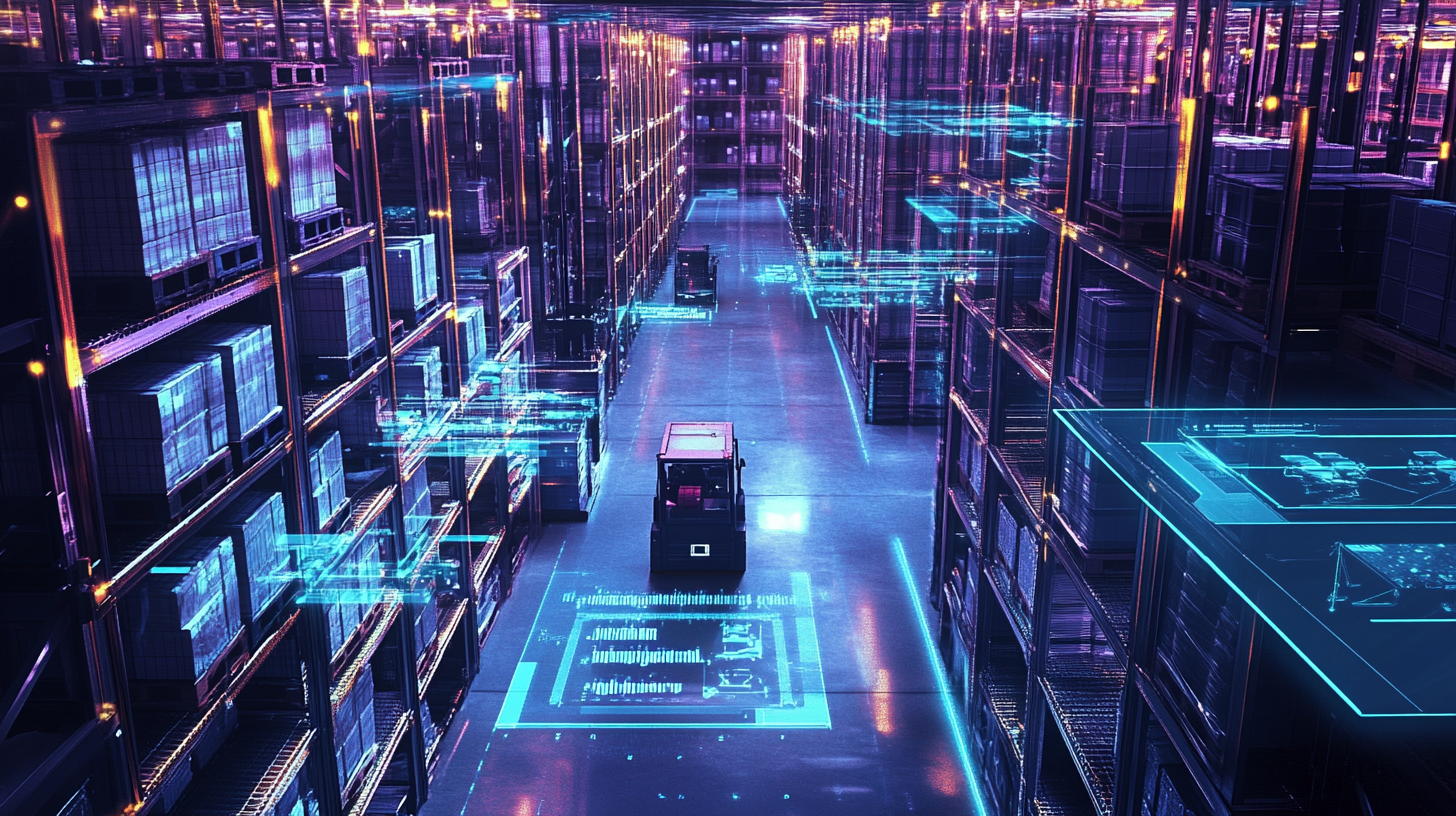
Flying cooling logistics and frozen high-class bearing: Modern pallet warehouse technologies for optimal cold chains-Image: Xpert.digital
Automation in the frozen industry: This is how modern high -bay warehouses work
Infrastructure for freshness: the potential of frozen high -beam bearings
In the modern food industry, frozen logistics play an increasingly important role. With an annual consumption of almost 47 kilograms of frozen food per capita in Germany and an increasing tendency, the market is growing continuously. This report examines the current developments, challenges and technological innovations in frozen logistics with a special focus on frozen high -class bearings as the central infrastructure elements of this specialized industry. The special requirements for temperature management, constant surveillance and the seamless cold chain present companies with complex logistical challenges that can be mastered by modern automation and control technologies.
Suitable for:
- Cold Chain Logistics Strategies: For more sustainable cold logistics and frozen logistics in global industrial logistics
Fundamentals of frozen logistics
The frozen logistics deals with the transport, storage and handling of goods at constant temperatures between -25 and -18 degrees Celsius. This specialized form of logistics is essential for the food industry, especially for manufacturers and dealers of frozen products such as ice cream, baked goods, meat, vegetables, ready meals and potato products. A complete frozen chain under controlled transport conditions is the basic requirement for the preservation of the quality of all frozen products.
The demand for frozen products has increased significantly in recent years, which has led to an increased need for specialized storage infrastructure. This trend is also strengthened by the growing online food trade with its wide range and comfortable delivery service. The challenge for logistics service providers is to operate this increasing demand and at the same time meet the strict temperature and quality requirements.
The frozen logistics include various elements: from manufacturing to storage and transport to delivery to the end customers. Each step in this chain requires specialized facilities and technologies to maintain the necessary temperatures. Central elements of this infrastructure are frozen high -lace warehouse, frozen transport vehicles and covering devices, all of which are designed for the special requirements of the frozen area.
Market development and current challenges
The market for frozen products is growing constantly, with the variety and the offer in recent years in a clear upward trend. This development presents the industry with several central challenges.
One of the greatest challenges in frozen logistics is the ongoing shortage of workers. The extreme working conditions at temperatures of -18 ° C and below make it difficult to find and keep qualified staff. The physical stress and the need to wear warm protective clothing contribute to the low motivation of the employees. This situation is exacerbated by increasing wage costs, which affects the profitability of the companies and increases the pressure to automate.
Another critical factor is the high energy consumption. Frying bearings need immense amounts of energy to maintain the required low temperatures. This leads to high energy costs, which make up a significant share of operating costs. Companies are therefore faced with the challenge of implementing energy -efficient technologies and devices in order to reduce both costs and environmental pollution.
The increasing demand has also led to an increased need for storage areas. Since the acquisition of new space is expensive, companies have to optimally use the existing storage capacities. This explains the trend towards highly compressed warehouse solutions such as high -bay bearings and automated systems that can use the available space more efficiently and maximize the storage capacity.
Frozen high -bay warehouse as a modern solution
Frozen high -class bearings represent the most modern solution for the challenges of frozen logistics. These specialized systems are designed to store large quantities of frozen products at constant temperatures and optimally use the available space.
Construction methods and dimensions of modern frozen high -bay warehouse
Modern frozen high-bay warehouse is typically designed in siloba way as a canal bearing with shuttle vehicles or shelf operating devices. This self -supporting construction enables maximum use of the available space and offers impressive capacities. The dimensions of these systems are often remarkable:
The Cool Port 2 frozen high -class bearing in Rotterdam, which is operated by Lineage Logistics/Kloosterboer, measures 69 meters in length, 139 meters in width and 41 meters in height and offers space for 60,000 pallet spaces. For this project, 4,100 tons of steel were installed to realize the self -supporting siloba.
Another example is the frozen high -class warehouse of the Coppenrath & Wiese Conditorei, which is about 85 meters long, 34 meters wide and 33 meters high and has over 20,000 pallet parking spaces. The frozen logistics center in Wustermark (TCW) is similarly dimensioned, which provides storage capacities for more than 20,500 pallets.
The Belgian company Coldo is currently building a frozen high -lane warehouse that will offer almost 60,000 pallet parking spaces after its completion at the end of 2025 and will achieve a throughput of 400 pallet movements per hour.
Performance index and efficiency
The performance of modern frozen high -bay warehouse is impressive. They are designed for high throughput rates in order to meet the requirements of the fast -moving food industry. The Coppenrath & Wiese frozen high-bay warehouse, for example, reaches an output of 200 double games per hour, while the Coldo project is designed for 400 pallet movements per hour.
Another important aspect is efficiency in loading. In Cool Port 2, four trucks can be unloaded per hour, which corresponds to an hourly goods input of 136 pallets. This high performance is crucial for the smooth handling of the logistics processes.
Energy efficiency is another advantage of modern frozen high -bay warehouse. Due to the compact design and optimized use of space, the volume to be cooled can be reduced, which leads to significant energy savings. The Cool Port 2 frozen high-class warehouse is, for example, 35-45% more energy-efficient than a conventional frozen bearing.
Automation technologies in frozen logistics
The extreme conditions in frozen plants and the shortage of skilled workers have led to a high degree of automation in frozen logistics. Automated processes are worthwhile in all logistical areas, but above all at the lowest temperatures.
Suitable for:
- German industry in the rush of height: Highly bay warehouse transforms logistics sustainable and digital
Shuttle systems and shelf operations devices
One of the most important automation technologies in frozen high-lanes are pallet shuttle systems. These systems enable multiple depth of storage and thus maximize use of space. The Pallet shuttle system Multiflex from Dambach, which is used at Coppenrath & Wiese, works according to the following principle: The carrier transports the “Huckepack” shuttle to the desired channel, which goes into the channel independently, absorbs a pallet there and goes back to the carrier.
A similar system is the Swisslog powerstore system, which is used at Virto in Spain at an ambient temperature of minus 30 degrees Celsius. Constructed as a compact warehouse with multiple-deep alleys, the shuttle system ensures high land use and is particularly suitable for systems with structural restrictions, in which a very high storage density in connection with maximum throughput is important.
Shelf operations (RBG) are another important technology. In the high-performance low cooler of Cool Port 2, six RBG take over the storage and outsourcing of hundreds of heavily loaded pallets per hour at temperatures of up to -25 ° C. A special feature is the LASTELLIT® load record, which accesses profiles that support and protect the pallets. This construction increases the lifespan of the pallets and prevents damaged charge carriers from jamming and the system can be blocked.
Adjustments for frozen conditions
The extreme temperatures in frozen bearings place special requirements for the technology used. Therefore, individual components must be specially adapted so that the systems also work reliably even at these temperatures. These adjustments range from the specific design of timing belts to the use of cold -resistant lubricant and similar components.
The technology kit remains the same, but certain parts must be adapted so that the technologies are and remain compatible with frozen. The cooling phase is an enormously important process, since this shows whether there is, for example, deformations of containers or similar problems.
Software and control systems
Automation in frozen logistics is supported by advanced software solutions. Warehouse Management Systems (WMS) monitor goods today and the vehicles that they transport. Stocks are followed with portable RF scanners and even drones. Computers take over the warehouse loading planning, the product placement and the task management of the employees.
An example of an advanced control system is the Warehouse Execution System (WES) SAVANNA.NET® from Westfalia, which in Cool Port 2 conducts complete warehouse management and material flow control. As an all-in-one software solution, it combines comprehensive functions of warehouse management software and warehouse control software. It also offers a tailor -made interface for customers and maximum transparency of the logistics services.
Xpert partner in warehouse planning and construction
Automated solutions for more efficiency and environmental friendliness
Efficiency and sustainability in frozen logistics
The frozen logistics are faced with the challenge of dealing with high operating costs through energy consumption and at the same time implementing sustainable solutions.
Energy efficiency as a central factor
Frying stores consume immense amounts of energy to maintain the required low temperatures. Modern frozen high -class stores therefore rely on energy -efficient technologies and construction methods to reduce energy consumption.
One example is the compact design of shuttle camps, which reduces the room volume to be cooled and thus causes significant energy savings. In addition, these systems are characterized by a good performance-weight ratio: While large shelf control units weigh several tons, a carrier with a shuttle with a weight of around 1,000 kg moves a load of 1,000 kg.
Due to these and other measures, the Cool Port 2 frozen high-class warehouse in Rotterdam is 35-45% more energy-efficient than a conventional frozen bearing. It was built according to Breeam requirements and is designed to carry up to 2,700 solar modules for energy consumption if necessary.
Sustainable concepts and solutions
Sustainability is becoming increasingly important in frozen logistics. Although climate change and sustainability issues in public discussion have temporarily taken a back seat, this does not change the fact that sustainable management is a prerequisite for a future -proof economy.
Many of the current trends in logistics also contribute to sustainability through efficiency increases. Ultimately, everyone benefits from this: environment, people and companies. Examples of sustainable concepts in frozen logistics are energy -efficient cooling units, optimized storage density and the use of renewable energies.
Automation also contributes to sustainability by optimizing processes and using resources more efficiently. The automation of processes such as warehouse management and route optimization minimizes errors and reduces costs associated with manual work, fuel and storage.
Practical examples of the most modern frozen high -bay warehouse
The theoretical concepts of frozen logistics are practical in various impressive projects worldwide. These case studies show the diversity and innovative strength of the industry.
Cool Port 2 Rotterdam: A prime example of modern frozen logistics
The Cool Port 2 frozen high -class warehouse at City Terminal Rotterdam, which is operated by Lineage Logistics/Kloosterboer, went into operation in January 2022. It initially serves the anchor customer Lamb Weston/Meijer, one of the largest manufacturers of frozen potato products. The export products of the Dutch production locations are handled over the port of Rotterdam, delivering to Cool port 2, loaded onto containers and transported to the Maasvlacts to the container terminals.
The 6-course fully automatic frozen high-lane warehouse is 69 meters long, 139 meters wide, 41 meters high and comprises 60,000 shelf parking spaces. It is operated at temperatures of up to -25 ° C and is equipped with six shelf operating devices that reach a height of around 38 meters.
A special feature of Cool Port 2 is the high-performance sequencing buffer, which supports the immense throughput. The shelf control units store the goods unsorted and on the distance, only in the buffers it is sequenced in a container -friendly manner. This combination of compact storage, high capacity and enormous loading speed makes Cool Port 2 a lighthouse project in the industry.
Treboy high -bay warehouse at COPPENRATH & WIESE Conditerei
The Conditerei Coppenrath & Wiese (CCW) has built a frozen high-lamely warehouse in its logistics center, which is internally referred to as “Tiefkühl-Hochamalllager 6 (TK-HRL 6)”. With a length of about 85 meters, a width of 34 meters and a height of 33 meters, it offers space for 20,000 pallet spaces.
What is special about this project is the use of the Palette shuttle system Multiflex from Dambach. It enables a higher parking space capacity than with the previously used systems with shelf operating devices and individual place access. The system, which is tempered and oxygen -reduced to -25 degrees C, has 12 levels and can absorb both Euro pallets and industrial pallets.
With 200 double games per hour, the symmetrically built system enables a very high pallet envelope. At least six conventional shelf control units would have been required for this service.
Further projects and application examples
The Belgian company Coldo, a provider of frozen logistics and specialist for Third-Party Logistics (3PL), is currently building a state-of-the-art frozen high-class bearing that is scheduled to go into operation at the end of 2025. Equipped with 32 “Movu Atlas” pallet shuttles, it will offer almost 60,000 pallet parking spaces and reach 400 pallet movements per hour. Coldo will store a variety of frozen products in the freezers, including meat, ice cream, bread, vegetables, fries fries and potatoes.
Another example is the planned frozen bearing from Wiesbauer Gourmet Gastro, which is scheduled to go into operation in autumn 2026. In this project, the focus is on automation in order to make the work processes more efficient and relieve the staff from physically demanding activities. A planned automatic small division warehouse is operated at around -22 degrees Celsius and has tablar as a charging average. With a capacity of over 21,000 parking spaces, it will offer enough space for flexible warehousing.
Trends and future prospects
The frozen logistics are continuously developing, driven by technological innovations and changing market requirements.
Digitalization and automation
One of the most remarkable trends in today's logistics is the digitization of all processes. The automation of processes such as warehouse management and route optimization minimizes errors and reduces costs associated with manual work, fuel and storage. In 2025, the logistics and supply chain industry will continue to be strongly influenced by new technologies such as AI, automation and robotics.
The intralogistics industry is preparing for further innovations. For example, the intralogistics specialist SSI Schäfer announces a “revolutionary automation solution” for LogiMat 2025, which is said to be a game changer for the industry. The focus of the exhibition includes robotics applications, shuttle and hanging technology as well as solutions for frozen logistics.
Artificial intelligence and machine learning
Artificial intelligence (AI) and machine learning are increasingly integrated into daily operation in order to optimize processes and increase efficiency. In the logistics industry, AI is no longer a separate trend, but an indispensable part of almost all logistics trends.
An important aspect for 2025 is the increasing forecast capacity of IT systems, which improves planning and scalability. With increasing digitization, the vulnerability of companies also increases, which makes cyber security more important than ever - especially for a critical industry like logistics.
Robotics in frozen logistics
The use of robots in logistics increases continuously, especially in markets with high labor costs and increasing expectations of quick deliveries. Thanks to the use of robots, warehouse processes are automated and navigated autonomously. They support inventory management through real -time information and enable precise delivery time forecasts.
The robotic solutions include picking robots, sorting robots, pack robots, autonomous vehicles and drones. These technologies are particularly interesting for frozen logistics, since they can reduce the use of human labor under extreme temperature conditions.
Suitable for:
- Daifuku Europe: Automation of intralogistics through autonomous mobile robots (AMR) and automated guided vehicle (AGV)
The frozen logistics in change
Frozen logistics are faced with numerous challenges, but also offers a wide range of opportunities for innovation and optimization. The growing market for frozen products, the shortage of skilled workers, the high energy costs and the increasing demands on sustainability are driving the development of new technologies and concepts.
Frozen high -bay warehouse plays a central role as an efficient and sustainable solution for storing large amounts of frozen products. With impressive dimensions, high performance and innovative technologies, you set new standards in the industry. Automated systems such as shuttle solutions and shelf operations optimize space use and throughput, while advanced software solutions ensure transparency and efficiency.
The future of frozen logistics will be shaped by digitization, AI and robotics. These technologies will help to further optimize the processes, to improve energy efficiency and to facilitate working conditions. At the same time, sustainability aspects will gain in importance in order to reduce the ecological footprint of energy -intensive frozen logistics.
For companies in frozen logistics, this means that they have to continuously invest in new technologies and concepts in order to remain competitive and to meet the changing market requirements. The successful examples such as Cool Port 2 in Rotterdam or the frozen high -class warehouse from Conditorei Coppenrath & Wiese show that such investments pay off due to higher efficiency, lower operating costs and improved customer satisfaction.
Xpert.Plus warehouse optimization - high-bay warehouses such as pallet warehouses consulting and planning
We are there for you - advice - planning - implementation - project management
☑️ SME support in strategy, consulting, planning and implementation
☑️ Creation or realignment of the digital strategy and digitalization
☑️ Expansion and optimization of international sales processes
☑️ Global & Digital B2B trading platforms
☑️ Pioneer Business Development
I would be happy to serve as your personal advisor.
You can contact me by filling out the contact form below or simply call me on +49 89 89 674 804 (Munich) .
I'm looking forward to our joint project.
Xpert.Digital - Konrad Wolfenstein
Xpert.Digital is a hub for industry with a focus on digitalization, mechanical engineering, logistics/intralogistics and photovoltaics.
With our 360° business development solution, we support well-known companies from new business to after sales.
Market intelligence, smarketing, marketing automation, content development, PR, mail campaigns, personalized social media and lead nurturing are part of our digital tools.
You can find out more at: www.xpert.digital - www.xpert.solar - www.xpert.plus