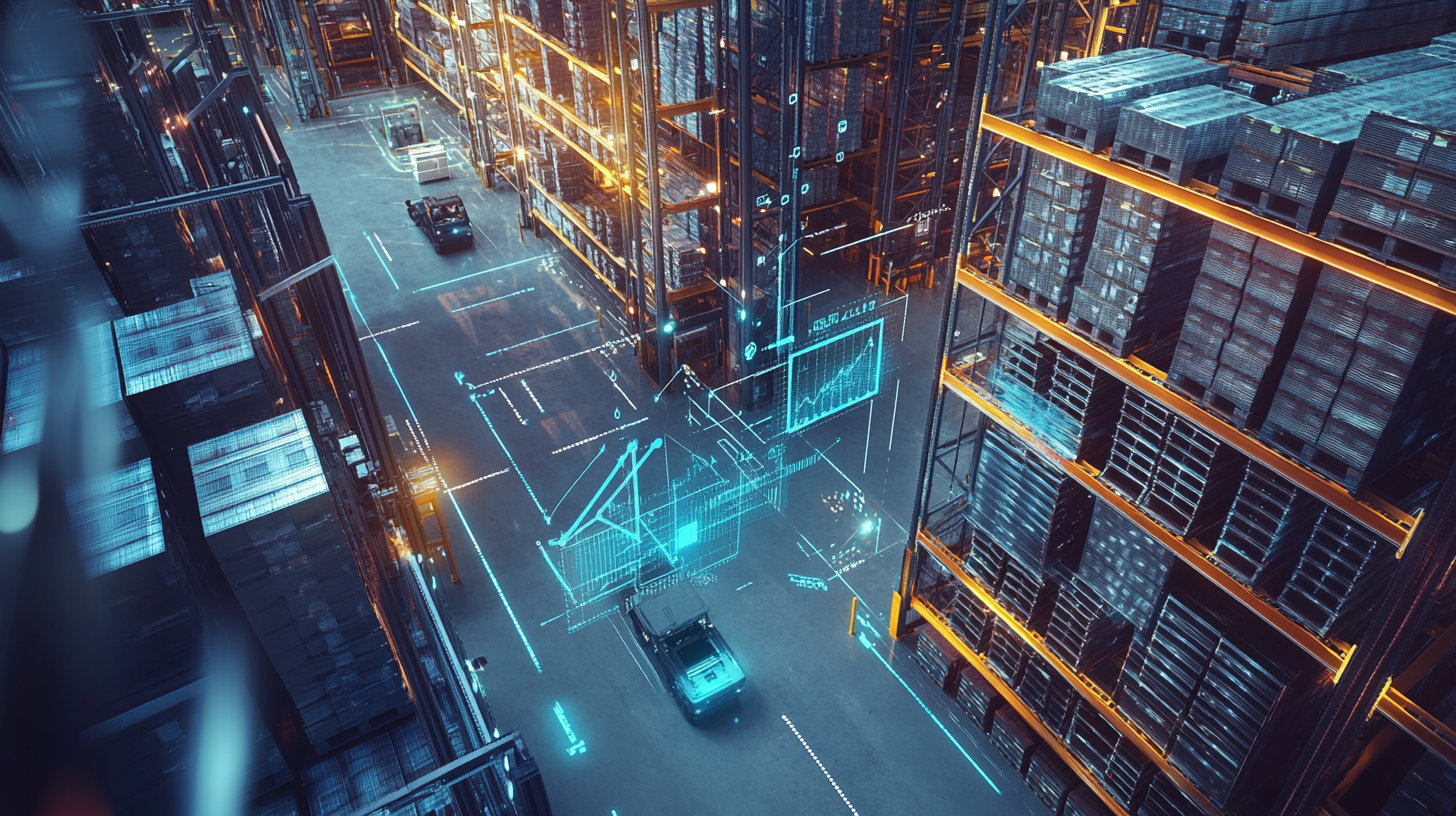
Poland: Fully automated high-bay warehouse and pallet warehouse solutions and consulting, construction, implementation & installation – Image: Xpert.Digital
Efficiency in logistics: Why Polish companies rely on fully automated warehouses
Future of warehousing: Polish companies invest in automation
Polish companies are increasingly relying on fully automated high-bay warehouses and pallet storage solutions to increase their logistics efficiency. These modern systems offer numerous advantages, including optimized space utilization, higher process speed and increased productivity. A comprehensive overview of these technologies is given below, supplemented by interesting insights into current projects and their advantages.
Fully automated high-bay warehouse
High-bay warehouses are specially developed storage structures that can usually reach heights of up to 45 meters. They enable space-saving storage of pallets or pallet boxes and are often equipped with stacker cranes that ensure quick storage and retrieval. These warehouses offer high storage density and are often modular in design so that they can be adapted to individual requirements.
The automation of these warehouses occurs through the use of technologies such as storage and retrieval machines, conveyor technology and software solutions for warehouse management. These systems coordinate the material flow and enable precise control of all processes.
Benefits of automation
Automated high-bay warehouses bring numerous advantages:
- Optimal use of space: Vertical storage maximizes the available space.
- Increased efficiency: Automated processes reduce errors and speed up processes.
- Safety: Minimizing manual intervention reduces the risk of accidents.
- Cost savings: In the long term, automated systems reduce operating costs through reduced personnel and energy costs.
- Flexibility: The systems can be adapted to different industry requirements, e.g. B. for frozen products or dangerous goods.
Examples from Poland
Ceramika Paradyż: Tailor-made solution for the ceramics industry
The Ceramika Paradyż company has built an automated high-bay warehouse in a silo design. This warehouse has a capacity of more than 20,200 pallets and is 25 meters high. It includes eight aisles with single-depth shelving on either side. The integration of the Easy WMS software enables efficient management of warehouse processes.
Particularly noteworthy is the two-story building structure at the entrance to the camp. While incoming and outgoing goods are organized on the lower level, the upper level is used for order compilation. This division increases productivity significantly.
Amica: The highest high-bay warehouse in Poland
Amica, a leading manufacturer of household appliances, has built the highest high-bay warehouse in Poland with a height of 45 meters. This warehouse has space for 25,760 pallets and can store around 230,000 electrical devices. The stacker cranes enable double-deep storage with a load capacity of 2 x 550 kilograms per device.
The high system performance allows up to 160 pallets to be removed and 120 pallets to be stored per hour. Control is carried out via a control center that is seamlessly integrated into the company's SAP system.
Julius Blum GmbH: Expansion of logistics capacities
The furniture fittings manufacturer Julius Blum GmbH has built a new high-bay warehouse near Poznań that includes eight storage and retrieval machines. In addition to warehouse automation, the inventory conveyor technology was also modernized to ensure a smooth flow of materials between the individual logistics areas.
The stacker cranes used are characterized by their longevity and modular design, which makes them particularly adaptable. This facility not only improves storage capacity, but also the efficiency of the entire logistics chain.
Technological innovations
Modern high-bay warehouses rely on advanced technologies such as:
- Storage and retrieval machines: These devices move vertically and horizontally along the shelves and take over the storage and retrieval of pallets.
- Conveyor technology: Various conveyors transport goods within the storage system.
- Warehouse management software (WMS): Systems control all processes in the warehouse and ensure transparency.
- Material flow control: This technology optimizes the flow of goods within the warehouse.
The process: From consultation to installation
The success of a high-bay warehouse or pallet warehouse begins in the planning phase. Polish companies attach great importance to carefully analyzing the needs of their customers and developing the best solutions together. The process can be divided into several steps:
1. Advice and needs assessment
In the first phase, the customer's specific needs are determined. This includes analyzing the existing storage space, the products to be stored and the desired throughput. The aim is to develop a solution that is optimally tailored to the needs of the customer.
2. Planning and Design
During the planning phase, engineers create detailed plans for the warehouse. The most modern CAD software and simulation tools are used to optimize the functionality and efficiency of the system. Particular attention is paid to the integration of automated systems such as storage and retrieval machines, conveyor belts and warehouse management software.
3. Construction and manufacturing
Polish companies rely on high-quality materials and the most modern manufacturing technologies. The components for the high-bay warehouses are prefabricated in specialized workshops, which enables quick assembly on site.
4. Installation and commissioning
Installation is carried out by experienced teams who ensure that the system works precisely and reliably. After installation, the system undergoes extensive testing to ensure that all components work properly together.
5. Training and Maintenance
After commissioning, customers receive comprehensive training so that they can make optimal use of the new system. In addition, many Polish providers offer long-term maintenance contracts to ensure the longevity and reliability of the system.
Challenges and solutions
Despite their advantages, automated high-bay warehouses face challenges such as high investment costs and complex implementation. To overcome these hurdles, providers offer tailor-made solutions that are precisely tailored to the needs of their customers.
An example of this is the possibility of gradually automating existing manual storage systems or replacing individual components such as stacker cranes. This allows companies to better plan their investments while benefiting from the benefits of automation.
Future prospects
The demand for automated warehouse systems will continue to increase, especially in the context of Industry 4.0. Technologies such as artificial intelligence (AI) and machine learning could enable even more precise inventory forecasts in the future and further increase efficiency.
It is also expected that sustainable solutions such as energy-efficient storage and retrieval machines or CO₂-neutral logistics centers will become more important.
Automation increases your competitiveness
Fully automated high-bay warehouses set new standards in the logistics industry. They not only offer high efficiency and security, but also tailor-made solutions for different industry requirements. Projects like those by Ceramika Paradyż, Amica or Julius Blum impressively show how companies can increase their competitiveness through automation. With a view to future innovations, this technology remains a central component of modern logistics strategies.
Suitable for: