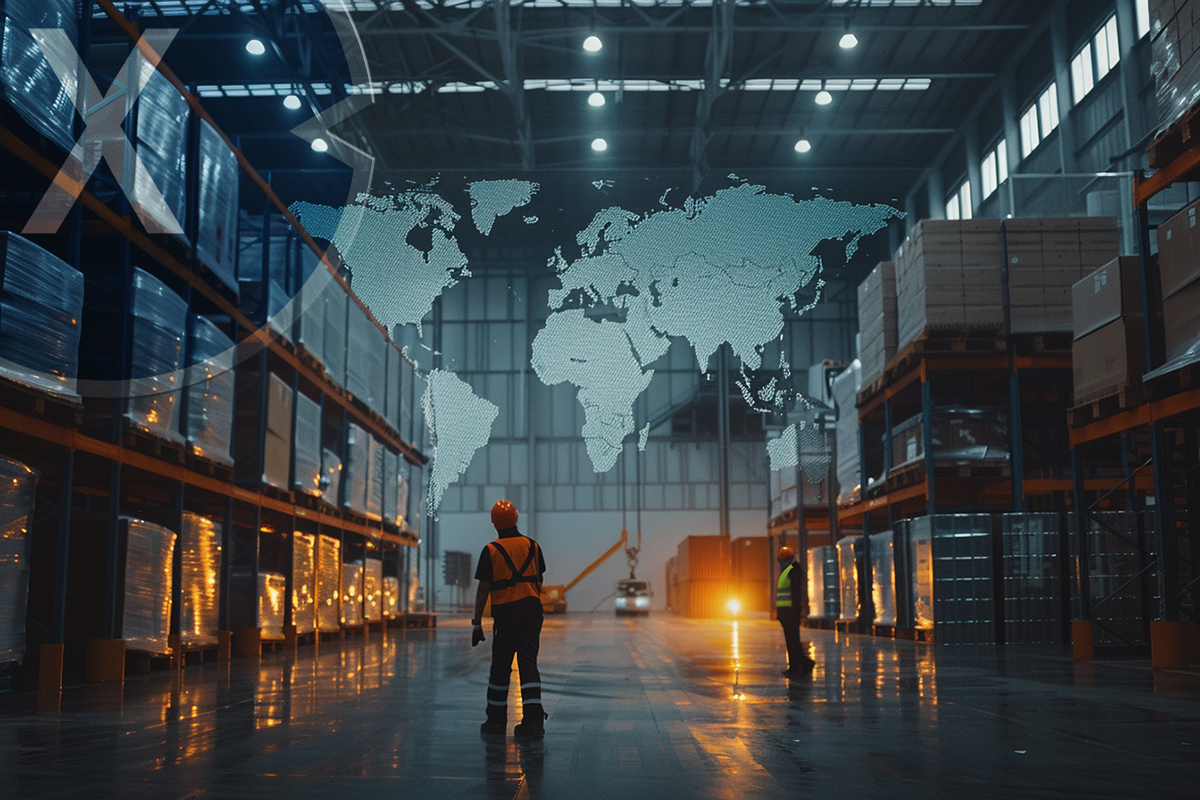
Nearshoring and buffer stocks: Strategies for risk minimization in global supply chains – Image: Xpert.Digital
From global to local: Nearshoring as a response to crises
In an increasingly globalized world, companies rely on making their supply chains efficient and low-risk. Recent global events, such as the COVID-19 pandemic and geopolitical tensions, have exposed the fragility of traditional supply chain models. Two strategies that have proven to be particularly effective in minimizing risk are nearshoring and building buffer stocks.
Matches:
Nearshoring: A return to proximity
Nearshoring refers to the relocation of production or service processes to geographically closer countries. This strategy offers several advantages:
Shorter delivery times
By being close to sales markets, companies can react more quickly to changes in demand. This not only reduces delivery times, but also transport costs.
Improved communication
The smaller geographical distance makes exchange between the parties involved easier. Cultural and language barriers are often lower, which improves collaboration.
Risk reduction
Political instability or natural disasters in distant countries can significantly disrupt supply chains. Nearshoring minimizes these risks by reducing dependencies on distant regions.
An example of successful nearshoring is the automotive industry in Europe, which is increasingly relying on production facilities in Eastern Europe. These countries not only offer cheaper labor but also a strategic location within Europe.
Buffer storage: security through stocks
Buffer stocks are inventories that companies create to cushion fluctuations in demand or disruptions in the supply chain. This strategy has proven particularly useful for dealing with unforeseen events:
Continuity of care
By creating buffer warehouses, companies can ensure that they can continue to serve their customers even in the event of delivery bottlenecks.
flexibility
Buffer storage enables companies to react flexibly to changes in the market. You can respond quickly to spikes in demand without having to wait for new deliveries.
Cost control
Although the creation of buffer warehouses involves costs, these can be more than offset by avoiding production downtimes and sales losses.
An example of the successful use of buffer storage can be found in retail. Large retail chains use buffer stocks to compensate for seasonal fluctuations and ensure that popular products are always available.
Integration of both strategies
The combination of nearshoring and buffer storage can be an extremely effective strategy for minimizing risk. While nearshoring reduces dependence on distant countries and increases flexibility, buffer warehouses provide an additional layer of security against unforeseen disruptions.
Challenges and solutions
Despite their advantages, both strategies are not without challenges:
Cost
Both nearshoring and the creation of buffer warehouses require investments. Companies must carefully consider whether the potential savings from reduced risks justify these costs.
Logistical complexity
Implementing these strategies can be complex and requires careful planning and coordination.
To overcome these challenges, companies should use modern technologies. Digital tools such as supply chain management systems and real-time data analytics can help optimize processes and make more informed decisions.
Future developments
Further trends that influence nearshoring and buffer storage could develop in the future:
sustainability
The pressure on companies to act more sustainably is increasing. Nearshoring can help reduce the carbon footprint through shorter transport routes.
Technological innovations
Advances in automation and robotics could make nearshoring even more attractive as labor costs become less of an issue.
Geopolitical changes
The political landscape is constantly changing. Companies must remain flexible and adapt their strategies regularly.
Ways to minimize risk in global supply chains
Nearshoring and buffer storage offer effective ways to minimize risk in global supply chains. They enable companies to react more flexibly to changes and increase their security of supply. Despite the challenges, they offer significant long-term benefits in terms of cost control and risk management. In a world full of uncertainty, these strategies are valuable tools for any company that wants to remain competitive.
Xpert partner in warehouse planning and construction
Nearshoring and buffer storage: Strategies for minimizing risk in global supply chains
Global supply chains have come under increasing pressure in recent years. Disruptions caused by political tensions, natural disasters and, last but not least, the COVID-19 pandemic have forced companies worldwide to rethink their supply chain strategies. Traditionally, supply chain management has been based on the global distribution of production and resources, with a focus on reducing costs and increasing efficiency. But in an increasingly uncertain and volatile world, flexibility, risk protection and resilience of supply chains are becoming increasingly important. Two key strategies that help companies minimize risk and make their supply chains more resilient are nearshoring and buffer storage. These approaches not only provide greater control over the supply chain, but also faster responsiveness to market changes and unforeseen disruptions.
1. The importance of nearshoring
Nearshoring is a concept in which companies relocate their production or parts of the supply chain from distant countries back to geographically closer regions. In contrast to offshoring, where production is often relocated to countries with lower labor costs (e.g. Asia), nearshoring involves relocation to countries closer to the home market, often within the same geographical or economic region.
Advantages of nearshoring
1. Shorter delivery routes and faster response times
A key advantage of nearshoring is the reduction of the physical distance between production and market. This allows delivery times to be significantly shortened, which is particularly advantageous in industries that rely on quick time to market and flexibility, such as the fashion or electronics industry. Companies can respond more quickly to changes in demand and avoid long transportation times that often cause delays in global supply chains.
2. Better control and quality assurance
The geographical proximity gives companies the opportunity to monitor their production processes more closely and ensure higher quality assurance. In many cases, nearshoring also enables closer collaboration with suppliers and better communication. This can be particularly advantageous in technologically demanding industries where quality and precision are crucial.
3. Reducing political and logistical risks
Nearshoring offers companies the opportunity to avoid political instability, trade conflicts or sudden tariff increases in distant countries. Proximity to more stable markets and access to well-developed logistics and infrastructure systems in neighboring countries significantly reduce the risk of supply chain disruptions.
Challenges of nearshoring
Despite the many advantages, nearshoring is not without its challenges. Labor costs in nearshoring countries are often higher than in traditional offshoring destinations. Companies must therefore weigh up whether the benefits of shorter supply chains outweigh the higher production costs. There may also be a lack of specialized labor or specific technologies that are more readily available in traditional producing countries.
2. Buffer stock as a risk management strategy
Buffer stocks, also known as safety stocks or security stocks, represent another strategy for minimizing risks in the supply chain. They refer to the accumulation of additional inventory levels that go beyond actual requirements and are used to absorb fluctuations in demand or interruptions in the supply chain.
Advantages of buffer storage
1. Protection against supply bottlenecks
One of the main goals of buffer warehouses is to avoid supply shortages. By maintaining additional inventory, companies can bridge temporary disruptions in the supply chain, such as natural disasters or production downtimes. This is particularly important in industries with complex supply chains and dependent production steps, such as in the automotive industry or electronics manufacturing.
2. Flexibility in response to changes in demand
In a dynamic market environment, fluctuations in demand can change from one moment to the next. Buffer storage offers companies the flexibility to respond quickly to unexpected spikes in demand without having to interrupt production. This is particularly valuable in seasonal industries or when launching new products.
3. Stability of production
Buffer storage helps maintain production stability even if there are unexpected delays in the delivery of raw materials or intermediate products. This reduces the risk of expensive production stops and ensures that companies can achieve their production targets even in times of crisis.
Challenges of buffer storage
Although buffer storage offers many advantages, they also come with significant costs. Building and maintaining additional inventory can be expensive, especially when it comes to perishable goods or products with a short lifespan. In addition, buffer stocks tie up capital that could be invested elsewhere in the company. Another challenge is the correct dimensioning of the buffer storage: stocks that are too large lead to unnecessary costs, while stocks that are too small do not adequately cushion the risk of bottlenecks.
3. The combination of nearshoring and buffer storage: A strategic approach
While nearshoring and buffer storage already offer significant advantages as individual strategies, it turns out that the combination of both approaches enables an even higher level of resilience and flexibility in the supply chain. Companies that locate their production geographically closer to home markets while simultaneously building buffer stocks can take advantage of both strategies to protect themselves against a variety of risks.
Case study: The automotive industry
An example of the successful combination of nearshoring and buffer storage can be found in the automotive industry. Automotive manufacturing relies on a highly complex supply chain that includes thousands of components, often sourced from different countries. In recent years, many car manufacturers have begun to relocate parts of their production from Asia to nearby countries in order to reduce dependence on distant suppliers and shorten delivery times. At the same time, they have set up buffer warehouses to avoid bottlenecks in the supply of critical components such as semiconductors. This combination allows automobile manufacturers to react more flexibly to market changes and minimize the risk of production interruptions.
Advantages of the combination
The combination of nearshoring and buffer storage offers several strategic advantages:
1. Maximum flexibility
Companies can respond quickly to market changes by taking advantage of both the geographical proximity of production and the availability of inventory. This enables rapid adjustment to fluctuations in demand or unexpected delivery failures.
2. Optimized risk distribution
Nearshoring reduces dependence on distant and potentially unstable markets, while buffer storage provides additional insurance against unforeseen events. Together, these strategies enable a balanced distribution of risk and minimize the risk of default.
3. Cost efficiency through synergies
Although both nearshoring and buffer storage involve costs, combining both approaches can result in synergies that reduce overall costs. For example, shorter supply chains can reduce inventory costs because less safety stock is required to accommodate delays.
4. Future prospects: Resilient supply chains in the 21st century
In a world increasingly characterized by uncertainty and disruption, supply chain resilience is becoming a critical competitive factor. Companies that are able to react quickly and flexibly to changes will have a clear advantage over their competitors. Nearshoring and buffer storage are central components of this new supply chain strategy. But in the future, other factors, such as the digitalization of the supply chain, the introduction of artificial intelligence and the development of new logistics technologies, will also play an important role.
Companies that recognize these trends early and incorporate them into their strategic considerations will be able to make their supply chains not only more resilient, but also more efficient and sustainable. Nearshoring and buffer storage are just the beginning of a comprehensive change in supply chain management that will become even more important in the coming years.
Suitable for: