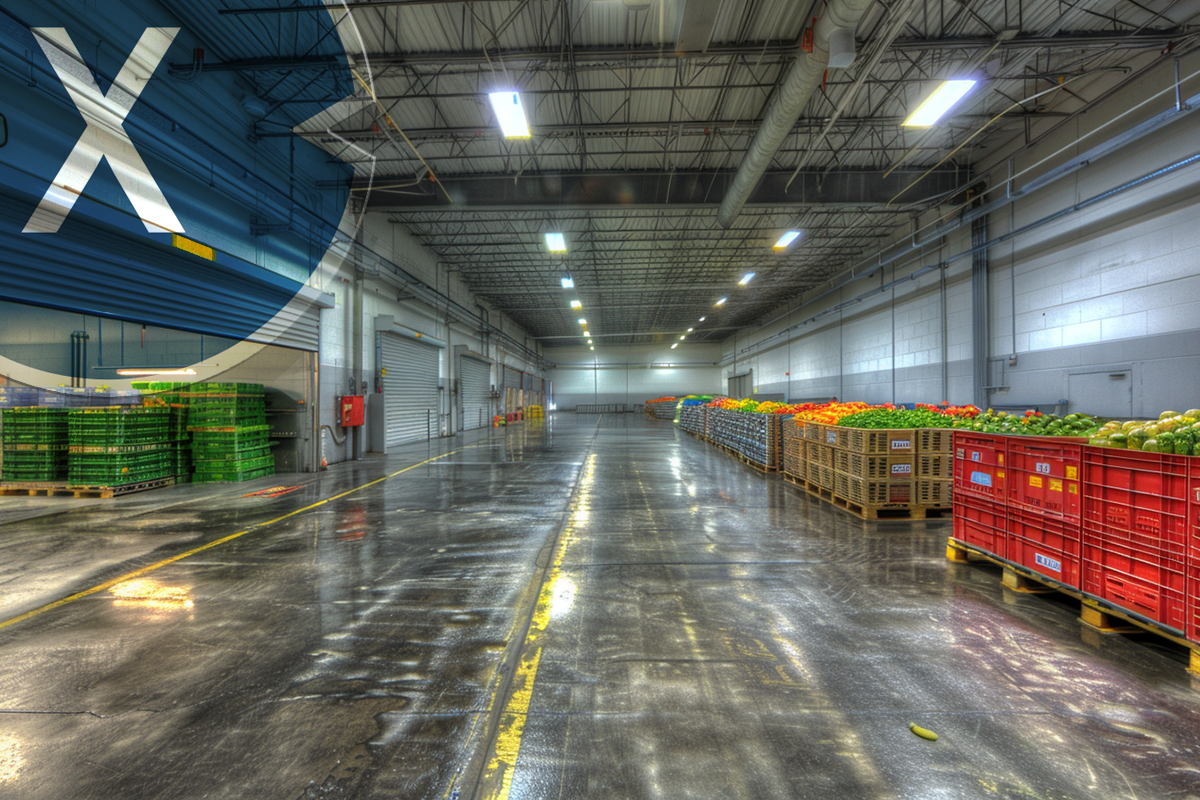
Fresh storage and cold storage Weak points in the cold chain: The key and foundation for efficiency and sustainability – Image: Xpert.Digital
Sustainable cooling technologies: Optimization of energy consumption in warehouses
The planning and operation of fresh food and cold storage facilities pose particular challenges for energy efficiency. Ultimately, the goal is to store sensitive food and other temperature-sensitive goods under optimal conditions while simultaneously keeping energy consumption and environmental impact as low as possible. A well-thought-out energy concept forms the essential foundation for this – from the initial planning phase through construction and ongoing operation. It helps identify energy losses, uncover savings potential, and set the course for sustainable and economical operation.
Where is the energy lost? – Vulnerability analysis in cold storage
Before concrete measures can be taken to save energy, the energy weak points of a cold storage facility must be identified. Where is cold lost, where unwanted heat penetrates and where is energy used inefficiently?
Typical weak points in the cold chain
Poor insulation
Inadequate insulation of walls, ceilings, floors and doors leads to a constant flow of heat from outside to inside. The refrigeration system has to constantly fight against this heat loss, which increases energy consumption.
Leaks
Gaps and joints on doors, windows, gates and ducts act like thermal bridges. Even small leaks can lead to significant energy losses.
Inefficient refrigeration technology
Outdated refrigeration systems, incorrectly dimensioned components or inadequate control of cold generation and distribution cause unnecessary energy losses.
Heat input through use
Every opening of doors and gates, the storage and retrieval of goods, the lighting and the use of industrial trucks in the cold storage facility lead to heat input, which must be compensated for by the refrigeration system.
Lack of waste heat utilization
The waste heat generated during cooling has enormous potential for savings. If it is released into the environment unused, valuable energy is lost.
Energy criteria in focus – The adjustment screws for greater efficiency
A holistic energy concept for fresh and cold storage takes into account various energy criteria and shows optimization potential:
1. Power consumption
At over 70%, electricity consumption accounts for the lion's share of the total energy requirements of a cold storage facility. The main consumers are the refrigeration system, lighting and the office and social rooms.
Optimization potential
Use of energy-efficient refrigeration systems
Modern refrigeration systems with speed-controlled compressors, heat recovery systems and optimized control technology work significantly more efficiently than older models.
lighting concept
Switching to LED lighting reduces the power consumption of the lighting system by up to 80% compared to conventional fluorescent tubes. Intelligent lighting control systems with presence detectors and daylight utilization ensure additional savings.
Energy management in the office
Significant savings can also be achieved in the office and social wing through the use of energy-efficient devices, optimized heating control and raising employees' awareness of how to use energy consciously.
2. Transmission heat losses
Heat losses through the building envelope can be minimized through optimal insulation and the avoidance of thermal bridges.
Optimization potential
High-quality insulation materials
Modern insulation materials such as polyurethane (PUR) or polyisocyanurate (PIR) offer excellent insulation properties with a low installation height.
Thermal bridge-free construction
Through careful planning and execution of the building envelope, thermal bridges can be avoided in critical places such as window reveals, door connections and building corners.
Airtight building envelope
An airtight building envelope prevents warm air from outside from entering the cold storage facility and putting additional strain on the refrigeration system.
3. Heat input
The lower the heat input into the cold storage, the lower the energy requirement of the refrigeration system.
Optimization potential
High-speed gates
High-speed doors at the entrances and exits of the cold storage minimize the opening time and thus reduce heat input.
Thermal insulating curtains
Thermally insulating strip curtains on frequently frequented passageways act as an additional cold curtain and minimize the exchange of air between the temperature zones.
Optimized storage
Well-thought-out storage of goods with sufficient distance from each other and from the walls ensures optimal air circulation and prevents the formation of heat islands.
4. Carbon footprint
The CO2 footprint of a cold storage facility is significantly influenced by the energy consumption of the refrigeration system.
Optimization potential
Natural refrigerants
The use of natural refrigerants such as ammonia (NH3) or carbon dioxide (CO2) is more environmentally friendly than the use of synthetic refrigerants with high global warming potential.
Waste heat utilization
The waste heat generated during cold generation can be used to prepare hot water, to heat offices and social rooms or for other processes.
Photovoltaic system
The installation of a photovoltaic system on the roof of the cold storage facility enables the use of solar energy to generate electricity and reduces the consumption of fossil electricity.
Suitable for:
Investments in energy efficiency pay off
A well-thought-out energy concept is the basis for energy-efficient and sustainable operation of fresh and cold storage facilities. The investments in modern refrigeration technology, optimal insulation, the avoidance of thermal bridges and the use of renewable energies pay for themselves through lower energy costs and a smaller CO2 footprint. In addition, companies benefit from an improved image and increasing competitiveness in a market in which sustainability and environmental protection are becoming increasingly important.
Xpert partner in warehouse planning and construction
Vulnerability analysis in cold storage
Vulnerability analysis in cold storage facilities is crucial to increasing efficiency and minimizing energy losses. Here are some of the most common vulnerabilities and possible optimization measures:
Energetic vulnerabilities
1. Temperature management
Storage temperatures that are too high or too low can cause wasted energy. A temperature difference of 1°C can affect energy consumption by 3 to 4%.
Measures
Optimization of evaporation temperatures and location of condensers to increase efficiency.
2. Insulation
Inadequate insulation of pipes can lead to significant performance losses.
Measures
Improving insulation, especially in suction pipes, to reduce energy losses.
3. Door and gate openings
Frequently opening doors and gates allows warm air to enter, which increases the need for cooling.
Measures
Installation of high-speed doors and airlocks to minimize cold loss.
Technical deficits
1. Outdated equipment
Old refrigerators can be inefficient and break down more often.
Measures
Investment in modern cooling technologies with IoT monitoring for proactive error detection.
2. Oil separator
Lack of oil separators can affect the efficiency of the evaporators and condensers.
Measures
Retrofitting oil separators to increase performance.
Logistical challenges
1. Capacity constraints
Insufficient storage capacity can hinder operations.
Measures
Use of compact storage systems to maximize available space.
2. Lack of skilled workers
Labor shortages in demanding environments such as cold storage facilities are a growing problem.
Measures
Automating processes to reduce staffing requirements.
Safety and quality management
1. Interruption of the cold chain
Interruptions can lead to loss of quality.
Measures
Implementation of SAS systems (Security Airlock System) to avoid cold losses during high goods traffic.
2. Security protocols
Inadequate security measures can increase risks.
Measures
Regular safety inspections and training for staff to minimize hazards.
Through a thorough vulnerability analysis, these problems can be identified and targeted measures can be taken to improve efficiency and safety in cold storage.
Suitable for: