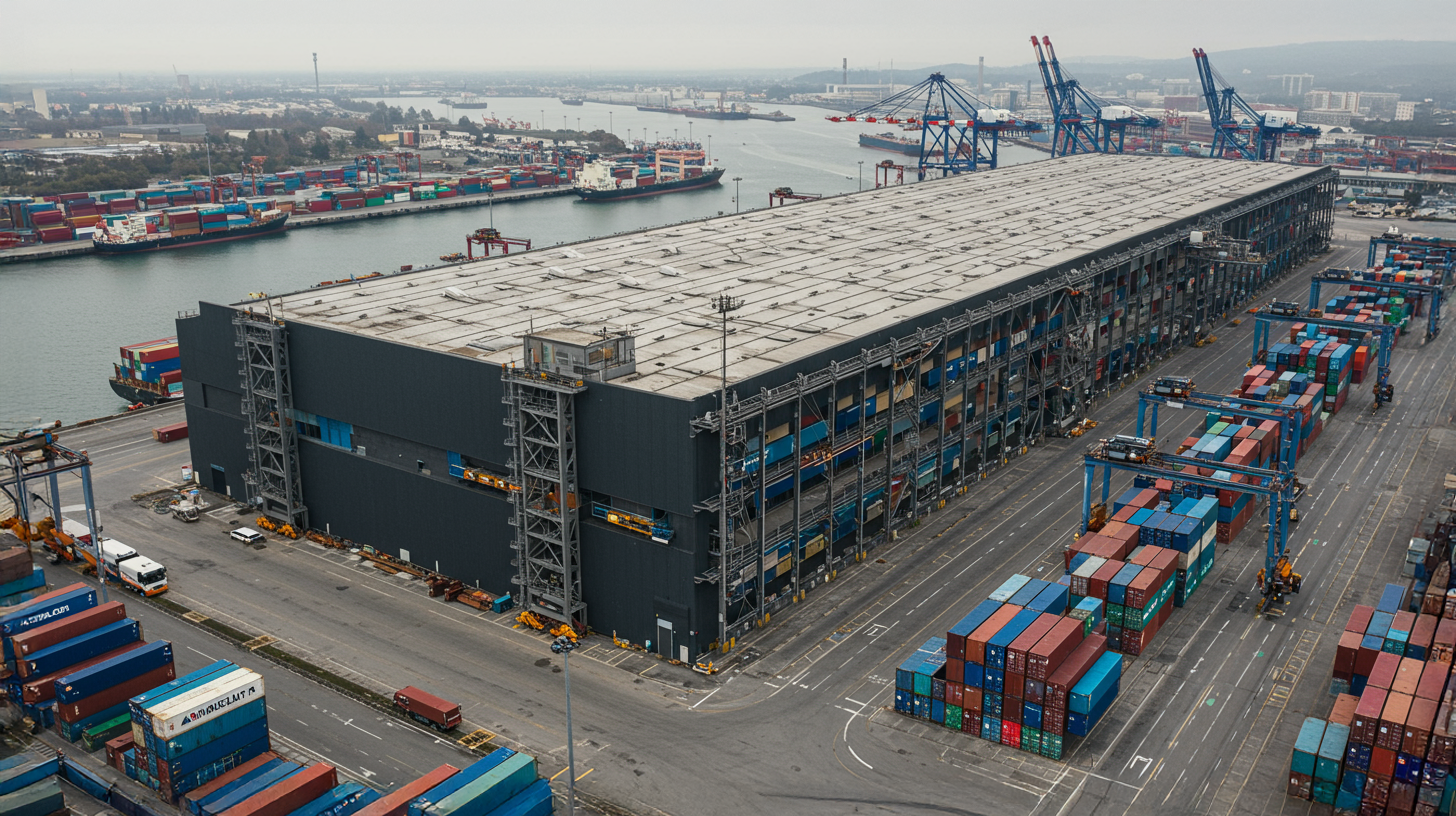
Die simple wie evolutionär gewachsene Idee vom Container-Regallager: Ein Paradigmenwechsel in der globalen Logistik – Kreativbild: Xpert.Digital
Das Bücherregal für Container: Wie eine simple Idee die weltweiten Häfen für immer verändert – Warum diese deutsche Erfindung die größte Verschwendung in Häfen beendet
Was ist eigentlich ein Container-Regallager und warum sprechen Experten von einer Revolution?
Ein Container-Regallager, auch als Container-Hochregallager oder High-Bay Storage (HBS) bezeichnet, ist im Grunde eine einfache und zugleich geniale Idee: Anstatt Container traditionell übereinanderzustapeln, werden sie in einem vollautomatisierten Regalsystem gelagert, ähnlich wie in einem riesigen Bücherregal. Jeder Container erhält dabei seinen eigenen festen Lagerplatz in einem bis zu 50 Meter hohen Stahlregal und kann jederzeit direkt zugegriffen werden, ohne dass andere Container bewegt werden müssen.
Die Revolutionäre Natur dieser Technologie liegt in ihrer scheinbaren Schlichtheit. Während wir heute selbstverständlich davon ausgehen, dass jedes Buch in einer Bibliothek seinen festen Platz hat und sofort auffindbar ist, war dies in der Containerlogistik bislang undenkbar. Container wurden stets gestapelt, blockiert und umständlich umgeschichtet. Das Container-Hochregallager beendet diese Ineffizienz ein für alle Mal.
Wie entstand diese scheinbar einfache Idee und was macht sie so innovativ?
Die Wurzeln des Container-Hochregallagers liegen ironischerweise nicht in der Hafenlogistik, sondern in der Schwerindustrie. Die deutsche SMS Group entwickelte seit Jahrzehnten vollautomatisierte Hochregallager für bis zu 50 Tonnen schwere Metallcoils in Stahlwerken. Diese bewährte Technologie wurde in einem Joint Venture mit DP World aus Dubai für Container adaptiert und zum BOXBAY-System weiterentwickelt.
Das Innovative liegt in der Übertragung einer etablierten Industrietechnik auf ein völlig neues Anwendungsfeld. Wo andere Komplexität sahen, erkannten die Entwickler eine einfache Analogie: Ein 40-Tonnen-Container ist letztendlich nur ein anderes schweres Lagergut, das präzise gehandhabt werden muss. Die jahrzehntelange Erfahrung mit Regalbediengeräten, automatisierten Kranen und Lagerverwaltungssystemen konnte direkt auf die Hafenlogistik übertragen werden.
Warum ist diese Technologie gerade jetzt so relevant für die Hafenlogistik?
Die Antwort liegt in den fundamentalen Herausforderungen, denen Häfen weltweit gegenüberstehen. Der globale Containerumschlag wächst kontinuierlich – 2024 wurden weltweit rund 161 Millionen TEU umgeschlagen, ein Plus von 6,2 Prozent gegenüber dem Vorjahr. Gleichzeitig sind die meisten großen Seehäfen historisch gewachsen und befinden sich in dicht besiedelten städtischen Gebieten, wo eine horizontale Flächenerweiterung praktisch unmöglich ist.
Diese Flächenknappheit führt zu einem Teufelskreis: Häfen müssen Container immer dichter stapeln, was die operative Effizienz dramatisch verschlechtert. In traditionellen Container-Yards müssen zwischen 30 und 60 Prozent aller Kranbewegungen als unproduktive “Reshuffling”-Bewegungen durchgeführt werden. Das bedeutet, dass Container nur bewegt werden, um an darunterliegende Container zu gelangen – pure Verschwendung von Zeit, Energie und Ressourcen.
Wie funktioniert die traditionelle Containerlagerung und wo liegen ihre Grenzen?
In herkömmlichen Container-Yards werden Container in Blöcken direkt übereinandergestapelt, meist fünf bis sechs Lagen hoch. Wenn ein bestimmter Container benötigt wird, der sich nicht an der obersten Position befindet, müssen alle darüberliegenden Container zunächst mit Kranen entfernt und zwischengelagert werden. Erst dann kann der gewünschte Container entnommen werden, woraufhin die umgelagerten Container oft wieder zurückbewegt werden müssen.
Diese “Reshuffling”-Problematik wird mit zunehmender Auslastung exponentiell schlimmer. Sobald ein Lagerblock zu mehr als 70-80 Prozent gefüllt ist, bricht die Leistung zusammen, da immer mehr unproduktive Bewegungen erforderlich werden. Das führt zu unvorhersehbaren Wartezeiten für LKW-Fahrer, ineffizientem Energieverbrauch und einer schlechten Planbarkeit der Terminaloperationen.
Zusätzlich begrenzt die Notwendigkeit des Umstapelns die maximale Stapelhöhe. Während theoretisch höher gestapelt werden könnte, wird dies durch die Zugänglichkeitsproblematik praktisch unmöglich. Moderne RTG-Kräne schaffen maximal 5-6 Lagen, was die Flächeneffizienz drastisch begrenzt.
Was macht das Container-Hochregallager so grundlegend anders?
Das Container-Hochregallager löst diese fundamentalen Probleme durch einen Paradigmenwechsel: Statt Container zu stapeln, erhält jeder Container seinen eigenen festen Lagerplatz in einem Regal. Vollautomatisierte Regalbediengeräte können jeden Container jederzeit direkt erreichen, ohne andere Container bewegen zu müssen. Dies führt zu einer 100-prozentigen Direktzugänglichkeit – das Reshuffling gehört der Vergangenheit an.
Die Technologie ermöglicht eine Verdreifachung der Lagerkapazität auf der gleichen Grundfläche. Während traditionelle Systeme meist nur 3-4 Container übereinander stapeln können, erreichen Container-Hochregallager Höhen von 7 bis 18 Lagen. Das BOXBAY-System in Dubai beispielsweise lagert Container auf bis zu 11 Ebenen bei einer Gesamthöhe von 50 Metern.
Welche konkreten Leistungsdaten zeigen die Überlegenheit dieser Technologie?
Die Proof-of-Concept-Anlage von BOXBAY im Hafen von Dubai liefert beeindruckende Zahlen. Nach über 200.000 Containerbewegungen seit der Inbetriebnahme wurden die ursprünglichen Leistungserwartungen nicht nur erreicht, sondern übertroffen. Das System erwies sich als schneller und energieeffizienter als ursprünglich angenommen.
Die erste kommerzielle Implementierung im südkoreanischen Hafen Busan wird 350.000 unproduktive Bewegungen pro Jahr eliminieren und die LKW-Abfertigungszeit um 20 Prozent verbessern. Bei einer Anlage mit 792 Containerstellplätzen entspricht dies einer enormen Effizienzsteigerung.
Die Flächeneffizienz ist bemerkenswert: Ein Container-Hochregallager benötigt nur ein Drittel der Grundfläche eines konventionellen Containerlagers mit vergleichbarer Kapazität. Dies ermöglicht es Häfen, ihre Kapazität massiv zu erweitern, ohne neue Flächen erschließen zu müssen – ein entscheidender Vorteil in flächenbegrenzten Hafenstädten.
Wie wirkt sich diese Technologie auf die Nachhaltigkeit aus?
Container-Hochregallager bieten erhebliche Umweltvorteile. Die Stromversorgung erfolgt über Solarzellen auf dem Anlagendach, wodurch das System energieautark betrieben werden kann. Die vollautomatisierten, elektrisch betriebenen Regalbediengeräte sind deutlich energieeffizienter als dieselbetriebene Portalkräne.
Der Wegfall unproduktiver Reshuffling-Bewegungen reduziert den Energieverbrauch dramatisch. Wenn 30-60 Prozent aller Kranbewegungen entfallen, sinkt auch der Energiebedarf entsprechend. Zusätzlich führt die höhere Flächeneffizienz zu weniger Landverbrauch und geringeren Infrastrukturkosten.
Die Lärmemissionen werden durch die geschlossene Bauweise und elektrische Antriebe erheblich reduziert. Container sind vor direkter Sonneneinstrahlung geschützt, was besonders für Kühlcontainer vorteilhaft ist und Energie spart. Das System ist wetterresistent und kann bei Wind, Regen und Schnee betrieben werden, während traditionelle Kranbetrieb oft wetterbedingt eingestellt werden muss.
Automatisierte Häfen der Zukunft: Revolutionäre Lagertechnologie im Check
Welche historischen Parallelen gibt es zu dieser technologischen Revolution?
Die Container-Hochregallager-Technologie steht in einer direkten historischen Linie zur ursprünglichen Container-Revolution von Malcolm McLean. 1956 verließ das erste Containerschiff “Ideal X” mit 58 Containern den Hafen von Newark nach Houston und revolutionierte den Welthandel. McLean erkannte damals, dass die zeitaufwändige Stückgutverladung durch standardisierte Container ersetzt werden musste.
Wie McLeans Innovation wurde auch die Container-Hochregallager-Technologie zunächst skeptisch betrachtet. “Wenn wir auf die Geschichte des Containers zurückblicken, hat sich seit seiner Einführung 1956 nichts Wesentliches geändert”, konstatierte Carsten Heide von AMOVA. Das Container-Hochregallager stellt die erste fundamentale Weiterentwicklung der Container-Handhabung seit über 65 Jahren dar.
Beide Innovationen folgten demselben Prinzip: Eine bewährte Technologie aus einem anderen Bereich wurde auf die Logistik übertragen. McLean adaptierte das Konzept des Wechselbrückentransports von der Straße auf das Schiff. Container-Hochregallager übertragen die Hochregallager-Technologie aus der Industrielogistik auf die Hafenlogistik.
Wie entwickelt sich die Markteinführung und wo stehen wir heute?
Die Markteinführung verläuft planmäßig und beschleunigt sich. Nach dem erfolgreichen Praxistest in Dubai folgte 2023 der erste kommerzielle Vertrag für den Hafen Busan in Südkorea. Dies markierte den Übergang von der Proof-of-Concept-Phase zur kommerziellen Marktdurchdringung.
Die SMS Group wurde 2022 mit dem Deutschen Logistik-Preis für die BOXBAY-Technologie ausgezeichnet. Die Jury würdigte besonders die Kombination aus Innovation und Nachhaltigkeit: “Wir sehen eine Verdichtung von Containerflächen auf ein Drittel, Lärm- und Lichtschutz, Stromerzeugung über den eigenen Bedarf hinaus”.
Der Markt entwickelt sich von vereinzelten Pilotprojekten zu einem eigenständigen, schnell wachsenden Marktsegment. Verschiedene Hersteller bringen eigene Systeme auf den Markt, von serienreifen Marktführern wie BOXBAY bis hin zu spezialisierten Nischenlösungen für Kühlcontainer oder militärische Anwendungen.
Welche Herausforderungen müssen noch überwunden werden?
Die größte Herausforderung liegt in der Überwindung der Trägheit etablierter Systeme. Hafenbetreiber haben über Jahrzehnte in traditionelle Krantechnik und Infrastruktur investiert. Ein vollständiger Systemwechsel erfordert nicht nur hohe Anfangsinvestitionen, sondern auch ein komplettes Umdenken in der Betriebsführung.
Interessant ist deshalb der Ansatz von Konecranes-AMOVA mit ihrem “SideGrid Retrofit”-Konzept. Anstatt komplett neue Anlagen zu bauen, werden bestehende Container-Yards schrittweise modernisiert und mit HBS-Regalstrukturen ergänzt. Dies ermöglicht eine graduelle Transformation ohne gigantische Anfangsinvestitionen.
Die Personalqualifikation stellt eine weitere Herausforderung dar. Container-Hochregallager erfordern andere Fähigkeiten als traditionelle Kranoperationen. Gleichzeitig bieten sie aber auch bessere Arbeitsbedingungen durch ergonomische Arbeitsplätze und geringere Wetterabhängigkeit.
Wie verändert diese Technologie die gesamte Logistikkette?
Container-Hochregallager ermöglichen eine neue Form der integrierten Logistik. Das HBS kann physisch direkt an Lagerhäuser oder Produktionslinien angebaut werden, wodurch der Zwischentransport per LKW entfällt. Der Container wird vollautomatisch aus dem Regal an eine bestimmte Laderampe oder Fördertechnikschnittstelle transportiert.
Dies führt zu einer nahtlosen Kette vom Schiff bis zur Produktionslinie als einen einzigen, automatisierten und datengesteuerten Prozess. Die Zeitersparnis ist erheblich: keine Wartezeiten für LKW, keine Staus im Hafen, keine Transportkosten für den “letzten Kilometer”.
Die Digitalisierung spielt dabei eine Schlüsselrolle. Container-Hochregallager sind vollständig digitale Systeme mit Energiemanagement, Warehouse Management System und Business Intelligence Modulen. Sie können mit jedem bestehenden Terminal Operating System (TOS) integriert werden und bieten vollständige Transparenz über die Position jedes Containers.
Welche Rolle spielt künstliche Intelligenz in der Zukunft der Hafenlogistik?
Die Kombination von Container-Hochregallagern mit KI-Technologien eröffnet völlig neue Möglichkeiten. KI kann Containerströme vorhersagen, Wartungsbedarfe erkennen und Betriebsabläufe optimieren. Die vollständige Digitalisierung des Container-Hochregallagers schafft die ideale Datenbasis für KI-Anwendungen.
In Hamburg testen bereits Projekte wie “Pin-Handling-mR” den Einsatz autonomer Roboter für Containeroperationen. Mobile Roboter übernehmen das Umsetzen von Arretierungszapfen an Containerzügen und beweisen, dass auch bislang rein manuelle Tätigkeiten automatisiert werden können.
Die Vision der “Smart Ports” wird durch Container-Hochregallager realisierbar. Häfen werden zu intelligenten, vernetzten Systemen, die autonom auf Veränderungen reagieren können. 5G-Technologie ermöglicht dabei die notwendige Echtzeitkommunikation zwischen allen Systemkomponenten.
Warum ist diese Entwicklung evolutionär und nicht nur eine weitere technische Neuerung?
Container-Hochregallager sind evolutionär, weil sie das fundamentale Problem der Containerlogistik lösen: den Zielkonflikt zwischen Flächeneffizienz und operativer Effizienz. Seit der Erfindung des Containers 1956 wurde dieser Grundkonflikt nie aufgelöst, sondern nur durch immer komplexere Kranoperationen und Hofstrategien verwaltet.
Die Evolution zeigt sich auch in der schrittweisen Erweiterung der Anwendungsbereiche. Was als Lösung für Metallcoils begann, wird nun für Container, Luftfracht-ULDs und sogar militärische Anwendungen genutzt. Die Technologie entwickelt sich von einer Nischenlösung zu einer universellen Plattform für automatisierte Lagersysteme.
Die gesellschaftliche Evolution ist ebenso bedeutsam. Container-Hochregallager ermöglichen es, Häfen näher an städtische Gebiete zu integrieren, ohne die Anwohner durch Lärm und Emissionen zu belasten. Sie schaffen bessere Arbeitsbedingungen und reduzieren die physische Belastung der Hafenarbeiter.
Wie wird diese Technologie die globale Logistik in den nächsten Jahren verändern?
Die Auswirkungen werden tiefgreifend sein. Container-Hochregallager werden die Kapazitätsengpässe der Häfen auflösen und damit das Wachstum des Welthandels weiter ermöglichen. Die drastische Effizienzsteigerung wird die Transportkosten senken und neue Handelsrouten wirtschaftlich machen.
Die Technologie wird sich zunächst in flächenbegrenzten Häfen durchsetzen, wo der Kostendruck am höchsten ist. Von dort wird sie sich auf alle großen Containerterminals ausbreiten. Hybrid-Lösungen wie das Retrofit-Konzept werden den Übergang erleichtern und beschleunigen.
Langfristig werden Container-Hochregallager zum neuen Standard werden, genau wie Container heute selbstverständlich sind. Die nächste Generation von Hafenarbeitern wird sich gar nicht mehr vorstellen können, dass Container einmal mühsam umgestapelt werden mussten.
Was bedeutet das für die Zukunft des Welthandels?
Container-Hochregallager sind mehr als nur eine technische Innovation – sie sind ein Paradigmenwechsel, der die Grundlagen der globalen Logistik neu definiert. Wie Malcolm McLeans Container vor 70 Jahren machen sie das Unmögliche möglich: eine weitere Effizienzrevolution im Welthandel.
Die simple Idee, Container wie Bücher in einem Regal zu lagern, löst Probleme, die als unlösbar galten. Sie beendet die Ära des Reshuffling, überwindet Flächengrenzen und schafft die Basis für vollautomatisierte, intelligente Häfen der Zukunft.
Die Evolution ist bereits im Gange. Was in Dubai als Experiment begann, wird in Busan zur Realität und bald weltweit zum Standard. Container-Hochregallager sind nicht die Zukunft der globalen Logistik – sie sind ihre Gegenwart. Die Frage ist nicht mehr, ob sie sich durchsetzen werden, sondern nur noch, wie schnell die Transformation erfolgt.
In einer Welt, die immer enger vernetzt und von Geschwindigkeit getrieben ist, bieten Container-Hochregallager genau das, was die globale Wirtschaft braucht: mehr Effizienz, weniger Ressourcenverbrauch und die Möglichkeit, auch in begrenzten Räumen zu wachsen. Sie sind die evolutionäre Antwort auf die Herausforderungen des 21. Jahrhunderts – einfach, elegant und unvermeidlich.
Ihr globaler Marketing und Business Development Partner
☑️ Unsere Geschäftssprache ist Englisch oder Deutsch
☑️ NEU: Schriftverkehr in Ihrer Landessprache!
Gerne stehe ich Ihnen und mein Team als persönlicher Berater zur Verfügung.
Sie können mit mir Kontakt aufnehmen, indem Sie hier das Kontaktformular ausfüllen oder rufen Sie mich einfach unter +49 89 89 674 804 (München) an. Meine E-Mail Adresse lautet: wolfenstein∂xpert.digital
Ich freue mich auf unser gemeinsames Projekt.