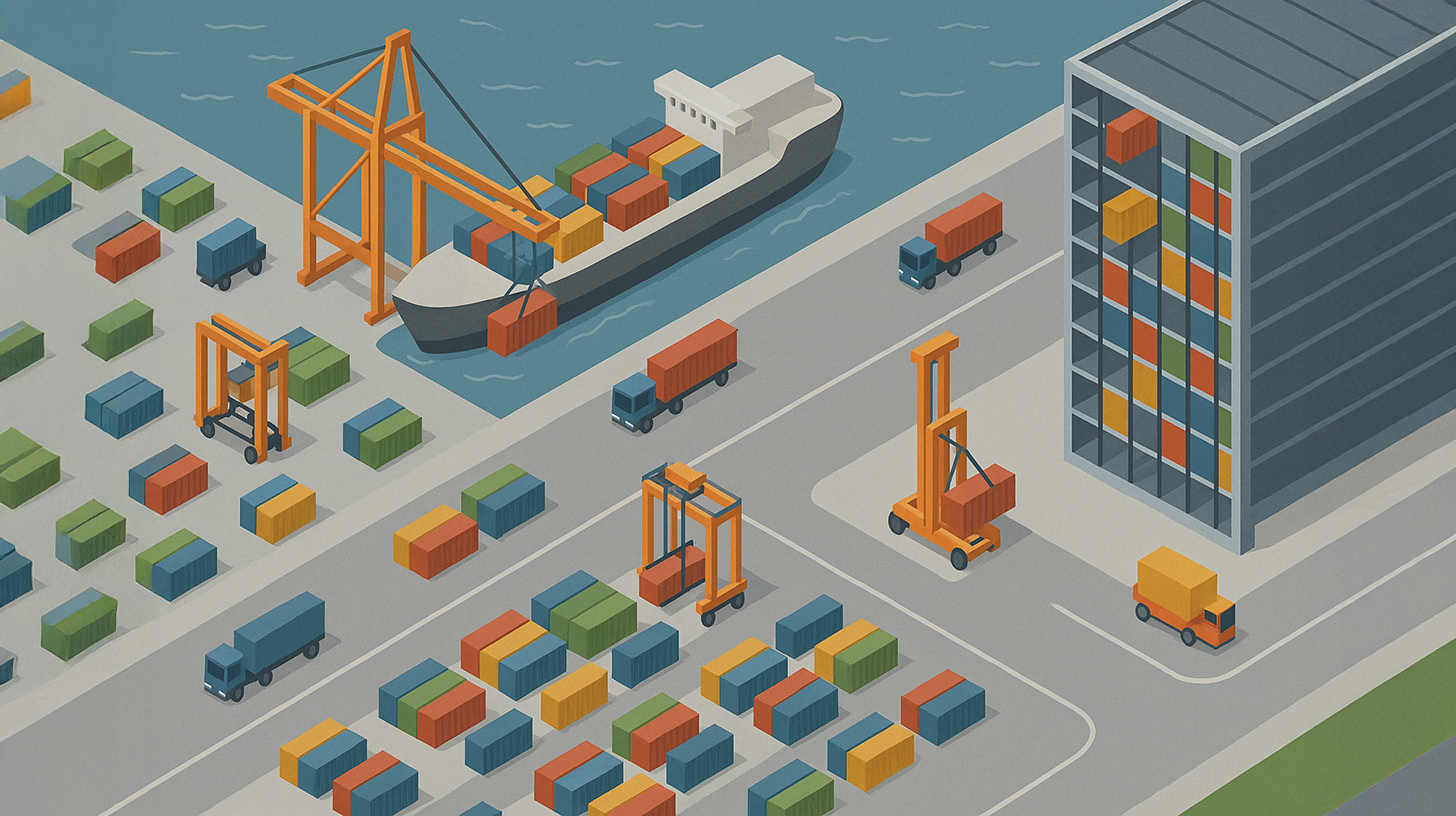
Sviluppo dei terminali del contenitore: dai cantieri del contenitore a cuscinetti a raggio alto contenitore verticale completamente automatizzato – Immagine: Xpert.Digital
Spazio come strategia: la reinvenzione della logistica del contenitore globale
Miracolo in pizzo della logistica: sistemi di archiviazione intelligenti cambiano il commercio mondiale
Ulteriore sviluppo dei terminali di container dai cantieri dei container (parcheggio dei container), a cuscinetti a travi verticali verticali di container ottici di Space (traffico combinato da strada, ferrovia e mare) del trasporto merci globale.
Il punto di svolta della logistica globale – Quando la stanza diventa una risorsa strategica
La rete logistica globale, la spina dorsale del moderno commercio mondiale, geme sotto il peso del suo stesso successo. Una crescita inarrestabile del volume commerciale, abbinata a un drammatico aumento delle dimensioni delle navi – particolare le navi da container ultra grandi (ULC), che possono trasportare fino a 24.000 TEU (unità equivalente di venti piedi): – portato il modello tradizionale del terminale del contenitore ai suoi limiti fisici e operativi assoluti. Alle interfacce dei flussi globali di merci, nei porti, una crisi si manifesta che minaccia di paralizzare l'intera catena di approvvigionamento.
Questo sviluppo ha rivelato un conflitto centrale di obiettivi della moderna logistica del porto: il paradosso insolubile tra la necessità di una densità di conservazione sempre più elevata su aree strette e costose e la conseguente perdita catastrofica dell'efficienza operativa nei sistemi convenzionali. Il terminale del contenitore, un tempo punto di transito puro, è diventato un collo di bottiglia critico, che determina il ritmo dell'intera catena di approvvigionamento globale. L'ulteriore sviluppo di ampie aree di parcheggio dei container, i cosiddetti cantieri di container, verso cuscinetti a raggio verticale ottimizzati, completamente automatizzati e supportati dall'intelligenza artificiale non è quindi un semplice aggiornamento tecnologico. Piuttosto, è una risposta necessaria, che cambia paradigma a una crisi sistemica che costringe una ridefinizione fondamentale del funzionamento dei terminali di trasbordo nel traffico combinato (KV) da strada, ferrovia e marina.
Adatto a:
- I primi dieci dei produttori e linee guida per cuscinetti di alta classe container: tecnologia, produttore e futuro della logistica delle porte
The Age of Borders – Terminali di container tradizionali sul fodero
Anatomia di un terminale di contenitore convenzionale: un ecosistema sotto pressione
Per comprendere l'ambito della prossima rivoluzione, è essenziale uno sguardo all'anatomia e il funzionamento di un terminale tradizionale contenitore. Tale terminale è un ecosistema complesso che consiste in diversi componenti fisici chiaramente definiti e zone operative. In prima linea c'è il Kaianlage con gli ormeggi (ormeggi), su cui catturano le enormi navi contenitori. Qui le potenti gru da nave a terra (STS), le cui interpreti si estendono su tutta la larghezza delle navi per caricare ed estinguere i contenitori. Tuttavia, il cuore del terminal è l'ampio cortile dei contenitori (CY), un'area enorme e fortificata che funge da campo di buffer temporaneo per migliaia di contenitori pieni e vuoti. Una flotta di attrezzature specializzate di movimentazione e trasporto opera all'interno di questo cortile. Questi includono gru portali in gomma (gru a cavalletto in gomma, RTG), gru portali legate a binario (gru a cavalletto montate su rotaia, RMG), alette portali (portante a strati) e stacker di portate (raggiungi gli stacker), che sono responsabili per lo stacking e il trasporto dei contenitori all'interno dei cortili. Il terzo elemento essenziale è il complesso di gate, il tubo dell'ago per il traffico del paese, su cui vengono gestiti i camion, il contenitore viene registrato e vengono eseguiti controlli di sicurezza. Ciò è spesso integrato da un sistema ferroviario per ulteriori trasporti nell'entroterra. Le operazioni del cantiere includono l'archiviazione, l'organizzazione e la fornitura dei contenitori. Le operazioni del cancello e ferroviario garantiscono il collegamento senza soluzione di continuità alle modalità di atterraggio. In teoria, questo è un processo di flusso. In pratica, tuttavia, la massa pura di contenitori, che viene eliminata da un'unica ulcera, ha portato questo sistema al limite del crollo.
Il circolo vizioso dell'inefficienza: il paradigma del blocco impilamento
Il tallone di Achille di ciascun terminale di container convenzionale risiede nella sua filosofia di progettazione fondamentale: impilamento di blocchi. Indipendentemente dal fatto che un terminale utilizzi un layout lineare o un blocco, il principio si basa su contenitori di impilamento direttamente l'uno sull'altro per sfruttare l'area limitata. Ciò che sembra logico a prima vista è in verità la fonte dell'inefficienza profonda e sistemica. Il problema principale è il cosiddetto "processi circostanti improduttivi", noto anche come "rimodellamento" o "mosse shuffle". Per accedere a un contenitore che si trova nella parte inferiore di uno stack, tutti i contenitori sopra devono prima essere sollevati e conservati altrove. Solo allora si può rimuovere il contenitore target, dopodiché i contenitori intermedi devono spesso essere spostati di nuovo. Le analisi mostrano che questi movimenti improduttivi che non creano tempo o valore rappresentano tra il 30 % e il 60 % di tutti i movimenti della gru in un cortile convenzionale. Nel peggiore dei casi, ciò significa che oltre la metà dell'intera attività della gru dei rifiuti puri. Questo fatto crea un circolo vizioso: per aumentare la capacità in uno spazio limitato, gli operatori del terminale sono costretti a impilare i contenitori più in alto. Ma con ogni livello aggiuntivo, la probabilità e la complessità dei processi circostanti aumentano in modo esponenziale. Da un tasso di riempimento del 70-80 %, le prestazioni di un blocco di guardia si rompono drasticamente. Il risultato sono tempi di risoluzione imprevedibili, ingorghi di traffico enormi all'interno del terminale e una performance operativa che non può più essere pianificata. Le dimensioni dei vantaggi dei megail in mare vengono distrutti da enormi inefficienze sulla terra.
L'imperativo del traffico combinato (KV): quando il collo della bottiglia paralizza la catena
Queste inefficienze sono fatali per i terminali del traffico combinato (KV), che fungono da interfaccia critica tra la nave, la ferrovia e il camion. Le prestazioni dell'intera rete intermodale dipendono dall'efficienza e dall'affidabilità di questi punti di copertura. Un terminal convenzionale, afflitto da processi circostanti non pianificabili e ingorghi interni, agisce come un freno per l'intera catena logistica. I tempi di attesa lunghi e imprevedibili per i camion alle porte e per i treni merci sui terminali ferroviari sono l'episodio diretto. Un contenitore tardivo può ritardare la partenza di un intero treno merci, che a sua volta confonde gli orari in tutta la rete ferroviaria e le connessioni di connessione mettono in pericolo. I vantaggi economici ed ecologici del traffico combinato – il raggruppamento dei trasporti e il trasferimento dalla strada alla ferrovia – sono minati dal collo del bottiglia nel porto. L'imprevedibilità degli impianti terminali attraverso l'intera catena di approvvigionamento e rende quasi impossibile la logistica just-in-time affidabile. Diventa chiaro che l'inefficienza dei terminali tradizionali non è un problema di gestione, ma un errore sistemico che radica nella sua architettura fisica. Questo modello un tempo adeguato è diventato obsoleto a causa del ridimensionamento e della velocità del moderno commercio globale e ha reso i terminali la principale fonte di attrito e imprevedibilità nelle catene di approvvigionamento.
The Vertical Revolution – The High -Bay Warehouse come nuovo paradigma
Dall'espansione orizzontale alla densità verticale: il concetto di HRL
In risposta alla crisi sistemica dei terminali convenzionali, viene creato un nuovo approccio radicale: il magazzino ad alta base (HRL) completamente automatizzato (HRL), noto a livello internazionale come archiviazione ad alto livello (HBS). Invece di espandersi ulteriormente in orizzontale, che è geograficamente impossibile ed ecologicamente discutibile nella maggior parte delle città portuali, il concetto di HRL sposta lo stoccaggio nel verticale. È una strategia che cambia fondamentalmente l'equazione dell'uso della terra. Questo concetto non è una pura finzione, ma si basa su una tecnologia comprovata e solida che proviene da un settore inaspettato: l'industria pesante. I principali fornitori come il gruppo Deutsche SMS hanno decenni di esperienza con cuscinetti ad alto livello completamente automatizzati per carichi estremamente pesanti, come 50 tonnellate di bobine in acciaio, che sono gestite in modo affidabile in condizioni industriali approssimative in attività 24/7. L'adattamento di questa tecnologia provata e testata per la logistica dei container riduce in modo significativo il rischio percepito per gli operatori portuali e dà il salto nell'innovazione una solida base industriale.
Adatto a:
Decostruzione della tecnologia: il principio di accesso individuale diretto
Un HRL è molto più di un semplice scaffale. È un sistema altamente complesso e completamente automatizzato, il cui genio è su un singolo principio: l'accesso individuale diretto a ciascun singolo contenitore. Questo principio è reso possibile da due componenti principali. Al massimo, la struttura della rastrelliere in acciaio: un'enorme struttura in acciaio che può essere fino a undici contenitori alti forma lo scheletro del magazzino. Ogni contenitore è posto nel suo ripiano indirizzabile individualmente. Un dettaglio cruciale è che questi ripiani non hanno bisogno di pavimenti continui. I contenitori ISO standardizzati sono autosufficiente e sono tenuti solo nei loro raccordi per angolo (Twistlocks). Ciò riduce significativamente l'uso di materiali, il peso totale e i costi di costruzione senza influire sulla statica. In secondo luogo, i dispositivi di controllo degli scaffali automatizzati (RBG), chiamati anche gru a stacker: queste gru a livello ferroviario e ad alta velocità si muovono autonomamente attraverso i corridoi tra le file di scaffale. Sono dotati di bracci di presa regolabili (spargitore), che sono bloccati con precisione sui contenitori. Eliminato da un sistema di controllo centrale, un RBG può controllare direttamente e rimuovere qualsiasi contenitore nel magazzino – senza dover spostare un singolo altro contenitore. Ecco il nucleo rivoluzionario della tecnologia. L'accesso individuale diretto elimina i processi circostanti improduttivi. Ogni movimento di una gru è un movimento produttivo. Il conflitto target fondamentale tra densità di stoccaggio e efficienza di accesso, che paralizza terminali tradizionali, viene sciolto. La vera rivoluzione dell'HRL non è quindi la verticalità stessa, ma il cambiamento da un magazzino secento (impilato) per accedere alla filosofia centrale (scaffale). Il magazzino si trasforma da un grande magazzino in un nodo di smistamento e buffer altamente dinamico.
Caso di studio: il sistema Boxbay come "prova della fattibilità"
La fattibilità tecnologica e le prestazioni di questo concetto non sono più una teoria. La joint venture Boxbay, una cooperazione tra il Global Terminal Operator DP World e il Gruppo SMS del produttore dell'impianto tedesco, ha fornito l'impressionante "rilevamento di fattibilità" con il suo progetto pilota nel porto di Jebel Ali a Dubai. Entro la fine del 2024, sono stati eseguiti con successo oltre 330.000 movimenti di container. I risultati hanno superato le aspettative: la performance della copertura ha raggiunto 19,3 movimenti all'ora all'interfaccia per la banchina e impressionanti 31,8 movimenti all'ora sulle gru di camion lato terra. Queste cifre mostrano che il sistema non funziona solo, ma consente anche prestazioni e prevedibilità senza pari. È già stato fatto il prossimo passo cruciale: nel marzo 2023 fu firmato il primo ordine commerciale per l'attuazione di "retrofitting" nel porto di Pusan, in Corea del Sud. Lì il sistema Boxbay viene adattato in un terminale esistente e all'avanguardia. L'obiettivo: l'eliminazione di 350.000 processi circostanti improduttivi all'anno e una riduzione dei tempi di gestione dei camion del 20 %. Il successo di questo progetto sarà una cartina di tornasole per la capacità della tecnologia di modernizzare l'infrastruttura esistente dei porti del mondo ed è seguito da tutto il settore con la massima attenzione.
Sistemi nervosi digitali: il terminale container del futuro tra alta tecnologia ed efficienza
I motori del cambiamento – automazione, robotica e digitalizzazione
Il terminale automatizzato: da parziale all'automazione completamente
L'automazione nei terminali contenitori non è una condizione binaria, ma uno spettro con diversi gradi di maturità. La maggior parte dei terminali noti come "automatizzato" oggi rientra nella categoria dell'automazione parziale. Qui, il processo di stoccaggio nel cantiere è in genere automatizzato utilizzando gru a impilamento automatizzato (gru a impilamento automatizzato, ASC), mentre il trasporto orizzontale tra Kai e Warehouse Block continua a svolgersi con servito manualmente. Invece di camionisti, i sistemi di trasporto senza conducente (veicoli guidati automatizzati, AGV) o veicoli di sollevamento automatizzati (veicoli di sollevamento automatizzati, ALV) assumono il trasferimento dei container. Nonostante l'enorme interesse per queste tecnologie, solo circa il 3-4 % di tutti i terminali di container in tutto il mondo è parzialmente o completamente automatizzato. Ciò chiarisce che gli ostacoli per l'introduzione sono alti. Il concetto di cuscinetto ad alto livello rappresenta il livello di automazione integrato più alto e profondo, durante la memorizzazione e la gestione di fondersi in un singolo sistema robotico chiuso.
Adatto a:
- L'idea semplice ed evolutiva del campo base dei contenitori: un cambio di paradigma nella logistica globale
Il sistema nervoso digitale: IoT e il "porto intelligente"
Un sistema nervoso digitale richiede che un sistema altamente automatizzato possa funzionare come HRL come tutto coerente, un sistema nervoso digitale. L'Internet of Things, IoT) assume questo ruolo. Una rete densamente di sensori su gru, veicoli, infrastrutture e persino sui contenitori stessi sono mappati digitalmente in tempo reale. Innanzitutto, trasparenza in tempo reale: gli operatori sanno ogni secondo in cui ogni contenitore e ogni dispositivo si trovano e in quale condizione è. In secondo luogo, il monitoraggio delle condizioni e la manutenzione predittiva (monitoraggio delle condizioni e mantenimento predittivo): i sensori su componenti critici come motori o archiviazione misurano continuamente dati come vibrazioni, temperatura e pressione. Gli algoritmi analizzano questi flussi di dati e possono prevedere potenziali guasti prima di entrare. Ciò consente una modifica da una coltura di riparazione costosa e reattiva a una manutenzione proattiva e pianificata, che riduce drasticamente i tempi di inattività e può ridurre i costi di manutenzione fino al 50-75 %. In terzo luogo, la creazione di gemelli digitali: le immagini virtuali 1: 1 del porto fisico possono essere create dai dati IoT. In queste simulazioni, nuovi processi, layout o scenari di emergenza possono essere testati e ottimizzati a rischio senza rischi e ottimizzati prima di essere implementati nel mondo reale.
Il nucleo intelligente: ottimizzazione e controllo basati sull'intelligenza artificiale
Se l'IoT è il sistema nervoso, allora l'intelligenza artificiale (AI) e l'apprendimento automatico (ML) sono il cervello del moderno terminal. La quantità pura e la velocità dei dati generati dai sensori IoT non possono più essere elaborate efficacemente dai dispatcher umani. Qui vengono utilizzati sistemi di intelligenza artificiale integrati nel sistema operativo del terminale centrale (TOS) – piattaforma software per il controllo di tutti i processi –
Processo decisionale ottimizzato: gli algoritmi di intelligenza artificiale prendono decisioni complesse in frazioni di secondi. Determinate lo spazio di archiviazione ottimale per ogni contenitore in arrivo che tiene conto di fattori come peso, destinazione e tempo di raccolta. Pianificano la sequenza di movimento più efficiente per le gru e calcolano le rotte ideali per gli AGV per evitare gli ingorghi e ridurre al minimo gli vuoti.
Analisi di preveazione (analisi predittiva): analizzando i dati storici e attuali, l'IA può prevedere i tempi di arrivo delle navi in modo più preciso, prevedere imminenti colli di bottiglia nel cantiere e anticipare il futuro bisogno di personale e dispositivi. Ciò consente una pianificazione proattiva anziché reattiva delle risorse.
Gestione delle risorse: l'intelligenza artificiale ottimizza l'assegnazione di ormeggi, gru e veicoli per massimizzare il throughput complessivo e ridurre al minimo i tempi di attesa per navi e camion. I primi utenti dell'IA nella logistica riportano successi significativi, come la riduzione dei costi logistici del 15 % e un aumento dell'efficienza del servizio del 65 %.
Diventa chiaro che la robotica fisica e l'intelligenza digitale sono indissolubilmente legate. La struttura rigida e altamente complessa di una HRL è gestibile solo da un'intelligenza artificiale altamente sviluppata. Al contrario, il potenziale di ottimizzazione dell'IA può essere completamente sfruttato in un ambiente ricco di dati completamente automatizzato. Questo crea un ciclo di feedback positivo: i migliori dati consentono un'intelligenza artificiale più intelligente, che a sua volta controlla processi fisici più efficienti. L'osservazione spesso citata che le porte automatizzate sono talvolta anche meno produttive di quanto manuale trova la tua spiegazione qui: senza il cervello intelligente (AI), il corpo automatizzato è solo una raccolta di macchine rigide. Il successo dell'automazione dipende in modo evidente dall'intelligenza del tuo sistema di controllo.
Un salto quantistico – i vantaggi a più livelli della nuova generazione di termini
Ri -Finizione dell'efficienza: un salto quantistico in throughput e velocità
I dati sulle prestazioni dei nuovi sistemi ridefiniscono gli standard per l'efficienza. In primo luogo è l'efficienza dell'area: un magazzino ad alto contenuto di battito può raggiungere la tripla capacità di stoccaggio di un cantieri convenzionali gestiti con RTG sulla stessa area di base. In alcune configurazioni, ciò significa ridurre il requisito dello spazio richiesto fino al 90 %. Per i porti intrappolati in dense stanze urbane, questo è un vantaggio inestimabile, allo stesso tempo la velocità della busta aumenta in modo significativo. L'eliminazione di movimenti improduttivi e l'accesso diretto a qualsiasi contenitore può aumentare l'uscita di gestione sul kai fino al 20 %. Ciò riduce i tempi sdraiati delle navi nel porto – un enorme profitto economico per le compagnie di navigazione, per le quali ogni giorno nel porto provoca costi elevati. I tempi di gestione per i camion possono anche essere ridotti del 20 %, il che porta a meno ingorghi alle porte e un migliore utilizzo delle capacità di trasporto.
La tabella seguente confronta gli indicatori di prestazione delle varie tecnologie e illustra il salto quantistico, il magazzino alto.
Confronto di diversi terminali di container
Nella logistica e nell'infrastruttura portuale, i file di termini contenitori svolgono un ruolo cruciale nell'efficienza e nella sostenibilità. Un confronto dettagliato di diversi sistemi di archiviazione mostra differenze significative: il cantiere RTG convenzionale rappresenta metodi di archiviazione tradizionali con una densità di archiviazione di 700-1000 TEU per ettaro e processi circostanti alti tra il 30-60%. Al contrario, l'ASC Yard automatizzato offre una densità di stoccaggio significativamente più elevata di circa 2.000 TEU e costi operativi moderati. Il magazzino alto -bay (HBS) rappresenta la soluzione più avanzata, con un'impressionante densità di stoccaggio di oltre 3.000 TEU, un ambiente completamente eliminato e un inquinamento ambientale minimo.
I sistemi differiscono in modo significativo per produttività, costi e impatti ambientali. Mentre i sistemi convenzionali causano elevate emissioni locali e inquinamento acustico, il magazzino automatizzato e alto -bay offre alternative significativamente più efficienti e rispettose dell'ambiente con un'unità elettrica e una riduzione dei costi operativi. I costi di investimento aumentano proporzionalmente alla complessità tecnologica, per cui il magazzino ad alta base ha i più alti investimenti iniziali, ma anche i costi operativi più bassi.
L'equazione economica: rivalutazione dei costi e rendimento del capitale
L'introduzione di sistemi altamente automatizzati porta a un cambiamento fondamentale nella struttura dei costi. Il modello tradizionale – bassi costi di investimento (Capex) per aree e dispositivi semplici, ma sono invertiti alti costi operativi in corso (OPEX) per personale e – . Un terminal HRL segue un modello ad alta intensità di OPEX. Gli alti costi di investimento sono il più grande ostacolo. I progetti possono costare da diverse centinaia di milioni a oltre un miliardo di dollari USA. Per molti, in particolare gli operatori terminali più piccoli, queste somme sono proibitive. I costi del personale, l'articolo più grande nei terminali manuali, possono essere ridotti fino al 70 %. I costi energetici diminuiscono significativamente a causa del funzionamento completamente elettrico e del recupero dell'energia (recupero); Il progetto pilota Boxbay ha mostrato costi energetici inferiori del 29 % del previsto. Inoltre, ci sono risparmi significativi nella manutenzione a causa della manutenzione in avanti e più robusta a causa dei processi automatizzati. Il ritorno sull'investimento (rendimento del capitale) è complesso e dipendente. Tuttavia, esiste un modello di business convincente se si combina i risparmi OPEX con l'immenso valore delle aree salvate o liberate. Con prezzi immobiliari da 2.000 a 3.000 euro per metro quadrato, il risparmio di soli tre ettari di terra può rappresentare un valore da 60 a 90 milioni di euro, il che mette notevolmente gli alti investimenti iniziali in prospettiva.
The Green Terminal: un nuovo standard di sostenibilità
La nuova generazione di generazione di terminali stabilisce anche standard ecologicamente nuovi e diventa una componente centrale per un settore portuale sostenibile. Il driver principale è l'elettrificazione: i sistemi HRL e i veicoli di trasporto senza conducente associati sono completamente elettricamente ed eliminano le emissioni locali di CO2, ossidi di azoto (NOX) e polvere fine causata da macchine diesel. La combinazione con energie rinnovabili può essere raggiunta. L'enorme area del tetto di un magazzino ad alta baia è ideale per l'installazione di sistemi fotovoltaici che forniscono al terminale l'elettricità verde e potenzialmente lo trasformano in un sistema di energia e l'impatto ambientale viene drasticamente ridotto. Poiché l'operazione avviene completamente automaticamente in un sistema chiuso o incapsulato, il cantiere può essere erogato. Ciò non solo riduce il consumo di energia, ma minimizza anche l'inquinamento luminoso. Allo stesso modo, l'inquinamento acustico per le aree urbane vicine è significativamente ridotto – un vantaggio decisivo per i porti in una posizione urbana. Infine, l'immensa efficienza dell'area dà un contributo diretto alla protezione ambientale, poiché riduce la necessità di progetti di acquisizione di terreni ecologicamente discutibili e costosi da parte di otturazioni.
Rafforzare la rete di trasporto combinata
Questi vantaggi sono trasformativi per i terminali del traffico combinato. Un terminale dotato di HRL cambia da un collo di bottiglia imprevedibile a un nodo di busta ad alta prestazione, affidabile e veloce. L'elevata velocità e, soprattutto, la pianificazione precisa dei processi di gestione per camion e treni sincronizzano le interfacce tra le compagnie di trasporto. Questa affidabilità rende l'intera catena intermodale più competitiva al puro trasporto su strada. Se gli spedizionieri e gli operatori ferroviari possono fare affidamento su una consegna puntuale e rapida nel porto, l'incentivo a spostare i trasporti verso la nave più ecologica o la nave interna aumenta. L'HRL diventa un "fattore abilitante" decisivo per una divisione modale più efficiente e sostenibile nel trasporto di trasporto merci globale.
Rischi e opportunità per l'automazione del porto – ciò che le aziende devono sapere
Il modo per implementare – Navigazione attraverso le sfide
L'ostacolo di investimento: capitale, complessità e regolamentazione
Gli ostacoli primari sono ovvi. L'onere finanziario degli enormi costi di investimento è un enorme ostacolo che può solo gestire i più grandi e migliori operatori e società portuali. La complessità di tali principali progetti pluriennali è immensa e richiede profonde conoscenze specialistiche nei settori della costruzione di piante, della robotica, dell'integrazione IT e della gestione dei progetti. I problemi di interfaccia possono portare a ritardi significativi e aumenti dei costi. Ultimo ma non meno importante, lunghi ostacoli normativi e procedure di approvazione per progetti di costruzione così grandi in molti paesi sono un'altra grande sfida.
Nuovo edificio vs. retrofitting: i due percorsi per la modernizzazione
Esistono due scenari fondamentalmente diversi nell'attuazione, le cui sfide differiscono notevolmente. Il nuovo approccio edilizio, cioè la costruzione di un nuovo terminal sul "Green Meadow", è lo scenario ideale. Offre la completa libertà di progettazione per coordinare il layout, l'infrastruttura e i processi da zero. Il progetto pilota Boxbay a Dubai è un esempio di un tale progetto di costruzione quasi nuovo che ha dimostrato la fattibilità tecnica in condizioni ideali. La nuova tecnologia deve essere integrata in un'operazione 24/7 senza disturbare eccessivamente i processi in corso e il servizio clienti. Ciò richiede un'implementazione complessa e graduale in cui vengono convertite parti del terminale, mentre altre continuano a funzionare. Tali progetti possono durare per anni e sostenere un alto rischio di costi imprevisti e disturbi operativi. L'ordine commerciale per Boxbay a Pusan è quindi di eccezionale importanza: se questa attuazione di retrofit ha successo, ciò dimostra l'idoneità pratica del concetto per la maggior parte dei porti mondiali e potrebbe essere il segnale per un'accettazione del mercato più ampia.
Nella modernizzazione delle infrastrutture e dei sistemi tecnologici, le aziende sono fondamentalmente due modi centrali per scegliere: il nuovo edificio o il retrofit. Entrambi gli approcci differiscono fondamentalmente nelle loro caratteristiche e sfide.
Il nuovo edificio offre la massima libertà di progettazione, consente un coordinamento ottimale di layout e tecnologia e consente un'architettura infrastrutturale completamente nuova. Tuttavia, i costi di investimento iniziali sono molto alti perché tutti i sistemi devono essere ricostruiti. La complessità di integrazione è inferiore perché i sistemi uniformi vengono creati dall'inizio. Il rischio del progetto rimane elevato, principalmente a causa delle immense somme di investimento.
Al contrario, il retrofitting, che è caratterizzato da una libertà di design gravemente limitata. Qui devono essere apportate regolazioni alle strutture esistenti, che progetta l'integrazione estremamente complessa. I costi possono essere potenzialmente inferiori rispetto al nuovo edificio, ma questo approccio comporta un rischio molto elevato di disturbi operativi. Le aziende devono aspettarsi una possibile perdita di capacità nel corso degli anni.
Entrambe le scene del progetto hanno lunghi programmi, con il nuovo edificio più prevedibile, mentre i progetti di retrofit sono più suscettibili ai ritardi imprevisti. La decisione tra questi due modi richiede un'attenta considerazione dei requisiti aziendali specifici, del quadro tecnologico e delle risorse finanziarie.
Il fattore umano: effetti socio -economici e il futuro del lavoro portuale
L'automazione porta inevitabilmente a profondi cambiamenti socio -economici. Non elimina solo i lavori, ma trasforma radicalmente i profili dei requisiti. Le attività manuali come quelle dei leader della gru, i camionisti nel cortile o Laschern sono notevolmente ridotti o scomparino completamente. Allo stesso tempo, si presentano un'alta necessità di nuovi specialisti altamente qualificati nelle aree di esso, robotica, analisi dei dati, monitoraggio del sistema e manutenzione di sistemi complessi. Le strategie proattive e complete per la riqualificazione e l'ulteriore qualifica non sono quindi solo una questione di responsabilità sociale, ma anche una necessità economica per poter coprire la nuova necessità di lavoratori qualificati. Senza personale qualificato per manutenzione e controllo, i sistemi costosi non possono sviluppare il loro potenziale. La partnership sociale svolge un ruolo decisivo. La comunicazione precoce, trasparente e onesta con i sindacati e i rappresentanti dei dipendenti è essenziale per ridurre la resistenza e apportare il cambiamento in modo costruttivo. I concetti sviluppati congiuntamente al cuscino sociale della transizione, per partecipare agli utili della produttività e per progettare i nuovi posti di lavoro possono trasformare i potenziali partner degli avversari della trasformazione e sono un fattore di successo cruciale per un'implementazione regolare.
Rischi digitali: sicurezza informatica nella porta iper -networking
Con la crescente networking e la dipendenza dei sistemi di controllo digitale, sorge nuove vulnerabilità critica: il rischio di attacchi informatici. Un terminal altamente automatizzato è un obiettivo attraente per hacker, sabotatori o attori statali. Un attacco riuscito al sistema operativo del terminale centrale potrebbe paralizzare l'intera operazione porta e avrebbe effetti catastrofici sulle catene di approvvigionamento globale. Ciò richiede un ripensamento fondamentale nella strategia di sicurezza. Sono richieste architetture robuste e multistrato di sicurezza informatica, che includono sia i sistemi IT che OT (tecnologia operativa). Concetti come una "strategia di difesa collettiva", in cui le autorità portuali, gli operatori terminali e le autorità di sicurezza scambiano informazioni e reagiscono insieme alle minacce, diventano una necessità. Il monitoraggio continuo, i test di penetrazione regolari e la formazione del personale nella gestione delle minacce digitali non sono più extra opzionali, ma parte integrante della gestione del rischio in una porta 4.0.
Il terminale del contenitore come sistema operativo logistico
L'analisi mostra che l'ulteriore sviluppo di cantieri di container piatti in cuscinetti verticali a base di intelligenza artificiale non è un miglioramento incrementale, ma una nuova architettura fondamentale della funzione di un terminale container. L'area di parcheggio del contenitore cambia da un luogo fisico per archiviare le merci in un "sistema operativo logistico" ad alte prestazioni e controllato dai dati. I tradizionali fattori competitivi come il prezzo di maneggevolezza puro o la velocità massima prendono un sedile posteriore. Nuovi imperativi strategici sono messi al loro posto: prevedibilità, affidabilità, resilienza e sostenibilità. Un terminal che può garantire l'autorizzazione del camion al minuto è più prezioso per la logistica moderna di uno teoricamente più veloce, ma è imprevedibile in pratica. La visione strategica va ancora oltre. Il magazzino ad alto contenuto di Bay probabilmente non è il punto finale dello sviluppo. Concetti più radicali come la logistica del contenitore sotterraneo (Logistica del contenitore sotterraneo, UCL), in cui i contenitori vengono trasportati completamente automaticamente tra diversi nodi HRL, la banchina e la connessione dell'entroterra, sono già in fase di sviluppo. In tale scenario, il traffico di container scomparirebbe completamente dalla superficie. L'HRL non sarebbe più la soluzione complessiva, ma un componente decisivo in un ecosistema logistico futuro, tridimensionale e completamente integrato.
Per gli attori coinvolti, ciò si traduce in chiare raccomandazioni strategiche per l'azione:
Per gli operatori e gli investitori portuali: l'attenzione deve essere trasferita dai costi di investimento puri (CAPEX) ai costi operativi totali (costo totale di proprietà, TCO) e al valore strategico dell'affidabilità e dell'efficienza dell'area. Gli investimenti nella standardizzazione dei processi e nello sviluppo del personale devono precedere l'implementazione tecnologica.
Per le autorità politiche e normative: il compito è abilitare e accelerare questa trasformazione. Ciò richiede la creazione di un quadro normativo di supporto, la promozione della ricerca e lo sviluppo, il finanziamento dei programmi di qualificazione e l'istituzione di standard internazionali per lo scambio di dati al fine di garantire l'interoperabilità.
Per l'industria logistica: gli spedizionieri, le compagnie di navigazione e gli operatori ferroviari devono adattarsi a una nuova era di interfacce di porte trasparenti iper-efficienti, pianificate e di dati. Questi consentiranno nuovi modelli di business basati su un livello precedentemente senza eguali di integrazione della catena di approvvigionamento e la visione di un trasporto merci globale senza soluzione di continuità, è a portata di mano.
Xpert.Plus Warehouse Optimization – magazzino ad alto contenuto di battite come consulenza e pianificazione del magazzino pallet
Siamo lì per te – Consigli – Pianificazione – Implementazione – Gestione del progetto
☑️ La nostra lingua commerciale è l'inglese o il tedesco
☑️ NOVITÀ: corrispondenza nella tua lingua nazionale!
Sarei felice di servire te e il mio team come consulente personale.
Potete contattarmi compilando il modulo di contatto o semplicemente chiamandomi al numero +49 89 89 674 804 (Monaco) . Il mio indirizzo email è: wolfenstein ∂ xpert.digital
Non vedo l'ora di iniziare il nostro progetto comune.