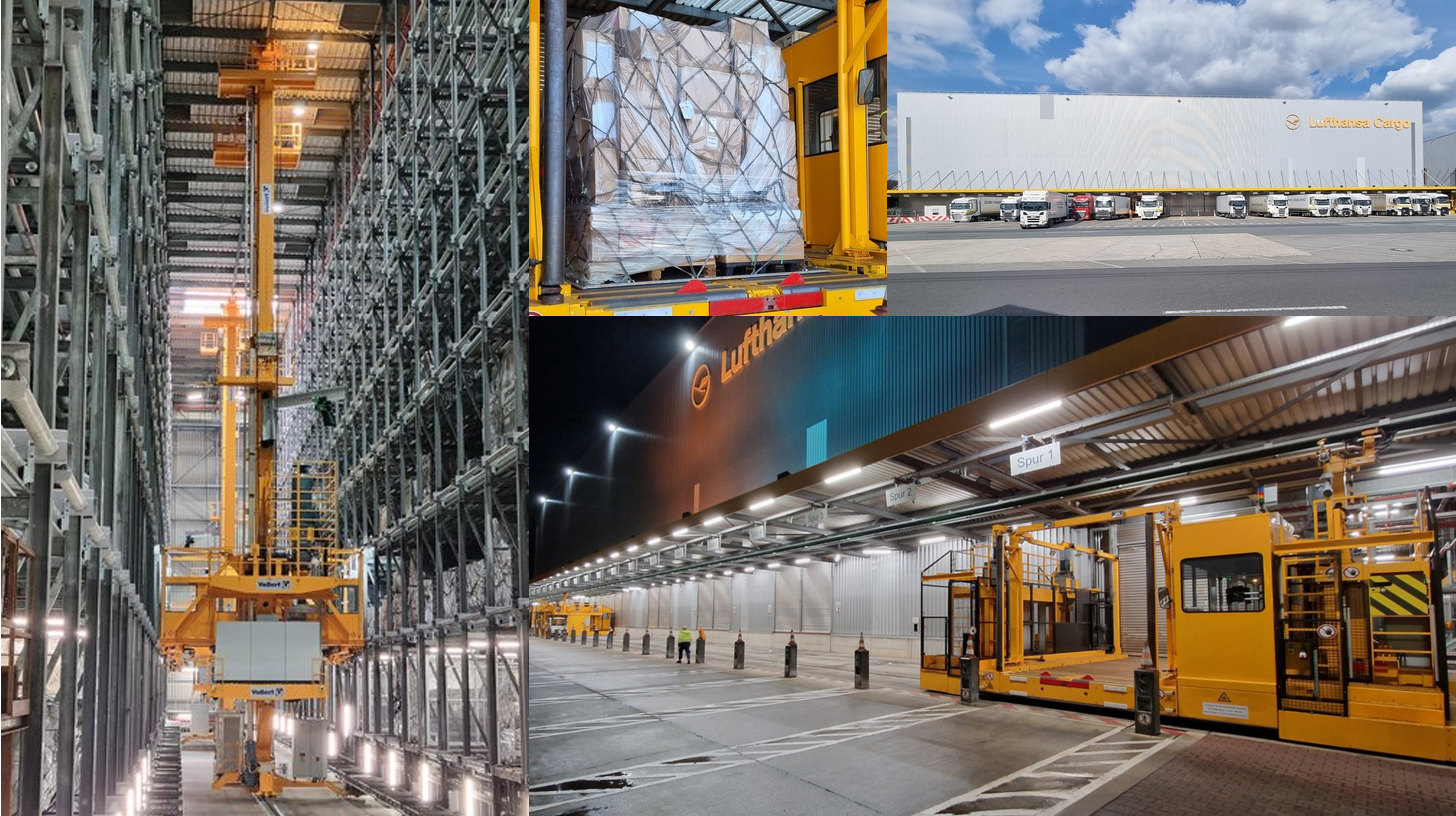
Vollert Container Logistics Solution: Schwerlast-Intralogistik mit mehrstöckigem Hochregallager und Regalbediengeräten – Bilder: Vollert Anlagenbau GmbH
Vollert Anlagenbau GmbH - Schwerlast-Intralogistik und mehrstöckige Hochregallager für Container
Schwerlast-Intralogistik im Wandel – das Vollert Container Logistics Solution Konzept als Schlüssel für die automatisierte, platzsparende Containerlogistik der Zukunft
Die internationaleistikbranche erlebt aktuell einen grundlegenden Paradigmenwechsel. Digitale Vernetzung, steigende Umschlagvolumina, der Ruf nach nachhaltigen Lösungen sowie der Druck, innerbetriebliche Lieferketten resilienter zu gestalten, machen traditionelle Containerhöfe und Freilagerflächen zusehends zum Engpass. Wurden See-, Binnen- und Industriehäfen Jahrzehnte lang von Reach-Stackern, Portal- oder Brückenkranen dominiert, rücken heute automatisierte Hochregallager für Standardcontainer in den Fokus. Einer der Pioniere dieser Entwicklung ist die im schwäbischen Weinsberg beheimatete Vollert Anlagenbau GmbH. Mit dem Vollert Container Logistics Solution Konzept überträgt das Unternehmen seine jahrzehntelange Schwerlast- und Intralogistik-Erfahrung aus Stahlwerken, Betonfertigungsanlagen und der Automobilindustrie auf den Containerumschlag – und stellt damit ein modulares Baukastensystem für hochverdichtete, mehrstöckige Containerlager vor, das gleichzeitig Effizienz, Flexibilität und Umweltverträglichkeit verbindet.
Passend dazu:
- Die Top Ten der Container-Hochregallager-Hersteller und Leitfaden: Technologie, Hersteller und Zukunft der Hafenlogistik
Vom Freilager zum mehrstöckigen Hochregallager – warum der Paradigmenwechsel notwendig ist
Weltweit werden jährlich mehrere hundert Millionen TEU umgeschlagen. Bislang beruhten logistische Drehkreuze auf horizontaler Ausdehnung: Fuhren die Volumina hoch, vergrößerte man den Umschlagplatz oder vermietete zusätzliche Freiflächen. Doch Boden ist vielerorts knapp und teuer; außerdem steigen die Energie- und Personalkosten. Parallel sorgen strengere Emissionsvorgaben, Lärmschutzauflagen und zunehmende Unwetterereignisse dafür, dass klassische Freiflächen‐Containerhöfe an wirtschaftliche und ökologische Grenzen stoßen. All diese Faktoren begünstigen vertikale Lagerlösungen, bei denen Container in Regalgassen übereinander gestapelt werden, ohne dass hierfür Stapler, Straddle-Carrier oder Reach-Stacker permanent umschichten müssen. Genau hier setzt das Vollert-Konzept an.
Wesentliche Bausteine der Vollert Container Logistics Solution
1. Vollautomatisches, mehrstöckiges Hochregallager (High-Bay Store, HBS)
Das Herzstück bildet ein Regalgerüst aus hochfestem Stahl, das – je nach Kundenanforderung – bis zu acht oder mehr Ebenen umfasst. ISO-Container mit bis zu 40 t Gesamtgewicht werden in individuell adressierbaren Lagerfächern abgelegt. Anders als bei herkömmlichem Block-Stacking ist dabei jeder Container ohne Umstapelprozesse direkt erreichbar. Das spart Zeit, Energie und Verschleiß.
2. Kompakte Schwerlast-Regalbediengeräte (RBG)
Für den schnellen Transport zwischen den Regalgassen dienen eigens entwickelte Regalbediengeräte. Sie navigieren auf Schienen und heben beziehungsweise verfahren die Container mittels teleskopierbarer Greifer. Dank frequenzgeregelter Antriebe, Energierückspeisung und hochauflösender Wegmesssysteme erreichen die RBGs Geschwindigkeiten, die bislang nur aus leichten Palettenlagern bekannt waren – nun aber für 20- und 40-Fuß-Behälter möglich sind.
3. Modularität von Anfang an
Sowohl das Stahlbau-Raster als auch die RBG-Einheiten und Fördertechniken sind konsequent modular konzipiert. Betreiber können also zunächst ein Kernsystem installieren und bei steigenden Umschlagsmengen sukzessive zusätzliche Gassen, Ebenen oder Geräte integrieren, ohne den laufenden Betrieb zu stoppen. Das verringert Investitionsrisiken und erlaubt eine schrittweise Skalierung.
4. Durchgängige Software-Architektur
Hinter dem sichtbaren Stahlkoloss steckt eine intelligente Steuerungs- und Leitebene. Vollerts eigens entwickelte Warehouse-Control-Software verbindet sensorische Echtzeitdaten mit Algorithmen für Leerlaufoptimierung, Priorisierung und Kollisionsvermeidung. Über standardisierte Schnittstellen – etwa OPC UA oder REST – lässt sich das HBS nahtlos an übergeordnete Terminal-Operating-Systeme oder ERP-Plattformen ankoppeln. Digitale Zwillinge ermöglichen Simulationen, während Condition-Monitoring-Module Wartungsbedarfe vorausschauend melden.
5. Schnittstellen zur Außenwelt
Ob Bahn-, Binnenschiff- oder Straßenzufahrt: Die Lösung kann auf verschiedenen Ebenen mit Portal- oder Brückenkranen, automatisierten Guided Vehicles (AGV) oder Straßen-Lkw andocken. Dabei sorgen Übergabestationen – wie Shuttle-Bahnen oder sogenannte Moving Truck Docks – für einen durchgängigen Materialfluss vom Anliefer- bis zum Versandtor.
Nutzenpotenziale im Detail
Flächeneinsparung
Durch die vertikale Stapelung reduziert sich der Grundflächenbedarf laut Vollert um bis zu 70 Prozent gegenüber konventionellen Containerplätzen gleicher Kapazität. Freiwerdende Areale können für wertschöpfendere Prozesse genutzt oder in Grünflächen umgewandelt werden.
Verkürzte Durchlaufzeiten
Weil jeder Container gezielt angesteuert wird, entfallen zeitintensive Umstapelvorgänge. In Spitzenzeiten lassen sich Ein- und Auslagersequenzen parallelisieren, wenn mehrere RBGs simultan arbeiten.
Wetter- und Emissionsschutz
Das Regalgebäude schützt die Ware vor Niederschlag, UV-Strahlung und Sturm. Gleichzeitig läuft der komplette Bewegungszyklus vollelektrisch. Dies spart Diesel, senkt CO₂-Emissionen und minimiert Lärmbelastung für Beschäftigte und Anwohner.
Arbeitssicherheit und Ergonomie
Fahrerlose Systeme reduzieren das Risiko von Kollisionen, Abstürzen oder Quetschungen. Bedienpersonal wechselt von körperlich belastenden Outdoor-Tätigkeiten zu überwachenden Aufgaben in klimatisierten Leitwarten, was die Attraktivität des Arbeitsplatzes steigert.
Flexibilität im Branchenmix
Vom Seehafen über Rail-Terminals bis zur dezentralen Container-Distribution für Bau-, Chemie- oder Automotive-Industrie – überall dort, wo Schwerlast-Behälter schnell, sicher und werterhaltend bewegt werden müssen, lassen sich Vollerts Modulbaukästen anpassen. Selbst temperaturempfindliche Güter sind denkbar, wenn die Regalgassen beispielsweise als Thermokammer ausgerüstet werden.
Ein Blick hinter die Kulissen – so funktioniert ein Vollert-HBS Zyklus
1. Ankunft und Identifikation
Ein Lkw oder ein Schienenwagon erreicht die Übergabezone. Kamerasysteme erfassen die Containernummer, während RFID-Tags die Verbindung zum Auftrag herstellen. Das Leitsystem ordnet dem Gebinde augenblicklich einen Lagerplatz zu.
2. Horizontaler Transfer
Ein Shuttle-System oder ein Kettenförderer übernimmt den Container und übergibt ihn an das zuständige Regalbediengerät. Diese Quertransporte sind exakt getaktet, sodass Wartezeiten entfallen.
3. Vertikale Positionierung und Einlagerung
Das RBG hebt den Container auf die Zielhöhe, verfährt zur eingeteilten Fachadresse und setzt ihn auf lastabtragende Stahlauflager. Durch integrierte Gewichtssensoren wird die zulässige Fachbelastung überwacht; Überlastungen werden automatisch geblockt.
4. Überwachung und Bestandsverwaltung
Parallel aktualisiert das WMS die Lagerbestände in Echtzeit. Unstimmigkeiten lassen sich über Bilderkennung klären: Jedes Fach verfügt optional über Kameras, die bei Abweichungen einen Snapshot senden.
5. Auslagerung & Versand
Für Abrufe erfolgt der Vorgang spiegelbildlich. Sequenzoptimierte Algorithmen bündeln Aufträge nach Zielrelation, sodass Touren oder Schiffsabfahrten ohne Verzögerung starten können.
Vom Hafen zur High-Tech-Fabrik-Lösung: Intelligente Containerlogistik
Digitalisierung und Industrie 4.0 – mehr als nur Schlagworte
Vollert kombiniert robuste Mechanik mit modernen IT-Konzepte:
- Digitale Zwillinge simulieren Lastkollektive, Fahrwege und Energieströme, um bereits in der Projektierungsphase optimale Layouts zu finden.
- Predictive Maintenance erkennt anhand von Schwingungs- oder Temperaturdaten, wann Antriebe oder Rollen getauscht werden müssen, bevor Ausfälle auftreten.
- Künstliche Intelligenz optimiert Einlagerstrategien, indem sie historische Abrufmuster analysiert und oft benötigte Container in Zugriffs-Hotspots positioniert.
- Sicherheits-Layer schützen vor unautorisierten Zugriffen und gewährleisten, dass Not-Stop-Signale sämtliche Bewegungen innerhalb von Millisekunden stillsetzen.
Nachhaltigkeit als Leitgedanke
Ein Container-HBS spart nicht nur Diesel-Verbräuche traditioneller Yard-Ausrüstung. Zusätzliche Maßnahmen steigern die Ökobilanz:
- Regenerative Energierückspeisung: Beim Abbremsen speist der Frequenzumrichter der RBGs Strom ins Netz zurück.
- Photovoltaik auf Dachflächen: Die riesigen Dächer sind prädestiniert für Solarpaneele, die einen Teil des Eigenverbrauchs decken.
- LED-Beleuchtung mit Präsenzsteuerung reduziert Stromaufnahme um bis zu 70 Prozent gegenüber herkömmlichen Leuchten.
- Stahlbau-Recycling: Vollert setzt auf sortenreinen Stahl, der bei Anlagenumbauten nahezu vollständig recycelt werden kann.
Case Study – Lufthansa Cargo Hub Frankfurt
Wie sich die Technologie in der Praxis bewährt, zeigt die umfassende Hub-Modernisierung am Frankfurter Flughafen. Lufthansa Cargo musste ihren Road-Feeder-Service (RFS) beschleunigen, um die Durchlaufzeit zwischen Frachtflugzeug und Lkw weiter zu verringern. Zwar handelt es sich hierbei um Unit Load Devices (ULDs) und nicht um ISO-Seefrachtcontainer, doch die Prinzipien sind identisch.
Das Herzstück des Vorhabens: zwei 28 m hohe Vollert-Regalbediengeräte, die das vorhandene Hochregallager revitalisierten. Ergänzt wurden sie durch innovative Moving Truck Docks – verfahrbare Docking-Stationen, die ganze Lkw-Auflieger innerhalb weniger Minuten be- und entladen. Das Ergebnis waren signifikant erhöhte Umschlagkapazitäten, niedrigere Personalkosten und ein reibungsloser 24/7-Betrieb selbst bei Spitzenaufkommen während Nachtflug-Wellen.
Der besondere Clou: Sämtliche Maßnahmen fanden im „Brownfield-Modus“ statt. Anstatt den Frachtbetrieb zu unterbrechen, installierte Vollert Module für Modul in nächtlichen Wartungsfenstern. Die modulare Systemarchitektur zahlte sich somit doppelt aus – bei der Erstinstallation und bei zukünftigen Erweiterungen.
Wirtschaftlichkeit und Return on Investment
Automatisierung kostet Geld, doch sie rechnet sich meist rasch:
- Personaleinsparungen entstehen, weil RBGs rund um die Uhr ohne Schichtwechsel laufen.
- Höhere Flächenrentabilität senkt Pacht- oder Investitionskosten für Grundstücke.
- Geradlinige Prozesszeiten verringern Pönalen durch Verzögerungen und verbessern die Liefertreue.
- Energie-Effizienz zahlt sich in reduzierten Betriebskosten aus.
- Restwert des Stahlbaus bietet Planbarkeit: Das Regalgerüst kann bei Bedarf versetzt oder verkauft werden.
Kunden berichten, dass sich das System in vier bis sechs Jahren amortisiere – ein Zeitraum, der angesichts von Förderprogrammen für klimaneutrale Logistik weiter sinken kann.
Skalierbare Anwendungsfelder über die klassische Hafenlogistik hinaus
1. Industrie-Inbound
Automobile OEMs erhalten vormontierte Komponenten in Hoch-See-Containern. Ein innerbetriebliches HBS erlaubt es, Material abrufbereit direkt am Montageband bereitzustellen, ohne dass Container langwierig ausgepackt werden müssen.
2. Chemische Industrie
Containerisierte Chemikalien können in isolierten Gassen gelagert werden, während Sensorik Temperatur oder Füllstände überwacht. Gefahrstoffe bleiben so jederzeit rückverfolgbar.
3. Off-Site-Construction
Fertighaus- bzw. Modulbauhersteller versenden komplette Raummodule in Spezialcontainern. Ein automatisches HBS beschleunigt die Baustellen-Belieferung und schützt empfindliche Oberflächen.
4. Katastrophenschutz-Depots
Staatliche Organisationen lagern Hilfsgüter in Containern, die bei Krisenfall binnen Stunden verladen werden müssen. Ein Container-HBS stellt sicher, dass medizinische Ausrüstung, Zelte und Wasseraufbereitungsanlagen in der richtigen Reihenfolge verfügbar sind.
Pflege, Wartung und Lebenszyklus-Management
Vollert liefert nicht nur die Hardware, sondern ein ganzheitliches Life-Cycle-Support-Paket. Regelmäßige Remote-Health-Checks, Ersatzteil-Pooling und Instandhaltungsverträge verlagern Verantwortung von der Betreiber- zur Lieferantenseite. Dadurch wird die Gesamtanlageneffektivität (OEE) transparent und planbar; Stillstände lassen sich auf ein Minimum reduzieren.
Update vom 23. Juli 2025:
- Insolvenz: Die Vollert Anlagenbau GmbH, Anbieter von Intralogistik-, Betonfertigteil- und Rangiersystemen, ist pleite
Blick in die Zukunft – wohin geht die Reise?
- 5G-Campus-Netze werden Latenzzeiten weiter minimieren und ermöglichen, dass autonome Fahrzeuge nahtlos mit Regalbediengeräten kooperieren.
- Edge-Computing bringt Rechenleistung dorthin, wo Daten anfallen. Statt zentraler Server verarbeitet jeder RBG Entscheidungen lokal und nur hochaggregierte Informationen wandern in die Cloud.
- Grüne Stähle sowie alternative Konstruktionswerkstoffe wie Carbonbeton verringern künftig den CO₂-Fußabdruck des Anlagenbaus.
- Mikro-Grids koppeln PV-Anlagen, Batteriespeicher und Verbraucher zum energieautarken Terminal.
Vollert positioniert sich hier als Enabler, indem das bestehende Baukastensystem offen für Upgrades bleibt. Wer also ein HBS heute errichtet, kann morgen mit wenig Aufwand neue Features nachrüsten.
In einer Zeit, in der Flächen knapp, Lieferketten verwundbar und Nachhaltigkeitsziele ambitioniert sind, liefert das Vollert Container Logistics Solution Konzept eine ebenso pragmatische wie zukunftsweisende Antwort. Durch die Verbindung von bewährter Schwerlast-DNA, modularer Mechanik und modernster Software entsteht ein System, das gleich mehrere Stellschrauben gleichzeitig bedient: höhere Umschlagleistung, geringere Betriebskosten, bessere Umweltbilanz und gesteigerte Arbeitssicherheit. Die erfolgreiche Umsetzung am Lufthansa-Cargo-Hub unterstreicht die Praxisreife ebenso wie das Potenzial für diverse Branchen. Unternehmen, die heute in automatisierte Hochregallager für Container investieren, schaffen damit die Grundlage für eine wettbewerbsfähige, flexible und klimafreundliche Logistik von morgen.
Wir sind für Sie da - Beratung - Planung - Umsetzung - Projektmanagement
☑️ Unsere Geschäftssprache ist Englisch oder Deutsch
☑️ NEU: Schriftverkehr in Ihrer Landessprache!
Gerne stehe ich Ihnen und mein Team als persönlicher Berater zur Verfügung.
Sie können mit mir Kontakt aufnehmen, indem Sie hier das Kontaktformular ausfüllen oder rufen Sie mich einfach unter +49 89 89 674 804 (München) an. Meine E-Mail Adresse lautet: wolfenstein∂xpert.digital
Ich freue mich auf unser gemeinsames Projekt.