems for the operation of various systems or machines to reduce human effort and time and increase accuracy. Automation engineers design and maintain everything from electromechanical devices and systems to high-speed robots and programmable logic controllers.
Automation describes a wide range of technologies that reduce human intervention in processes. Human intervention is reduced by defining decision criteria, sub-process relationships and associated actions in advance - and these definitions are implemented in machines.
Suitable for:
Largest automation technology companies worldwide by sales
Industrial automation / automation technology – Most important companies worldwide – Image: Xpert.Digital
The statistics show the largest companies in the automation industry worldwide measured by sales in 2019. With sales of around 12.3 billion US dollars, the US company Emerson reached second place in the global ranking of the largest companies in the field of automation technology.
Industrial automation – Most important companies worldwide by sales in 2019
- Siemens (Germany) – $13,625 million
- Emerson (USA) – $12,255 million
- ABB (Switzerland) – $11,222 million
- Schneider Electric (France) – $7,052 million
- Rockwell Automation (US) – $6,737 million
- Fortive (Danaher) (US) – $4,428 million
- Mitsubishi Electric (Japan) – $3,979 million
- Honeywell (US) – $3,756 million
- Yokogawa Electric (Japan) – $3,427 million
- Ametek EIG (US) – $3,323 million
- Omron (Japan) – $3,236 million
- Endress+Hauser (Switzerland) – $3,113 million
- Phoenix Contact (Germany) – $2,912 million
- Spectris (UK) – $2,085 million
- Sick AG (Germany) – $2,013 million
Automation is achieved through various means including mechanical, hydraulic, pneumatic, electrical, electronic devices and computers, mostly in combination. Complicated systems such as Some systems, such as modern factories, aircraft and ships, typically use all of these combined techniques. The benefits of automation include saving labor, reducing waste, saving electricity costs, saving material costs and improving quality, accuracy and precision.
The most commonly cited benefit of automation in industry is that it is associated with faster production and cheaper labor costs. Another advantage is that it replaces hard, physical or monotonous work. Additionally, tasks that occur in hazardous environments or that are otherwise beyond human capabilities can be performed by machines, since machines can also operate in extreme temperatures or in atmospheres that are radioactive or toxic. They can also be maintained with simple quality controls. However, not all tasks can currently be automated, and some tasks are more expensive to automate than others. The initial cost of installing the machines in the factories is high and failure to maintain a system can result in loss of the product itself.
What are the benefits of automation?
- Increased throughput or productivity
- Improved quality
- Increased predictability
- Improved robustness (consistency) of processes or products
- Increased consistency of output
- Lower direct personnel costs and expenses
- Reduced cycle time
- Increased accuracy
- Relieving people of monotonous, repetitive work
- Increased human freedom to do other things
The main major disadvantage of automation is the high initial cost.
Automation primarily describes machines that replace human activity, but is also loosely associated with mechanization, i.e. machines that replace human work. Coupled with mechanization, the expansion of human capabilities in terms of size, strength, speed, endurance, visual distance & sharpness, hearing frequency & precision, electromagnetic feeling & action, etc., the following advantages arise:
- Relieving people from dangerous workloads and work-related injuries
- Relieving people from dangerous environments
Industrial Automation Engineering – Industrial automation
Automation, i.e. the use of technologies that allow a process or system to run automatically without human intervention, has a long history. The first records of simple automation date back to Ancient Greece, and efforts to automate tasks in the manufacturing industry can be traced back to the 17th century. However, in the 1940s, the term automation was first used to describe the trend toward automating processes in the automotive industry. Today, humans have access to technology like never before, allowing us to automate various tasks in an increasing number of industries.
The Internet of Things and industrial automation
Industrial automation, see also Intralogistics 4.0 , includes a number of technologies that complement each other. On the one hand, there are technologies that enable the design and manufacture of a product using a computer, as well as machines that are involved in the manufacturing, assembly and packaging of the product. On the other hand, in addition to solutions that enable all these devices to be connected and communicated, an infrastructure (also called the Industrial Internet of Things) is also needed. Once connected, the devices can be monitored and controlled as a system, and the data the devices retrieve can be collected and analyzed at the edge of the network or in the cloud, enabling improved production and maintenance efficiency.
Robots as an option for automating physical tasks
In an automated manufacturing plant, machines take over tasks that were previously carried out by human workers. The machines can be simple, such as: B. CNC machines or palletizers designed for a specific task, or more complicated, such as. B. Robots that can be programmed to perform various tasks.
The tasks that robots perform are typically boring, dirty, dangerous, or difficult (collectively referred to as the 4 Ds of robotization) and are therefore better suited to machines. However, not all workers welcome the increasing number of robots in the workplace. Understandably, they are afraid of being replaced by robots. While it is true that some low-skilled workers will lose their jobs to robots, the introduction of robots can lead to the creation of new jobs. The three countries with the most robots per 10,000 manufacturing workers – Singapore, South Korea and Japan – have some of the lowest unemployment rates in the APAC region. Although robots' capabilities are increasing, they still cannot do everything that humans can. The way forward could therefore be to combine the strengths of robots and humans and create workspaces where they can work together. While collaborative robots still only make up a small portion of all robots, their share is expected to continue to grow at least through 2022.
Suitable for:
- Germany is a leader in robotics
- Robotics & automation in the warehouse
- Learn from Amazon Logistics
- Amazon is expanding its share of robots
That's why Xpert.Plus for advice on industrial automation of intralogistics with the Internet of Things
Xpert.Plus is a project from Xpert.Digital. We have many years of experience in supporting and advising on storage solutions and in logistics optimization, which we bundle in a large network Xpert.Plus
I would be happy to serve as your personal advisor.
You can contact me by filling out the contact form below or simply call me on +49 89 89 674 804 (Munich) .
I'm looking forward to our joint project.
Xpert.Digital – Konrad Wolfenstein
Xpert.Digital is a hub for industry with a focus on digitalization, mechanical engineering, logistics/intralogistics and photovoltaics.
With our 360° business development solution, we support well-known companies from new business to after sales.
Market intelligence, smarketing, marketing automation, content development, PR, mail campaigns, personalized social media and lead nurturing are part of our digital tools.
You can find out more at: www.xpert.digital – www.xpert.solar – www.xpert.plus