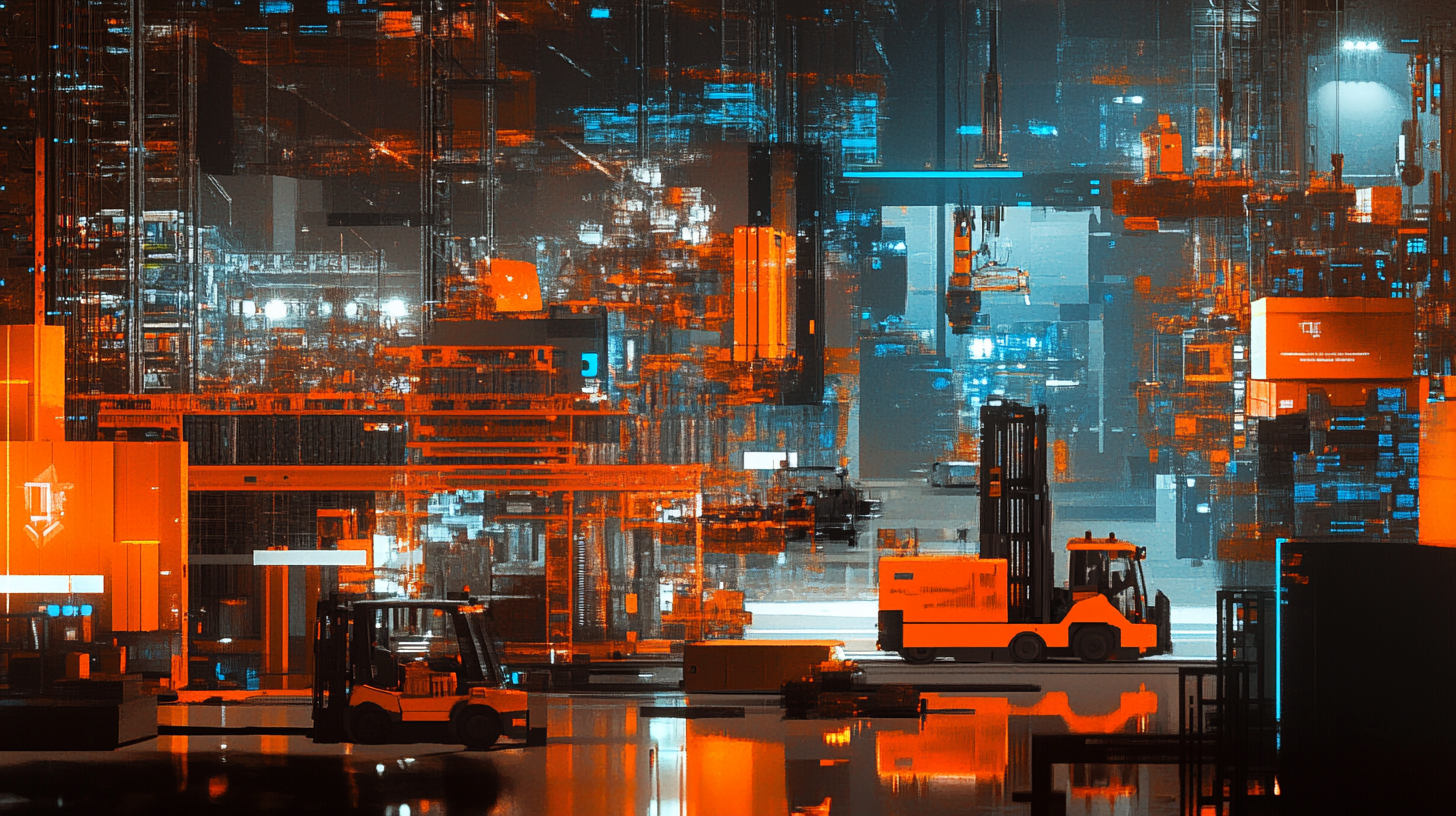
Warehouse automation: When optimization is enough and when a comprehensive retrofit is unavoidable - Image: Xpert.Digital
Retrofit vs. warehouse optimization: How to find the best solution for your company
Step by step to the perfect storage strategy: analysis, evaluation and decision
The question of whether targeted warehouse optimization is the best solution or whether a comprehensive retrofit is unavoidable depends on a variety of factors that each company must evaluate individually. The aim is to analyze the current status of the storage system in detail and compare it with the future requirements and goals of the company. There is no general answer, but a structured approach helps to make the right decision.
Suitable for:
The path to warehouse optimization: Targeted improvements for more efficiency
Warehouse optimization is a sensible and often more cost-effective alternative if the basic substance of the warehouse is still intact. This means that the mechanical infrastructure, such as shelves, conveyor technology or any installed automatic components, still serves its purpose and does not have any serious defects. If only adjustments or selective improvements are necessary to accelerate existing processes or make them more efficient, optimization may be sufficient. The focus here is primarily on increasing efficiency within the existing framework without making any profound technological changes.
Specific measures as part of warehouse optimization can be diverse: The implementation or a significant improvement of the warehouse management system (LVS) often plays a central role. A modern WMS enables more precise inventory management, optimizes picking routes and improves overall order processing. By recording warehouse movements and stocks in detail, bottlenecks can be identified and resources can be planned better.
Optimizing the warehouse layout and the associated workflows can also bring about significant increases in efficiency. A well-thought-out arrangement of storage locations, consideration of turnover rates and a clear structuring of the picking zones can shorten walking distances and reduce throughput times. The introduction of clearly defined processes and responsibilities also contributes to a smoother process.
An often underestimated factor is people. Targeted training of employees in new processes, how to use new software or optimized workflows can make a significant difference. Improved control of employees, for example through more detailed work instructions or performance monitoring, can also contribute to increasing efficiency.
The introduction of mobile devices such as scanners or tablets or even the use of smart glasses for direct process support can increase accuracy and reduce processing times. Employees have all relevant information directly in their field of vision and can carry out work steps faster and more accurately.
The comprehensive retrofit: When renewal becomes a necessity
A retrofit, on the other hand, is unavoidable or at least the more economically sensible option if the existing system is getting old and this results in frequent malfunctions and associated downtimes. If replacement parts for outdated components have become difficult to obtain or prohibitively expensive, this also indicates the need for a major overhaul. Rising operating costs due to inefficiencies, for example due to high energy consumption of old systems or inefficient processes, can also be a strong argument for a retrofit.
Security aspects play a crucial role. If existing systems no longer meet current safety standards or even pose safety risks, a retrofit is essential to protect the health of employees and meet legal requirements. Even if a significant increase in the performance of the bearing is required, which cannot be achieved with existing resources, there is hardly any way around a retrofit.
The integration of new technologies or comprehensive automation solutions is another important driver for retrofit projects. Companies that want to strengthen their competitiveness through the use of modern technologies such as artificial intelligence (AI) or augmented reality (AR) will generally not be able to avoid a retrofit.
The many advantages of a retrofit
A key advantage of a retrofit is the lower costs compared to a completely new building. As a rule, the costs for a retrofit are between 30 and 70 percent of the costs of a completely new system. This allows companies to modernize their warehouse infrastructure without putting undue strain on the budget.
A well-carried retrofit significantly extends the service life of the system, often by 15 to 20 years. This is an important aspect as it means the original investment can be used for longer and the depreciation periods are extended.
In many cases, system availability is significantly increased by a retrofit, often by more than 20 percent. By replacing vulnerable components and modernizing the control technology, susceptibility to faults is reduced and operational reliability is increased.
The performance of the warehouse also benefits from a retrofit. Throughput increases of 10 to 30 percent are not uncommon. This is achieved through faster conveyor technology, more intelligent control algorithms and more efficient processes.
Another important aspect is improving energy efficiency. Modern drives, energy-optimized controls and intelligent operational management can significantly reduce energy consumption and thus sustainably reduce operating costs. This not only contributes to economic efficiency, but is also an important contribution to environmental protection.
The retrofit also offers the opportunity to integrate modern technologies such as AI or AR. For example, AI can be used in warehouse management to create demand forecasts, optimally allocate storage spaces or predict maintenance intervals (predictive maintenance). AR can support maintenance work or picking processes by displaying relevant information directly in the employees' field of vision.
The path to the right decision: Structured decision-making
In order to make an informed decision as to whether warehouse optimization is sufficient or a comprehensive retrofit is necessary, a structured approach is recommended:
First of all, a comprehensive system analysis is essential. The current condition of the mechanics, control technology, software and the entire infrastructure should be recorded in detail. Which bottlenecks are currently hindering the smooth process? Which components are particularly susceptible to failure? What is the current level of automation?
In the next step, the product life cycle of the installed components should be evaluated. Are important components already discontinued or about to expire? Is the supply of spare parts secured or is there a risk of bottlenecks? This provides information about how long the existing system can probably continue to be operated reliably.
A detailed analysis of current and future business needs is also crucial. How will order volumes develop? Are there any changes planned in the product range or sales channels? What requirements do customers have in terms of delivery times and flexibility? The warehouse must be able to meet these future requirements.
Based on these analyses, a cost-benefit calculation should be created for various scenarios. What costs are associated with pure optimization? What investments are necessary for a retrofit and what benefits does it bring (e.g. higher performance, lower operating costs, improved safety)? Long-term aspects should also be taken into account.
The impact on ongoing operations must also be taken into account in the decision. Can a retrofit be carried out during ongoing operations or are longer downtimes unavoidable? What impact would this have on delivery capability and customer satisfaction? In many cases it is possible to carry out a retrofit in phases to minimize disruption.
A retrofit is particularly useful if the mechanics of the system is still in good condition, but the control, the drives and the software are outdated and no longer meet the current requirements. The existing mechanical infrastructure can continue to be used, while the “intelligent” components are brought up to date.
Ultimately, the decision depends on the company's specific needs, available budget, and long-term goals. Careful planning and detailed analysis are crucial in order to make the right choice between optimization and retrofit and thus ensure the efficiency and competitiveness of the warehouse in the long term. It is advisable to seek advice from experienced experts who have the necessary know-how to evaluate the different options and find the best solution.
The future of warehouse automation: More than just increasing efficiency and reducing costs
Advancing warehouse automation is not a trend, but a necessity, driven by a variety of factors and the unstoppable progress in technology and economics. The reasons for automation are complex and go far beyond simply reducing costs. In the future, the role of the warehouse will change fundamentally, from a pure storage location to an intelligent logistics center.
The driving forces of warehouse automation
Increasing efficiency and reducing costs remain key motivators for automation. Automated systems work around the clock, without fatigue and with high precision. This leads to a significant acceleration of warehouse processes compared to manual work. In the long term, automation reduces operational costs by reducing staffing requirements, minimizing errors and optimizing energy consumption. Optimal use of available storage space, achieved through automated storage systems, can result in space savings of up to 80 percent.
Automation is also an answer to the growing challenges of modern logistics. The increasing shortage of skilled workers in the logistics industry is making it increasingly difficult to find and retain qualified personnel. Automated systems can close some of this gap. At the same time, customer expectations regarding delivery speed and quality are constantly increasing. E-commerce and same-day delivery are no longer a thing of the future, but a reality. Automated warehouses allow companies to meet these needs. The volatility of the markets and the growing demands of e-commerce also require flexible and responsive logistics solutions that can be realized through automation.
An often overlooked aspect is improving working conditions. Automation relieves employees of monotonous and physically demanding tasks that can lead to long-term health problems. Occupational safety is increased by taking over dangerous tasks from machines. In addition, more ergonomic workplaces can be created, for example in order picking, where robots lift heavy loads or take on repetitive tasks.
A look into the future: The trends in warehouse automation
The future of warehouse automation is characterized by rapid technological developments and innovative concepts:
Advanced robotics and artificial intelligence (AI) will play an increasingly important role. The use of autonomous mobile robots (AMR) for flexible transport tasks within the warehouse will continue to increase. These robots can orient themselves without fixed routes and adapt dynamically to changing conditions. Collaborative robots (cobots) that can work safely with people are being used in more and more areas, for example in order picking or packaging. The integration of AI and machine learning enables predictive analysis, for example to predict machine failures (predictive maintenance) or to optimize inventory levels. AI-supported systems will also be able to make complex decisions autonomously and continuously improve processes. Even swarm intelligence, in which many small robots work together in a coordinated manner, could play a role in the future. AI will also be used in quality control, for example through image recognition to identify damaged products.
Suitable for:
Innovative technologies will revolutionize warehouse logistics. The use of drones for inventory tasks, where they fly independently through the aisles and record inventory, becomes more efficient and faster. In the future, drones could also be used to transport goods within the warehouse or even for the last mile. Virtual and augmented reality (VR/AR) offer new possibilities for system planning and employee training. Employees can train new processes in virtual environments or familiarize themselves with the operation of complex systems. AR glasses can help with maintenance work by displaying technical information or step-by-step instructions directly in the technician's field of vision. The use of digital twins, virtual images of the real warehouse, enables the simulation and optimization of warehouse processes before changes are implemented in the real world. Blockchain technology could also play a role in the future to increase transparency and traceability in the supply chain.
Suitable for:
Networking and data use are becoming increasingly important. The Internet of Things (IoT) enables real-time monitoring and control of systems and processes. Sensors record data about the condition of machines, the fill level of containers or the position of goods. This data is used to optimize processes and respond to disruptions at an early stage. Cloud computing provides the necessary infrastructure to process and analyze huge amounts of data. Big data analytics makes it possible to identify patterns and trends and make informed decisions. The integration of various systems, such as WMS, transportation management systems (TMS) and enterprise resource planning systems (ERP), ensures a seamless flow of information throughout the supply chain. Cybersecurity is becoming an increasingly important topic in order to protect sensitive data from unauthorized access.
Sustainability and flexibility are also becoming increasingly important. The use of energy-efficient and resource-saving automation solutions is becoming increasingly important in order to reduce the ecological footprint. This includes, for example, the use of energy-efficient drives, the use of renewable energies or the optimization of transport routes to save fuel. There is also a trend towards scalable and flexible systems that can quickly adapt to changing requirements. Modular automation solutions allow companies to expand or reduce capacity as needed. The trend towards smaller, decentralized warehouses close to customers (micro-fulfillment centers) will increase to enable faster deliveries and reduce last-mile costs. Circular economy concepts will also become increasingly important in warehouse logistics, for example through the reuse of packaging materials or the return of products. Human-machine collaboration (MMK) will be an important part of future warehouses. Robots will not completely replace human workers, but rather take on supporting tasks and work hand in hand with employees.
In the future, warehouse automation will lead to a comprehensive transformation of the logistics industry, with a focus on efficiency, flexibility, sustainability and collaboration between people and machines. Companies that recognize these developments early on and integrate them into their strategy can secure important competitive advantages and consolidate their position in the global market. The future of the warehouse is intelligent, connected and autonomous - a place where technology and human competence work together optimally.
Xpert partner in warehouse planning and construction
Warehouse automation: When is warehouse optimization enough and when is a retrofit necessary?
The decision between warehouse optimization and a retrofit presents a key challenge for many companies. At a time when efficiency and adaptability are key factors for success in logistics, making the right choice is crucial. This guide highlights the most important aspects, offers valuable insights and expands the topic with future-oriented perspectives.
Warehouse optimization: More efficiency with targeted adjustments
Warehouse optimization can be the right choice if the existing infrastructure is largely intact and only minor adjustments are needed to make processes more efficient.
When does warehouse optimization make sense?
- Technical integrity: The warehouse's mechanics and basic infrastructure are still functional and meet current requirements.
- Minimal adjustments: Only minor improvements or extensions are required.
- Process-focused goals: The focus is on increasing the efficiency of existing processes without extensive technological innovations.
- Budget constraints: A complete modernization or retrofit would be oversized or too costly.
Possible warehouse optimization measures
- Improving the warehouse management system (WMS): A modern WMS enables more precise control of warehouse processes and improves transparency.
- Optimizing the warehouse layout: The arrangement of shelves, picking stations and paths can bring significant efficiency gains.
- Employee training: Investing in staff training to make optimal use of existing resources.
- Use of mobile technologies: Smart glasses or mobile devices can provide real-time information and accelerate processes.
Retrofit: modernization instead of new construction
A retrofit is recommended when the existing infrastructure no longer meets the requirements, but a completely new system is neither necessary nor economical.
When is a retrofit necessary?
- Age of the system: The existing systems are outdated, which leads to malfunctions or downtimes.
- Spare parts problems: Spare parts are difficult to obtain or are expensive.
- Increased operating costs: Inefficiencies drive up running costs.
- Security risks: New security standards can only be met through modernization.
- Technological requirements: The integration of new technologies such as automation or digital systems is necessary.
Advantages of a retrofit
A retrofit offers numerous benefits, including:
- Cost efficiency: The costs are typically between 30-70% of a new building.
- Service life extension: The system service life is increased by 15 to 20 years.
- Performance increase: Higher throughput rates from 10% to 30%.
- Energy efficiency: Improved technologies reduce energy consumption.
- Seamless integration: Modern technologies such as AI and AR can be easily integrated.
Decision making: optimization or retrofit?
The decision between warehouse optimization and a retrofit requires a comprehensive analysis. The following steps will help you make a decision:
- Analysis of the existing systems: Technical condition, efficiency and capacities must be assessed.
- Life cycle assessment: How long will the existing components still be economically viable?
- Business requirements: Are the current and future requirements for the warehouse known?
- Cost-benefit analysis: Which scenario offers the best returns?
- Impact on operations: How severely will ongoing operations be affected?
A retrofit is particularly recommended if the mechanical infrastructure is still solid, but controls, drives or software need to be modernized. Well-planned retrofits can even be carried out during ongoing operations.
Why warehouse automation?
The automation of warehouses is becoming increasingly important. The reason for this lies in the diverse benefits it offers and the challenges it addresses.
Increased efficiency and reduced costs
- Speed: Automated processes run up to ten times faster than manual ones.
- Cost reduction: Reduced personnel requirements and lower error rates reduce operating costs in the long term.
- Space savings: Up to 80% of storage space can be saved through compact automation solutions.
Overcoming challenges
- Shortage of skilled workers: Automation helps to compensate for the increasing labor shortage in logistics.
- Increasing customer expectations: Fast deliveries and high quality are becoming the standard.
- Flexibility: Automated systems adapt more quickly to market changes.
Improvement of working conditions
- Ergonomics: Employees are relieved of heavy or repetitive tasks.
- Safety: Dangerous activities are carried out by machines.
- Motivation: Collaboration with modern technologies increases satisfaction.
Future trends in warehouse automation
The future of warehouse automation will be shaped by innovation and technological advances. Here are the key trends:
Advanced robotics and AI
- Autonomous mobile robots (AMR): These robots offer flexible solutions for transport and order picking.
- Collaborative robots (cobots): Cobots work side by side with humans and can take on tasks such as packaging.
- Predictive analytics: AI-based systems optimize warehouse processes through real-time data analysis.
Matches:
Innovative technologies
- Drones: These can carry out inventory and potentially even transport goods.
- Virtual and Augmented Reality (VR/AR): These technologies support the planning of systems and the training of employees.
- Blockchain: For more transparency and security in the supply chain.
Suitable for:
Networking and data use
- Internet of Things (IoT): Sensors monitor and control warehouse processes in real time.
- Digital twins: Virtual models of the warehouse help to simulate and optimize processes.
- Seamless integration: Systems are networked together to ensure a smooth flow of information.
Sustainability and flexibility
- Energy efficiency: Automated systems reduce energy consumption.
- Decentralized warehouses: Smaller warehouses close to customers shorten delivery times.
- Scalability: Systems can be adapted to growing requirements.
Decision making is a strategic process
The decision between warehouse optimization and retrofit is a strategic process that depends on the specific needs of a company. Both approaches offer their own advantages and must be carefully planned. Looking ahead, it is clear that warehouse automation remains the key to competitiveness. Companies that invest in intelligent solutions now will secure long-term benefits in a rapidly changing world.
Xpert.Plus warehouse optimization - high-bay warehouses such as pallet warehouses consulting and planning
We are there for you - advice - planning - implementation - project management
☑️ SME support in strategy, consulting, planning and implementation
☑️ Creation or realignment of the digital strategy and digitalization
☑️ Expansion and optimization of international sales processes
☑️ Global & Digital B2B trading platforms
☑️ Pioneer Business Development
I would be happy to serve as your personal advisor.
You can contact me by filling out the contact form below or simply call me on +49 89 89 674 804 (Munich) .
I'm looking forward to our joint project.
Xpert.Digital - Konrad Wolfenstein
Xpert.Digital is a hub for industry with a focus on digitalization, mechanical engineering, logistics/intralogistics and photovoltaics.
With our 360° business development solution, we support well-known companies from new business to after sales.
Market intelligence, smarketing, marketing automation, content development, PR, mail campaigns, personalized social media and lead nurturing are part of our digital tools.
You can find out more at: www.xpert.digital - www.xpert.solar - www.xpert.plus