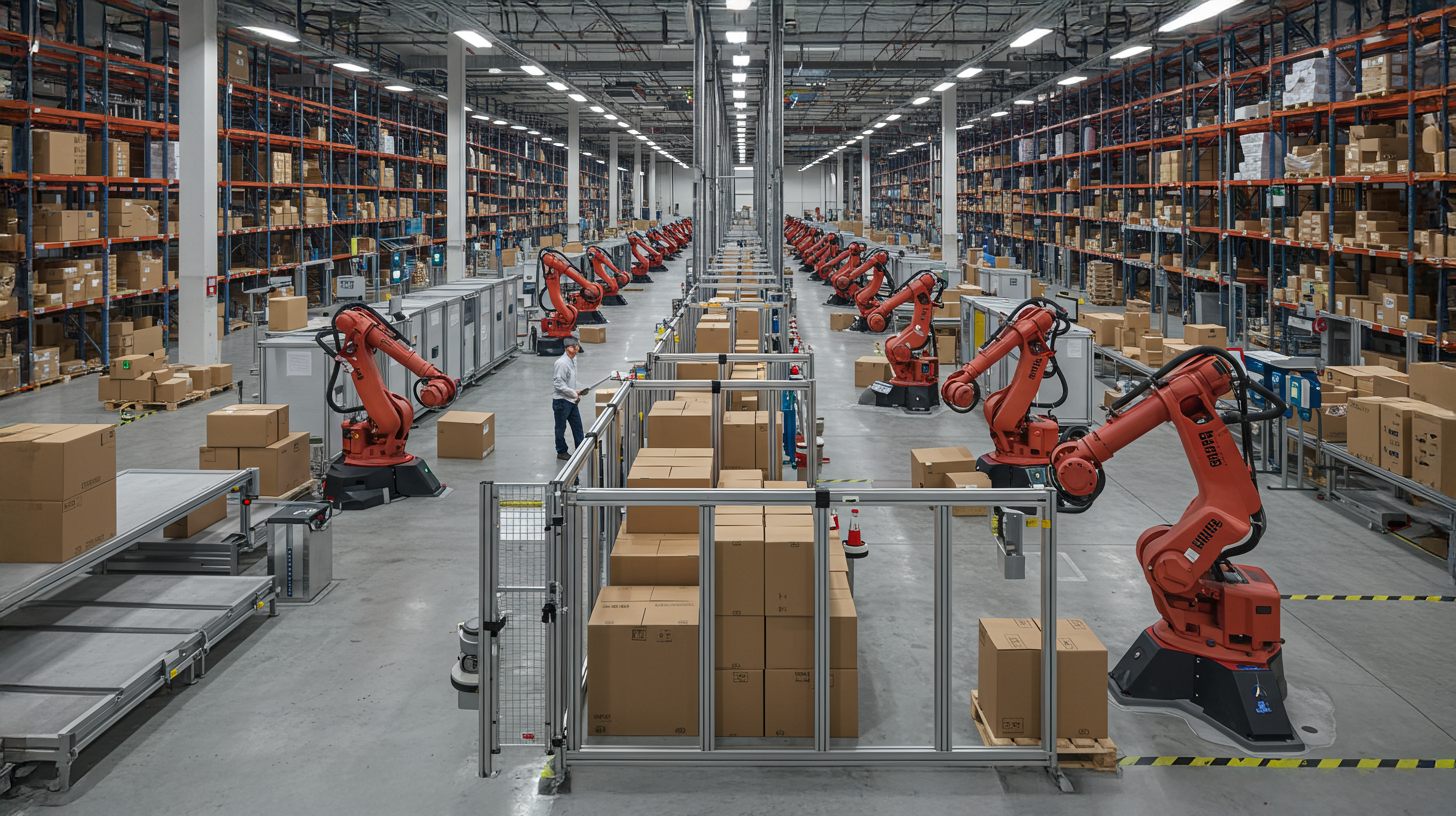
Escasez local? AS/RS y Automatización de almacenes: la clave para 85% más de capacidad y ahorro de costos masivos – Imagen creativa: xpert.digital
Desde el factor de costo hasta el recurso estratégico: tecnologías de almacén modernas
Transformación del proveedor: 5 claves para la agilidad
En el panorama económico dinámico actual, las empresas enfrentan la enorme tarea de hacer que sus cadenas de suministro de ágil, más eficientes y más resistentes. El almacén, una vez un factor de costo puro, se muda al centro de consideraciones estratégicas. La automatización, en particular mediante el uso de sistemas automatizados de almacenamiento y provisión (AS/RS), ya no es una visión futurista, sino una necesidad operativa. Este artículo sirve como un examen profundo que tiene como objetivo iluminar cualquier aspecto crítico de la tecnología AS/RS y su ecosistema circundante. El objetivo es ofrecer a los fabricantes de decisiones estratégicas de una base de datos bien fundada para una de las inversiones más importantes en intralogísticas modernas.
El imperativo estratégico para la automatización de almacenes
¿Por qué la automatización de los almacenes, especialmente a través de AS/RS, se ha convertido en un tema tan crítico y urgente para las empresas modernas?
La urgencia de promover la automatización de almacenes resulta de la reunión de varias fuerzas de mercado fundamentales e irreversibles. Estas fuerzas actúan juntas y crean presión quirúrgica de que los procesos manuales difícilmente pueden resistir.
Primero, experimentamos un crecimiento sin precedentes en el sector logístico. Se espera que el mercado global de almacenamiento y distribución alcance un volumen de $ 650 mil millones para 2026, impulsado por una tasa de crecimiento anual robusta de alrededor del 8 %. Este crecimiento por sí solo requiere una escala masiva de capacidades, lo cual es difícil de realizar con los métodos tradicionales.
En segundo lugar, el auge del comercio electrónico es el catalizador decisivo para un cambio estructural en los requisitos. Para 2025, se espera que el comercio electrónico realice el 22 % de las ventas minoristas mundiales. Esto cambia los perfiles de pedido radicalmente: en lugar de grandes entregas de paletas a algunas ramas, los centros de cumplimiento ahora tienen que manejar un número inmenso de pedidos más pequeños y complejos con períodos de entrega más cortos a clientes finales individuales. Esta complejidad se endurece por el hecho de que el cumplimiento del comercio electrónico necesita hasta tres veces más espacio de almacenamiento que la logística minorista tradicional, lo que hace que la optimización de la habitación sea una prioridad absoluta. Como resultado, el 40 % de las empresas planean invertir en automatización para satisfacer esta demanda.
Tercero, las empresas actúan en un mercado laboral cada vez más tenso. El aumento de los costos laborales y una falta aguda de trabajadores disponibles para actividades de rodamiento repetitivas y físicamente agotadoras representan un obstáculo quirúrgico significativo. Por lo tanto, casi el 60 % de los operadores de almacén planean inversiones dirigidas en tecnologías de automatización, como AS/RS y Robótica, en los próximos dos años para aumentar la productividad y reducir la dependencia de un trabajo de trabajo reducido.
Finalmente, la pandemia Covid 19 ha revelado la fragilidad de las cadenas de suministro globales y ha puesto la necesidad de resiliencia en primer plano. Las empresas reconocen que la automatización es un factor clave para fortalecer sus cadenas de suministro. Reduce la susceptibilidad a las fallas de la fuerza laboral y permite una adaptación rápida a fluctuaciones impredecibles en la demanda, como ser observada durante la pandemia.
Estas cuatro fuerzas – crecimiento del mercado, complejidad del comercio electrónico, escasez de mano de obra y el llamado a la resiliencia – forman un "alicates operativos" que hace que los procesos manuales sean cada vez más insostenibles. Por lo tanto, la automatización de AS/RS ya no es una medida de eficiencia opcional, sino una necesidad estratégica de asegurar la capacidad quirúrgica para actuar y estar en competencia. La inversión cambia de una medida de reducción de costos puros a un pionero decisivo para el crecimiento empresarial y la satisfacción del cliente.
¿Qué es exactamente un sistema automatizado de almacenamiento y provisión (AS/RS) y qué ventajas fundamentales promete?
Un almacén automatizado y un sistema de provisión, para abreviar AS/RS, es un sistema controlado por computadora que lleva a cabo el almacenamiento y la subcontratación de bienes con una intervención humana mínima. Representa una combinación altamente desarrollada de hardware y software. El hardware generalmente incluye estructuras de estanterías, unidades de control de estantes (RBG), transbordadores, robots y tecnología de transporte, mientras que el software del control de almacenamiento (inodoro), la ejecución del almacén (WES) y los sistemas de gestión de almacenes (WMS) consiste en que coordine todas las actividades.
Las ventajas fundamentales de un AS/RS se pueden resumir en varias áreas clave que van mucho más allá de un simple aumento de la eficiencia:
- Uso efectivo del espacio: la ventaja más obvia es la mejora drástica de la densidad de almacenamiento. Mediante el uso de la altura vertical de un edificio, como/rs maximice la capacidad de almacenamiento en un área de piso determinada. Esto reduce la necesidad de extensiones de edificios costosas o ubicaciones adicionales.
- Aumento de rendimiento: debido a la automatización de los procesos de entrada y subcontratación, AS/RS puede mover un volumen significativamente mayor de productos por hora que los sistemas manuales. Esto es crucial para amortiguar las cargas superiores y garantizar tiempos de entrega rápidos.
- Precisión mejorada de selección: los errores humanos en la selección son una de las principales causas de costos y satisfacción del cliente. AS/RS funciona con precisión controlada por computadora, lo que conduce a una composición de orden casi perfecta.
- Ergonomía y seguridad mejoradas: AS/RS se adquiere tareas físicamente agotadoras, repetitivas y potencialmente peligrosas, como levantar cargas pesadas o trabajar a alturas altas. Esto reduce el riesgo de accidentes laborales y mejora significativamente las condiciones de trabajo para los empleados.
- Aumento de la seguridad del producto y el control de inventario: los sistemas ofrecen acceso controlado a los bienes y un seguimiento exacto basado en software de cada movimiento de almacén individual. Esto minimiza el riesgo de robo, daño y existencia.
- Los costos de mano de obra reducidos y los cuellos de botella: la automatización reduce significativamente la dependencia del trabajo manual, lo que no solo reduce los costos salariales directos, sino que también reduce la susceptibilidad a la escasez de mano de obra.
Estas ventajas conducen a un cambio de paradigma fundamental en las operaciones de almacén. El principio tradicional de "persona a buena", en el que los empleados cubren largas distancias en el almacén para elegir artículos, se reemplaza por el principio de "pieza-zur" (bienes a persona). En este modelo, el AS/RS lleva los elementos requeridos directamente a un lugar de trabajo estacionario y optimizado ergonómicamente. Dado que las rutas de ejecución de los empleados pueden obtener hasta el 50 % de sus horas de trabajo, este cambio lleva a un aumento dramático de la productividad. La introducción de un AS/RS es, por lo tanto, más que una actualización tecnológica; Es un catalizador que obliga a un rediseño completo y estandarización de los procesos de almacén y, por lo tanto, permite un nivel de eficiencia completamente nuevo.
¿Pueden estas ventajas prometidas estar respaldadas con datos específicos? ¿Qué mejoras cuantitativas de rendimiento puede esperar de manera realista?
Sí, las promesas cualitativas de la tecnología AS/RS están respaldadas por una impresionante serie de datos de rendimiento cuantitativos que se han demostrado en numerosas implementaciones. Estos números forman la base para cada caso de negocio sólido.
Ahorro y densidad de espacio: AS/RS puede aumentar la capacidad de almacenamiento en un 40 % a 80 % mediante el uso óptimo de la altura de la habitación vertical. En algunas configuraciones, especialmente con sistemas de alta densidad, la densidad de almacenamiento se puede aumentar hasta un 85 % en comparación con los sistemas de estantería tradicionales. Esto significa que casi el doble de productos se pueden almacenar en la misma área base.
Precisión: la precisión de los sistemas controlados por computadora permite la precisión de selección del 99.9 % o incluso más. Este valor no es solo una cifra clave operativa, sino que también tiene profundos efectos financieros. Una reducción de la tasa de error, por ejemplo, del 2 % (típico de los sistemas manuales) al 0.1 % significa una reducción de 20 veces en rendimientos costosos, entregas después de la entrega y clientes insatisfechos.
Rendimiento y velocidad: la automatización de los procesos de entrada y subcontratación conduce a tiempos de procesamiento de pedidos hasta tres veces más rápidos. Esto permite a las empresas ofrecer tiempos de aceptación posteriores para pedidos (tiempos de corte), lo cual es una ventaja competitiva significativa en el comercio electrónico.
Costos laborales y productividad: la reducción de la dependencia del trabajo manual conduce a una reducción en los costos laborales en un 40 % a 70 %. Al mismo tiempo, los aumentos de productividad del 30 % al 50 % se realizan, ya que los empleados restantes trabajan en estaciones de trabajo "de bienes a persona" altamente eficientes.
Seguridad: al minimizar el manejo manual y la interacción de las personas con carretillas elevadoras en los pasillos, los incidentes de seguridad y los accidentes de trabajo pueden reducirse hasta un 50 %.
Tiempo de funcionamiento: AS/RS está diseñado para operación continua y permiten operaciones las 24 horas, los 7 días de la semana sin interrupciones o cambios de cambio, lo que maximiza la utilización de la capacidad del capital invertido.
Retorno de la inversión (ROI): debido a estos considerables aumentos de ahorro y rendimiento, las empresas que invierten en AS/RS a menudo logran un retorno de la inversión en solo 1 a 3 años. En un caso documentado, un ROI del 204 % incluso se logró con un período de amortización de solo 6 meses.
Estas ventajas cuantitativas no deben verse de forma aislada, sino que crean un efecto de retroalimentación positiva. Una mayor precisión reduce los costos de resolución de problemas y aumenta la lealtad del cliente. Un mayor rendimiento permite un mayor volumen de ventas con la misma infraestructura y fuerza laboral. La combinación de estos efectos no solo conduce a un ROI rápido, sino que también crea una ventaja competitiva sostenible y difícil de copiar. El almacén se convierte en una necesidad pura de un motor para la rentabilidad y el crecimiento.
Promesas de rendimiento cuantificable de los sistemas AS/RS: ¿Qué mejoras realistas se pueden probar?
Promesas de rendimiento cuantificable de los sistemas AS/RS: ¿Qué mejoras realistas se pueden probar? – Imagen: xpert.digital
Los sistemas automatizados de almacenes (AS/RS) ofrecen impresionantes mejoras de rendimiento en varias áreas corporativas. El análisis de los indicadores clave de rendimiento (KPI) muestra ventajas significativas: en el uso del espacio, las empresas pueden aumentar la densidad de almacenamiento hasta en un 85 % y aumentar la capacidad de almacenamiento en un 40 a 80 %. Con respecto a la eficiencia, estos sistemas permiten un tiempo de procesamiento hasta tres veces más rápido y aumentar la productividad en un 30 a 50 %.
Otra ventaja crucial es el potencial de una operación 24/7 que maximiza la continuidad de los procesos de almacén. La precisión de la recolección alcanza un impresionante 99.9 % y, por lo tanto, supera claramente los procesos manuales. La optimización de costos también es un aspecto clave: los costos laborales se pueden reducir en un 40 a 70 %. Además, los sistemas AS/RS mejoran la seguridad ocupacional al reducir los incidentes de seguridad hasta en un 50 %.
Desde un punto de vista financiero, el retorno de la inversión típico (ROI) es entre uno y tres años, lo que subraya el atractivo económico a largo plazo de esta tecnología.
Socio experto en planificación y construcción de almacenes
Actualización tecnológica: los sistemas inteligentes detrás de un almacenamiento eficiente
Una visión técnica: la anatomía de las soluciones modernas como/RS
¿Cuáles son los tipos principales de AS/RS y para los cuales los escenarios operativos específicos son los más adecuados?
El mundo de los sistemas automatizados de almacenamiento y provisión es diverso, y la elección del sistema correcto depende de manera crucial de los requisitos específicos de una empresa. No hay un sistema universal "mejor"; Más bien, cada tecnología representa un compromiso optimizado entre la densidad de almacenamiento, el rendimiento y la flexibilidad. Los tipos principales se pueden clasificar de la siguiente manera:
Carga unitaria AS/RS (Pallet-Akl)
Esta es la forma clásica del AS/RS, diseñada para el manejo de unidades de carga grandes y pesadas, como paletas o cajas de red. Las unidades de control del estante (RBG) se mueven hacia adentro y hacia afuera en corredores estrechos y almacenan las paletas dentro y fuera en estantes altos. Este sistema es ideal para el almacén de amortiguación en la producción, el almacenamiento de materias primas o la consolidación de productos listos de productos hechos, es decir, escenarios con relativamente pocas variantes de artículos (SKU), pero de alto volumen por SKU.
Mini-carga AS/RS (Container-Akl)
El sistema de mini carga para manejar artículos pequeños a medianos está diseñado como una contraparte del sistema de carga de la unidad en contenedores, cajas o tabletas estandarizadas. Es la columna vertebral de muchas soluciones de puesta en servicio de "Ware-Zur-Person" y es ideal para aplicaciones con una gran variedad de SKU y altas demandas sobre la precisión, como es típico en el comercio electrónico, en la industria farmacéutica o en la logística de repuestos.
Sistemas de transporte
Esta tecnología representa un desarrollo adicional del principio de mini carga y ofrece el más alto nivel de flexibilidad y escalabilidad. Los transbordadores autónomos se mueven independientemente en cada nivel de un sistema de estante, mientras que los elevadores separados se apoderan del transporte vertical. Este desacoplamiento del movimiento horizontal y vertical permite tasas de rendimiento extremadamente altas. Los sistemas de transporte están predestinados para operaciones de comercio electrónico altamente dinámico con volúmenes de orden fuertemente fluctuantes, ya que el rendimiento se puede ajustar simplemente agregando o eliminando los transbordadores. Algunos sistemas ofrecen una escalabilidad del 100 %.
Sistemas de elevación vertical (VLM) y carrusel
Estas son soluciones de almacén encapsuladas de alta densidad. Los VLM funcionan como un armario con dos filas de tabletas y un extractor en el medio, lo que lleva la tableta solicitada a una apertura ergonómica. Los carruseles giran horizontal o verticalmente para llevar los productos almacenados al operador. Son ideales para almacenar piezas pequeñas en un espacio muy limitado, por ejemplo, directamente en la línea de producción, en talleres o para piezas de servicio.
Sistemas de almacenamiento cúbico (por ejemplo, Autostore)
Esta arquitectura ofrece la densidad de almacenamiento más alta posible. Los robots impulsan una cuadrícula (cuadrícula) sobre un bloque de contenedores apilados directamente. Levantan contenedores y excavan ("excavar") si es necesario. Como no se requieren corredores, el uso del espacio es insuperable. Este sistema es perfecto para aplicaciones en las que maximizar la capacidad de almacenamiento en un área base limitada tiene una prioridad máxima y se requiere un rendimiento medio a alto.
La elección del sistema es una decisión estratégica profunda. Refleja las expectativas de una empresa de su futuro volumen de negocios y su volatilidad. Un entorno de producción estable podría ser bien servido con un sistema de carga unitario robusto. Una compañía de comercio electrónico en rápido crecimiento que tiene que adaptarse a las puntas de demanda impredecibles preferirá la escalabilidad y el rendimiento de un sistema de transporte o la densidad de un sistema cúbico. La evolución de estos sistemas muestra una tendencia clara: lejos de las arquitecturas monolíticas y centralizadas (un RBG por equipo) hacia los sistemas descentralizados, resilientes y granularmente escalables (flotas de transbordadores o robots), que están mejor preparados para las incertidumbres de la economía moderna.
Cuando nos sumergimos en la tecnología, ¿cómo funcionan realmente los componentes centrales mecánicos de los dispositivos de operación de estanterías (en sistemas de carga unitaria) y transbordadores?
Para comprender el rendimiento y los límites de los diversos tipos AS/RS, es esencial una mirada a sus componentes del núcleo mecánico. Las filosofías de diseño de los dispositivos y transbordadores de estantería difieren fundamentalmente.
Unidades de control de estante (RBGS / Grulas de apilamiento)
Los RBG son los caballos de trabajo de la paleta y el contenedor tradicionales como/Rs. Su principio funcional es monolítico e integrado.
Principio básico y eje de movimiento: un RBG es un vehículo de mástil alto que conduce en un solo riel en el piso y, a menudo, con un riel de guía superior en el techo del estante a lo largo de una pandilla estrecha. Su movimiento tiene lugar simultáneamente en dos ejes principales: horizontalmente a lo largo de la pandilla (eje de conducción) y verticalmente a lo largo del mástil a través de un trineo de elevación (eje de elevación). La capacidad de llevar a cabo ambos movimientos al mismo tiempo (viaje diagonal) es crucial para minimizar el tiempo de ciclo.
Alojamiento de carga (LAM): el LAM está unido al trineo Lamban, lo que hace que el depósito real y la subcontratación. En los sistemas de paletas, estos son típicamente horquillas telescópicas que simplemente o dos veces profundas en los sujetos del estante, elevan la paleta y se retiran. Con los sistemas de mini carga, estos pueden ser tablas telescópicas para contenedores de pinza, aspiradora o pequeñas para contenedores.
Diseño del mástil: el diseño del mástil es un factor crítico para la estabilidad y el rendimiento. Los RBG de un ascenso son más ligeros y potencialmente más eficientes energéticamente, pero más susceptibles a las vibraciones a altas velocidades o grandes alturas, lo que puede afectar la precisión del posicionamiento. Aquí, se requiere una tecnología de control sofisticada para la amortiguación de vibraciones.
Los RBG de dos ascensos ofrecen rigidez y estabilidad significativamente mayores, lo que hace que se prefieran para aplicaciones muy altas (más de 40 metros) o cargas muy pesadas. Sin embargo, esta estabilidad se compra con un mayor peso y, por lo tanto, un mayor consumo de energía para la aceleración y el frenado.
Vehículos de transporte
Los sistemas de transporte se basan en el principio de descentralización y desacoplamiento de los ejes de movimiento, lo que les da una mayor dinámica y flexibilidad.
Principio revelado: en contraste con el RBG, la conducción y el levantamiento se combinan en una máquina, el sistema de transporte separa estas funciones.
Movimiento horizontal: el transporte en sí es un vehículo plano, operado por la batería y autónomo. Funciona en rieles dentro de un solo nivel del sistema de estantería y solo es responsable del movimiento horizontal rápido para obtener contenedores o cajas de los sujetos de los estantes y para llevar el comienzo de la marcha.
Movimiento vertical: al final de cada curso hay uno o más elevadores de alto rendimiento. Estos absorben un servicio de transporte (a menudo ya cargado con un contenedor) y lo transportan extremadamente rápido entre los diferentes estantes y para conectarse a la tecnología de financiación previa a la zona, donde los contenedores se entregan a los lugares de recolección.
Estos diferentes enfoques mecánicos tienen profundas consecuencias. El cuello de botella en un sistema RBG es el RBG en sí mismo; Su tiempo de ciclo dicta el rendimiento de todo el curso. En un sistema de transporte, el elevador es el posible cuello de botella. El diseño del sistema tiene como objetivo utilizar de manera óptima este cuello de botella "alimentando" el elevador de varios transbordadores. Esto no solo hace que el sistema sea más potente, sino también granularmente escalable: si necesita más rendimiento, agregue más transbordadores hasta que se alcance la capacidad del elevador. Esto ofrece flexibilidad que un sistema RBG monolítico no puede hacer.
Shuttle vs. Robot: ¿Qué sistema de almacenamiento dominará la industria?
¿Cómo las arquitecturas del sistema líderes – almacenamiento cúbico basado en RBG, basado en transporte y cúbico – se adaptan a figuras clave críticas como el rendimiento, la densidad de almacenamiento y la flexibilidad?
La decisión de una arquitectura AS/RS específica requiere una consideración cuidadosa de los tres parámetros de rendimiento central: densidad de almacenamiento, rendimiento y flexibilidad. Cada tecnología tiene sus fortalezas y debilidades específicas aquí.
Densidad de almacenamiento
La densidad indica cuántos elementos se pueden almacenar en un área de piso determinada.
Sistemas cúbicos (por ejemplo, Autostore): ofrecen la densidad de almacenamiento más alta indiscutible, especialmente en edificios con una altura de techo limitada (menos de 12 metros o 40 pies). Dado que evitan completamente los corredores y apilan los contenedores directamente uno por encima del otro, prácticamente no se desperdicia espacio. Puede aumentar la capacidad de almacenamiento en cuatro veces en comparación con los sistemas de estantes manuales.
Sistemas de transporte y RBG: estos sistemas logran su alta densidad a través de corredores extremadamente estrechos y la capacidad de aprovechar la altura completa del edificio (a menudo hasta 25 metros o más). En edificios muy altos (más de 12-15 metros) puede lograr una densidad más alta que los sistemas cúbicos, ya que estos últimos no pueden explotar completamente la dimensión vertical. La densidad se puede aumentar aún más mediante el almacenamiento de profundidad doble o múltiple, pero esto limita el acceso directo a cada artículo individual y aumenta el esfuerzo administrativo.
Rendimiento
El rendimiento mide el número de entrada y subcontratación por unidad de tiempo.
Sistemas de transporte: se consideran los reyes del rendimiento. Al desacoplar los ejes de movimiento y el uso paralelo de muchos vehículos, puede alcanzar las tasas de rendimiento más altas. Son la opción preferida para los requisitos de rendimiento "muy altos o ultra altos", como los que tienen el cumplimiento dinámico de comercio electrónico. Un solo elevador puede mover hasta 400 contenedores por hora.
Sistemas RBG: ofrece un rendimiento sólido, alto y muy constante. Sin embargo, el rendimiento es limitado debido a los límites físicos de una unidad de control de estante por marcha. Un RBG de paleta típico crea alrededor de 40 entradas y subcontratación por hora. Son muy adecuados para procesos estables con un alto volumen planificado.
Sistemas cúbicos: lograr un rendimiento promedio a alto. El rendimiento se puede escalar muy fácilmente aquí simplemente usando más robots en la cuadrícula y se instalan puertos de selección adicionales. Un factor limitante puede ser la necesidad de borrar el contenedor superior para llegar a más profundo ("excavar"), lo que puede extender el tiempo de ciclo para ciertos pedidos.
Flexibilidad y escalabilidad
Esta dimensión describe la capacidad del sistema para adaptarse a los requisitos comerciales cambiados.
Sistemas de transporte y cúbicos: ofrece la máxima flexibilidad. El rendimiento se puede adaptar dinámicamente al crecimiento empresarial agregando otros vehículos (transbordadores o robots) a la flota sin tener que cambiar el estante básico o la estructura de rejilla. Esto permite una estrategia de inversión de "pago por uso".
Sistemas RBG: son significativamente más limitados en su escalabilidad. El rendimiento está firmemente vinculado a la cantidad de engranajes. Un aumento significativo en el rendimiento generalmente requiere la construcción de corredores completamente nuevos, lo que representa una gran inversión repentina.
Un factor decisivo que conecta estas tres dimensiones es la infraestructura de construcción. La elección de la tecnología y la estrategia de bienes raíces están inextricablemente vinculadas. Una compañía que quiere adaptar un almacén existente con un techo bajo probablemente preferirá la densidad sin igual de un sistema cúbico. Una compañía que está planeando un nuevo edificio en una propiedad costosa podría construir un salón extremadamente alto para minimizar el área base e instalar un sistema de transporte para combinar el máximo rendimiento y alto uso.
Comparación del sistema para la flexibilidad y escalabilidad: ¿Qué tecnología de almacenamiento se adapta mejor al crecimiento y los cambios?
Comparación del sistema para la flexibilidad y escalabilidad: ¿Qué tecnología de almacenamiento se adapta mejor al crecimiento y los cambios? – Imagen: xpert.digital
En la logística y la tecnología de almacén, existen varias soluciones del sistema que difieren en flexibilidad y escalabilidad. Una comparación detallada muestra las ventajas y desventajas de las diferentes tecnologías de almacenamiento.
El sistema RBG (unidad de control de estante) se caracteriza por una alta densidad de almacenamiento, que se logra mediante corredores estrechos y uso óptimo de alturas. Con una altura de hasta 40 metros, ofrece acceso directo a cada paleta. Sin embargo, su escalabilidad es limitada y una falla del sistema detiene inmediatamente todo el engranaje.
Los sistemas de transporte impresionan con tasas de rendimiento muy altas y excelente escalabilidad. Puede reaccionar de manera flexible a los cambios a través de la operación paralela de varios transbordadores. Alcanzan alturas de hasta 25 metros y ofrecen una alta tolerancia a fallas.
Los sistemas cúbicos como Autostore son ideales para ubicaciones limitadas en el espacio. Puede lograr una densidad de rodamiento extremadamente alta sin corredores y permitir una escalabilidad muy alta al agregar robots. La tolerancia a fallas es muy alta porque otros pueden ser compensados por otros.
Los sistemas de almacenamiento vertical (VLM) o los carruseles son particularmente adecuados para el almacenamiento de piezas pequeñas y las islas de producción. Utilizan la altura completa del módulo, pero tienen una velocidad de rendimiento más baja y escalabilidad limitada.
La elección del sistema correcto depende de requisitos específicos como el volumen de pedidos, los requisitos de espacio, la estabilidad del proceso y la flexibilidad.
¿Qué tecnologías de sensores forman el "sistema nervioso" de un AS/RS, y cómo se asegura del nivel requerido de precisión, seguridad y eficiencia?
AS/RS modernos y los robots autónomos que interactúan con ellos son sistemas mecatrónicos complejos, cuya función depende de un "sistema nervioso" sofisticado de varias tecnologías de sensores. Estos sensores proporcionan los datos que son esenciales para los movimientos precisos, la seguridad del personal y el material, así como la eficiencia general del sistema.
Sensores de posición
Son la base para el control preciso. Su tarea es comprender continuamente la posición exacta de los componentes móviles – como la unidad de control del estante, el trineo de elevación en el mástil o el transporte en su nivel – Esto se realiza por tecnologías como sensores de distancia láser que miden la distancia a la medición actual, codificador de tren de cuerda que mide el manejo de una cuerda o sistemas de medición lineales muy precisos que leen una banda de código de barras montada en el estante. Sin esta precisión del milímetro, los espacios de almacenamiento serían imposibles.
Distancia y sensores fotoeléctricos
Este grupo de sensores se hace cargo de una variedad de tareas de vigilancia y control. Funcionan como los "ojos y oídos" del sistema a poca distancia.
Control especialista en ocupación: antes de almacenar una unidad de carga, un sensor verifica si el lugar objetivo es realmente libre de evitar colisiones y reservas falsas.
Control de presencia: detectar sensores a la tecnología del transportador o en la capacidad de carga, ya sea que un contenedor o una paleta se haya registrado correctamente y esté disponible.
Control de supervisión: una de las funciones de seguridad más importantes. Los sensores fotoeléctricos (barreras de luz) crean un "marco" virtual alrededor de la unidad de carga. Si parte de la carga sobresale más allá de este cuadro, el movimiento se detiene para evitar una colisión con la estructura del estante.
Sensores de visión (visión por computadora)
Los sistemas de cámaras, a menudo en relación con los algoritmos de IA, le dan al AS/RS una forma de "visión". Van más allá del reconocimiento de presencia pura y permiten tareas más complejas, como la identificación de objetos, la revisión de códigos de barras o códigos QR para la verificación, el control de calidad (por ejemplo, la detección de envases dañados) y la posición fina de alta precisión al comenzar un espacio de almacenamiento.
LiDAR (detección de luz y rango)
Esta tecnología se encuentra menos en el ferrocarril que se encuentra en sí mismo, pero aún más se encuentra en los robots móviles autónomos (AMR) que navegan libremente que transportan productos a AS/RS. Los sensores LIDAR escanean los alrededores con pulsos láser y crean una tarjeta de nube de puntos 2D o 3D precisa desde el término de la luz reflejada. Esta tarjeta sirve al AMR para la navegación y para detectar obstáculos en tiempo real.
Slam (localización y mapeo simultáneo)
SLAM no es un sensor, sino un algoritmo crucial que procesa los datos de los sensores (como lidar o cámaras). Él resuelve el "problema del huevo de Henne" de la navegación autónoma: un robot necesita una tarjeta para localizarse en una tarjeta. Para crear una tarjeta, necesita saber dónde está. SLAM permite que el robot haga ambas cosas al mismo tiempo – cree un mapa de un entorno desconocido y rastree continuamente su propia posición dentro de esta tarjeta.
La verdadera fuerza de los sistemas autónomos modernos se encuentra en el sensorus. En lugar de confiar en una sola tecnología, los AMR avanzados combinan los datos de diferentes sensores. Por ejemplo, fusionan las mediciones de distancia de alta precisión de LIDAR (bueno para el mapeo de paredes y objetos grandes) con los datos de imágenes de alta resolución de las cámaras (bueno para la detección de pequeños obstáculos planos o signos de lectura). Este enfoque crea una comprensión redundante y mucho más robusta del entorno, que aumenta drásticamente la seguridad y la confiabilidad en los almacenes dinámicos en los que los humanos y las máquinas comparten el mismo espacio. La evolución de la tecnología de sensores desde sensores de posición simples hacia la detección reversible compleja y fusionada es un reflejo de la evolución de la automatización de almacén en sí – desde sistemas rígidos y aislados hasta ecosistemas flexibles y colaborativos.
Xpert.Plus Optimización de almacén – almacén de alto tiempo, como consejos y planificación del almacén de paletas
Su socio global de marketing y desarrollo empresarial
☑️ Nuestro idioma comercial es inglés o alemán.
☑️ NUEVO: ¡Correspondencia en tu idioma nacional!
Estaré encantado de servirle a usted y a mi equipo como asesor personal.
Puedes ponerte en contacto conmigo rellenando el formulario de contacto o simplemente llámame al +49 89 89 674 804 (Múnich) . Mi dirección de correo electrónico es: wolfenstein ∂ xpert.digital
Estoy deseando que llegue nuestro proyecto conjunto.