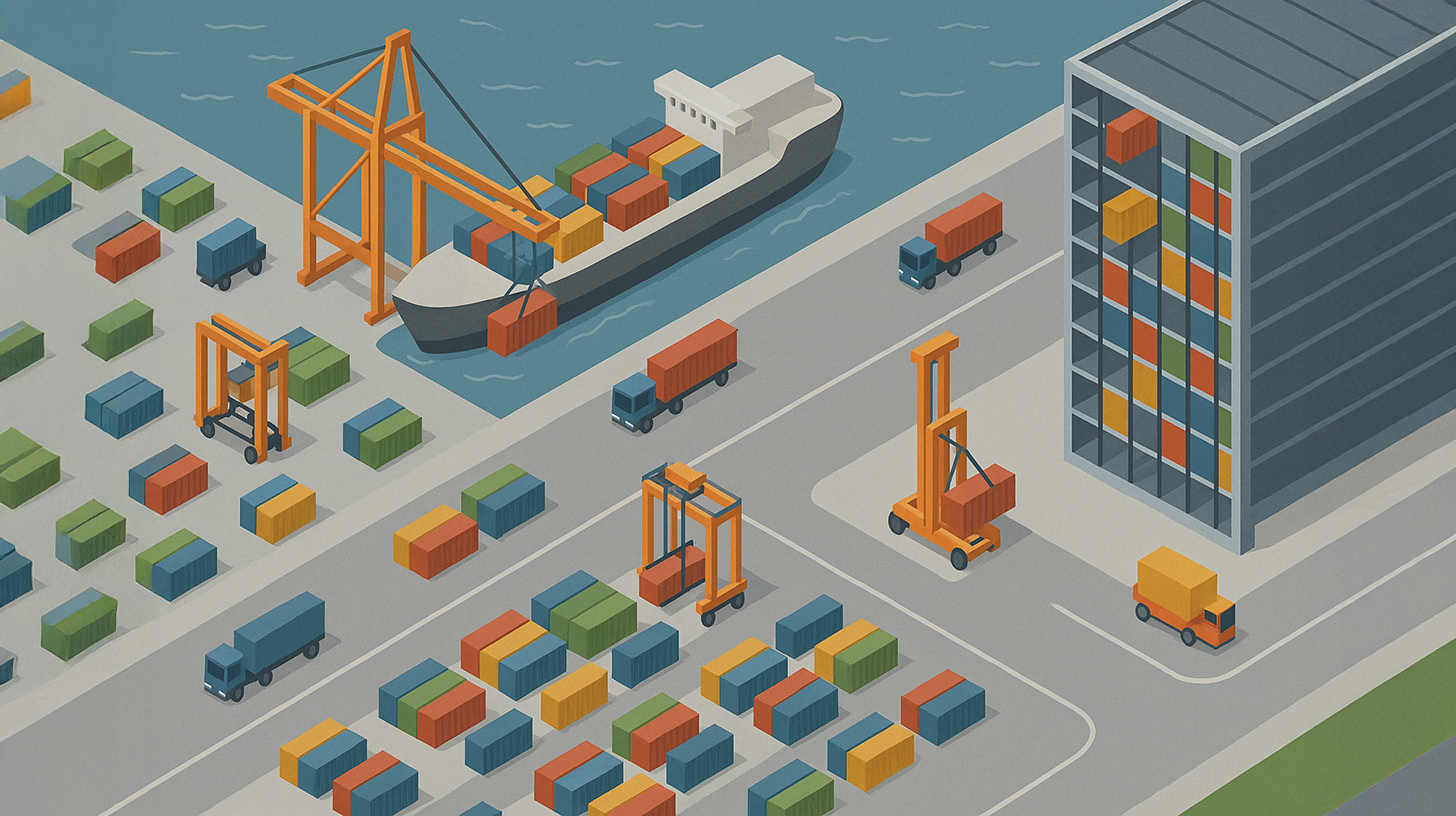
Development of the container terminals: From container yards to fully automated vertical container high-beam bearings – Image: Xpert.digital
Space as a strategy: the reinvention of global container logistics
Lace miracle of logistics: intelligent storage systems change world trade
Further development of the container terminals from container yards (container parking space), to space-optimized, fully automated and AI-supported vertical container high-beam bearings of the KV terminal (combined traffic from street, rail and seafaring) of global freight transport.
The turning point of global logistics – when the room becomes a strategic resource
The global logistics network, the backbone of modern world trade, groans under the burden of his own success. An unstoppable growth of the commercial volume, paired with a dramatic increase in ship sizes – in particular the Ultra Large Container Ships (ULCS), which can transport up to 24,000 TEU (Twenty-Foot Equivalent Unit) – brought the traditional model of the container terminal to its absolute physical and operational limits. At the interfaces of the global flows of goods, in the ports, a crisis manifests itself that threatens to paralyze the entire supply chain.
This development has disclosed a central conflict of goals of modern port logistics: the insoluble paradox between the need for ever higher storage density on tight, expensive areas and the resulting catastrophic loss of operational efficiency in conventional systems. The container terminal, once a pure transit point, has become a critical bottle neck, which dictates the pace of the entire global supply chain. The further development of extensive container parking areas, the so-called container yards, towards space-optimized, fully automated and AI-supported vertical container high-beam bearings is therefore not a mere technological upgrade. Rather, it is a necessary, paradigm -changing response to a systemic crisis that forces a fundamental redefinition of the functioning of transshipment terminals in combined traffic (KV) from street, rail and seafaring.
Suitable for:
- The top ten of the container high-class bearing manufacturers and guidelines: technology, manufacturer and future of port logistics
The age of borders – traditional container terminals on the scabbard
Anatomy of a conventional container terminal: an ecosystem under pressure
In order to understand the scope of the upcoming revolution, a look at the anatomy and the functioning of a traditional container terminal is essential. Such a terminal is a complex ecosystem that consists of several clearly defined physical components and operational zones. At the forefront is the Kaianlage with the berths (Berths), on which the huge container ships capture. Here the mighty Ship-to-Shore (STS) cranes, the interpreters of which extend over the entire width of the ships to load and extinguish containers. However, the heart of the terminal is the extensive container yard (CY), a huge, fortified area that serves as a temporary buffer camp for thousands of full and empty containers. A fleet of specialized handling and transport equipment operates within this yard. These include rubber-tires portal cranes (Rubber-Tired Gantry Cranes, RTGS), rail-bound portal cranes (Rail-Mounted Gantry Cranes, RMGS), Portal lugs (Straddle Carrier) and gripping stacker (REACH Stackers), which are responsible for stacking and transporting the containers within the yards. The third essential element is the gate complex, the needle tube for the country's traffic, on which trucks are handled, container is registered and security controls are carried out. This is often supplemented by a railway system for further transportation into the hinterland. The yard operations include the storage, organization and provision of the containers. The gate and rail operations ensure the seamless connection to the landing modes. In theory, this is a flowing process. In practice, however, the sheer mass of containers, which is deleted by a single ulcer, brought this system to the edge of the collapse.
The vicious circle of inefficiency: the paradigm of the block stacking
The Achilles' heel of each conventional container terminal lies in its fundamental design philosophy: stacking of blocks. Regardless of whether a terminal uses a linear or a block layout, the principle is based on stacking containers directly on top of each other in order to take advantage of the limited area. What seems logical at first glance is in truth the source of profound and systemic inefficiency. The core problem is the so-called “unproductive surrounding processes”, also known as “reshuffling” or “shuffle moves”. In order to access a container that is located on the bottom of a stack, all containers above it must first be raised and stored elsewhere. Only then can the target container be removed, whereupon the intermediate containers often have to be moved again. Analyzes show that these unproductive movements that do not create time or value make up between 30 % and 60 % of all crane movements in a conventional yard. In the worst case, this means that more than half of the entire crane activity of pure waste serves. This fact creates a vicious circle: In order to increase capacity in a limited space, the terminal operators are forced to stack the containers higher. But with every additional level, the likelihood and complexity of surrounding processes increases exponentially. From a filling rate of 70-80 %, the performance of a warding block breaks down dramatically. The result is unpredictable termination times, massive traffic jams within the terminal and an operational performance that can no longer be planned. The size advantages of the megails at sea are destroyed by massive inefficiencies on land.
The imperative of the combined traffic (KV): When the bottle neck paralyzes the chain
These inefficiencies are fatal for the terminals of combined traffic (KV), which act as a critical interface between the ship, railway and truck. The performance of the entire intermodal network depends on the efficiency and reliability of these cover points. A conventional terminal, which is plagued by unplannable surrounding processes and internal traffic jams, acts like a brake for the entire logistics chain. Long and unpredictable waiting times for trucks at the gates and for freight trains on the rail terminals are the direct episode. A late container can delay the departure of an entire freight train, which in turn confuses timetables throughout the rail network and endangers connection connections. The economic and ecological advantages of combined traffic – the bundling of transports and the relocation from the road to rail – are undermined by the bottle neck in the harbor. The unpredictability of the terminal plants through the entire supply chain and makes reliable just-in-time logistics almost impossible. It becomes clear that the inefficiency of traditional terminals is not a management problem, but a systemic error that roots in its physical architecture. This once adequate model has become obsolete due to the scaling and speed of modern global trade and made the terminals the main source of friction and unpredictability in the supply chains.
The vertical revolution – the high -bay warehouse as a new paradigm
From horizontal expansion to vertical density: the HRL concept
In response to the systemic crisis of conventional terminals, a radical new approach is created: The fully automated container high-base warehouse (HRL), known internationally as High-Bay Storage (HBS). Instead of further expanding horizontally, which is geographically impossible and ecologically questionable in most port cities, the HRL concept shifts storage into the vertical. It is a strategy that fundamentally changes the equation of the use of land. This concept is not a pure fiction, but is based on proven and robust technology that comes from an unexpected sector: the heavy industry. Leading providers such as the Deutsche SMS Group have decades of experience with fully automated high-bay bearings for extremely heavy loads, such as 50 tons of steel coils, which are reliably handled under rough industrial conditions in 24/7 operation. The adaptation of this tried and tested technology for container logistics significantly reduces the perceived risk for port operators and gives the leap in the innovation a solid industrial basis.
Suitable for:
Deconstruction of the technology: The principle of direct individual access
An HRL is much more than just a high shelf. It is a highly complex, fully automated system, the genius of which is on a single principle: direct individual access to each individual container. This principle is made possible by two core components. At most, the steel rack structure: a massive steel structure that can be up to eleven containers high forms the skeleton of the warehouse. Each container is placed in its own, individually addressable shelf. A crucial detail is that these shelves do not need continuous floors. The standardized ISO containers are self-supporting and are only held on their four corner fittings (Twistlocks). This reduces the use of materials, the total weight and the construction costs significantly without affecting the statics. Secondly, the automated shelf control devices (RBG), also called stacker cranes: these rail -guided, high -speed cranes move autonomously through the corridors between the shelf rows. They are equipped with adjustable gripping arms (spreader), which are precisely locked on the containers. Deleted from a central control system, an RBG can directly control and remove any container in the warehouse – without having to move a single other container. Here is the revolutionary core of the technology. The direct individual access eliminates unproductive surrounding processes. Every movement of a crane is a productive movement. The fundamental target conflict between storage density and access efficiency, which paralyzes traditional terminals, is dissolved. The true revolution of the HRL is therefore not the verticality itself, but the change from a warehouse -centered (stacked) to access -centered (shelf) philosophy. The warehouse turns from a sluggish department store into a highly dynamic sorting and buffer node.
Case study: The Boxbay system as “proof of feasibility”
The technological feasibility and performance of this concept are no longer a theory. The joint venture boxbay, a cooperation between the global terminal operator DP World and the German plant manufacturer SMS Group, has provided the impressive “feasibility detection” with its pilot project in the port of Jebel Ali in Dubai. By the end of 2024, over 330,000 container movements were successfully carried out. The results exceeded the expectations: the cover performance reached 19.3 movements per hour at the interface to the quay and impressive 31.8 movements per hour on the land-side truck cranes. These figures show that the system not only works, but also enables unmatched performance and predictability. The next crucial step has already been taken: in March 2023 the first commercial order for “retrofitting” implementation in the port of Pusan, South Korea, was signed. There the Boxbay system is retrofitted in an existing, state-of-the-art terminal. The goal: the elimination of 350,000 unproductive surrounding processes per year and a reduction in truck handling times by 20 %. The success of this project will be a litmus test for the ability of the technology to modernize the existing infrastructure of the world ports and is followed by the entire industry with the greatest attention.
Digital nervous systems: the container terminal of the future between high-tech and efficiency
The engines of change – automation, robotics and digitization
The automated terminal: from partial to fully automation
Automation in container terminals is not binary condition, but a spectrum with different maturity degrees. Most of the terminals known as “automated” today fall into the category of partial automation. Here, the storage process in the yard is typically automated by using automated stacking cranes (automated stacking cranes, ASCS), while the horizontal transport between KAI and warehouse block continues to take place with manually served. Instead of truck drivers, driverless transport systems (automated guided vehicles, AGVs) or automated lifting vehicles (Automated Lifting Vehicles, ALVS) take over the transfer of the containers. Despite the enormous interest in these technologies, only about 3-4 % of all container terminals worldwide are partially or fully automated. This clarifies that the hurdles for the introduction are high. The concept of the high -bay bearing represents the highest and deepest integrated level of automation, when storing and handling merge into a single, closed robotic system.
Suitable for:
- The simple and evolutionary-grown idea of the container base camp: a paradigm shift in global logistics
The digital nervous system: IoT and the “intelligent harbor”
A digital nervous system requires that a highly automated system can function as a HRL as a coherent whole, a digital nervous system. The Internet of Things, IoT) takes on this role. A densely network of sensors on cranes, vehicles, the infrastructure and even on the containers themselves are digitally mapped in real time. First, real-time transparency: the operators know every second where every container and every device is located and in what condition it is. Second, the condition monitoring and predictive maintenance (Condition Monitoring & Predictive Mainness): Sensors on critical components such as engines or storage continuously measure data such as vibrations, temperature and pressure. Algorithms analyze these data flows and can predict potential failures before entering. This enables a change from an expensive, reactive repair culture to a proactive, planned maintenance, which drastically reduces downtime and can reduce the maintenance costs by up to 50-75 %. Third, the creation of digital twins: virtual 1: 1 images of the physical harbor can be created from the IoT data. In these simulations, new processes, layouts or emergency scenarios can be tested and optimized in risk -free and optimized before they are implemented in the real world.
The intelligent core: AI-based optimization and control
If the IoT is the nervous system, then artificial intelligence (AI) and machine learning (ML) are the brain of modern terminal. The sheer quantity and speed of the data generated by the IoT sensors can no longer be processed effectively by human dispatchers. Here, AI systems are used that are integrated into the central terminal operating system (TOS) – software platform for controlling all processes –
Optimized decision-making: AI algorithms make complex decisions in a fractions of seconds. You determine the optimal storage space for every incoming container taking into account factors such as weight, destination and collection time. They plan the most efficient movement sequence for the cranes and calculate the ideal routes for the AGVs to avoid traffic jams and minimize empties.
Foresighting analysis (Predictive Analytics): By analyzing historical and current data, AI can predict the arrival times of ships more precisely, predict impending bottlenecks in yard and anticipate the future need for personnel and devices. This enables proactive instead of reactive resource planning.
Resource management: The AI optimizes the assignment of berths, cranes and vehicles to maximize the overall throughput and minimize waiting times for ships and trucks. Early users of AI in logistics report significant successes, such as reducing logistics costs by 15 % and an increase in service efficiency by 65 %.
It becomes clear that the physical robotics and digital intelligence are inextricably linked. The rigid, highly complex structure of an HRL is only manageable by a highly developed AI. Conversely, the optimization potential of the AI can only be fully exploited in a fully automated, data -rich environment. This creates a positive feedback loop: better data enable more intelligent AI, which in turn controls more efficient physical processes. The often cited observation that automated ports are sometimes even less productive than manual finds your explanation here: Without the intelligent brain (AI), the automated body is just a collection of rigid machines. The success of automation depends crucially on the intelligence of your control system.
A quantum leap – the multi -layered advantages of the new terminal generation
RE -Finition of efficiency: a quantum leap in throughput and speed
The performance data of the new systems redefine the standards for efficiency. In the first place is the area efficiency: a high -bay warehouse can reach the triple storage capacity of a conventional yards operated with RTGs on the same base area. In some configurations, this means reducing the required space requirement by up to 90 %. For ports that are trapped in dense urban rooms, this is an invaluable advantage, at the same time the envelope speed increases significantly. The elimination of unproductive movements and direct access to any container can increase the handling output on the KAI by up to 20 %. This shortens the lying times of the ships in the harbor – an enormous economic profit for the shipping companies, for which every day in the port causes high costs. The handling times for trucks can also be reduced by 20 %, which leads to less traffic jams at the gates and better utilization of the transport capacities.
The following table compares the performance indicators of the various technologies and illustrates the quantum leap, the high -bay warehouse.
Comparison of different container terminals
In the logistics and port infrastructure, container terminal files play a crucial role in efficiency and sustainability. A detailed comparison of different storage systems shows significant differences: The conventional RTG yard represents traditional storage methods with a storage density of 700-1,000 TEU per hectare and high surrounding processes between 30-60%. In contrast, the automated ASC Yard offers a significantly higher storage density of around 2,000 TEU and moderate operating costs. The high -bay warehouse (HBS) represents the most advanced solution, with an impressive storage density of over 3,000 TEU, fully eliminated surroundings and minimal environmental pollution.
The systems differ significantly in productivity, costs and environmental impacts. While conventional systems cause high local emissions and noise pollution, automated and high -bay warehouse offer significantly more efficient and environmentally friendly alternatives with electrical drive and reduced operating costs. Investment costs increase proportionally to technology complexity, whereby high -bay warehouse has the highest initial investments, but also the lowest operating costs.
The economic equation: re -evaluation of costs and return on capital
The introduction of highly automated systems leads to a fundamental shift in the cost structure. The traditional model – low investment costs (Capex) for areas and simple devices, but high ongoing operating costs (Opex) for personnel and diesel – is reversed. An HRL terminal follows a Capex-intensive but opex-light model. The high investment costs are the biggest hurdle. Projects can cost from several hundred million to over one billion US dollars. For many, especially smaller terminal operators, these sums are prohibitive. Personnel costs, the largest item in manual terminals, can be reduced by up to 70 %. The energy costs decrease significantly due to fully electric operation and energy recovery (recuperation); The Boxbay pilot project showed energy costs that were 29 % lower than expected. In addition, there are significant savings in maintenance due to forward -looking maintenance and more robust because automated processes. The return on investment (capital return) is complex and dependent. Nevertheless, there is a convincing business model if you combine the Opex savings with the immense value of the areas saved or freed. With property prices of 2,000 to 3,000 euros per square meter, the saving of only three hectares of land can represent a value of 60 to 90 million euros, which considerably puts the high initial investments into perspective.
The green terminal: a new standard of sustainability
The new generation of terminal generation also sets ecologically new standards and becomes a central component for a sustainable port industry. The main driver is the electrification: HRL systems and the associated driverless transport vehicles are fully electrically and eliminate the local emissions of CO2, nitrogen oxides (NOx) and fine dust caused by diesel machines. The combination with renewable energies can be achieved. The huge roof area of a high-bay warehouse is ideal for the installation of photovoltaic systems that supply the terminal with green electricity and potentially make it into an energy-plus system, and the environmental impact is drastically reduced. Since the operation takes place fully automatically in a closed or encapsulated system, the yard can be dispensed with. This not only reduces energy consumption, but also minimizes light pollution. Likewise, the noise pollution for neighboring urban areas is significantly reduced – a decisive advantage for ports in an urban location. Finally, the immense area efficiency makes a direct contribution to environmental protection, since it reduces the need for ecologically questionable and expensive land acquisition projects by fillings.
Strengthening the combined transport network
These advantages are transformative for the terminals of combined traffic. A terminal equipped with an HRL changes from an unpredictable bottle neck to a high -performance, reliable and fast envelope node. The high speed and, above all, the precise planning of the handling processes for trucks and trains synchronize the interfaces between the transport companies. This reliability makes the entire intermodal chain more competitive to pure road transport. If freight forwarders and rail operators can rely on punctual and quick handover in the port, the incentive to shift transports to the more environmentally friendly rail or the inland ship increases. The HRL becomes a decisive “enabler” for a more efficient and sustainable Modal Split in global freight transport.
Risks and opportunities for port automation – what companies need to know
The way to implement – navigation through the challenges
The investment hurdle: capital, complexity and regulatory
The primary obstacles are obvious. The financial burden of the enormous investment costs is a massive hurdle that can only manage the largest and finest port operators and corporations. The complexity of such multi-year major projects is immense and requires profound specialist knowledge in the areas of plant construction, robotics, IT integration and project management. Interface problems can lead to significant delays and cost increases. Last but not least, lengthy regulatory hurdles and approval procedures for such large construction projects in many countries are another major challenge.
New building vs. Retrofitting: The two paths for modernization
There are two fundamentally different scenarios in implementation, the challenges of which differ greatly. The new building approach, ie the construction of a new terminal on the “green meadow”, is the ideal scenario. It offers complete freedom of design to coordinate layout, infrastructure and processes from scratch. The Boxbay pilot project in Dubai is an example of such a quasi-new building project that demonstrated the technical feasibility under ideal conditions. The new technology must be integrated into a 24/7 operation without excessive disturbing the ongoing processes and customer service. This requires a complex, gradual implementation in which parts of the terminal are converted, while others continue to work. Such projects can last for years and mount a high risk of unforeseen costs and operational disorders. The commercial order for Boxbay in Pusan is therefore of outstanding importance: If this retrofitting implementation succeeds, this proves the practical suitability of the concept for the majority of the world ports and could be the signal for a wider market acceptance.
In the modernization of infrastructure and technology systems, companies are basically two central ways to choose from: the new building or retrofitting. Both approaches fundamentally differ in their characteristics and challenges.
The new building offers maximum design freedom, enables optimal coordination of layout and technology and allows a completely new infrastructure architecture. However, the initial investment costs are very high because all systems have to be rebuilt. The integration complexity is less because uniform systems are created from the start. The project risk remains high, primarily due to the immense investment sums.
In contrast, the retrofitting, which is characterized by severely limited freedom of design. Here adjustments to existing structures must be made, which designs the integration extremely complex. The costs can be potentially lower than in the new building, but this approach carries a very high risk of operational disorders. Companies must expect possible loss of capacity over the years.
Both project scenes have long schedules, with the new building more predictable, while retrofitting projects are more susceptible to unforeseen delays. The decision between these two ways requires careful consideration of the specific corporate requirements, technological framework and financial resources.
The human factor: socio -economic effects and the future of port work
Automation inevitably leads to profound socio -economic changes. It does not just eliminate jobs, but radically transforms the requirement profiles. Manual activities such as those of crane leaders, truck drivers in the Yard or Laschern are greatly reduced or completely disappear. At the same time, a high need for new, highly qualified specialists in the areas of IT, robotics, data analysis, system monitoring and maintenance of complex systems arises. Proactive and comprehensive strategies for retraining and further qualification are therefore not only a question of social responsibility, but also an economic necessity in order to be able to cover the new need for skilled workers. Without qualified staff for maintenance and control, the expensive systems cannot develop their potential. The social partnership plays a decisive role. Early, transparent and honest communication with the unions and employee representatives is essential to reduce resistance and make the change constructively. Concepts developed jointly to the social cushion of the transition, to participate in the productivity profits and to design the new jobs can turn potential opponents partners of the transformation and are a crucial success factor for smooth implementation.
Digital risks: cyber security in the hyper -networked port
With the increasing networking and the dependency of digital control systems, new, critical vulnerability arises: the risk of cyber attacks. A highly automated terminal is an attractive goal for hackers, saboteurs or state actors. A successful attack on the central terminal operating system could paralyze the entire port operation and would have catastrophic effects on global supply chains. This requires a fundamental rethink in the security strategy. Robust, multi-layer cyber security architectures are required, which include both IT and OT systems (operational technology). Concepts such as a “collective defense strategy”, in which port authorities, terminal operators and security authorities exchange information and react together to threats, become a necessity. Continuous monitoring, regular penetration tests and the training of staff in dealing with digital threats are no longer optional extras, but an integral part of risk management in a port 4.0.
The container terminal as a logistics operating system
The analysis shows that the further development of flat container yards into vertical, AI-based high-bay bearings is not an incremental improvement, but a fundamental new architecture of the function of a container terminal. The container parking area changes from a physical place to store goods into a high-performance, data-controlled “logistics operating system”. The traditional competitive factors such as pure handling price or maximum speed take a back seat. New, strategic imperatives are put in their place: predictability, reliability, resilience and sustainability. A terminal that can guarantee truck clearance to the minute is more valuable for modern logistics than one that is theoretically faster, but is unpredictable in practice. The strategic view goes even further. The high -bay warehouse is probably not the end point of development. More radical concepts such as the underground container logistics (underground container logistics, UCL), in which containers are transported fully automatically between different HRL nodes, the quay and the hinterland connection, are already in development. In such a scenario, container traffic would completely disappear from the surface. The HRL would then no longer be the overall solution, but a decisive component in a future, three-dimensional, fully integrated logistics ecosystem.
For the actors involved, this results in clear strategic recommendations for action:
For port operators and investors: The focus must be relocated from the pure investment costs (Capex) to the total operating costs (Total Cost of Ownership, TCO) and the strategic value of reliability and area efficiency. Investments in the standardization of processes and the development of staff must precede technological implementation.
For politics and regulatory authorities: The task is to enable and accelerate this transformation. This requires the creation of supportive regulatory framework, the promotion of research and development, the financing of qualification programs and the establishment of international standards for data exchange in order to ensure interoperability.
For the logistics industry: freight forwarders, shipping companies and rail operators must adapt to a new era of hyper-efficient, planned and data transparent port interfaces. These will enable new business models that are based on a previously unmatched level of supply chain integration and the vision of a seamless, intelligent and sustainable global freight transport is within reach.
Xpert.plus warehouse optimization – high -bay warehouse such as pallet warehouse advice and planning
We are there for you – advice – planning – implementation – project management
☑️ Our business language is English or German
☑️ NEW: Correspondence in your national language!
I would be happy to serve you and my team as a personal advisor.
You can contact me by filling out the contact form or simply call me on +49 89 89 674 804 (Munich) . My email address is: wolfenstein ∂ xpert.digital
I'm looking forward to our joint project.