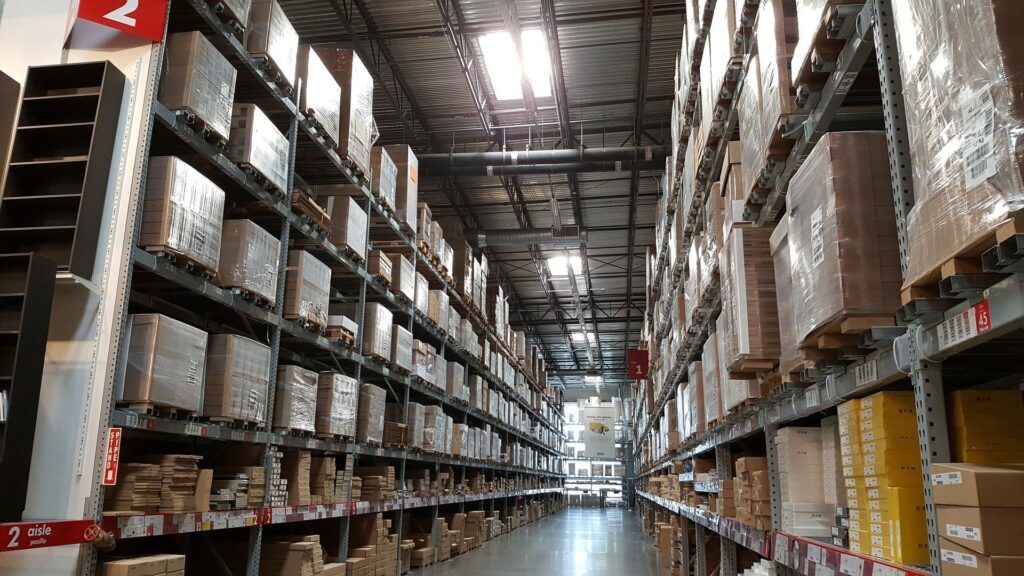
Why pick up the furniture from the rack warehouse if you can't do it via a pick station? (Source: Pixabay)
Pick up furniture at Ikea at the drive-thru counter
Who does not know that? You're in the car, you're hungry and you suddenly decide to stop at one of the big fast food chains, order one of the burger menus at the drive-in terminal and have the bulging bag handed to you through the open window a few meters later. How convenient would it be to be able to purchase bulkier goods such as furniture or hardware store items in the same way?
After the first drive-ins appeared in Germany in the 1950s in the form of drive-in cinemas, it took until the 1980s before McDonald's opened the first drive-in in Berlin to sell its burgers. Since then, drive-ins have enjoyed an impressive triumph in this country and their success has meant that the practical counters are no longer only used by fast food restaurants.
A focus was on supermarket chains such as Rewe , Metro and Real , which tested the collection of items previously purchased online in their stores. There is a good reason for the retailers' activism, as the online giant Amazon already positioned itself in the USA with its Fresh program for groceries and the associated pick-up stations. Observers therefore see the food segment as one of the most important areas of application for Click & Collect and other pickup solutions, in which buyers load their goods into the car like a drive-thru.
So far, handy articles are in the foreground – what about furniture and bulky goods?
But it doesn't just have to be everyday items. Many people who push their way through a crowded hardware store on a Saturday or push their bulky shopping cart through one of the large furniture stores on a Saturday have probably at some point wished that they could conveniently pick up their previously ordered goods at a pickup station in such a store instead of rushing into the weekend hustle and bustle to have to.
Everyone knows them, the huge high-bay warehouses of furniture stores a la Ikea and Co., in which all the Billy, Raka and Kalla cabinets are stored before buyers load them onto their shopping carts. By design, automated vertical carousel warehouses are ideal for storing such large and heavy goods. With their small dimensions, they can be optimally accommodated in limited spaces and can be expanded in height to ten meters or more. Why shouldn't such a storage lift be integrated into the entrance area or directly into the store's parking garage? Consumers could save themselves the tedious walk through the hardware or furniture store and pick up the item they want directly. But customers of Ikea and its competitors have to be patient for the time being, because none of the companies have yet shown any plans to set up such pick-up stations. No wonder, as furniture stores benefit immensely from the many impulse purchases of their customers, who pass countless tempting offers with their purchases on their long way to the checkout.
Although the same applies to hardware stores, they are already further ahead. A pickup station definitely makes sense, especially when it comes to picking up heavy goods such as tiles or building materials. Large players such as Hornbach and Bauhaus have already reacted in this regard, as they occasionally offer consumers markets with integrated drive-in areas.
From vision to reality: Walmart lets customers pick up their purchases from a shuttle
Regardless of whether it is furniture or groceries, compared to shipping, the pickup system has the advantage that the customer has to take a detour and pick up the goods themselves, but can freely decide on the pickup time and saves the sometimes steep shipping costs. Given the broad geographical coverage of supermarket chains in Germany, the detour should not be of any importance for most customers. Technically, such a solution is now easily feasible thanks to modern storage systems, as some of them can also accommodate refrigerated goods.
The US trade giant Walmart . The company has started to build “Pickup Tower” in its US business, from which customers collect their previously placed purchases online. The pick -up stations from the format of a warehouse shuttle have now been set up in the entrance areas of 200 shops, with another 500 of these units to be added by the end of 2018.
Storage devices like the tower used by Walmart have the advantage that they can safely store a very large number of heterogeneous items in a comparatively small footprint and make them available extremely quickly when required. The accuracy required when handing out purchases is also maintained with these systems with their picking precision of almost one hundred percent.
After purchasing, customers will receive an email with the barcode, which will be scanned at the tower. The goods are then made available in less than a minute. In order to be able to sell larger items such as televisions in this way, the devices are now equipped with additional lockable boxes. Walmart is very satisfied with customer acceptance, as over 500,000 orders have been placed via the tower so far. It remains to be seen whether and when Ikea & Co. will be convinced by such a solution. They would be assured of the thanks of their customers.