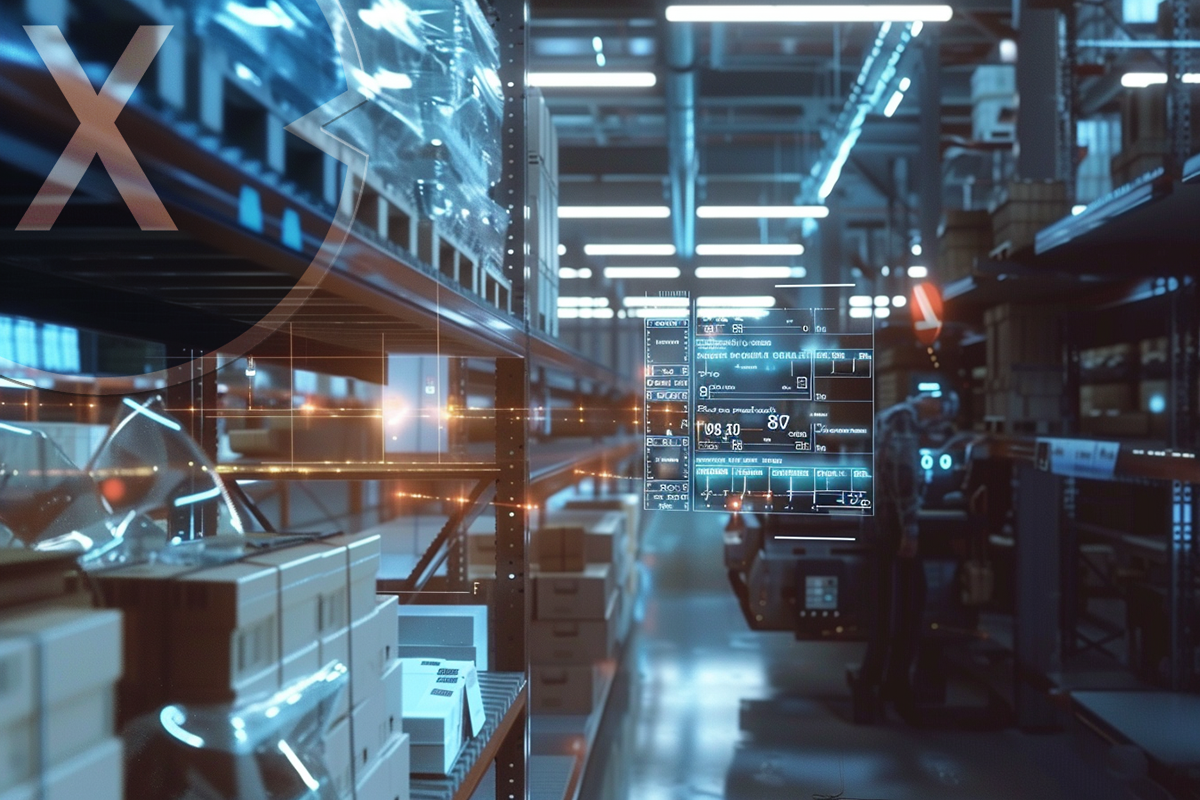
Identification and elimination of bottlenecks in logistics and in the picking methods – Image: Xpert.digital
How to efficiently eliminate bottlenecks in logistics
The efficiency of logistics and especially the picking processes is crucial for the success of a company. Bottlenecks can lead to delays, increased costs and customer dissatisfaction. Therefore, it is of utmost importance for the logistics manager to identify potential obstacles early and implement effective solutions.
The importance of bottleneck identification in logistics
Bottlenecks in logistics can occur in various places: be it in warehousing, transport or in the picking processes. Not only do they lead to internal inefficiencies, but they also impact the supply chain and ultimately customer satisfaction. A systematic approach to identifying and eliminating these bottlenecks is therefore essential.
Steps to effectively identify bottlenecks
1. Get employee feedback
Employees are the heart of every logistics process. Valuable insights can be gained through regular meetings and feedback sessions. Employees experience the daily processes up close and can often best point out where there are problems. Open communication also promotes trust and motivation in the team.
2. Data analysis and metrics
Collecting and evaluating data is crucial. By analyzing lead times, error rates, inventory levels and other relevant metrics, patterns can be recognized and specific bottlenecks can be identified. Modern software solutions make it possible to record and evaluate this data in real time.
3. Process observation on site
Theoretical analysis is important, but nothing replaces direct observation. By observing the picking processes on site, inefficient processes, waiting times or unnecessary steps can be identified. Gemba Walks, a concept from lean management, emphasize the importance of going to where value creation occurs.
4. Use of technological aids
Technologies such as warehouse management systems (WMS) or warehouse execution systems (WES) provide real-time data about inventory levels and picking activities. They not only help identify bottlenecks, but also eliminate them through optimized workflows.
5. Consider customer feedback
Complaints or suggestions from customers can indicate internal problems. Delayed deliveries or incorrect orders are often symptoms of deeper bottlenecks in the logistics process.
Strategies to improve picking methods
1. Optimization of inventory placement
The arrangement of goods in the warehouse plays a crucial role. By placing frequently used items near the picking stations, paths can be shortened and efficiency increased. Methods such as ABC analysis help to categorize products according to their turnover frequency.
2. Implementation of modern picking methods
Techniques such as pick-by-light, pick-by-voice or augmented reality can significantly speed up the picking process and reduce errors. They support employees with visual or auditory instructions and enable hands-free work.
3. Training and ongoing education
Well-trained employees are more efficient and make fewer mistakes. Regular training ensures that staff are familiar with the latest technologies and procedures. Further training also promotes employee satisfaction and reduces fluctuation.
4. Automation of processes
The use of conveyor belts, automated racking systems or order picking robots can increase efficiency and minimize human errors. Automation is particularly useful in areas with high volumes and repetitive tasks.
5. Process standardization and lean management
Standardized work instructions ensure consistency and quality. By applying lean principles, waste can be identified and eliminated. Methods like Kaizen promote a culture of continuous improvement.
6. Integration of supply chain management systems
Seamless integration of all links in the supply chain enables a smooth flow of information. Advanced Planning and Scheduling (APS) systems help optimize production and delivery schedules, which can prevent bottlenecks in advance.
The role of technology in modern logistics
In today's digital era, technologies play an increasingly important role. The Internet of Things (IoT) makes it possible to network devices and systems and receive real-time data. Artificial intelligence (AI) and machine learning can improve forecasts and support decision-making processes. Blockchain technology provides transparency and security in the supply chain.
Suitable for:
Employee engagement and company culture
A culture that promotes openness and innovation is crucial. Employees should be encouraged to contribute ideas and critically question processes. Incentive programs can help motivate employees and increase productivity.
Sustainability and environmental awareness
Bottlenecks are not only economically relevant, but also ecologically relevant. Inefficient processes lead to increased energy consumption and waste. By optimizing logistics processes, companies can reduce their ecological footprint and contribute to sustainability.
Is an ongoing process
Identifying and eliminating bottlenecks in logistics and picking methods is an ongoing process that requires commitment, technology and an open company culture. Through a systematic approach and the use of modern technologies, the logistics manager can not only solve existing problems, but also proactively address future challenges. Ultimately, this leads to more efficient processes, cost savings and higher customer satisfaction.
Xpert partner in warehouse planning and construction
Short version: Identification of bottlenecks in logistics and picking methods
In order to identify bottlenecks in logistics, especially in picking methods, and make improvements, the logistics manager should take a few important steps into account:
Steps to identify bottlenecks
Obtain employee feedback
Hold regular meetings or feedback sessions with employees to hear their observations and suggestions. Employees are often the best informed about where there are problems in daily operations.
Data analysis
Collect and analyze data on lead times, error rates and other relevant metrics. This helps recognize patterns and identify specific bottlenecks.
Process observation
Direct observation of the picking processes on site to identify inefficient processes or waiting times.
Use technological tools
Using technologies such as warehouse management systems (WMS) to obtain real-time data on inventory levels and picking activities.
Possible improvements
Optimization of warehouse placement
Place frequently used items closer to the picking stations to shorten paths.
Suitable for:
Training and continuing education
Provide regular training to employees to increase their efficiency and accuracy.
automation
Use of automation technologies such as conveyor belts or picking robots to increase efficiency.
Process standardization
Develop standardized work procedures to improve picking consistency and quality.
Through these measures, the logistics manager can not only identify existing bottlenecks, but also achieve long-term improvements in picking methods.
Suitable for: