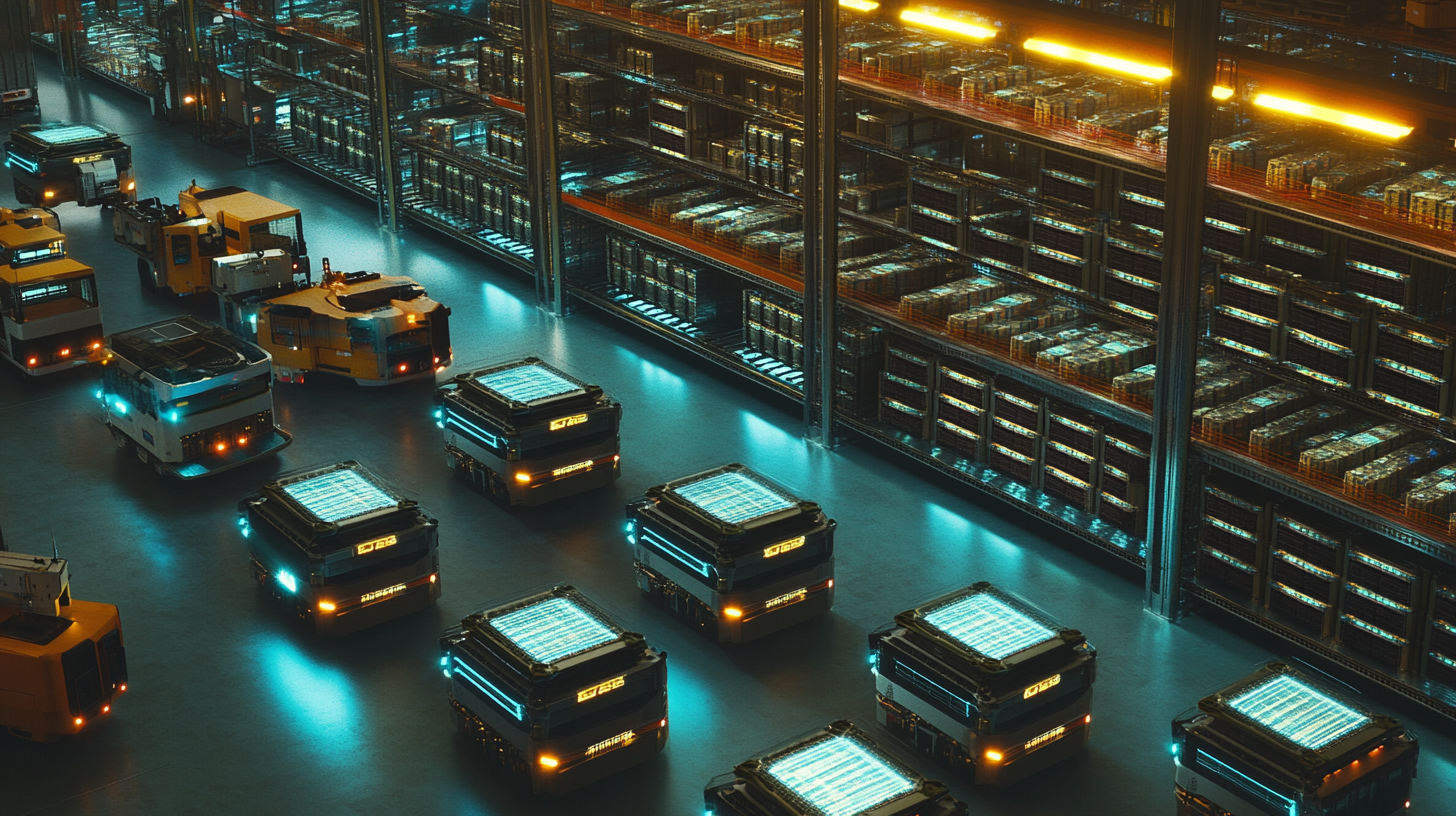
Warehouse management is facing a groundbreaking change: product identification with GTIN and the GS1 Data Matrix Code – Image: Xpert.Digital
The planned changes through the GS1 initiative
Warehouse management is facing a groundbreaking change: From 2027, the global GS1 organization will set new standards with its so-called “Sunrise 2027” initiative to increase efficiency and transparency throughout the entire supply chain. A central element of this development is the introduction and greater use of 2D barcodes such as QR codes and DataMatrix codes, in which, among other things, the Global Trade Item Number (GTIN) is stored. This GTIN remains essential for clear product identification, but is supplemented by further product information. This transition brings with it comprehensive improvements that impact processes, automation, data exchange and the long-term competitiveness of companies. The following explains in detail what advantages these 2D codes offer for warehouse management, how the GTIN continues to play a central role, what extended product data storage is all about and why an early changeover is so important for companies.
The importance of accurate data collection
“The future of warehouse management lies in precise and secure data capture,” say many experts. In this context, GS1, as one of the most important global organizations for standardized identification and communication solutions in the supply chain, has set the course for 2027. The aim is to enable quick and reliable identification of products across the entire value chain. The previous 1D barcodes are no longer sufficient for this because they can often only display the GTIN. Although this standard has made a significant contribution to revolutionizing trade and logistics worldwide, the demands on modern warehouse management and merchandise management systems have increased enormously. Companies today need additional information such as batch numbers, expiry dates or detailed product specifications in order to speed up storage processes, facilitate recalls and maintain a complete overview of all inventories.
The advantages of 2D barcodes
This is where 2D barcodes come in, which can store significantly more information using QR codes and DataMatrix codes. “Compared to traditional 1D barcodes, up to 7000 characters can be represented in 2D codes,” says many specialist publications. This significant data density is a decisive advantage, for example when it comes to integrating exact serial numbers, batch information or production details in a single code.
This offers a number of advantages for warehouse management: The simple recording of this information using appropriate scanners or mobile devices allows much more precise inventory management. This means that goods can be collected, located and removed more quickly. Every movement of a product leaves a digital footprint that is reflected in real time in the warehouse management software. In this way, stockouts can be reduced and potential bottlenecks can be identified at an early stage.
“Advanced Supply Chain Management” as a key component
Another key point of the GS1 Sunrise 2027 initiative is the so-called “Extended Supply Chain Management”. This includes not only data about inventories and goods movements, but also information about the product life cycle. For example, 2D codes can be used to ensure that perishable goods are removed and delivered in good time before the best-before date expires. In practice, this is done by the software specifically generating a warning as soon as the expiry date approaches.
This not only reduces food waste, but can also make an important contribution to customer satisfaction by ensuring the quality and freshness of the product. The same principle applies to products that require special storage conditions: As soon as it is noted in the product information that a maximum storage temperature must not be exceeded, the system can specifically check whether the prescribed conditions in the warehouse are being met.
The central role of GTIN in the new era
“The Global Trade Item Number remains the central key for identifying each individual item, even with 2D codes,” emphasize GS1 managers. Despite the wealth of additional information, the GTIN is still the basis for clearly identifying the product. In combination with the expanded data, a kind of digital profile of the item is created that can be queried at every relevant step in the supply chain.
This is precisely where the aspect of traceability becomes more important: If there is a recall or a quality problem, each affected individual item can be quickly identified and removed from circulation thanks to the saved batch or serial numbers. This saves time, costs and, above all, protects consumers' trust in the brand.
Challenges and requirements for companies
Many companies are wondering how complex the transition will be. Since GS1 is a global organization, it's a process that everyone involved along the value chain must support – from producers to logistics service providers to retailers.
“The change primarily affects the technology and software with which barcodes are printed, recorded and processed,” explain industry insiders. Some warehouse management systems are already up to date and can read 2D codes without any problems. Other systems must be adapted to the additional data fields. It may also be necessary to purchase new printers or scanners that meet the higher resolution and reading speed requirements.
Internal processes and the training concept for employees also play a central role: only if everyone involved understands the potential of the new standards and is able to use the technology correctly can the desired gain in efficiency be achieved.
Improving automation and networking
A significant benefit lies in the better automation and networking of different systems. As warehouse management systems, merchandise management solutions and external partners communicate with each other via standardized GS1 interfaces, an information flow is created that connects all links in the chain.
“Automated queries about the inventory situation and availability will fundamentally change everyday work in logistics,” is how visionaries in the industry put it. This also means that when a delivery is received, it is automatically checked whether the goods actually correspond to the information on the delivery note. Discrepancies can be identified and reported immediately. This not only saves time, but also reduces the error rate.
Advantages of increased transparency through 2D codes
In addition to the direct improvements in inventory management, the increased transparency for customers is also a crucial factor. More and more end consumers want information about the origin of products, their production and composition. When this data is stored in 2D code, it can be verified at any point in the supply chain. Some people are even thinking about making this information available directly on the product. However, the prerequisite for this is that data protection is maintained and there is a clear separation between internal company data and information visible to outsiders. “Transparency must not come at the expense of a company’s know-how,” is a frequently expressed objection. For this reason, 2D codes are usually structured so that only certain data segments can be freely read, while other areas can remain password-protected or encrypted.
Challenges when introducing 2D codes
Despite the advantages, there are also some challenges. On the one hand, new technologies are always associated with investment costs, which poses financial questions, especially for small and medium-sized companies. “Is the switch worth it?” many people ask themselves. The answer is: yes, in the long term it is worth it. The added value through optimized processes, reduced error rates, faster inventory updates and more effective warehouse utilization usually significantly outweighs the initial costs. In addition, some major customers or logistics partners may require the use of 2D codes in the future in order to be able to continue working together as a group. It is therefore advisable to prepare for the new standards at an early stage in order not to risk any competitive disadvantages.
Ensuring data security when dealing with 2D codes
Another critical point is data security. Anyone who stores extensive product and batch data in a barcode must ensure that only authorized people or systems have access to it. The same applies to the warehouse management software that evaluates this data. Comprehensive security concepts are required here, from encrypted transmission paths to clearly defined user roles and access authorizations. Companies should definitely ensure that their IT infrastructure can meet these requirements in order to avoid data loss, manipulation or unauthorized insights.
Perspective: Automation and intelligent networking
However, the changes outlined here are just the beginning. With increasing digitalization and the trend towards Industry 4.0 approaches, warehouse management will become increasingly automated and intelligently networked. Robots can independently identify products based on 2D barcodes and transport them to the correct storage locations. Shelving systems equipped with sensors communicate with warehouse management systems and report when a storage compartment becomes empty or conditions violate regulations. Artificial intelligence could carry out analyzes in real time and trigger automated ordering processes as soon as defined minimum quantities are exceeded. “The future belongs to integrated and self-learning systems” is a credo that is becoming increasingly established in numerous companies. And Sunrise 2027 creates an important basis for exactly this by setting international standards that can be understood and used by everyone involved.
Procedure for practical implementation
For practical implementation, it is recommended to proceed step by step. First, companies should take stock of their current barcode system and existing hardware. It is then clarified which data should actually be stored in the 2D codes. Not every company necessarily needs the full range of product information. It is crucial that all data necessary for efficient warehouse and supply chain management is recorded and provided in high quality. The technical rollout then follows: new printing and reading devices as well as corresponding software updates must be integrated. Here it is advisable to work closely with technology partners and suppliers who are already familiar with the GS1 standards and can offer training if necessary. Ultimately, continuous improvement is an important aspect: Once the system is up and running, processes can be further refined and additional functions can be used, such as tracking key figures or integrating into a customer relationship management system (CRM).
Sunrise 2027 as a driver for change in warehouse and supply chain transparency
In summary, it shows that the GS1 Sunrise 2027 initiative goes far beyond a purely technical switch from 1D to 2D barcodes. It's about realigning the entire warehouse and supply chain processes, aiming for greater transparency, automation and accuracy. The GTIN remains the backbone of product identification, while expanded information in the codes themselves ensures improved traceability and more efficient inventory management. “If we don’t adapt our processes now, we will no longer be competitive in a few years,” say leading managers from trade and industry. Early implementation is therefore essential in order to fully benefit from the new standards and to identify potential stumbling blocks in good time.
Ultimately, it can be said that the switch to 2D codes and the consistent use of the GTIN in conjunction with extended product data make a lasting contribution to modernizing warehouse management. Companies benefit from significantly improved efficiency, lower error rates, transparent supply chain management and higher customer satisfaction. Anyone who approaches this step with careful planning and makes the necessary investments in technology and employee training will lay the foundation for a smooth future in an increasingly connected world. “Sunrise 2027 marks not only a technical, but above all a cultural change in the global merchandise economy,” says many conversations among industry experts. And this change has the potential to shape the entire market for warehouse and logistics processes in the long term.
Xpert.plus warehouse optimization – high -bay warehouse such as pallet warehouse advice and planning
We are there for you – advice – planning – implementation – project management
☑️ SME support in strategy, consulting, planning and implementation
☑️ Creation or realignment of the digital strategy and digitalization
☑️ Expansion and optimization of international sales processes
☑️ Global & Digital B2B trading platforms
☑️ Pioneer Business Development
I would be happy to serve as your personal advisor.
You can contact me by filling out the contact form below or simply call me on +49 89 89 674 804 (Munich) .
I'm looking forward to our joint project.
Xpert.digital – Konrad Wolfenstein
Xpert.Digital is a hub for industry with a focus on digitalization, mechanical engineering, logistics/intralogistics and photovoltaics.
With our 360° business development solution, we support well-known companies from new business to after sales.
Market intelligence, smarketing, marketing automation, content development, PR, mail campaigns, personalized social media and lead nurturing are part of our digital tools.
You can find more at: www.xpert.digital – www.xpert.solar – www.xpert.plus