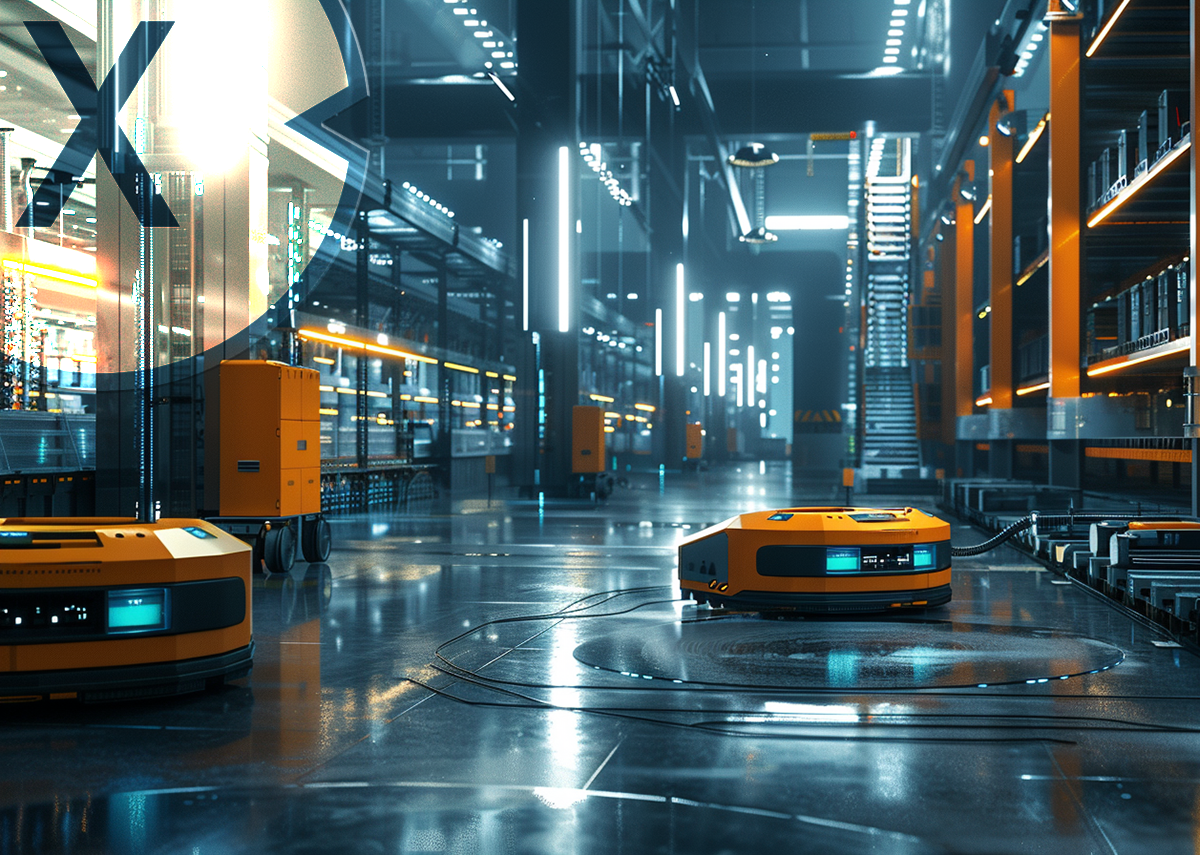
The advanced professionalization (Hyper Logistics) of storage in the cold chain industry – Image: Xpert.Digital
🏭 The role of AS/RS and STV in the cold chain industry
📦 A recurring theme in cold storage storage revolves around effectively accommodating an ever-growing range of goods in a limited space. The variety of frozen food SKUs and the trend toward smaller orders exacerbate the challenge of managing the required volumes using traditional fixed warehouse racks and floor storage methods.
🧊 When we talk about food SKUs, we are referring to the specific storage units of food. Each different type of food product, including different brands, packaging sizes and varieties, has its own SKU. For example, a package of frozen pizza of a certain brand, size, and variety has a unique SKU that distinguishes it from other products.
📊 The SKU stands for “Stock Keeping Unit” - in German: storage unit. A SKU is a clear identifier that is used to identify a specific article in the inventory of a company. This identifier helps to manage and persecute stocks in the warehouse.
🥶 The term “food sku” or food skating is particularly relevant in the food industry and cold chain logistics, since these areas handle a wide variety of products that all have to be followed individually and managed. Effective management of skus is crucial for precise inventory management, efficient storage and fast order processing.
💡 In summary, a SKU is simply a specific identifier for an individual food product within an inventory system, used for precise management and tracking.
🌍 As we have recently seen across the industry globally, building supply chain resilience has become a key concern, further motivating retailers to protect against infrastructure and environmental risks.
🤖 In the ever-evolving landscape of industrial technology, the cold chain industry is a great example of adaptation and innovation. With the ever-increasing demand for efficiency, speed and precision, warehouse automation has emerged as a transformative solution. Among the numerous automation tools, automated storage and retrieval systems (AS/RS) and sortation transport vehicles (STV) have played a key role in revolutionizing the storage processes in the cold chain industry.
🧩 Unique challenges and opportunities
🍦 The cold chain industry covers a wide range of products, including perishable goods such as dairy products, frozen foods and fresh fruits and vegetables. Unlike traditional warehouses, refrigerated food storage requires precise temperature control, strict inventory management and rapid order fulfillment to ensure product quality and safety standards.
🔄 Cold storage facilities that serve supermarkets and restaurant chains have high mix, small batches, and fast inventory turnaround times. Critical to this process is the management of goods based on expiry dates, best before dates and delivery information – a continuous flow of pallet storage, removal and picking based on specifications.
🚀 Traditionally, cold storage warehouses relied heavily on manual labor for tasks such as picking, packing and inventory management. However, this approach often resulted in inefficiencies, higher labor costs, and a higher risk of errors. With the advent of automation technologies, the industry has witnessed a transformation towards more optimized and efficient operations.
📦🤖 AS/RS and STV: Efficiency in warehouse logistics
AS/RS and STV are abbreviations used in the field of warehouse logistics and automation. AS/RS and STV enable highly automated and efficient warehouse logistics that meet the requirements of modern supply chain management processes. Here is a brief explanation of both terms:
1. AS/RS (Automated Storage and Retrieval System)
AS/RS, or Automated Storage and Retrieval System in German, refers to an automated system for storing and collecting goods. These systems use various technologies such as storage and retrieval machines, robots, conveyors and software to manage inventory. They improve the efficiency, accuracy and speed of warehouse processes and reduce space requirements and labor costs. AS/RS systems find application in various industries including manufacturing, retail and distribution.
Suitable for:
2. STV (Shuttle Transport Vehicle)
STV, or Shuttle Transport Vehicle, is an automated guided vehicle system used in automated warehouses. These vehicles move within a warehouse system to transport goods between different storage locations, work stations or storage and retrieval points. Shuttle systems are particularly efficient in handling small to medium quantities of items and can be used in multi-story storage structures. They help reduce storage cycle times and increase overall storage capacity.
Suitable for:
- Top Ten Vertical & Horizontal AGVs (Automated Guided Vehicles) & Robot Shuttle Systems
- Automatic pallet shuttle system (PSS) for fully automatic pallet warehouse shuttle rack storage system (SRL)
- Storage solutions: Scalable shuttle technology in the storage technology of standard pallets and half-pallets in high-bay warehouses
📌 Other suitable topics
📦❄️ Aryzta: Leading the transformation of the frozen bakery industry through intelligent packaging solutions in frozen logistics
Ice-cold innovation: Aryzta's contribution to smart frozen logistics and sustainability in the baked goods industry - Image: Smurfit Kappa Deutschland GmbH
The Aryzta company has established itself as a leading manufacturer of frozen baked goods in Europe and is moving forward with innovative concepts to overcome the industry's challenges in the areas of logistics, environmental protection and cost efficiency. One of its most recent achievements in this area is the implementation of an advanced packaging solution that enables a significant reduction in CO2 emissions while realizing significant financial savings.
More about it here:
Xpert partner in warehouse planning and construction
🌟AS/RS: Maximize efficiency and use of space
🧤 AS/RS are the foundation of warehouse automation, providing unparalleled efficiency in storage and picking operations. These systems use a combination of storage racks, automated shuttles and cranes to store and retrieve goods precisely and quickly, focusing on high volume and storage efficiency.
🚨 In the context of the cold chain industry, AS/RS offers several key advantages
1. Temperature control
AS/RS are designed to work seamlessly in refrigerated environments, preserving temperature-sensitive goods throughout the storage and retrieval process.
2. Optimized use of space
By effectively utilizing vertical space, AS/RS enable cold chain warehouses to maximize storage capacity without expanding their physical footprint. This is particularly important in urban areas where space is limited and land costs are high.
3. Improved inventory management
AS/RS are equipped with advanced inventory tracking and management capabilities that enable warehouse managers to monitor inventory in real-time and optimize inventory rotation to minimize waste.
4. Increased throughput performance
With automated picking processes, AS/RS reduce the time it takes to fulfill orders, improving overall throughput and customer satisfaction.
🚗 Sorting transfer vehicles (STV): Navigating the cold storage area
In addition to AS/RS, sorting-transfer vehicles (STV), a rail-guided transportation system, play an important role in improving the efficiency and flexibility of cold chain warehouse operations. STVs are capable of moving goods between warehouse racks and picking stations with minimal human intervention.
🌐 How STVs are transforming chilled food storage
1. Dynamic memory access
STVs seamlessly transport goods to and from an AS/RS. The system can autonomously navigate narrow aisles and confined spaces to deliver pallets to drop points from where the AS/RS can retrieve them for storage. This flexibility allows for faster pick times and smoother workflow coordination.
2. Collaboration in operations
STVs can work in collaboration with human operators and other automated equipment such as robotic arms and conveyor systems to optimize the entire order fulfillment process. This collaborative approach optimizes resource utilization and minimizes bottlenecks.
3. Improved work environments
By bringing goods to operators, picking tasks can be carried out in well-lit, safe and comfortable temperatures. This increases employee well-being and satisfaction as well as safer and more productive processes.
4. Scalability and modularity
STVs are inherently scalable, allowing cold chain warehouses to gradually expand their automation capabilities as demand increases. This modular approach to automation ensures investments remain flexible and in line with evolving business needs.
🚀 Usher in a new era of efficiency and reliability
The integration of AS/RS and STV represents a paradigm shift in how cold storage facilities operate. By harnessing the power of automation, these technologies enable warehouses to achieve unprecedented levels of efficiency, accuracy and reliability.
As the cold chain industry continues to evolve and respond to changing consumer demands and market dynamics, the adoption of warehouse automation will undoubtedly play a critical role in driving growth and competitiveness. By adopting AS/RS and STV, cold chain manufacturers and distributors can be at the forefront of innovation, delivering fresher products faster and more efficiently than ever before.
Our global intralogistics partner and expert has been offering logistics systems for refrigerated environments to a wide range of customers since 1973. Talk to us and our specialists about how we can help you transform your processes.
📣 Similar topics
- 🌡️ The evolution of cold chain logistics since the mid-20th century
- 🛠️ Technological Revolutions in Cold Storage: An Overview
- 🏷️ Grocery SKUs: The Art of Cold Chain Inventory Management
- 🌍 Global trade and the importance of robust supply chains
- 🔄 Building resilience in the cold chain industry against infrastructure risks
- 🤖 Automated storage and retrieval systems (AS/RS) in cold chain management
- 🚚 The role of sorting transfer vehicles (STV) in modern cold storage
- 🍦 Specific requirements for the storage of perishable goods
- 📈 Increasing the efficiency of warehouse processes through automation
- 🌟 The future of the cold chain industry: efficiency and reliability through technology
#️⃣ Hashtags: #Cold Chain Logistics #FoodSKU #Warehouse Automation #ASRSandSTV #TechnologicalInnovations
🌡️🚚 Professionalization in cold chain logistics 🌍
📈 Professionalization in cold chain logistics as we know it today has developed over several decades. While basic forms of cold chains and refrigerated transport began in the 19th century, modern professionalization in cold chain logistics essentially took shape in the second half of the 20th century, particularly through technological innovations and the increasing importance of global supply chains. Here are some key dates and developments:
🌨️ 1. Beginnings of refrigerated logistics in the 19th century
Ice began to be used to cool food, especially for transporting meat, as early as the 19th century. The invention of mechanical refrigeration in the late 1800s marked the start of serious cold chain solutions.
📈 2nd boom in the middle of the 20th century
1940s and 1950s
The widespread adoption of mechanical cold storage warehouses and refrigerated trucks led to a significant improvement in the storage and transportation of perishable goods.
1960s to 1980s
Technological improvements and increased demand for chilled and frozen foods continued to drive development. Supermarkets and expanding international trade increasingly required efficient and reliable cold chains.
📈 3. Increasing professionalization since the 1970s
1970s
Companies like Daifuku began to develop specialized logistics systems for refrigerated environments, which significantly improved efficiency and reliability in refrigerated logistics.
Global logistics also became more professional with the introduction of the barcode in 1973
Related here:
Automation and digitalization
With the introduction of computerized warehouse management systems, automation technologies such as AS/RS and cold chain management software over the last three decades, professionalization has been taken to a new level.
📡 4. In the 21st century
- The integration of real-time temperature monitoring, global positioning systems (GPS) and Internet of Things (IoT) technologies has made it possible to make cold chain logistics even more precise and reliable.
- Sustainability initiatives and stricter regulatory requirements have also contributed to professionalization by promoting more transparent and environmentally friendly practices in cold chain logistics.
Welcome to Hyper Logistics with the 2D matrix code, which will replace the barcode worldwide in 2027!
More about it here:
- Important information for logistics: Sunrise 2027, the Data Matrix code (2D barcode) or QR code will replace the barcode
- Conversion, conversion and upgrading of cash register systems to the 2D code: Matrix code for supermarkets, manufacturers and packaging
- Sensor technology and industrial sensors convert to 2D matrix code: The conversion of sensors and scanners with parallel barcode/barcode support
Xpert.Plus warehouse optimization - high-bay warehouses such as pallet warehouses consulting and planning
We are there for you - advice - planning - implementation - project management
☑️ Smart City & Factory: Industry expert for energetic 5G buildings and halls as well as advice and installation of solar systems
☑️ Xpert.Plus - logistics consulting and logistics optimization
☑️ Industry expert, here with his own Xpert.Digital Industry Hub with over 2,500 specialist articles
I would be happy to serve as your personal advisor.
You can contact me by filling out the contact form below or simply call me on +49 89 89 674 804 (Munich) .
I'm looking forward to our joint project.
Xpert.Digital - Konrad Wolfenstein
Xpert.Digital is a hub for industry with a focus on digitalization, mechanical engineering, logistics/intralogistics and photovoltaics.
With our 360° business development solution, we support well-known companies from new business to after sales.
Market intelligence, smarketing, marketing automation, content development, PR, mail campaigns, personalized social media and lead nurturing are part of our digital tools.
You can find out more at: www.xpert.digital - www.xpert.solar - www.xpert.plus