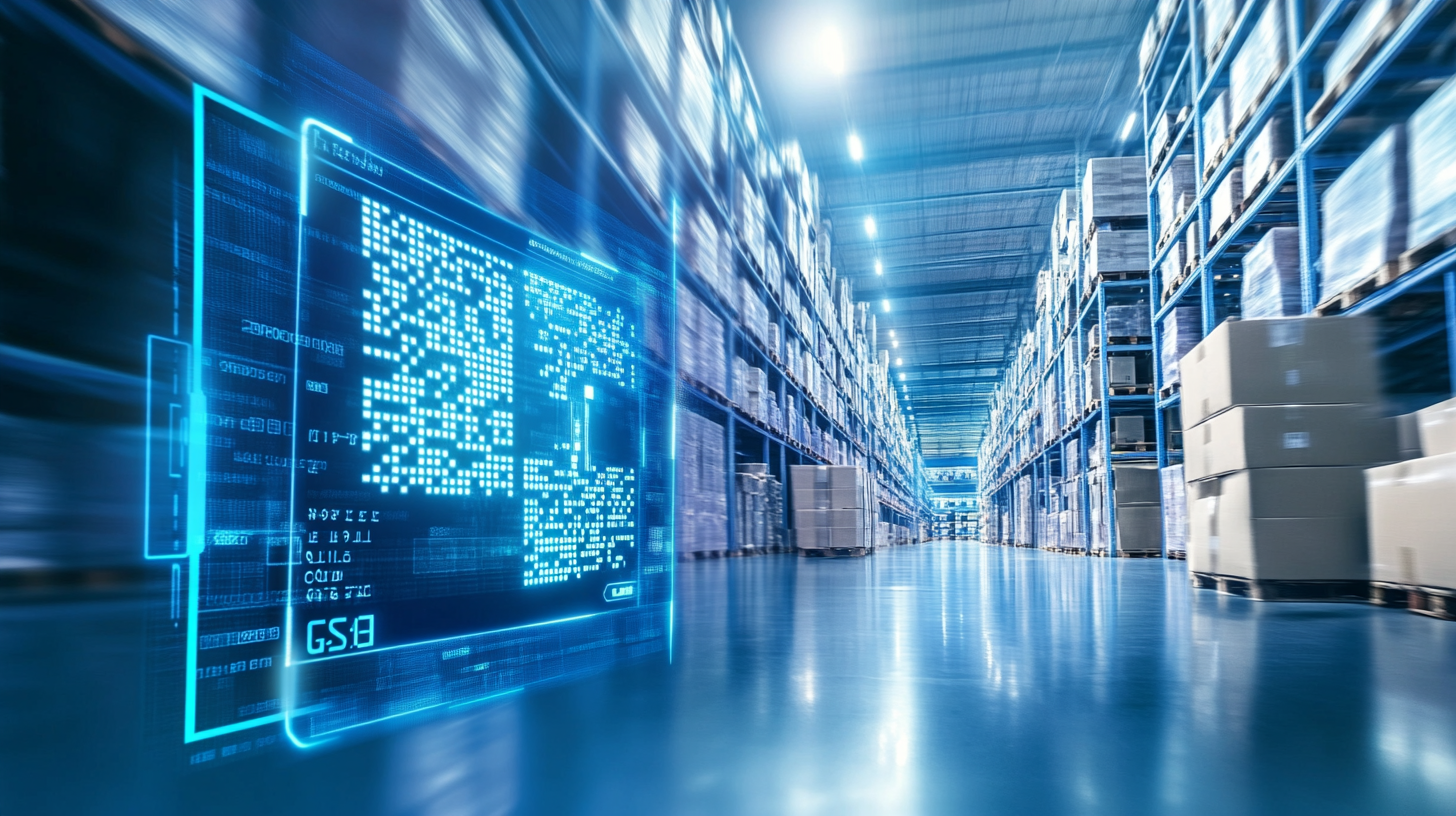
The choice between Datamatrix code (DMC) and Radio Frequency Identification (RFID)? - Image: Xpert.digital
The optimal labeling technology: How to make the right decision
RFID vs. Datamatrix? Smart solutions for manufacturing and logistics
The choice between Datamatrix code (DMC) and Radio Frequency Identification (RFID) is a central decision in modern manufacturing and logistics processes. Both technologies offer unique advantages and are optimized for specific applications. While the DMC represents a proven method for labeling products, RFID enables wireless and automated collection of data. The right choice depends on various factors such as costs, efficiency, environmental conditions and the individual requirements of a company.
This detailed guide illuminates the properties, advantages and disadvantages as well as potential applications from both technologies in order to offer a well-founded basis for decision-making.
Suitable for:
Basics of Datamatrix code and RFID
Datamatrix code (DMC)
The Datamatrix code is a two-dimensional barcode that stores information from a matrix of black and white modules. It can be both square and rectangular and is characterized by a high data density in a small space. A typical DMC can save up to 1,556 bytes of data, including alphanumeric characters, special characters and binary data.
The structure of a DMC consists of:
- Search pattern: an L-shaped limit that serves as a guide.
- Change pattern: a limitation that defines the size and position of the matrix.
- Data area: Here the actual information is saved and provided with an error correction.
DMCs are often used in the automotive, aviation and space industry and in medical technology, since they can be accommodated on small areas and can be applied directly to surfaces such as metal or plastic.
Suitable for:
Radio Frequency Identification (RFID)
RFID is a technology for wireless identification and persecution of objects using electromagnetic fields. An RFID system consists of:
- RFID-TAGE: Contain a microchip for storing information.
- Reading devices (reader): Collect the data of the RFID tags via radio waves.
- Antenne: Allows the data to be transmitted.
There are different RFID types:
- Passive RFID: The tags do not have their own energy source and use the electromagnetic field of the reader for transmission.
- Active RFID: The tags have their own power source and can bridge larger distances.
RFID is often used in logistics, retail and industrial production, since the technology enables rapid and contactless recording of large amounts of data.
Comparison of technologies
Data volume and storage capacity
DMCs store fixed data records such as serial numbers, batch numbers or manufacturing information. They are ideal for applications where no dynamic data update is required.
RFID tags offer greater storage capacity and enable continuous data update over the entire life cycle of a product. This is particularly advantageous in processes that require ongoing surveillance, for example in inventory management or in the tracking of production steps.
Reading speed and efficiency
DMCs must be read out with a scanner, which requires direct visual contact. This can be time -consuming in fast production processes or in large quantities of objects.
RFID, on the other hand, enables the simultaneous reading of several tags without visual contact. This leads to a significant increase in efficiency in automated processes, especially in areas with high throughput such as warehouses or manufacturing streets.
Environmental conditions and robustness
DMCs can be impaired by poor lighting, low contrasts or dirt in their readability. Nevertheless, they have a high fault tolerance and remain readable even with damage of up to 30 %.
RFID tags are insensitive to environmental influences such as dirt or moisture. However, metallic or liquid environments can affect the signal transmission, which leads to reading errors or limited range.
Costs and implementation
DMCs are inexpensive in the implementation, since they can be printed directly on the object or engraved and do not require expensive special devices.
RFID systems have higher acquisition and implementation costs. However, the long -term advantages such as automation, error reduction and reusability of the tags can justify this investment.
Application examples and decision criteria
Reusability of the marked object
- Closed loop systems: If an object is used several times and remains within a closed system, RFID is advantageous due to the updates of the tags.
- Open loop systems: In open processes in which the object leaves the process after one use one, a DMC is often sufficient and cost-efficient.
Frequency of data update
- One -time labeling: DMC is ideal for serial numbers or fixed product information.
- Dynamic data update: RFID is advantageous if information has to be continuously updated, e.g. B. at warehouse management.
Sacrifice for the marking
- Limited space: DMCs can be attached on very small areas.
- In terms of space: RFID tags need more space, but enable wireless data transmission.
Necessity of visual contact
- Direct visual contact possible: DMC is sufficient.
- No visual contact possible: RFID also enables reading through packaging or obstacles.
Environmental conditions
- Polluted or poorly illuminated environments: RFID offers advantages because no optical recording is required.
- Metallic or liquid environments: DMC is less prone to interference and therefore more suitable.
Suitable for:
Combination of DMC and RFID
In many cases, companies do not have to choose between DMC and RFID, but can combine both technologies. A common example is an RFID label with printed DMC.
Advantages of a combination
- Redundanz: If an RFID day cannot be read out, the DMC is available as a backup.
- Flexibility: The DMC can be used for manual processes, while RFID supports automated systems.
- Extended functionality: During DMC, RFID can save additional process data.
The choice between Datamatrix code and RFID depends on various factors, including the type of application, environmental conditions and costs. While DMCs offer an inexpensive, reliable solution for many labeling tasks, RFID enables more efficient and automated data acquisition without visual contact. In many cases, the combination of both technologies offers the best solution to ensure both efficiency and flexibility.
Companies should carry out a detailed analysis of their requirements in order to select the optimal technology for their specific needs. The future of industrial labeling will increasingly include hybrid solutions that combine the advantages of both systems and thus further improve efficiency and transparency in manufacturing and logistics.
Xpert partner in warehouse planning and construction
Technologies in comparison: When Datamatrix and when RFID makes sense - background analysis
The question of whether you choose Datamatrix codes (DMC) or radio frequency zeating (RFID) is a central point in many logistics and production processes. There is no general answer here, because the best choice depends heavily on the specific requirements of the respective application. Both technologies have their strengths and weaknesses, and understanding these differences is crucial for successful implementation. So let's consider some basic questions that can help you with decision -making, and let's go into detail in order to convey a comprehensive picture:
The life cycle of the object: Closed loop vs. Open-Loop
One of the first questions you should ask yourself is whether the marked object is reused or lost at the end of its path within the process chain. Here a distinction is made between “closed loop” and “open loop” applications. RFID is often the better choice for a closed loop application, such as in repeated use of reusable containers. Repeated use requires continuous persecution and update of the data, which can be realized more efficiently with RFID. An RFID day accompanies the property via several runs and can be described with new information. Open loop applications, on the other hand, in which the object leaves the process chain and not recurred, such as with disposable packaging, are a typical area of application for DMC. The Datamatrix code is applied once and does not have to be changed. Here is a clear identification in the foreground, which can also be carried out automatically via scans if necessary.
Data acquisition: once vs. repeated
The question of data acquisition is closely linked to the life cycle. If the labeling is made once and the data remain unchanged, the DMC is often the most practical solution. It serves the unique identification and can be printed on a wide variety of materials. However, if data is read, written or updated several times within the process chain, RFID has an advantage. The contactless read and describe the RFID tags enables flexible and dynamic processes. One can imagine, for example, that in a production process, the RFID day of a workpiece at various stations is provided with the respective process data such as time stamps, quality features or other relevant information.
Data volume: Little vs. A lot
The required data volume is another crucial factor. DMCs are limited in the amount of storable data. They are ideal for storing a clear serial number, article number or other short alphanumeric information. RFID is the more suitable technology for complex or extensive amounts of data. On an RFID day, far more information can be saved, including detailed product information, batch numbers, production data or even instructions for the further processing process. This is particularly important if there are extensive traceability and documentation requirements.
Process data: yes or no?
The question of whether process data is to be saved on the object is often decisive for the choice between the two technologies. If only simple identification is required, the DMC is usually sufficient. However, when it comes to recording and pursuing process data, RFID has a clear advantage. The possibility of saving process data directly on the day enables decentralized data acquisition and management. The data are available directly on the object and can be called up and updated in real time, which significantly improves process control and transparency. For example, it is possible to understand the entire résumé of a product from production to recycling.
Processing speed: high or not relevant?
The processing speed is another aspect that is of great importance in many industrial environments. If it does not matter to high speeds, a DMC can be the right choice. The code is then scanned manually or automatically. However, RFID systems are able to capture large quantities of objects at the same time and at high speed, without direct visual contact. In a logistics center in which thousands of products are moved per minute, the contactless and faster recording with RFID has a clear advantage. Here, the time gain can provide a decisive competitive advantage through the automatic reading of data.
Ambient conditions: light, contrast and visual contact
The environmental conditions also play a role in the decision. As a rule, DMC scanners need good lighting conditions and a sufficient contrast to reliably record the codes. In environments with poor lighting conditions or on surfaces with little contrast, recording may be difficult or impossible. RFID systems are more tolerant in this regard because radio technology works regardless of light and contrast. So they can also be reliably usable in dark or dirty environments.
Another important point is visual contact. While DMC scanner need direct visual contact with the code, RFID tags can also be read through non-metallic materials. This is a great advantage if the tags are, for example, in the packaging or behind a cover.
Space requirements and sources of interference
The size of the available space for labeling is also an important criterion. DMCs can be printed very small and are therefore well suited for objects with little space. RFID tags need more space, especially if they contain an antenna. Sources of interference, such as dirt or liquids, can affect the readability of DMCs, since the surface is dirty and the contrasts are lost. RFID tags, on the other hand, are less susceptible to dirt because they can be read without direct contact. Metals and liquids, in turn, can interfere with the RFID systems radio waves, which can affect the reading range and reliability. In environments with many metals or liquids, the use of DMCs is often the better choice.
The synergy: DMC and RFID in combination
But it doesn't always have to be a “either/or”. A combination of DMC and RFID can often be the optimal solution. A frequent scenario is an RFID label with a printed DMC. The DMC serves direct identification on the object, for example in the goods receipt or in quality control. The RFID day, on the other hand, fulfills further tasks, such as the pursuit of the object through the entire process chain and the storage of relevant process data. The advantage of this combination lies in flexibility. The DMC enables simple and inexpensive identification, while RFID offers the opportunity to dynamically record and manage data without the need for visual contact. For example, the data of the RFID tag can be used to pursue production progress, to manage the inventory or to ensure traceability. The combination of DMC and RFID also enables redundant systems to build up and increase the accuracy of data acquisition.
Specific applications and their requirements
In order to understand the advantages and disadvantages of both technologies even better, we look at some specific applications:
Logistics and supply chain management
Both technologies are often used in logistics. RFID tags are used to track goods in large camps and distribution centers. They enable quick and automated recording of goods movements and ensure efficient warehouse management. DMC is used here to identify articles on boxes and pallets, especially when it comes to tracking and sorting programs.
Production and production
Both DMC and RFID play an important role in production. DMC are often used for direct labeling of components and products to ensure traceability. RFID tags are used to monitor the production progress, control the material flow and ensure the product quality. For example, they can be attached to tools, machines or workpieces in order to monitor their use and condition.
Healthcare
RFID is used in the healthcare system to identify patients, pursue medical devices and monitor compliance with hygiene regulations. DMC is used here for the identification of medication and medical consumables to ensure counterfeiting and correct assignment.
retail trade
RFID tags are used in retail to accelerate the inventory, prevent theft and improve the customer experience. DMC are used here to scan products at the cash register and to record information such as the price and the product features.
Optimized processes: Why the combination of Datamatrix and RFID is the future
The choice between Datamatrix Codes and RFID is not an easy decision and depends on a variety of factors. It is important to understand the respective advantages and disadvantages of both technologies to find the right solution for the specific requirements. A careful analysis of the life cycle of the object, the required data volume, the necessary processing speed, the environmental conditions and the potential sources of interference is crucial for successful implementation. In many cases, the combination of both technologies can be the best solution to optimally use the advantages of both systems. Ultimately, the decision is always an individual decision based on a comprehensive analysis of the specific requirements and framework conditions. The future will show that the technology is developing so that the use and application is becoming more and better, cheaper and faster. It is now important to recognize the advantages and to use them profitably.
Suitable for:
Xpert.Plus warehouse optimization - high-bay warehouses such as pallet warehouses consulting and planning
We are there for you - advice - planning - implementation - project management
☑️ SME support in strategy, consulting, planning and implementation
☑️ Creation or realignment of the digital strategy and digitalization
☑️ Expansion and optimization of international sales processes
☑️ Global & Digital B2B trading platforms
☑️ Pioneer Business Development
I would be happy to serve as your personal advisor.
You can contact me by filling out the contact form below or simply call me on +49 89 89 674 804 (Munich) .
I'm looking forward to our joint project.
Xpert.Digital - Konrad Wolfenstein
Xpert.Digital is a hub for industry with a focus on digitalization, mechanical engineering, logistics/intralogistics and photovoltaics.
With our 360° business development solution, we support well-known companies from new business to after sales.
Market intelligence, smarketing, marketing automation, content development, PR, mail campaigns, personalized social media and lead nurturing are part of our digital tools.
You can find out more at: www.xpert.digital - www.xpert.solar - www.xpert.plus