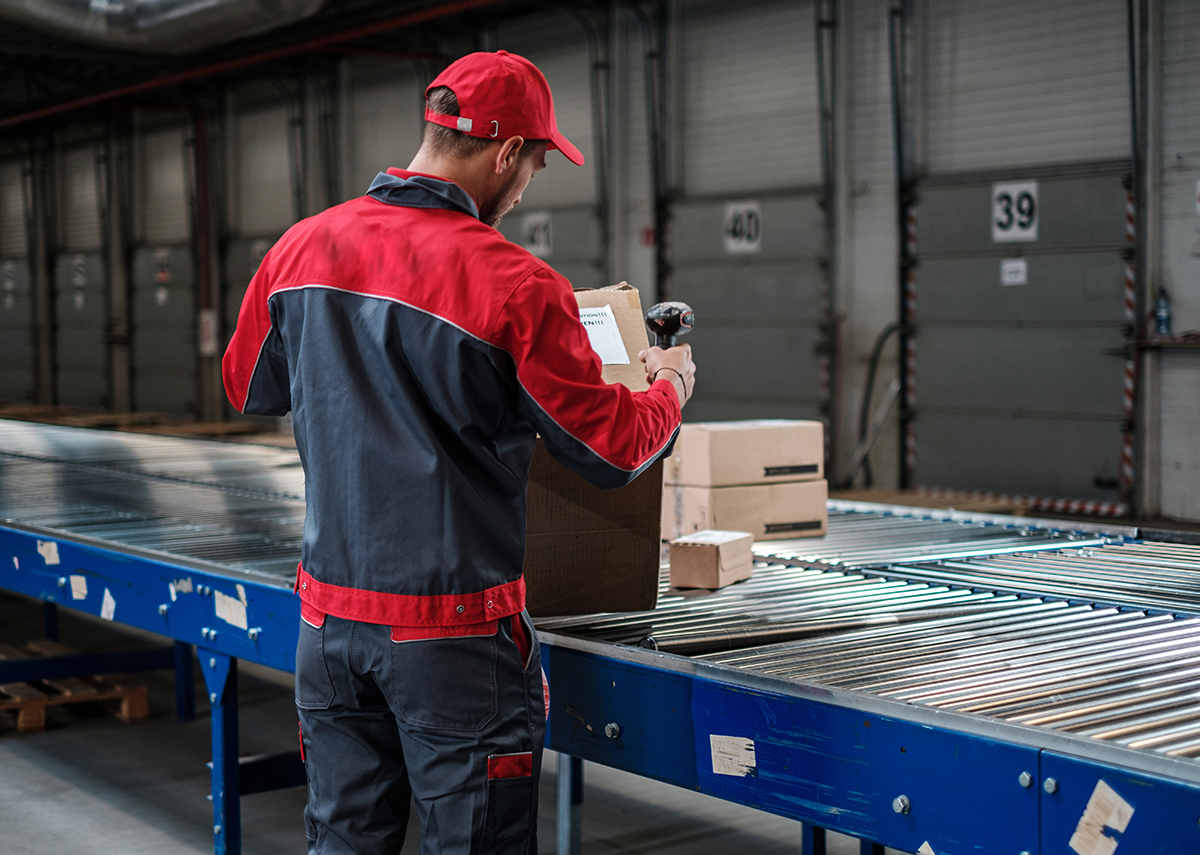
Future of warehouse logistics: AR and IoT with 2D matrix codes on the rise – Image: Nejron Photo|Shutterstock.com
More information in a small space: The advantages of 2D matrix codes for packaging
Real-time transparency in the warehouse: Integration of 2D matrix codes into warehouse management
The new 2D matrix code will undoubtedly bring about a revolutionary change in warehouse picking by significantly improving the efficiency and accuracy of order processing.
Easier and faster data collection
The 2D matrix code enables much faster and more accurate data capture compared to traditional barcodes or QR codes. Thanks to its denser information encoding, more data points can be stored in a single code, significantly reducing acquisition time. This allows warehouse staff to process orders faster and minimize data entry bottlenecks.
Advanced data storage
The 2D matrix codes offer the possibility of storing a variety of information in a small area. In addition to traditional order details such as item number, quantity and delivery address, additional information such as serial numbers, country of origin, expiry dates and more can be accommodated in a single code. This allows for better traceability and quality control in the warehouse.
Reduced error rate
Thanks to the higher data density and precise capture, the 2D matrix code minimizes human input errors and misunderstandings. Warehouse employees no longer have to manually enter long number combinations, but can scan the data directly from the code. This dramatically reduces the risk of errors, resulting in increased accuracy and a lower number of returns and complaints.
Space saving on packaging
The compact nature of 2D matrix code allows companies to fit more information into smaller packaging areas. This allows labels and stickers to be made smaller, which in turn saves costs and resources. The code also enables optimized labeling because it is easy to read even on uneven surfaces.
Better integration with warehouse management systems
Modern 2D code scanners and readers can be seamlessly integrated into warehouse management systems. This enables real-time tracking of orders, inventory and orders. Warehouse managers can access the current status of products and shipments at any time, resulting in improved warehouse visibility and optimized inventory management.
Support for Augmented Reality (AR) and Internet of Things (IoT)
The use of 2D matrix codes opens up new possibilities for innovative technologies such as augmented reality and the Internet of Things. AR-supported picking systems can show warehouse employees the exact location and route to the desired items using smart glasses or mobile devices. IoT sensors can monitor inventory in real time and automatically trigger reorders when certain thresholds are reached.
Higher security and protection against counterfeiting
The 2D matrix codes can be equipped with special security features that protect them against forgery and manipulation. This is particularly important for companies that store and ship high-value or sensitive products. Such security codes may, for example, contain encrypted information that can only be decrypted with special release keys.
Outlook
The use of the new 2D matrix code will fundamentally change warehouse picking. The combination of rapid data capture, expanded data storage, reduced error rates and improved integration with warehouse management systems will result in increased efficiency and productivity in the warehouse. The technology also opens up new opportunities for innovative applications that further optimize warehouse logistics and sustainably support business success.
In a nutshell - Efficient data collection in the warehouse: The advantages of the 2D matrix code
By 2027, the retail industry is planning a global initiative called “Sunrise 2027” to replace the traditional 12-digit barcode consisting of vertical lines printed on packaging with a two-dimensional version that is web-enabled. The effort is being coordinated by GS1, a nonprofit organization responsible for standardizing barcodes worldwide. In the US, the current Universal Product Code (UPC) barcodes are being replaced by a new 2D type that encodes information both horizontally and vertically. The aim of this measure is to only accept 2D barcodes at checkouts worldwide by 2027.
More about it here:
In a nutshell - Efficient data collection in the warehouse: The advantages of the 2D matrix code
Summary:
🚀 The new 2D matrix code brings a revolutionary change in warehouse picking.
💡 The code enables easier and faster data capture compared to traditional barcodes or QR codes.
📚 Thanks to advanced data storage, additional information can be stored in one code.
❌ The error rate is reduced by the precise 2D matrix code, which leads to fewer returns.
🏷️ The compact nature of the code saves space on packaging and allows for optimized labeling.
💻 The 2D matrix code can be seamlessly integrated into warehouse management systems and ensures more transparency.
🔍 Using the code enables innovative technologies such as augmented reality and IoT.
Hashtags: #warehouse picking #2D matrix code #increasing efficiency #innovation #warehouse logistics
Warehouse picking: Efficient order processing for business success
Warehouse picking, also known as order fulfillment or warehouse selection, is a critical process in warehousing that directly impacts the efficiency of supply chain operations. Items are selected and removed from inventory to fulfill customer orders accurately and quickly. In this article, we will look at the essential aspects of warehouse picking, examine various methods used in this process, and discuss strategies to increase efficiency.
The importance of efficient warehouse picking
Efficient warehouse picking is important for several reasons:
- Customer satisfaction: Timely and error-free order processing leads to higher customer satisfaction, promotes brand loyalty and positive reviews.
- Operational efficiency: A well-organized picking process optimizes processes, reduces throughput times and increases overall efficiency.
- Cost Optimization: Efficient warehouse picking helps minimize labor and storage costs by using resources effectively.
- Competitive advantage: Fast and error-free order processing differentiates companies from competitors and attracts more customers.
Common warehouse picking methods
Different picking methods are used in warehouses, each to suit specific business needs. Some of the most common methods are:
- Piece picking: This method involves selecting individual items one at a time to fulfill orders. It is suitable for small businesses or when the order consists of unique items.
- Collective picking: Collective picking involves selecting several orders at the same time in one pass. The order picker consolidates items for multiple orders into one cart or bin, increasing productivity.
- Zone picking: The warehouse is divided into zones and each picker is only responsible for picking items in their assigned zone. Once all zones are completed, items will be merged to complete jobs.
- Wave picking: Wave picking combines elements of collection and zone picking. Orders are grouped into waves based on their characteristics, and multiple pickers work synchronously to fulfill the waves.
Strategies to increase efficiency in warehouse picking
To achieve optimal warehouse picking efficiency, companies can implement the following strategies:
- ABC Analysis: Prioritize items based on their frequency of demand. High-demand items should be placed in easily accessible locations to allow for quick pickup.
- Optimal storage: Design the warehouse layout in such a way that the order pickers' walking distances are minimized and traffic jams in heavily frequented areas are avoided.
- Warehouse Management System (WMS): Implement a WMS with advanced picking algorithms to optimize routes and intelligently prioritize orders.
- Automated Guide Vehicles (AGVs): Introducing AGVs to transport carts or containers between picking areas and reduce manual material movements.
- Voice-based picking and RF scanning: Equip pickers with voice-based picking systems or RF scanners to enable hands-free, precise and efficient picking.
- Ongoing training: Train pickers regularly to improve their skills, reduce errors and ensure a safe work environment.
Outlook
Warehouse picking is a crucial function in warehouse operations. Their efficiency directly impacts customer satisfaction, operational costs and overall competitiveness. By applying appropriate picking methods and implementing efficient strategies, companies can optimize order fulfillment, increase productivity and gain a competitive advantage in a fast-moving market.
Xpert.Plus warehouse optimization - high-bay warehouses such as pallet warehouses consulting and planning
Xpert.plus-logistics advice and logistics optimization-industry expert, here with its own 'Xpert.digital Industrie-Hub' of over 1,000 specialist contributions
Xpert.Plus is a project from Xpert.Digital. We have many years of experience in supporting and advising on storage solutions and in warehouse optimization, which we bundle in a large network under Xpert.Plus.
I would be happy to serve as your personal advisor.
You can contact me by filling out the contact form below or simply call me on +49 89 89 674 804 (Munich) .
I'm looking forward to our joint project.
Xpert.Digital – Konrad Wolfenstein
Xpert.Digital is a hub for industry with a focus on digitalization, mechanical engineering, logistics/intralogistics and photovoltaics.
With our 360° business development solution, we support well-known companies from new business to after sales.
Market intelligence, smarketing, marketing automation, content development, PR, mail campaigns, personalized social media and lead nurturing are part of our digital tools.
You can find out more at: www.xpert.digital – www.xpert.solar – www.xpert.plus