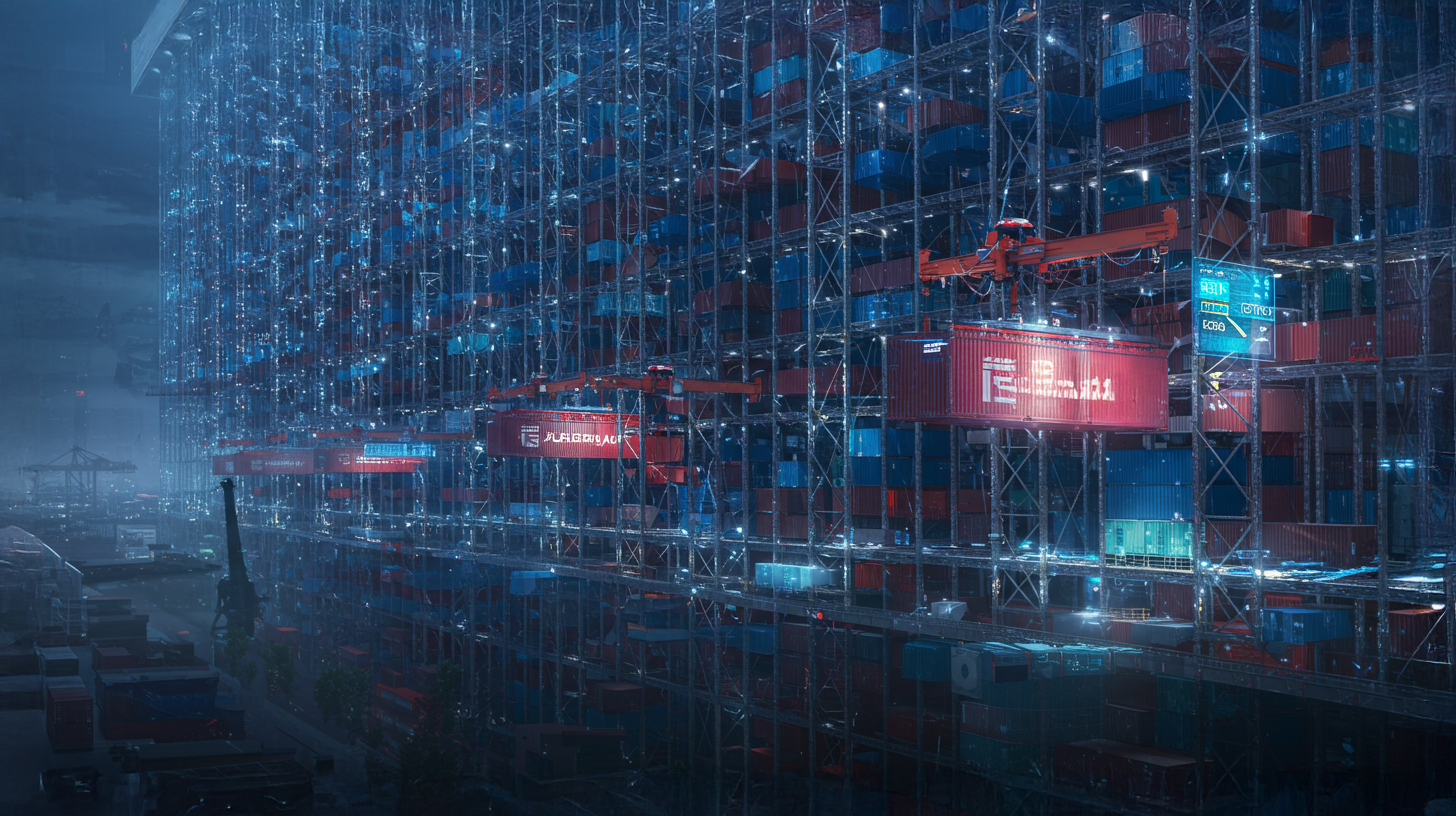
The top ten of the containers of high -bay warehouse manufacturers and guidelines: technology, manufacturer and future of port logistics - creative image: xpert.digital
Logistics of the future: automated ports and their smart infrastructure
Innovative container handling: more efficiency, less costs - the technology behind modern seaports
The world of global trade is inextricably linked to the sea container. But while the ships are getting bigger, the space in the ports remains limited. This needle fan leads to inefficiency, high costs and environmental pollution. A revolutionary technology promises to solve these problems: the container high-bay warehouse (High-Bay Storage, HBS). Instead of stacking containers and only a few layers, they are housed in huge, fully automated shelves. This article illuminates the technology, introduces the leading manufacturers and takes a look at the future of this groundbreaking development.
1. What exactly is a container high-bay warehouse (HBS)?
A container high-bay warehouse, often referred to as HBS (High-Bay Storage), is a logistics system for storing standard lake containers (typically 20-foot or 40-foot containers, also called TEU and Feu) in a highly compressed, vertical steel regal structure. You can imagine it like a huge, fully automatic bookshelf for containers.
In contrast to traditional container yards, in which containers with cranes or vehicles such as Straddle carrier (portal lugs) are stacked on top of each other, a HBS assigns a fixed, individual shelf to each individual container. The containers in and from these subjects are transported fully automatically by rail operations (stacker cranes) or other specialized robot systems. This enables direct and immediate access to each individual container without having to change other containers.
2. Why is this technology so revolutionary for ports and logistics centers?
The importance of HBS systems results from the solution of fundamental problems of conventional container storage:
Inefficiency by stacking (reshuffling): In a conventional container yard, containers are often stacked up to five or six layers in blocks. If a container is required on the bottom of the stack, all containers above it must first be removed and stored elsewhere. This process is referred to as “Reshuffling” or “Shuffle Move”. Studies show that up to 60 % of all crane movements in a traditional yard are unproductive surrounding movements. An HBS completely eliminates this problem because each container is directly accessible. This increases the cover speed dramatically.
Enormous shortage of surface: Large seaports are often located in densely populated urban areas in which land is extremely expensive and scarce. A horizontal extension is usually impossible. HBS systems use the room in the vertical. With stacking heights of 7 to 18 layers, you can store the three to four times amount of containers on the same floor area. This enables ports to massively increase their capacity without having to open up new country.
Security and automation: Traditional YARDS are busy and potentially dangerous work environments with heavy equipment and lots of staff. An HBS is a completely encapsulated and automated system. People do not enter the actual storage area, which drastically reduces the risk of accidents. The company runs around the clock (24/7) with maximum precision and reliability.
Sustainability and decarbonization: Most HBS systems are fully electric and can be operated with green electricity. Many manufacturers integrate photovoltaic systems on the huge roof areas of the bearings, which means that the systems can be operated locally CO₂-neutral or even energy positive. The elimination of countless truck and crane drives for conversion also significantly reduces energy consumption and noise emissions.
In summary, it can be said that HBS is not only a further development, but also a paradigm shift in container logistics, which raises efficiency, land use, security and sustainability to a new level.
3. Who is Boxbay and why are they considered the market leader?
Boxbay is a joint venture that was founded in 2019 and combines two industry giants: DP World, one of the largest global port operators based in Dubai, and the SMS Group, a worldwide leading German technology group in plant and mechanical engineering, whose subsidiary Amova is also active in the HBS market. This combination is strategically brilliant: DP World brings the expertise in port operations and direct market access, while the SMS Group delivers the engineering know-how for the construction of such complex systems.
Boxbay is considered the market leader because you are the first to realize a fully functional, commercially used HBS system on a large scale. Your system is characterized by the following features:
System name: Boxbay High-Bay Storage.
Technology: The system is store containers on a steel shelf with up to 11 layers. The storage and outsourcing is carried out by fully automatic shelf control units that move above (top grid) or on the side (side grid) of the shelf alley. Each container has its own place and can be reached directly at any time.
Realized projects: The decisive milestone was the commissioning of the pilot system in the port of Jebel Ali (Terminal 4) in Dubai in 2021. This system with a capacity of 792 TEU served as a “proof of concept” and demonstrated the functionality and efficiency of the system under real port conditions. In 2023, the breakthrough made the contract for the construction of a commercial system in the port of Busan (South Korea) for the operator PNC (Pusan Newport Company). This marks the transition from the pilot phase to commercial series production. DP World has also announced that feasibility studies are running for over 20 other locations worldwide.
Unique selling points: The area performance is outstanding - Boxbay promises more than three times the surface performance compared to conventional yards. Another central feature is sustainability: the entire system is fully electric, and the huge roof area of the system is designed for the installation of solar panels, which enables CO₂-neutral operation.
Your management position is based on the combination of a strong partnership, a proven product and the first commercial large order in one of the most important ports of Asia.
4. What role does Amova play, which also belongs to the SMS Group? Is there no competition with Boxbay here?
Amova is a subsidiary of the SMS Group and has many years of experience in building high-bay bearings for the heavy industry, especially for steel and aluminum coils that are heavy. Your expertise in dealing with extremely heavy loads is a perfect basis for container logistics.
System name: High-Bay Storage Systems (HBS).
Technology: Amova relies on very robust, rail -bound shelf control units (Stacker Cranes), which are designed for a load of up to 50 tons. This is important because loaded 40-foot containers can weigh over 30 tons. Your system is modular and can be adapted for large seaports as well as for smaller industrial and logistics parks in the hinterland.
Experience and market position: Amova has implemented several high -bay warehouse in steelworks since 2006. This experience in 24/7 operation Under rough industrial conditions is a strong sales argument. They position themselves as a provider of tailor-made HBS solutions that can be adapted to specific customer requirements. Your theoretical capacity indication is impressive: up to 160,000 TEU per hectare (HA), which underlines the enormous density of your systems.
On the question of competition with Boxbay: Although both belong to the SMS Group, they follow different, complementary strategies. Boxbay is a standardized, highly scalable product that is primarily pressed into the global seaport market by the partner DP World. Amova acts more as a flexible solution provider who offers its proven heavy load technology for a wider range of applications, including industrial and internal terminals. You can see it as a double strategy of the SMS Group to cover different market segments.
5. What is special about the Konecranes & Pesmel approach?
The Finnish crane manufacturer Konecranes and the automation specialist Pesmel entered the market in 2022 and form another strong European consortium. Konecranes is a world's leading name in port crane technology, while Pesmel is an expert in automated material flow systems in the paper and metal industry.
System name: Automated High-Bay Container Storage (AHBCS).
Technology: Your system stands out due to an impressive storage height of up to 14 layers, which further maximizes the area density. Instead of classic shelf control units, use a system of rack shuttle cranes. These shuttles can move very quickly within the shelves and hand over the containers to central lifting devices.
Unique selling point and market strategy: A central sales argument is the seamless connection to distribution centers. Your concept provides to dock the container camp directly to the loading lamps of a goods camp or a production hall. This enables “Ware-Zur-Halle” scenarios: an incoming container is stored directly from the ship or truck into the HBS and automatically transports the correct dock of the adjacent building if necessary. This eliminates intermediate steps such as transport via the yard via truck.
Market activity: Although they have only been active since 2022, they state that tenders in Europe and the Middle East are already underway. Your strong brand and your innovative approach to warehouse integration make you a serious competitor for Boxbay and Amova.
6. LTW Intralogistics already built an HBS in 2011. Why don't you stand up in the ranking?
LTW intralogistics from Austria is a pioneer in this area. You already realized a container camp for the Swiss army in Thun in 2011. This makes it one of the first providers worldwide with a functioning system.
System name: container warehouse.
Technology: The system in Thun uses a gait chassis with on-board shuttles. This means that a larger shelf operator drives through the corridor, but carries a smaller, more agile shuttle with it that inserts the container on the side of the shelf. The system is designed for a load of 18 tons and can even be operated in chilled environments up to -28 ° C, which is predestined for the storage of cooling containers (reefers) or sensitive goods.
Why not up? The reason is the scaling and market focus. The project for the Swiss army was a very specific, relatively small niche application. LTW has long focused on such special solutions and has not actively addressed the mass market of the large seaports, as DP World/Boxbay do. However, they collect: A second, significantly larger system is currently (2024/25) under construction, which doubles the capacity of the first project. This shows that LTW is now also in larger dimensions. Their placement in midfield reflects her role as a highly innovative niche provider who has the potential to continue to rise.
Xpert.Plus warehouse optimization - high-bay warehouses such as pallet warehouses consulting and planning
From Austria to China: global innovations in container logistics
7. Vollert plant construction is called in connection with Lufthansa Cargo. What is their specialty?
Vollert plant construction is a German company that specializes in severe intralogistics and maneuvering systems. Your approach for container storage is conceptual and is aimed at specific cargo customers.
System name: Container Logistics Solution (concept phase).
Technology: Your concept is based on a shelf operator (Stacker Crane), which is equipped with a side grip frame. This can absorb and stop containers from the side. A key component of your concept is the interface to driverless transport systems (AGVS) and adjacent warehouses.
Specialty and projects: Vollert is strong in the area of the air freight. A pioneering project is the implementation of a high -bay warehouse for ULDS (Unit Load Devices) - the standardized aviation containers of aviation - for Lufthansa Cargo, which is to be completed in 2025. Although Ulds are smaller and lighter than sea containers, this project proves its competence in the automated storage of large loading units. Their expertise is to integrate HBS systems seamlessly into complex logistics chains of cargo and air freight customers.
8. What do we know about JFE Engineering's Japanese solution?
JFE Engineering is another earlier pioneer. You already installed an HBS system in the Tokyo-Ohi Terminal in Japan in 2011.
System name: “Container Hangar”.
Technology: The system in Tokyo is designed for 840 TEU and stacks containers 7 layers. Technologically interesting is your in-course crane with an integrated rotary table. This enables the crane to turn the container to align it flexibly.
Market position: The system in Tokyo has been serving as a “proof of concept” for over a decade and has demonstrated its reliability. However, JFE Engineering does not seem to have been aimed at a broad international expansion. Their solution is proven and functional, but less ambitious compared to the latest systems from Boxbay or Konecranes/Pesmel in terms of height and scalability. They represent the solid but rather conservative Japanese approach to technology.
9. ZPMC is a giant in port crane technology. What is your contribution to the HBS market?
ZPMC (Shanghai Zhenhua Heavy Industries Company) from China is the world's largest manufacturer of harbor cranes. When ZPMC enters a market, this is a clear sign of its relevance.
System name: Fully Automated Empty Container High-Stack Yard.
Specialization: ZPMC is currently focusing on a specific but huge problem: the storage of empty containers. In many ports, empty containers make up a significant part of the inventory and consume valuable areas.
Project and technology: ZPMC is currently building a gigantic project in the port of Ningbo-Zhushan. This system is said to have a capacity of 25,000 TEU and the containers 18 layers are stacked up. This exceeds the amount of most other systems. The technology is based on a shuttle crane system that is operated 100 % electrically.
Strategic importance: by first concentrating on empty containers, you address an urgent need and can perfect your technology in a less complex environment (no different weights, no dangerous goods or cooling containers). However, it is very likely that ZPMC will also offer this technology for fully loaded containers in the future and thus rose to a global heavyweight in the HBS market.
10. What is known about the concepts of Container Logistics International (CLI) and the Retrofit module from Konecranes-Amova?
These two entries represent innovative niches and future approaches.
Container Logistics International (CLI): Cli is an emerging provider that is still in the pilot and offer phase.
System name: Tower Matrix System.
Technology: Your concept relies on particularly narrow shelf control units and side procedure, which enables a very dense package of the shelves. The system is modularly designed and can be easily expanded. Storage heights of up to 14 layers are planned. Similar to ZPMC, Cli aims onto the market for empty containers and internal terminals.
Konecranes-Amova (SIDEGRID Retrofit): This is not an independent HBS, but a clever retrofit concept.
Concept: Instead of rebuilding a complete HBS, they suggest gradually modernize existing, traditional container yards. Your port retrofit module integrates the HBS control structure (similar to the Boxbay Side-Grid or the AHBCS rack) with the existing cranes (e.g. rubber-tired portal cranes, RTGS). The crane takes over the transport of the container to the edge of the HB, where an automatic system carries out the storage to the shelf.
Market potential: This approach is extremely attractive for port operators who want to increase their efficiency, but shy away from gigantic initial investment for a completely new HBS. It enables a gradual transformation. Consulting projects in North America and the EU have been running since 2024.
11. LTW intralogistics and Armasuisse. What kind of project is that?
This is a highly innovative special application that shows the flexibility of HBS technology.
Project: Mobile Container HBS for defense purposes.
Partner: LTW Intralogistics (the technology provider) and Armasuisse, the Federal Office of Switzerland.
Purpose: The Swiss army needs a solution for the fast and efficient storage and provision of material that is stored in containers. An HBS offers 100 % direct access and 24/7 availability, which is decisive in military or crisis scenarios. The facility for the Swiss Armed Forces (planned for 2025) will double the capacity of the existing facility in Thun.
Technology: The system will use double -depth storage to further increase the density, but still guarantee 100 % direct access (the shelf operator can reach both subjects in depth). The term “mobile” may indicate that the system is designed in such a way that it could theoretically be broken down and rebuilt in another strategic place.
Suitable for:
- The high -bay warehouse of the Swiss Army | 18,000 kg of shelf control equipment from LTW: heavy -duty technology at a new level
Our recommendation: 🌍 Limitless reach 🔗 Networked 🌐 Multilingual 💪 Strong sales: 💡 Authentic with strategy 🚀 Innovation meets 🧠 Intuition
At a time when a company's digital presence determines its success, the challenge is how to make this presence authentic, individual and far-reaching. Xpert.Digital offers an innovative solution that positions itself as an intersection between an industry hub, a blog and a brand ambassador. It combines the advantages of communication and sales channels in a single platform and enables publication in 18 different languages. The cooperation with partner portals and the possibility of publishing articles on Google News and a press distribution list with around 8,000 journalists and readers maximize the reach and visibility of the content. This represents an essential factor in external sales & marketing (SMarketing).
More about it here:
Efficiency without limits: the technology breakthrough, the ports completely changed
12. The most important trend seems to be the “direct individual access”. Why?
The “direct individual access” is the heart and the largest efficiency driver of the HBS technology. To understand its meaning, you have to imagine the nightmare of a traditional container yard:
Imagine a stack of 10 books. You need the lowest book. You have to raise the upper nine books, set aside, take out the tenth book and stack the other nine back. This is exactly what happens millions of times in the world's ports every day. A truck driver comes to pick up container “XYZ”. However, this container is in series 5, 3rd place, in position 1 (at the bottom), and four other containers are stacked on it. A huge crane now has to raise these four “disturbing” containers one after the other and implement them for free places in the yard. Only then can he reach the desired container “XYZ” and load them onto the truck.
These unproductive movements are called “Shuffle Moves” or “Reshuffling”. The statistics that they can make up to 60 % of all crane movements illustrates the immense waste of time, energy and resources.
The HBS system radically solves this problem: each container is placed in its own, firmly assigned shelf. The automated shelf operator drives directly to this subject, removes the container and transports it to the transfer point. Not a single other container has to be moved. Each container can be reached 100 % directly at any time. This leads to:
Dramatically shorter handling times for trucks and trains.
Foreseeable and reliable envelope times.
Enormous energy saving because unproductive crane trips are no longer available.
Less wear on the devices.
All ten manufacturers presented rely on this principle because it heals the basic weakness of conventional storage.
13. How is the high area efficiency achieved?
The area efficiency of HBS systems is the result of two factors: vertical stacking and condensed geometry.
Vertical stacking: While traditional straddle-carrier fields can usually only stack up 3 to 4 layers (RTG-cranes create 5-6 layers), use HBS systems of 7 layers (JFE) to 11 (boxbay) up to 14 (Konecranes) or even 18 were (ZPMC). The storage capacity on the same base area is at least doubled or tripled.
Dignified geometry: In a conventional yard, wide passenger must be kept free for the huge straddle carriers or RTG cranes. These roads consume a significant part of the total area. In an HBS, the corridors between the shelves are extremely narrow - just wide enough for the shelf control device. There is no lost area for maneuvering processes.
As stated in the source, the result is a three to four times the use of land. A hectare (10,000 m²) land, on which maybe 1,000 TEU could traditionally be stored, can suddenly take up 3,000 to 4,000 TEU or more with a HBS. This is an invaluable advantage for a port like Singapore or Hamburg, where every square meter counts.
14. What role do fully electric drives and solar integration play for the future of the ports?
A very big one. Ports are under massive pressure to reduce their CO₂ emissions. They are hotspots for the consumption of diesel by trucks, cranes and other vehicles. HBS systems are an important building block for the “green harbor” of the future.
Fully electric drives: All cranes and shuttles in an HBS are powered electrically. This eliminates local emissions (CO₂, nitrogen oxides, fine dust) and significantly reduces the noise. Many systems also use regenerative drives. This means that when braking or lowering a heavy container, energy is recovered and fed into the system (similar to an electric car). This lowers the total energy consumption.
Solar integration: The roof area of a large HB can include several soccer fields. Manufacturers such as Boxbay, Konecranes/Pesmel and Amova plan their systems from the outset in such a way that these roofs can be fully equipped with photovoltaic modules. The solar energy generated in this way can be used directly to operate the warehouse. Depending on the location and size, the system can cover a large part of its own electricity requirements or even generate more energy than it consumes and thus become CO₂-neutral locally.
This combination makes HBS a showcase technology for decarbonizing the heavy industry and logistics.
15. What does the trend “connection to warehousing & production” mean?
This trend, which is mainly driven by Konecranes/Pesmel, and the second LTW generation, marks the next evolutionary level of the HBS: integration into the entire supply chain.
Traditionally, the container yard of a port is a separate unit. A container is stored there, then loaded onto a truck and driven to an external distribution center or a factory. He is unloaded there.
The new concept breaks open this separation. The HBS is physically grown directly to the warehouse or the production line. The process then looks like this:
A ship arrives, a container is unloaded and stored directly into the HBS.
The company's goods management system reports a need.
The HBS system gets the right container fully automatically from the shelf and transports it directly to a specific loading ramp or a conveyor technology interface of the adjacent building.
The intermediate step of the truck transport from the Yard to the warehouse does not apply. This has enormous advantages:
Saving time: No waiting times for trucks, no traffic jams in the port.
Cost reduction: No transport costs for the “last kilometer” in the port.
Emission reduction: no more diesel trucks necessary for this transport route.
Process optimization: The entire chain from the ship to the production line becomes a single, automated and data -controlled process.
This “Ware-Zur-Halle” scenario (or “container-zum-dock”) makes the HBS from a pure camp an active buffer and sorting center that is deeply integrated into the value creation processes of its customers.
16. How realistic is a speedy, wide market penetration of HBS technology?
The signs indicate a very quick development and a broad market penetration in the coming years. The data from the source support this forecast:
DP World's statement that there is feasibility studies for over 20 port locations is a strong indication. Port operators do not invest in expensive studies if there is no serious interest. This shows that the technology worldwide is on the big player agenda.
Konecranes' forecast of an annual market volume of over $ 1 billion from 2028 is also very meaningful. This implies that several large HBS systems are built worldwide every year. The main driver is the irreversible rural shortage in megaports.
The development of niche markets in the hinterland (rail hub terminals) and for special applications (empty container, military logistics) shows that the market is not only limited to the top 10 ports of the world. Providers such as ZPMC, CLI and LTW open up new fields of application here, which further accelerates the overall market dynamics.
In summary, it can be said that the technology has overcome its teething problems, the pilot projects were successful, the first commercial contracts are signed, and the biggest problems of port logistics (lack of space, inefficiency) are addressed directly. The broad market penetration is therefore no longer a question of the “whether”, but only of the “how fast”.
17. What is the final conclusion about the manufacturers and the technology?
The conclusion is clear and positive: Container high-bay warehouse develops from isolated pilot projects into an independent, rapidly growing and strategically decisive market segment of global logistics.
The manufacturers presented here are the driving forces behind this revolution. They can be divided into three groups:
The series tires market leaders (Boxbay, Amova, Konecranes/Pesmel): They have strong partnerships, proven technology and the ability to implement turnkey major projects for the most important seaports in the world.
The highly innovative industry specialists (LTW, complete): With their deep expertise, they serve niches such as cooling or dangerous goods storage, air freight or military applications and thus drive the technological diversity.
The scaling challengers and pioneers (JFE Engineering, ZPMC, CLI): This group comprises early pioneers (JFE), who could now scale their proven concept, as well as new, aggressive actors (ZPMC, CLI) who want to focus on specific problems such as empty containers.
Together, these companies cover the entire spectrum and ensure a healthy competition that accelerates innovations. They not only solve a logistical problem, but also make a significant contribution to automation, efficiency increase and, above all, to decarbonization of the port industry and the associated supply chains. The age of flat, inefficient and environmentally harmful container stacks is coming to an end - the future of container logistics is vertical, automated and green.
We are there for you - advice - planning - implementation - project management
☑️ Our business language is English or German
☑️ NEW: Correspondence in your national language!
I would be happy to serve you and my team as a personal advisor.
You can contact me by filling out the contact form or simply call me on +49 89 89 674 804 (Munich) . My email address is: wolfenstein ∂ xpert.digital
I'm looking forward to our joint project.