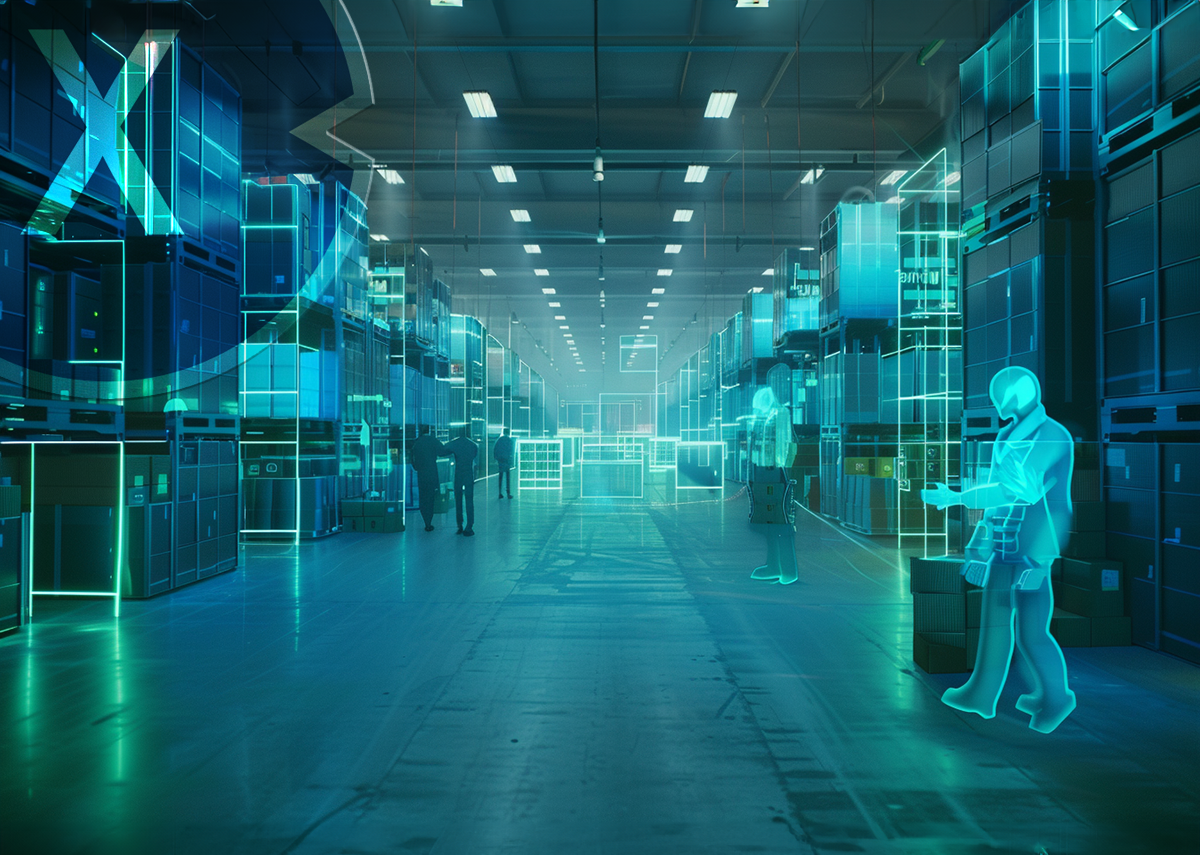
Maximum availability: Make your own warehouse and storage system maximally available - minimize downtimes & increase productivity with digital remote support - Image: Xpert.Digital
📦 Optimize warehouse processes: Minimize downtime with innovation
✔️💼 Warehouse success factor: How you can score points with remote support
In today's competitive business world, the efficiency of warehouse processes is critical to a company's success. Unplanned downtime can not only result in significant financial losses, but can also impact customer satisfaction. Supply chains have become more complex and customers' expectations for fast and reliable deliveries are constantly increasing. Therefore, it is of utmost importance to make your warehouse and storage system maximally available in order to minimize downtime and increase productivity. An effective solution to this is remote assistance, which allows problems to be quickly diagnosed and resolved without having to wait for a technician on site. In addition, it offers the possibility of monitoring and optimizing processes in real time.
🔍💰 Achieve maximum availability and minimize downtime costs
Every minute that a warehouse system isn't working means lost productivity and potentially lost business opportunities. Studies show that unplanned downtime can cost businesses thousands of dollars per hour, depending on the size of the operation and the type of products stored. The impacts range from delayed deliveries to production downtimes to a damaged reputation with customers and partners.
By using remote support, companies can maximize the availability of their systems. Experts can access systems remotely, identify problems and often fix them immediately. This significantly reduces the duration of outages and minimizes the associated costs. Additionally, preventive maintenance enabled by remote monitoring can identify and resolve potential problems before they result in failures. This increases the overall reliability of the system and contributes to smooth operations.
🛠️📡 Benefit from remote diagnosis and remote repair services
Remote diagnostics uses modern communication technologies to connect technicians to on-site systems. Secure internet connections allow them to access machine controls, sensors and other devices in real time. This allows for quick identification of problems without the need for a technician to be physically present.
The benefits are obvious: faster response times, reduced travel times and costs, and faster restoration of normal operations. In cases where physical intervention is required, remote diagnostics can help identify the necessary spare parts and tools in advance, making the on-site visit more efficient. Companies also benefit from ongoing support that can be available outside of regular business hours, which is particularly advantageous for companies with shift work or around the clock operations.
🛡️🔐 Implement a state-of-the-art security software system
With the increasing digitalization and networking of warehouse systems, the risk of cyber attacks and data breaches also increases. A security incident can not only disrupt operations, but also endanger sensitive company data. Therefore, implementing a state-of-the-art security software system is essential.
Such systems provide multi-layered protection against unauthorized access and ensure the integrity and availability of data. Features include firewall protection, intrusion detection systems, regular security updates and patches, and encryption of sensitive data. Additionally, it is important to establish strict access rights and authentication mechanisms to ensure that only authorized personnel can access critical systems.
Working with trusted remote assistance solution providers that maintain high security standards is crucial. This ensures that the benefits of remote support can be achieved without compromising system security.
📊🔍 Achieve more transparency in your warehouse processes
Transparency is a crucial factor for optimizing warehouse processes. By using remote monitoring tools, companies can access key performance indicators in real time. This includes information about inventory levels, machine performance, order status and more.
This increased transparency makes it possible to quickly identify bottlenecks and inefficient processes and take proactive measures. For example, delays in order processing or irregularities in the flow of materials can be identified and corrected immediately. In addition, transparency promotes better communication between different departments and locations because everyone involved has access to the same up-to-date data.
The ability to monitor processes remotely not only increases efficiency but also improves decision making. Managers can make informed decisions based on current data and trends, ultimately leading to better overall warehouse performance.
🖥️📈 Be able to monitor productivity with machine data analysis
Machine data analysis plays a crucial role in increasing productivity. By collecting and analyzing data from different machines and systems, companies can gain insight into the performance of their equipment. This data can include information about operating times, energy consumption, utilization, temperature, vibration and more.
Machine data analyzes make it possible to predict maintenance requirements, identify inefficient processes and uncover optimization potential. For example, an increase in vibration levels can indicate an impending mechanical problem, allowing preventive maintenance measures to be taken before a failure occurs.
With the help of remote support, this data can be collected and evaluated in real time. Experts can analyze trends, create reports and make recommendations for process improvements. This leads to faster response times and continuous improvement of operations.
Additionally, by using machine learning and artificial intelligence, companies can learn from this data and implement automated optimizations. This can lead to significant efficiency gains and cost savings.
👩🏫👨🏫 The role of employees and training
While technologies such as remote assistance and data analysis are important tools, people remain a crucial factor for success. It is important that employees receive appropriate training to use these technologies effectively. Training should not only cover technical aspects but also convey the importance of security policies and best practices.
Employees should be encouraged to be proactive, report problems and suggest improvements. A culture of continuous improvement and collaboration promotes the successful implementation of new technologies and processes.
🏭🔧 Maximize system availability and minimize downtime
Remote support offers numerous advantages for companies that want to optimize their warehouse processes. By maximizing system availability and minimizing downtime, companies can increase productivity and gain competitive advantage. The implementation of modern security software systems ensures the security of the systems and data.
The increased transparency and the ability to analyze machine data make it possible to continuously improve processes and make them more efficient. Companies can react more quickly to changes, make decisions based on current data and use their resources optimally.
At a time when speed and efficiency are critical factors for business success, leveraging remote support solutions is an important step to modernize and future-proof warehouse processes. Companies that implement these technologies better position themselves to meet increasing market demands and achieve long-term success.
Investing in remote support and modern technologies is not only a question of current efficiency, but also an investment in the future viability of the company. By adapting to the changing technological landscape and leveraging the benefits of digitalization, companies can strengthen their position in the market and explore new opportunities.
📣 Similar topics
- 🔧 Achieve maximum availability of your storage system
- 🛠️ Minimize downtime with remote support
- 🚀 Increase productivity with remote support
- 🕒 Efficiently reduce unplanned downtime
- 🌐 Take advantage of remote diagnostics and remote repairs
- 🔒 Implement security software systems for warehouse processes
- 📊 Increase transparency in your warehouse processes
- ⚙️ Monitor productivity through machine data analysis
- 💼 The role of employees and training in remote support
- 📈 Future-proof warehouse processes through modern technologies
#️⃣ Hashtags: #warehouse processes #remote support #security #productivity #transparency
Xpert partner in warehouse planning and construction
✳️ Make optimal use of your own warehouse and storage system - reduce downtime and increase efficiency
📦 In today's fast-paced business world, optimizing warehouse processes and systems is critical to a company's success. Efficient warehouse management can not only reduce operating costs, but also increase customer satisfaction and ultimately increase profits. In this comprehensive guide, we'll take an in-depth look at how to maximize your warehouse and storage system availability, minimize downtime, and increase productivity.
👁️🗨️ The importance of stock availability
The availability of a warehouse refers to the ability to maintain operations and store, process, and ship goods efficiently. High availability is crucial to fulfill customer requests, maintain delivery times and secure competitive advantages. Downtime, on the other hand, can lead to significant financial losses, customer dissatisfaction and reputational damage.
Factors affecting inventory availability
- Technical infrastructure
- Human resources management
- Process optimization
- Maintenance and repair
- Safety measures
🔧 Remote support as the key to optimization
A crucial factor in increasing warehouse availability is the use of remote support. This technology allows experts to remotely access systems, diagnose and often even fix problems without having to be physically there.
Benefits of Remote Support
Quick problem solving
With instant access to systems, problems can often be resolved in minutes rather than hours or days.
Cost efficiency
Reducing on-site visits saves time and travel costs.
24/7 availability
Remote support can be offered around the clock, which is particularly advantageous for warehouses with shift operations.
Preventive maintenance
Regular remote monitoring allows potential problems to be identified early and resolved before they lead to failures.
🛡️ Implementation of an advanced security software system
The safety of the warehouse and the goods stored in it is of utmost importance. A modern security software system should cover the following aspects:
1. Access control
Biometric systems or RFID cards for employees
2. Video surveillance
High-resolution cameras with motion detection
3. Alarm systems
Immediate notification of unauthorized access
4. Data security
Encryption of sensitive information and regular backups
5. Fire protection
Smart smoke detectors and automatic extinguishing systems
Integrating these security measures into a central management system enables efficient monitoring and rapid response to potential threats.
🔍 Increase transparency in warehouse processes
Transparency in warehouse processes is crucial for efficient operational management. It enables managers to make informed decisions and quickly identify bottlenecks.
Methods to improve transparency
Real-time tracking
Implementing RFID or barcode systems to accurately track goods.
Digital dashboards
Visualize important KPIs in real time for everyone involved.
Process automation
Use of automated conveyor systems and robots to reduce human errors.
Integrated software solutions
Using ERP and WMS systems for seamless data integration.
📊 Productivity monitoring through machine data analysis
Leveraging big data and machine learning can revolutionize productivity monitoring. By analyzing large amounts of data, patterns can be identified and predictions can be made, leading to continuous improvement of warehouse processes.
Areas of application of data analysis in the warehouse
Inventory optimization
Predict demand fluctuations and automatically adjust inventory levels.
Route optimization
Calculating the most efficient routes for forklifts and other means of transport in the warehouse.
Personnel planning
Analysis of workloads for optimal staff allocation.
Quality control
Early detection of quality deviations through pattern analysis.
Energy management
Optimizing energy consumption based on usage patterns.
⚙️ Strategies to minimize downtime
Reducing downtime is a key factor in maximizing inventory availability. Here are some proven strategies:
1. Preventive maintenance
Regular inspections and maintenance of equipment and systems to identify problems early.
2. Redundant systems
Install backup systems for critical components to quickly switch over in the event of failures.
3. Employee training
Regular training on how to properly operate equipment and identify potential problems.
4. Emergency plans
Develop and regularly practice emergency plans for various scenarios.
5. Fast spare parts supply
On-site storage of critical spare parts or arrangements with suppliers for quick deliveries.
🤖 Innovative technologies to increase efficiency
Integrating modern technologies can significantly increase the efficiency and productivity of a warehouse. Here are some forward-looking solutions:
Autonomous Mobile Robots (AMR)
These robots can move around the warehouse and transport goods independently, increasing efficiency and reducing human errors.
Drones for inventory
Drones can be used for quick and accurate inventory taking in large warehouses.
Augmented Reality (AR) for order picking
AR glasses can support employees in picking by displaying directions and product information in real time.
Internet of Things (IoT)
Networked sensors can monitor and automatically adjust environmental conditions such as temperature and humidity.
Artificial intelligence (AI) for demand forecasting
AI algorithms can analyze historical data and make precise predictions for future demand.
🌱 Sustainability in warehouse management
Sustainability is not only important from an environmental perspective, but can also lead to significant cost savings. Here are some approaches for sustainable warehouse management:
Energy efficient lighting
Switching to LED lighting and intelligent lighting control systems.
solar power
Installation of solar panels on warehouse roofs to generate your own electricity.
Water management
Implementation of rainwater harvesting systems and water saving technologies.
Waste reduction
Implement recycling programs and use reusable packaging materials.
Green logistics
Optimization of transport routes and use of electric vehicles for internal transport.
📈 Continuous improvement through key performance indicators (KPIs)
Regular monitoring and analysis of key performance indicators is crucial for continuous improvement of warehouse processes. Important KPIs for warehouse management are:
- Inventory turnover ratio
- Picking accuracy
- Lead time of orders
- Warehouse utilization
- Labor productivity
- Return rate
- Overall Equipment Effectiveness (OEE)
By regularly checking these KPIs, potential for improvement can be identified and targeted measures can be taken.
💡 Maximizing the availability of your own warehouse and storage system
Maximizing the availability of your warehouse and storage system is a complex but rewarding process. By using remote support, advanced security systems, increased process visibility and data-driven productivity monitoring, companies can optimize their warehouse processes, minimize downtime and increase efficiency.
The integration of innovative technologies, the focus on sustainability and the continuous monitoring of key performance indicators are other key factors for success. In an increasingly competitive business world, a well-optimized warehouse system can make all the difference.
Companies that invest in these areas and cultivate a culture of continuous improvement will not only reduce their operational costs, but also be better positioned to respond to ever-changing market demands. Ultimately, efficient and reliable warehouse management leads to higher customer satisfaction, stronger competitiveness and sustainable business success.
📣 Similar topics
- 📦 Optimized Warehouse Management: A Guide
- 📈 The importance of stock availability
- 🌐 Remote support as the key to optimization
- 🔒 Implementation of an advanced security software system
- 🔍 Increase transparency in warehouse processes
- 🤖 Productivity monitoring through machine data analysis
- 🔧 Strategies to minimize downtime
- 🚀 Innovative technologies to increase efficiency
- 🌱 Sustainability in warehouse management
- 📊 Continuous improvement through key performance indicators (KPIs)
#️⃣ Hashtags: #warehouse management #increasing efficiency #sustainability #technology #customer satisfaction
Xpert.Plus warehouse optimization - high-bay warehouses such as pallet warehouses consulting and planning
We are there for you - advice - planning - implementation - project management
☑️ Smart City & Factory: Industry expert for energetic 5G buildings and halls as well as advice and installation of solar systems
☑️ Xpert.Plus - logistics consulting and logistics optimization
☑️ Industry expert, here with his own Xpert.Digital Industry Hub with over 2,500 specialist articles
I would be happy to serve as your personal advisor.
You can contact me by filling out the contact form below or simply call me on +49 89 89 674 804 (Munich) .
I'm looking forward to our joint project.
Xpert.Digital - Konrad Wolfenstein
Xpert.Digital is a hub for industry with a focus on digitalization, mechanical engineering, logistics/intralogistics and photovoltaics.
With our 360° business development solution, we support well-known companies from new business to after sales.
Market intelligence, smarketing, marketing automation, content development, PR, mail campaigns, personalized social media and lead nurturing are part of our digital tools.
You can find out more at: www.xpert.digital - www.xpert.solar - www.xpert.plus