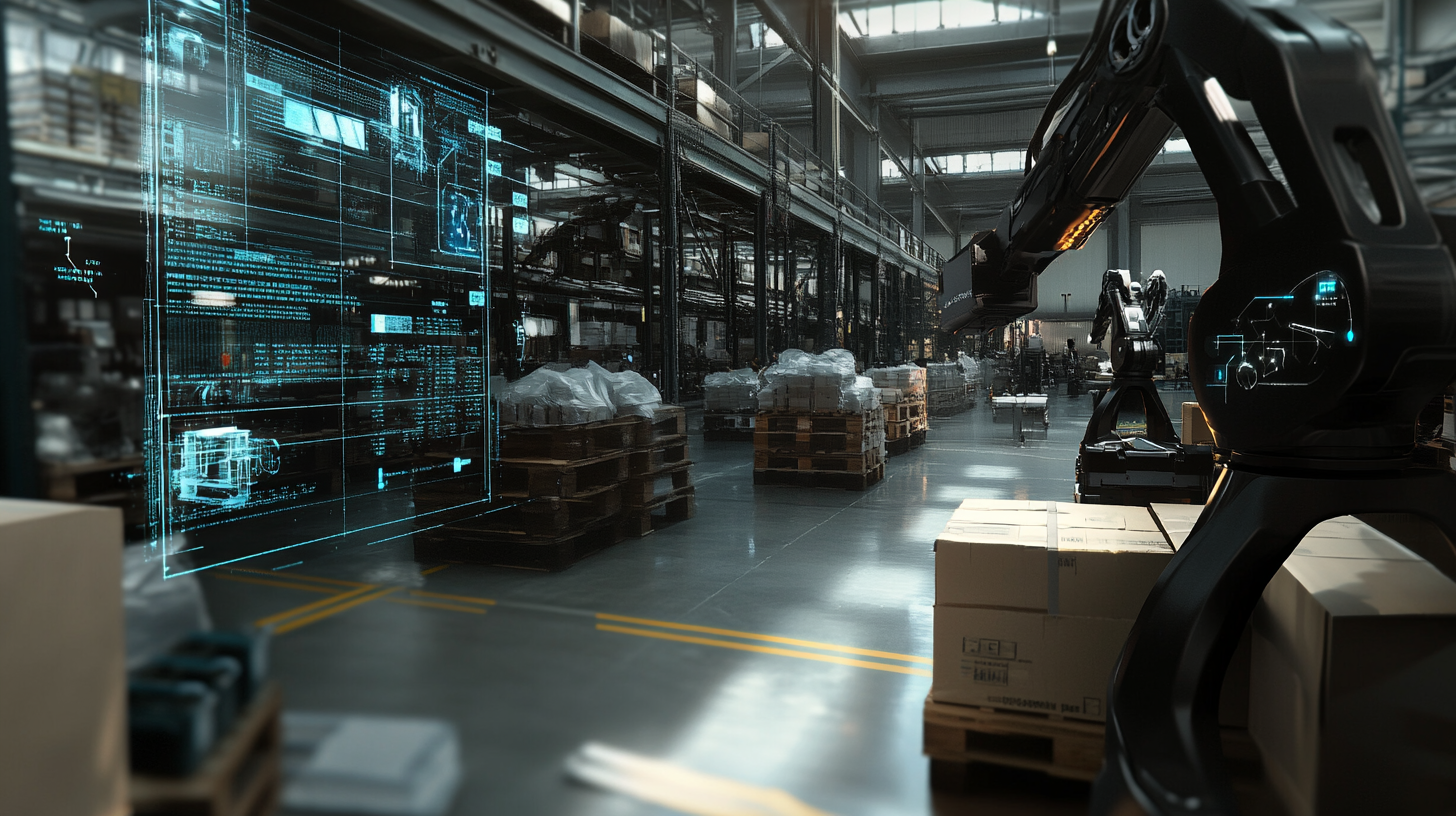
Innovative storage strategies – Focus on efficient placement of goods: Reduce costs, increase performance – Image: Xpert.Digital
The Art of Inventory Placement: Increase Efficiency, Reduce Costs
Efficient placement of goods in the warehouse: Optimization through digital twins and artificial intelligence
The efficient placement of goods in the warehouse is a crucial factor for a company's performance and cost control. A well-organized warehouse contributes significantly to reducing throughput times, minimizing error rates and improving overall efficiency. The challenge, however, is to place the goods in such a way that the processes for storage and retrieval as well as picking are optimally supported. This requires not only experience and intuition, but above all a data-supported approach that can flexibly adapt to changing order and demand structures.
In the age of digitalization, new technologies such as artificial intelligence (AI) and digital twins have the potential to dramatically increase efficiency and accuracy in warehouse management. The intelligent application of such technologies allows warehouse managers to optimize the placement of goods dynamically and based on real-time data. The following sections explain which factors need to be taken into account when placing the goods, what role warehouse management software plays and how digital twins and AI support this process.
Criteria for the optimal placement of the goods
The placement of goods in the warehouse is based on a variety of criteria that are primarily based on demand orientation and product characteristics. The most important factors include:
1. Rotation of goods (ABC analysis)
Many warehouses use ABC analysis to classify products according to their demand frequency. Items that are in high demand (A items) are placed in easily accessible areas, while lower demand items (C items) are stored in more distant or difficult to access areas. This arrangement reduces walking distances and speeds up picking.
2. Product type and handling characteristics
Heavier or bulky goods require special storage spaces and often machine support for transport. Hazardous substances must be stored in accordance with legal requirements, which requires a special arrangement in the warehouse. Temperature-sensitive goods such as food or medication also require special storage areas.
3. Seasonal fluctuations and current demand
Demand for certain products may be subject to seasonal fluctuations. For example, demand for certain goods increases during the Christmas months. A flexible storage strategy that anticipates such fluctuations is essential for the placement of goods.
4. Cross-docking potential
Products that need to be forwarded as quickly as possible without remaining in the warehouse for a longer period of time are positioned in the so-called cross-docking area. These products pass through the warehouse without extensive storage and are prepared directly for shipping.
Warehouse management software as the basis for an optimized warehouse structure
In order to manage the criteria mentioned efficiently, the use of warehouse management software is essential. This software analyzes inventories, records the movements of goods in the warehouse and highlights potential bottlenecks or excess storage capacity. Modern systems offer real-time monitoring of storage locations and often integrate into a higher-level ERP (Enterprise Resource Planning) system. Automatic data capture significantly reduces the risk of errors and the warehouse manager receives reliable information about the current inventory situation.
Warehouse management software also supports slotting, i.e. the management of storage positions in the warehouse. With slotting, storage spaces are allocated according to business aspects in order to maximize the efficiency of the warehouse processes. This includes, among other things, the allocation of storage spaces based on expected demand, product volume and packaging effort. Such data-based slotting allows routes to be shortened, picking to be accelerated and costs to be reduced.
Digitalization and automation: The role of AI and digital twins
With the introduction of artificial intelligence and digital twins, warehouse management goes far beyond the functionality of traditional warehouse management software. These technologies create the ability to simulate future scenarios, analyze inventory in real time and make dynamic decisions about product placement.
Digital twins as a reflection of reality
A digital twin is a virtual image of the real warehouse that is constantly synchronized with current data. This digital copy allows the bearing to be analyzed and tested in a secure, virtual environment. In this way, the movement of goods can be simulated, bottlenecks in the warehouse can be identified and the placement of products can be optimized. This takes place in real time, so that changes in demand or special events (e.g. delivery bottlenecks or conveyor system failures) can be responded to at any time.
A digital twin offers the great advantage of allowing warehouse managers and planners to run through different scenarios before making changes to the physical warehouse environment. “What if” scenarios allow you to analyze how the placement of goods affects the efficiency of picking and whether alternative routes could lead to better utilization. This can be particularly helpful when inventory changes rapidly or demand for certain items skyrockets.
Artificial intelligence as a decision-making tool
Artificial intelligence is used in particular to analyze large amounts of data generated in the warehouse. Algorithms are used to process goods movements, inventory data and historical sales data to create forecasts and automate decisions. For example, a smart warehouse management system could recognize that a particular product will be in increased demand in the next few days and adjust storage locations to place those items in close proximity to the shipping station.
AI-based systems can also learn from past data and make precise predictions for the future. These predictions are based on patterns that are often not visible to the human observer. The AI can not only optimize the existing warehouse structure, but also take seasonal fluctuations and special promotions into account in advance. For example, the system can recognize that products that are often ordered together should be stored in close proximity to each other to reduce picking effort.
Advantages and challenges of digital transformation in the warehouse
Integrating AI and digital twins into warehouse management offers a variety of benefits:
Increasing efficiency
Through the precise analysis of goods movements and the dynamic adjustment of storage locations, distances can be shortened and employee productivity increased.
Reduction of errors
Automating decision-making processes and real-time monitoring minimizes errors that could occur when placing goods manually.
flexibility
Digital twins and AI enable the warehouse structure to be flexibly adapted to changing market requirements and seasonal fluctuations in demand.
Cost savings
Accelerated picking and optimized use of space reduce operational costs and lead to more efficient use of resources.
However, there are also challenges that come with the introduction of these technologies. One of the biggest hurdles is the implementation and handling of the new systems, which require specialist knowledge and require adjustments to work processes. In addition, investing in AI and simulation technologies represents a financial burden for some companies that only pays off over a longer period of time.
Efficient warehouse management through innovative technologies
The efficient placement of goods in the warehouse is a dynamic process that can be significantly improved through the use of modern technologies. Digital twins and artificial intelligence offer the opportunity to establish a flexible, data-based and, above all, efficient warehouse structure that adapts to current requirements and market developments.
With the further development of AI and the increasing possibilities of digitalization, the potential of these technologies in warehouse logistics will continue to increase. Companies that invest in these technologies will benefit in the long term from faster and less error-prone inventory management.
Suitable for: