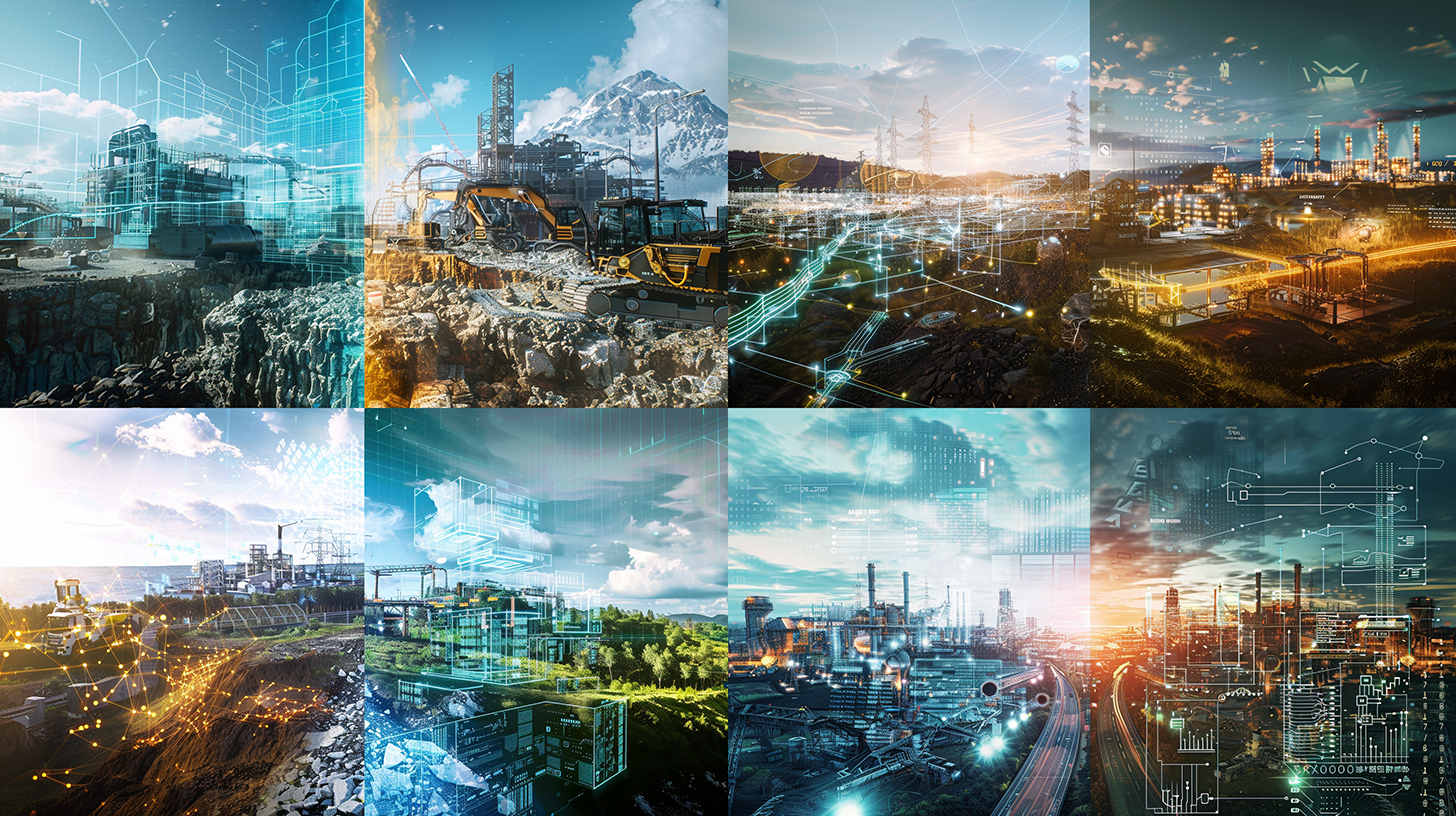
The digital twin in industry: The bridge between the virtual and physical world - Image: Xpert.Digital
Real-time data, maximum efficiency: The role of digital twins in modern industry
Digital Twins explains: The key to the connected industry of tomorrow
A digital twin represents the digital representation of a physical object, process or system. This representation is based on real-time data and is closely linked to its physical counterpart. This innovative technology connects the physical and digital worlds and forms a key component of modern industry, especially in the context of Industry 4.0.
Definition and concept
A digital twin goes far beyond simple digital models. It is a living image of the physical object that is continuously fed with data and can therefore act dynamically. Technology is not just a tool, but a strategic instrument to increase the efficiency and innovative power of companies.
The basis of the digital twin includes three essential elements:
- The physical object: The real item whose data is being collected.
- The virtual model: A digital clone that displays all relevant information.
- The Data Connection: Real-time interfaces that enable data flow between physical and digital space.
Functions and possibilities
The digital twin is a powerful tool that supports companies in many areas. Key features include:
- Real-time data analysis: Continuous data collection enables in-depth analysis and immediate insights.
- Simulation and optimization: Companies can test scenarios before implementing them in the real world.
- Error detection: Early identification of weak points reduces failures.
- Data-driven decisions: Informed decisions through precise analyzes and forecasts.
Areas of application in industry
Digital twins have proven to be a versatile technology and are used in various industrial sectors:
1. Production and manufacturing
- Optimization of production lines by simulating scenarios.
- Virtual commissioning of machines, saving time and costs.
2. Predictive Maintenance
- Continuous monitoring of machine conditions to accurately predict maintenance work.
- Avoiding unexpected failures and increasing operational efficiency.
3. Product development
- Virtual prototyping accelerates development cycles and reduces material costs.
- Simulation of physical properties before actual manufacturing.
4. Logistics and transportation
- Optimizing supply chains through real-time data analysis.
- Improving material flows in automated warehouses and autonomous vehicles.
5. Energy and environment
- Monitoring and optimization of energy systems to promote sustainability.
Benefits for the industry
The introduction of digital twins brings with it a variety of advantages:
1. Increased efficiency
Simulations and precise analyzes lead to better coordinated production processes and reduce rejects.
2. Cost reduction
Optimized maintenance planning and fewer failures save companies significant resources.
3. Customization
Through collected data, products can be individually tailored to the needs of customers.
4. Sustainability
Optimized processes mean lower consumption of resources and reduced environmental impact.
Implementation challenges
Although the digital twin offers immense benefits, companies face some challenges:
1. IT infrastructure and data management
Building a robust infrastructure is costly and requires expert knowledge.
2. Data integration
The seamless integration of IoT technologies and the processing of large amounts of data represent technical hurdles.
3. Interdisciplinary collaboration
Implementation requires cooperation between IT, production and management teams.
4. Security aspects
The protection of sensitive data from cyber attacks must be guaranteed.
How does a digital twin work?
The way a digital twin works is based on the networking of physical objects and their digital representation. This process is highly complex and integrates various technologies:
1. Sensors and data sources
Sensors continuously collect information such as:
- temperature
- Pressure
- Position and speed
- Energy consumption
- Environmental conditions
This raw data forms the basis for the digital image.
2. Data transfer
The collected data is transmitted to the digital platform in real time via protocols such as MQTT or HTTP. IoT hubs serve as intermediaries between devices and cloud services.
3. Digital modeling and AI
Using artificial intelligence (AI) and machine learning, a dynamic model is created from the data. This model:
- Captures patterns and trends.
- Allows predictions (predictive analytics).
- Identifies anomalies early.
4. Simulation and interaction
The digital twin simulates processes and makes it possible to test possible scenarios without endangering physical resources. At the same time, it can actively influence the physical object, for example through control commands.
5. Visualization
Technologies such as augmented reality (AR) or 3D models make the digital twin tangible. They make it easier to understand complex data and systems.
Future areas of application
As technologies such as the Internet of Things (IoT), 5G and artificial intelligence continue to develop, digital twins are becoming increasingly powerful. Future areas of application could include:
- Autonomous factories where digital twins monitor and control all processes.
- Smart cities in which twins make the infrastructure more efficient.
- Healthcare, with the simulation of patient models for personalized medicine.
The digital twin will not only remain a tool for industry, but will also revolutionize other areas of life.
The digital twin connects the physical and virtual worlds in an innovative way and enables companies to make their processes more efficient, reduce costs and work more sustainably. Despite the implementation challenges, this technology remains an essential part of Industry 4.0 and a bridge to a data-driven future. Those who recognize and use the potential of the digital twin today will be among the pioneers of a new industrial era tomorrow.
Suitable for: