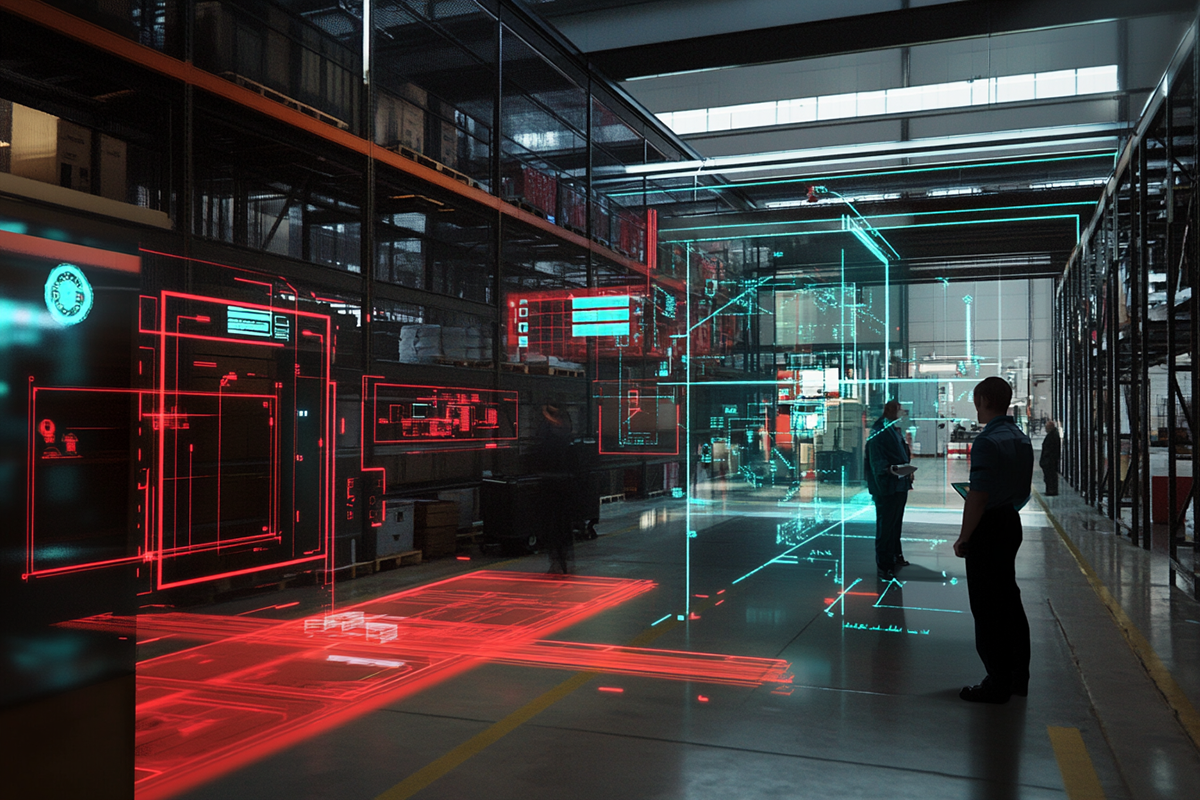
Do you know the Bottleneck Walk? Identifying bottlenecks in intralogistics and logistics in general – Image: Xpert.Digital
🔍 Identification of bottlenecks in intralogistics and logistics: The Bottleneck Walk
📦 The efficient design of processes plays a crucial role in modern logistics and intralogistics. Companies are under constant pressure to optimize their operations and reduce costs while ensuring customer satisfaction through on-time deliveries. One of the biggest challenges in this context is identifying and eliminating bottlenecks that can hinder the overall flow of materials and information. A proven tool for analyzing such bottlenecks is the so-called “Bottleneck Walk”. But what exactly does it mean and how can it contribute to improving logistical processes?
❓ What is a bottleneck?
Before we delve into the Bottleneck Walk, it is important to understand the term “bottleneck” or “bottleneck.” In logistics, a bottleneck refers to a point within a process or supply chain where capacity is limited. This limitation causes the entire process to slow down or even come to a halt. A classic example is a production line where one machine works slower than the others. Although the other machines could produce faster, they have to wait for the slowest link in the chain.
Bottlenecks can occur in various areas:
- Material flow: When certain machines or means of transport do not have sufficient capacity.
- Information Flow: When data is not processed or forwarded in a timely manner.
- Personnel: When there are not enough qualified employees available or workers are used inefficiently.
- Storage: When storage space is not used optimally or storage processes are inefficient.
🚶♂️ The Bottleneck Walk as a method
The Bottleneck Walk is a systematic method for identifying such bottlenecks. This is a kind of “walk” through the various processes of a company, specifically looking for places where delays or inefficiencies occur. This method has its origins in lean management and is often used in production, but can also be transferred to other areas such as intralogistics.
The goal of the bottleneck walk is to analyze the entire process flow and find out exactly where there is a problem. It's not just about identifying obvious problems, but also uncovering hidden bottlenecks that may not be immediately apparent at first glance.
📋 How does the Bottleneck Walk work?
A bottleneck walk follows a structured approach. Essentially it consists of the following steps:
1. Preparation
Before the actual walk begins, all relevant data should be collected. This includes production plans, inventory levels, lead times and other key figures that provide information about the current status of the processes.
2. On-site observation
The next step is to observe the actual workflow on site. This can happen in a warehouse, manufacturing facility, or distribution center. The aim is to understand the real material and information flow and to identify possible deviations from the planned processes.
3. Identification of bottlenecks
During the walk, we specifically look for places where there are delays. These can be, for example, machines that constantly fail or are overloaded, transport routes that are blocked, or work processes that are unnecessarily complicated.
4. Analysis of causes
Once a bottleneck has been identified, it is important to find out why the bottleneck exists. Methods such as the “5 Whys” principle – a root cause analysis technique – are often used to uncover deeper problems.
5. Development of measures
Once the causes of the bottleneck have been identified, measures must be developed to eliminate or at least mitigate it. This can happen through technical solutions such as purchasing new machines or through organizational changes such as better personnel deployment planning.
6. Implementation and monitoring
The measures developed must then be implemented and their success continuously monitored. It is important to ensure that the bottleneck has actually been eliminated and that no new problems arise.
🔧 Typical bottlenecks in intralogistics
There are some typical areas in intralogistics where bottlenecks often occur:
Warehouse management systems (WMS)
An inefficient warehouse management system can result in goods being stored incorrectly or orders being processed with delays.
Picking
Picking goods is often a time-consuming process. If this is not optimally designed - for example due to a lack of automation - this can lead to significant delays.
Transport routes within the warehouse
Long transport routes or poorly organized storage areas can result in goods being in transit for an unnecessarily long time.
Lack of qualified personnel
In many camps there is a shortage of well-trained specialists. This can result in certain tasks not being able to be completed efficiently.
🌟 Advantages of the Bottleneck Walk
The Bottleneck Walk offers numerous advantages for companies:
transparency
Transparency is created by taking a direct look at the process on site. It's often small details in daily operations that can have a big impact on efficiency.
Quick problem detection
Because the Bottleneck Walk takes a systematic approach and covers all relevant areas, problems can be identified and resolved quickly.
Cost savings
By identifying bottlenecks early, expensive production downtimes can be avoided.
Improved employee satisfaction
When processes run more smoothly and there is less stress caused by delays, this has a positive effect on the working atmosphere.
🚨 Challenges in implementation
Despite its many benefits, there are also some challenges to conducting a bottleneck walk:
1. Time commitment
A thorough bottleneck walk requires time and resources. It can take several days until all processes have been analyzed in detail.
2. Resistance to change
It is not uncommon for change measures to be met with resistance from employees or managers. It is therefore important to involve them in the process at an early stage and to communicate transparently about the goals of the Bottleneck Walk.
3. Complexity of modern logistics systems
In large companies with complex supply chains, it can be difficult to cover and reconcile all relevant areas.
🛠️ Bottleneck identification tool
The Bottleneck Walk is an extremely useful tool for identifying bottlenecks in intralogistics and logistics in general. A systematic approach can be used to uncover weak points in the flow of materials and information and to develop targeted measures for improvement. Companies not only benefit from greater efficiency and lower costs, but also from happier employees and customers.
In a time of increasing globalization and growing delivery time requirements, it is becoming increasingly important for companies to continually review and adapt their internal processes. The Bottleneck Walk offers a practical solution to this – provided it is carefully planned and carried out.
📣 Similar topics
- 🚶♂️ Increase efficiency: The Bottleneck Walk explained
- 🔍 Detecting bottlenecks: steps for problem analysis
- 🛠️ Bottleneck Walk: Tool for process optimization
- 🚦 Design intralogistics efficiently through bottleneck analysis
- 📉 Reduce costs through targeted elimination of bottlenecks
- 🤝 Employee satisfaction through optimized processes
- 📊 Transparency in the supply chain: The Bottleneck Walk
- 📈 Process analysis made easy: The Bottleneck Walk
- ⏱️ Save time through faster bottleneck diagnosis
- 📦 Warehouse optimization: Focus on bottlenecks
#️⃣ Hashtags: #BottleneckAnalysis #ProcessOptimization #Intralogistics #BottleneckWalk #LogisticsEfficiency
Our recommendation: 🌍 Limitless reach 🔗 Networked 🌐 Multilingual 💪 Strong sales: 💡 Authentic with strategy 🚀 Innovation meets 🧠 Intuition
At a time when a company's digital presence determines its success, the challenge is how to make this presence authentic, individual and far-reaching. Xpert.Digital offers an innovative solution that positions itself as an intersection between an industry hub, a blog and a brand ambassador. It combines the advantages of communication and sales channels in a single platform and enables publication in 18 different languages. The cooperation with partner portals and the possibility of publishing articles on Google News and a press distribution list with around 8,000 journalists and readers maximize the reach and visibility of the content. This represents an essential factor in external sales & marketing (SMarketing).
More about it here:
Xpert partner in warehouse planning and construction
📊🚀 The importance of bottleneck identification
🌟 Bottlenecks can slow down the entire logistics process, leading to increased costs, delays and unhappy customers. In intralogistics, i.e. internal logistics, such bottlenecks can be particularly serious as they affect the entire value chain. It is therefore essential to identify and correct these vulnerabilities at an early stage.
🔍 How does the Bottleneck Walk work?
1. Preparation
Before the Bottleneck Walk begins, clear goals should be defined and relevant data collected. This can include analyzing lead times, inventory levels and production schedules.
2. Carrying out the tour
Experts from different departments go through the processes together. They observe the processes, talk to employees on site and note any conspicuous points.
3. Identification of bottlenecks
During the tour, areas are identified where processes are backing up or resources are not being used optimally.
4. Analysis and evaluation
The information collected is evaluated to understand the causes of the bottlenecks.
5. Development of solutions
Based on the analysis, measures are developed to eliminate the identified bottlenecks.
6. Implementation and follow-up
The measures are implemented and it is checked whether they bring the desired improvements.
📦⏳ Frequent bottlenecks in intralogistics and logistics
- Inadequate storage space organization: Inefficient storage can lead to delays in picking and delivery.
- Outdated technology: Using outdated systems can slow down processes and increase errors.
- Lack of communication: Lack of or inadequate communication between departments can lead to misunderstandings and process disruptions.
- Overworked employees: A lack of staff or uneven distribution of work can affect productivity.
🌟✨The benefits of eliminating bottlenecks
- Increased efficiency: Through optimized processes, resources can be used better and throughput times can be shortened.
- Cost savings: More efficient operations reduce operating costs and increase profitability.
- Improved customer satisfaction: Faster and more reliable deliveries strengthen customer loyalty.
- Competitive advantage: Companies that continually improve their processes can assert themselves better in the market.
🚗📈 Case study: Successful bottleneck walk in practice
A medium-sized company in the automotive supply industry discovered that delivery delays led to customer complaints. Through a bottleneck walk, they identified that part picking was the bottleneck. The warehouse shelves were arranged inefficiently and employees had to walk long distances. After restructuring the warehouse and introducing a digital warehouse management system, throughput times were reduced by 30%.
👥💬 Tips for a successful bottleneck walk
- Interdisciplinary team: Involve employees from different areas to get different perspectives.
- Open communication: Encourage open dialogue with on-site employees as they often have valuable insights.
- Use data: Supplement observations with quantitative data to get a complete picture.
- Continuous Improvement: Don't see the Bottleneck Walk as a one-time activity, but rather as part of a continuous improvement process.
🔎📉 Observing and analyzing the processes
The Bottleneck Walk is an effective tool for identifying and eliminating bottlenecks in intralogistics and logistics. By directly observing and analyzing on-site processes, companies can uncover hidden inefficiencies and take targeted measures. At a time when speed and efficiency are critical, the Bottleneck Walk offers a clear path to streamlining operations and increasing competitiveness.
🛠️🚀 Your next step
Think about when you last took a close look at your internal processes. Maybe now is the right time for a bottleneck walk in your company. By acting proactively, you can not only solve current problems, but also prepare yourself for future challenges.
📣 Similar topics
- 🔍 Eliminating bottlenecks in logistics: A guide
- 🚶♂️ Bottleneck Walk: Improve efficiency through walking tours
- 🏗️ Optimize intralogistics: Key to competitiveness
- 📊 Data-driven improvement: Identify bottlenecks
- 🤝 Teamwork as a success factor: Interdisciplinary approaches in the Bottleneck Walk
- ⏱️ Saving time through bottleneck identification: Here's how it works
- 🏆 Increase competitiveness through process optimization
- 📉 Cost reduction through targeted measures in logistics
- 😊 Strengthen customer loyalty through faster deliveries
- 📈 Continuous improvement process: The key to success
#️⃣ Hashtags: #Logistics #ProcessOptimization #EfficiencyIncrease #BottleneckManagement #BottleneckWalk
Xpert.Plus warehouse optimization - high-bay warehouses such as pallet warehouses consulting and planning
We are there for you - advice - planning - implementation - project management
☑️ SME support in strategy, consulting, planning and implementation
☑️ Creation or realignment of the digital strategy and digitalization
☑️ Expansion and optimization of international sales processes
☑️ Global & Digital B2B trading platforms
☑️ Pioneer Business Development
I would be happy to serve as your personal advisor.
You can contact me by filling out the contact form below or simply call me on +49 89 89 674 804 (Munich) .
I'm looking forward to our joint project.
Xpert.Digital - Konrad Wolfenstein
Xpert.Digital is a hub for industry with a focus on digitalization, mechanical engineering, logistics/intralogistics and photovoltaics.
With our 360° business development solution, we support well-known companies from new business to after sales.
Market intelligence, smarketing, marketing automation, content development, PR, mail campaigns, personalized social media and lead nurturing are part of our digital tools.
You can find out more at: www.xpert.digital - www.xpert.solar - www.xpert.plus