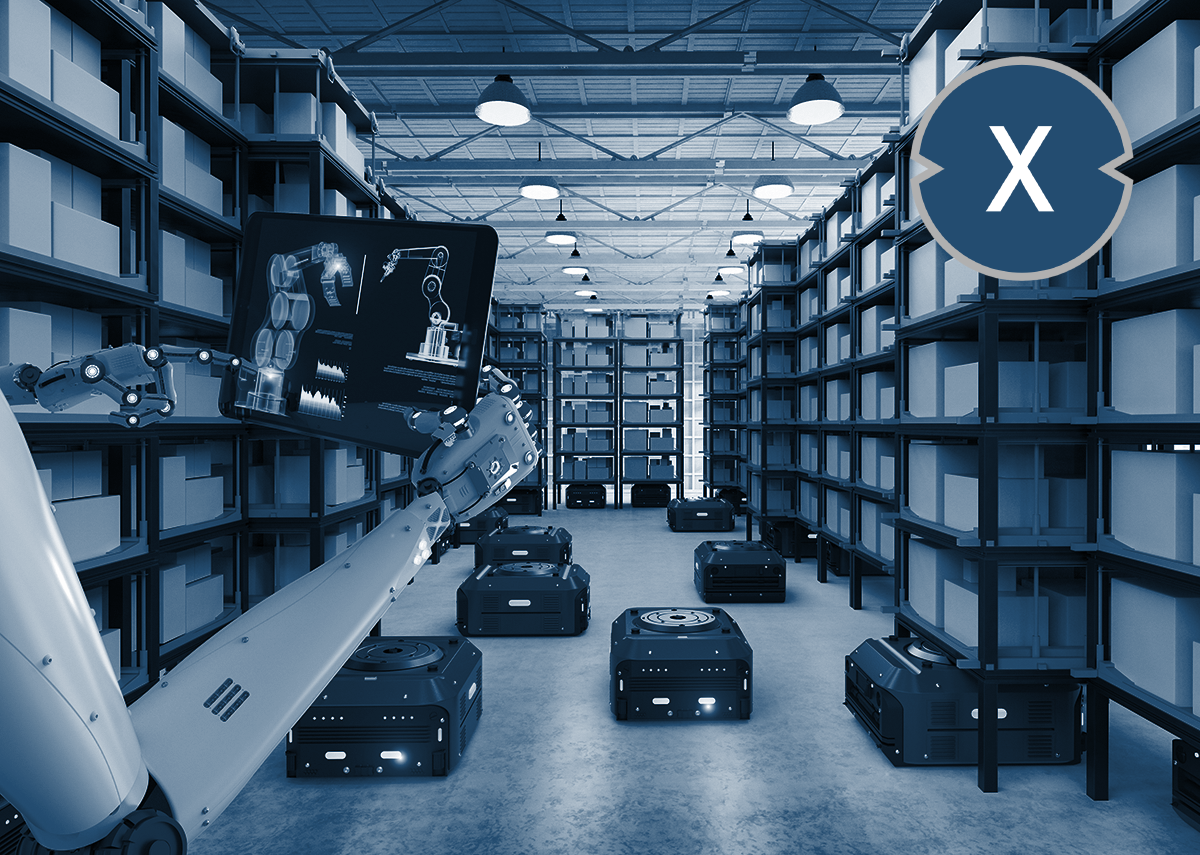
Smart Storage: Warehouse Robots – Logistics robots in the factory or warehouse – Phonlamai Photo|Shutterstock.com
Optimizing your own warehouse logistics is part of the core business for most companies, not just in the mail order business - and at the same time it is also usually one of the largest cost factors. Due to its complexity, improvements in this area are one of the most difficult and often cost-intensive tasks that companies have to face. In order to trim the processes for efficiency, one option is to automate the warehouse using automatic material flow and conveyor systems, in which the goods are stored in state-of-the-art rack warehouses.
But how do the goods get from there to the pick station?
Warehouse workers are often deployed at this point and are sent out with mobile scanners to collect the items for picking. A solution that, in addition to high personnel costs, entails restrictions in terms of time flexibility (keyword around-the-clock picking ) and disadvantages in terms of picking accuracy despite the use of the most modern scanner technology.
Intralogistics providers have also developed solutions to increase pick rates and thus the picking speed. Shipping logistics companies rely on the use of horizontal carousel warehouses. These transport the required items directly to the picking location. Through the automatically controlled provision of products at the workplace, employees can concentrate on other activities such as packaging the goods, which already leads to greater speed and accuracy. In addition, the warehouse employees are spared the tedious walk to the scattered goods, which shortens the walking distance and also increases ergonomics in the workplace.
Of course, technical development does not stop at this point, but continues to progress constantly. There are already several systems on the market that enable dynamic warehousing and picking with the help of autonomous small robot systems that take over the work in a resource-saving manner.
Kiva Robotics – the pioneer
The pioneer in this area is the US company Kiva , which was founded in 2003 and quickly attracted attention in the US logistics industry due to its groundbreaking new development; Their version did not require any conveyor belts, automated high-bay warehouses or new types of transport carts, but instead focused on small, autonomous robots that rolled through the warehouse and picked up small shelves at every point in order to transport them to the packing stations. After the items were removed, the shelves automatically went back and the robot looked for its next target.
Instead of sending warehouse employees with their pick lists or mobile scanners, this task was taken over by the small, orange robot, which, with the help of its integrated lifting technology, transported the entire (small) shelf containing the required goods. Instead of picking up the individual item, the entire shelf is simply taken and transported to the appropriate location. This means that the warehouse is almost constantly in motion, while the warehouse workers stationed at the picking points have the task of simply removing the required products from the shelves that have been brought in.
As everywhere in the age of electronically controlled warehouse logistics systems, the art lies in the software of the entire system, which directs the robots to the right place at the right time. It is obviously not an easy task to avoid the impending traffic jam when using hundreds of robots in warehouses that hold up to several thousand shelves. And it is precisely the almost unlimited scalability and flexibility that makes this system so interesting for users.
In addition to sufficient electricity and investing in the right robots and shelves as well as flat surfaces, the Kiva solution hardly requires any other requirements. On the contrary, numerous factors that are now indispensable when employing warehouse workers are eliminated. This means that the storage areas used do not need to be lit or heated; The robot also works in complete darkness and well below any temperature prescribed for labor law reasons. Except for removal and order picking, human labor is no longer necessary here; which is equivalent to reducing the physical limitations solely on the battery life of the robots. Statutory working and break times as well as factors such as fatigue or distraction are no longer of any importance in the storage process. According to Kiva , the system increases warehouse worker productivity three to four times.
All of these advantages are certainly one reason why the Kiva system is already in use at many of the top US mail order companies. For one of them, by far the largest of them - Amazon - the company concept was so interesting that it acquired the company in 2012, shortly after the technology was presented on the German market.
After purchasing Kiva, Amazon increased production significantly because its own robot demand alone - an estimated 18,000 units for Amazon warehouses worldwide - is about three times higher than the company's total production since its founding. The sale of the system to interested third parties will therefore have to be postponed for the time being.
And what is happening in Germany?
There are now also a number of German mechanical engineers who are working on a comparable solution. One of the pioneers here is the Grenzbach , which claims to be able to reduce picking effort by up to 70 percent with its newly developed G-Com system.
The Bavarian mechanical engineering company's G-Com solution is also based on mobile, agile robots - the so-called carries - which maneuver independently through the warehouse. Since the motors of the small robots are charged via induction, they can operate continuously, eliminating time lost due to time spent at the charging stations. Controlled by the software developed by Grenzbach, the carries drive to the designated shelves, lift them and move the goods to the ergonomically and flexibly configurable picking stations, where the warehouse workers remove the items and prepare them for shipping. The shelves are designed to be completely variable in terms of their layout and can therefore store items of different dimensions and weights. As a result, they are ideal for storing heterogeneous products and for providers who operate with a wide range.
But automation also has other advantages: While with conventional systems warehouse workers often have to travel 15 or even 18 kilometers a day, with robot solutions they can remain stationary at the picking stations without much physical strain, thereby enabling the goods-to-person system Employee travel times have been dramatically reduced. Grenzbach, the picking time is reduced by around 55% compared to conventional solutions. In addition, there is around 15% of the orientation and search time on the shelf, which leads to an increase in efficiency of 70%. Because only the pure picking and storing process of the items is handled manually, personnel costs are significantly reduced. In addition, due to the simplification of the processes, the training time for employees is reduced to just one or two days.
With G-Com, the storage area no longer needs to be lit, ventilated or heated. Here only the area of the picking areas must meet the legal requirements; which usually only affects around 10% of the entire storage area and consequently leads to significant savings in energy consumption.
No induction loops are required to control the carries, which makes the application extremely flexible and should also make moving the storage systems cost-effective and uncomplicated.
The German plant manufacturer Eisenmann is offering Kiva and G-Com its Logimover industrial truck, which operates on a double skid system and weighs just 60 kg. Equipped with a powerful lithium-ion battery concept, the driverless and extremely maneuverable vehicle transports loads of up to one ton in the smallest of spaces at a speed of one meter per second, thus helping to optimize processes in transport and warehouse logistics. The moving robot consists of two runners operating in parallel, which maneuver independently under standard pallets, lift them and transport them to a defined destination using an optical guidance system. The synchronization of the two independent runners is ensured by sophisticated software that monitors and controls the entire path of the vehicle.
According to the company, the Logimover is suitable for a wide range of tasks in intralogistics, from the provision of materials for machines, to the storage and retrieval of all types of goods, to complex picking tasks. The skid concept and the innovative control and drive system of the Logimover are now protected by patents in Europe.
Neobotix took an additional step : With the MT-400, the company presented another autonomous mobile robot at Automatica 2014, which was developed as a cost-effective, highly flexible transport system. Thanks to its compact design, the MT-400 can also move through very narrow aisles where neither floor markings nor other installations are necessary to orient the vehicle. Instead, the navigation system relies on information from an installed laser scanner, which allows the robot to independently avoid obstacles and react to unpredictable situations.
A self-controlling, thinking warehouse robot? From here, the step towards an autonomously operating overall solution that will at some point make the use of humans in the warehouse completely unnecessary does not seem to be far away.
Logistics robots? Who needs something like that?
Despite all their individual differences, the systems from Kiva and the German providers are specifically tailored to the needs of the rapidly growing e-commerce and multi-channel market due to their high level of automation and flexibility.
The main reasons for this are:
Optimal handling of wide product ranges
Due to their flexible and scalable design, the mobile helpers are primarily suitable for warehouse and order picking operations that put together a variety of different shipments from a wide range. They are therefore ideal for logistics solutions from mail order and multi-channel retail companies as well as fulfillment service providers active in the e-commerce industry. Here they can exploit their efficiency advantages and meet the ever-increasing demands of retailers for ever shorter delivery times and permanent cost reductions.
Flexible usage
With the systems presented, almost every item can be stored as long as it does not exceed the maximum dimensions of your chassis. The shelves can also be equipped with trays, drawers, hanging rods, etc. as required and can thus be flexibly adapted to the product range requirements. In this way, they help to use the available storage space more effectively, as each area can be used as a storage area for the mobile shelves. Due to their low demands in terms of technical installations, they can be easily integrated into existing warehouse buildings.
Fast deployment times
By immediately making the goods available at the picking station, the processing time for an order is reduced to just a few minutes. A time advantage that takes into account next and same day delivery
Conclusion
Of course, the use of the little helpers is still possible! – Boundaries set. This means that fast-moving items will continue to be stored most efficiently on pallets within easy reach of the picking stations. Kiva & Co. cannot currently handle the operation of ultra-modern storage lift systems, high and carousel racks or the transport of very heavy or large-volume goods. In the medium term, mixed solutions will be available in which the different systems are operated side by side and complement each other. But the devices can already make a major contribution to significantly increasing the efficiency of warehouse logistics.