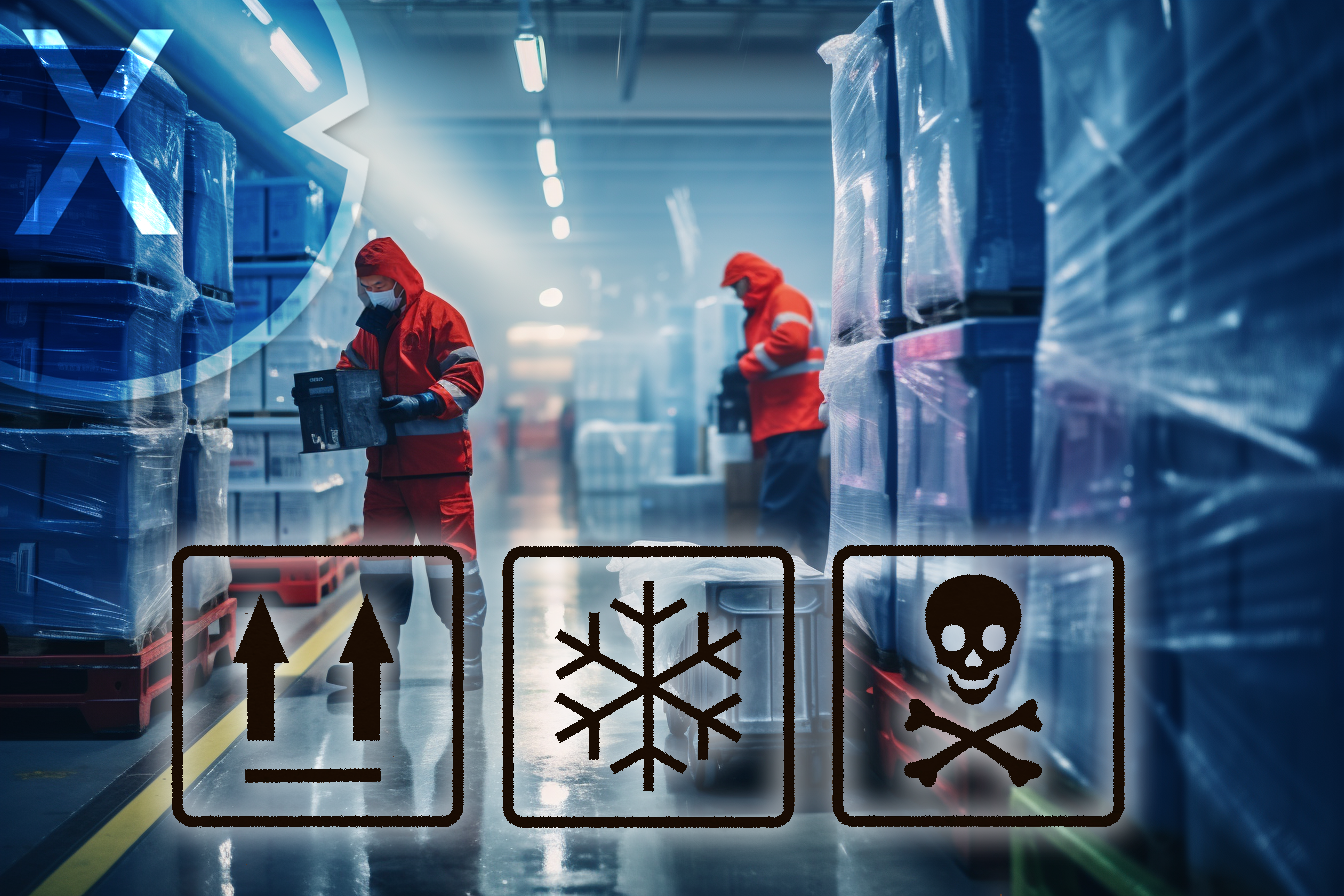
Cooling logistics/fresh logistics: Steam cooler with automated material flow Optimized Distribution processes – Image: Xpert.digital
🥕🥬🥦 Automation in fresh produce logistics is becoming increasingly important
😷👷♀️ In addition to the unpopular but necessary working conditions in refrigeration logistics and the associated shortage of skilled workers, two developments in particular are driving the market forward: On the one hand, advancing urbanization and the increase in the number of people living in cities. According to current forecasts, by 2050 over 68% of the world's population will already be living in cities. This leads to an increasing need for food and product deliveries to urban centers.
🥦🥕 On the other hand, interest in fresh vegan products is constantly increasing. According to studies, consumers are increasingly paying attention to their health and nutrition. Plant-based foods without animal ingredients are therefore becoming increasingly popular. Innovative and efficient logistics solutions are required here to ensure smooth supply even to large metropolises.
💡 An answer to these two challenges offer so -called “smart cities”. This term means cities that are made more resource -friendly and worth living by the broad use of digital technologies. Due to networking, automation and data -based optimization of various processes, the quality of life is to be increased in smart cities and the environmental pollution is reduced.
🗼 Asian countries like Japan in particular are considered pioneers here. Tokyo, one of the largest cities in the world with over 38 million inhabitants, impressively shows how high population density and quality of life can be combined with the help of innovative urban and infrastructure planning. The expansion of efficient transport and supply systems has been the focus here for decades.
🚚🥶 An important aspect is fresh logistics. The safe and quick transport of perishable goods such as food or medical products requires innovative concepts. Tokyo has highly developed refrigerated logistics networks that provide the urban population with a reliable supply of fresh products even during high temperatures or natural disasters.
🤖 A Japanese company that is setting new standards in this area is Daiichi Storehouse & Refrigeration. The company operates a state-of-the-art frozen food distribution center (Frozen DC) in Saitama Prefecture near Tokyo. Around 1,500 frozen foods, including ice cream and pre-cooked frozen foods, are temporarily stored in the four-story, earthquake-protected building every day. Of the 1,500 products, around 600 are particularly high-turnover products, meaning deliveries with a high product variety and small quantities are required, as well as strict batch control based on expiry dates.
Originally, processes such as incoming goods inspection, picking and packaging were carried out manually. However, the arctic temperatures of -25°C in the cold cells placed a physical strain on the staff. Given the increasing variety of products and employee bottlenecks, the company therefore sought to automate processes.
📣 Similar topics
- 🌆🚚 Automation meets urbanization: logistics in the city of the future
- 🌿📦 Green logistics: Fresh vegan products delivered smoothly
- 🤖🏙️ Smart Cities: Intelligent networks for sustainable urban living
- 🇯🇵🌐 Tokyo's Way: Leader in Smart City Innovations
- 🌡️📈 Heat wave vs. cooling deliveries: Tokyo's logistics network in climate change
- ❄️🏭 Daiichi Storehouse: Next-generation cold chain management
- 🔄📊 Process automation: increasing efficiency in cold storage
- 🚀🌱 Vegan boom: logistical challenges and opportunities
- 🏗️🔋 Innovative infrastructure: The building blocks of a smart city
- 🛣️🔗 Connected supply: The future of urban logistics**
#️⃣ Hashtags: #AutomatizationLogistics #VeganProducts #SmartCities #Urbanization #InnovativeLogistics
Xpert partner in warehouse planning and construction
🧊🏭 Daiichi Storehouse & Refrigeration: Increasing efficiency through automation in the deep-freeze warehouse 🧊
The installed Miniload (AS/RS) has nine memory/shelf machines (S/R) and can store up to 15,000 containers – Image: Daifuku
Daiichi Storehouse & Refrigeration has taken a significant step forward in the area of frozen food logistics. Their distribution center in Saitama City is a hub for delivering frozen products to a variety of stores in several prefectures in Japan. With a range of around 1,500 different frozen products, including high-quality items such as ice cream and pre-cooked frozen meals, the company represents a significant part of the food supply chain. Particularly worth mentioning here are the 600 top-selling products, which are a complex one due to their popularity and the associated high demand Logistics and an advanced warehousing system are required.
👷♂️ Challenge of the work environment
The challenge of working in an environment of minus 25 degrees Celsius should not be underestimated. These conditions place high demands on personnel and technical equipment. Before introducing the new system, most processes were carried out manually, which was not only time-consuming but also had a higher potential for errors. By implementing the automated storage and retrieval system (Mini-Load-AS/RS) and using hand-held terminals with character recognition, a significant improvement in efficiency and accuracy was achieved.
🔄 Optimization through technology
The modern material flow system is a core part of the optimization efforts. It includes innovative technologies such as wireless hand-held terminals that make it possible to quickly capture and process product information. The application of the automatic shipping label labeller and the conveyor line capable of moving a large number of containers shows how technology can be used to complement and relieve human labor.
📦 Upon arrival of the products in the warehouse
Each item is scanned, resulting in the generation of receipt labels that are applied to the containers. These preparatory steps are crucial to ensure rapid and accurate distribution and storage of products. The products are distributed across different storage areas depending on the category, allowing for systematic organization and efficient use of space.
When products arrive at the warehouse, employees use a hand-held terminal to scan the JAN or ITF codes as well as the best-before date and manufacturing date on the containers. Once scanned, a portable label printer automatically prints a receipt label that is applied to each container. The containers are then transported to one of four areas: Category A products are sent to the mobile racks, Category B and C products are sent to the Mini-Load AS/RS, and Category D products are sent to the fixed racks.
🚚 The delivery process is particularly interesting
Employees select products based on orders and assemble them into shipments. The automatic labeling system plays a central role in this, as it prints and applies the shipping labels depending on the products' destination. The subsequent sorting and loading onto the shipping lines is also automated. This minimizes human errors and ensures quick shipping processes.
🔄 Consolidation and outsourcing occurs automatically
Consolidation and outsourcing occurs automatically. This step reduces the need for manual intervention and allows staff to focus on more complex and value-added activities. After removal from storage, these products, like the other categories, are further processed on conveyor belts.
During delivery, employees use a hand-held terminal to select products in categories A and D from the mobile racks and fixed shelves. The selected products are grouped into orders and fed into an automated labeling system that automatically applies shipping labels based on the shipping destination. As the products move on to shipping, they are automatically sorted into shipping lines based on the labels. Before goods are loaded into shipping trucks, employees confirm that all containers are on the correct line. Category B and C products stored in the Mini-Load AS/RS are automatically consolidated and offloaded, requiring little on-site staff activity, freeing staff for other tasks. After being removed from the AS/RS, products in categories B and C are transported by conveyor belt and then treated in the same way as the other products.
🌟 The consistent further development and adaptation of the logistical processes in the Daiichi Frozen Distribution Center (Frozen DC)
Serves as an exemplary model for the entire industry. It shows how, by using modern technology and striving for continuous improvement, companies are able to not only increase their efficiency, but also improve the working conditions for their staff. These innovations are critical to meeting the increasing demands of the market while ensuring employee satisfaction and safety.
📣 Similar topics
- 🚀 Innovations in frozen logistics
- 📦 Efficient storage of frozen products
- 🔥 Challenges at minus 25 degrees Celsius
- 🤖 Automation in the Daiichi Frozen Distribution Center
- ❄️ Cold and precision: The new storage system
- 📋 Technology at the service of food supply
- 🏭 Modernization of logistical processes
- 📡 Wireless handheld terminals in frozen food logistics
- 📝 From manual process to accuracy
- 🌟 Success model for the entire industry
#️⃣ #InnovationsInLogistics #EfficientStorage #AutomationTechnology #ColdLogistics #ModernizationOfProcesses
Xpert.plus warehouse optimization – high -bay warehouse such as pallet warehouse advice and planning
We are there for you – advice – planning – implementation – project management
☑️ Smart City & Factory: Industry expert for energetic 5G buildings and halls as well as advice and installation of solar systems
☑️ Xpert.plus – logistics advice and logistics optimization
☑️ Industry expert, here with his own Xpert.Digital Industry Hub with over 2,500 specialist articles
I would be happy to serve as your personal advisor.
You can contact me by filling out the contact form below or simply call me on +49 89 89 674 804 (Munich) .
I'm looking forward to our joint project.
Xpert.digital – Konrad Wolfenstein
Xpert.Digital is a hub for industry with a focus on digitalization, mechanical engineering, logistics/intralogistics and photovoltaics.
With our 360° business development solution, we support well-known companies from new business to after sales.
Market intelligence, smarketing, marketing automation, content development, PR, mail campaigns, personalized social media and lead nurturing are part of our digital tools.
You can find more at: www.xpert.digital – www.xpert.solar – www.xpert.plus
Industrial & B2B Business Metaverse: Reduce costs with XR technology for photorealistic product images (XR 3D rendering machine)
XR technology offers a superior solution for creating photorealistic images and allows companies to free themselves from the expensive fees of external media agencies. It is common knowledge that media agencies charge high costs to create such images as it requires expertise, special software and collaboration with various experts.
More about it here: