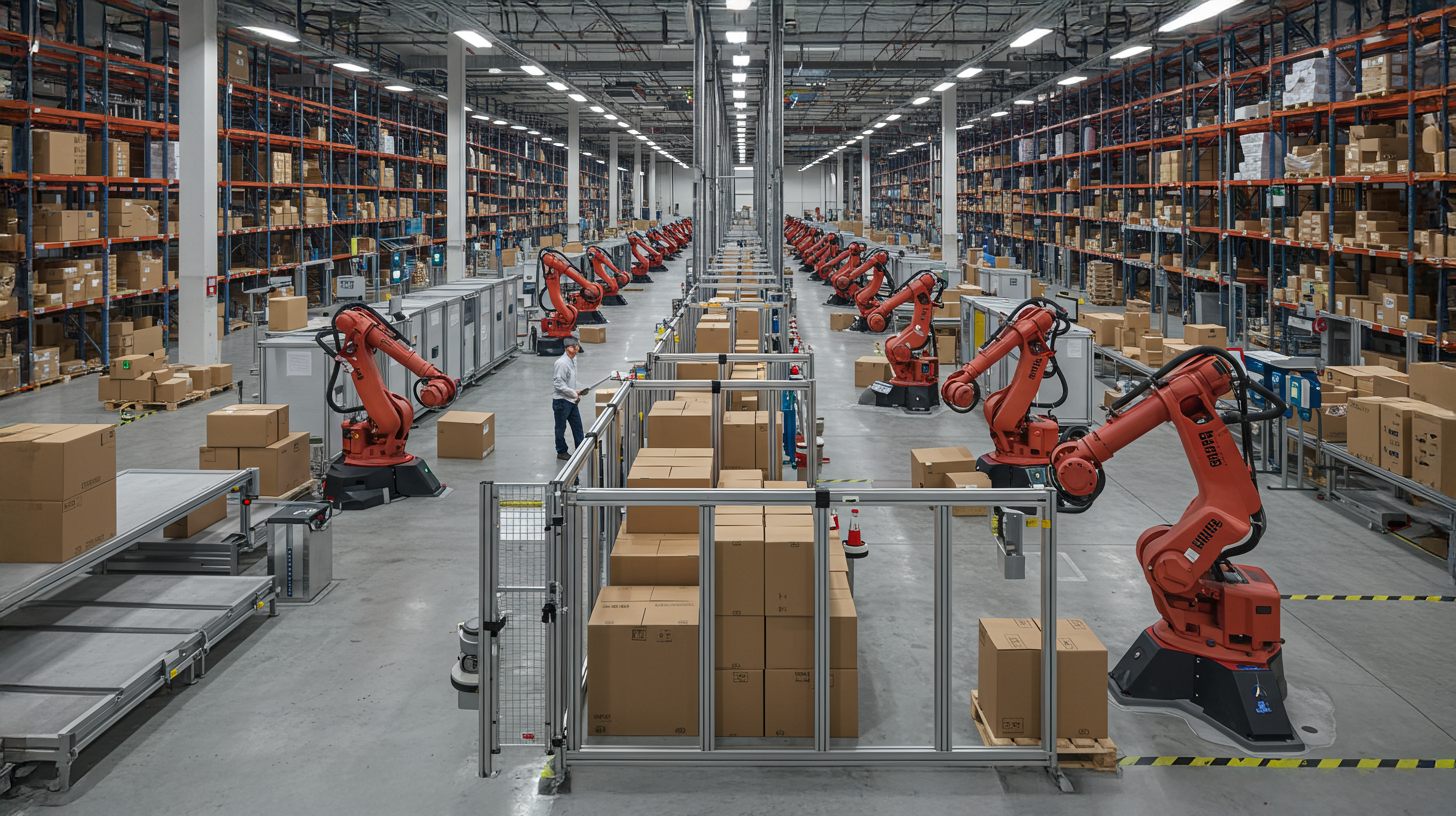
Arbeitskräftemangel? AS/RS und Lagerautomatisierung: Der Schlüssel zu 85% mehr Kapazität und massiven Kostenersparnissen – Kreativbild: Xpert.Digital
Vom Kostenfaktor zur strategischen Ressource: Moderne Lagertechnologien
Lieferketten-Transformation: 5 Schlüssel zur Agilität
In der heutigen dynamischen Wirtschaftslandschaft stehen Unternehmen vor der gewaltigen Aufgabe, ihre Lieferketten agiler, effizienter und widerstandsfähiger zu gestalten. Das Lager, einst ein reiner Kostenfaktor, rückt dabei ins Zentrum strategischer Überlegungen. Die Automatisierung, insbesondere durch den Einsatz von Automatisierten Lager- und Bereitstellungssystemen (AS/RS), ist nicht länger eine futuristische Vision, sondern eine betriebliche Notwendigkeit. Dieser Artikel dient als eine tiefgehende Untersuchung, die darauf abzielt, jeden kritischen Aspekt der AS/RS-Technologie und ihres umgebenden Ökosystems zu beleuchten. Ziel ist es, strategischen Entscheidungsträgern eine fundierte, datengestützte Grundlage für eine der wichtigsten Investitionen in der modernen Intralogistik zu bieten.
Der strategische Imperativ für die Lagerautomatisierung
Warum ist die Automatisierung von Lagerhäusern, insbesondere durch AS/RS, zu einem so kritischen und dringenden Thema für moderne Unternehmen geworden?
Die Dringlichkeit, die Lagerautomatisierung voranzutreiben, resultiert aus dem Zusammentreffen mehrerer fundamentaler und unumkehrbarer Marktkräfte. Diese Kräfte wirken zusammen und erzeugen einen operativen Druck, dem manuelle Prozesse kaum noch standhalten können.
Erstens erleben wir ein beispielloses Wachstum im Logistiksektor. Der globale Markt für Lagerhaltung und Distribution wird bis 2026 voraussichtlich ein Volumen von 650 Milliarden US-Dollar erreichen, angetrieben von einer robusten jährlichen Wachstumsrate von etwa 8 %. Dieses Wachstum allein erfordert eine massive Skalierung der Kapazitäten, die mit traditionellen Methoden nur schwer zu realisieren ist.
Zweitens ist der E-Commerce-Boom der entscheidende Katalysator für eine strukturelle Veränderung der Anforderungen. Bis 2025 wird erwartet, dass der E-Commerce 22 % des weltweiten Einzelhandelsumsatzes ausmacht. Dies verändert die Auftragsprofile radikal: Anstelle von großen Palettenlieferungen an wenige Filialen müssen Fulfillment-Center nun eine immense Anzahl kleinerer, komplexerer Aufträge mit kürzeren Lieferfristen an einzelne Endkunden abwickeln. Diese Komplexität wird durch die Tatsache verschärft, dass E-Commerce-Fulfillment bis zu dreimal mehr Lagerfläche benötigt als die traditionelle Einzelhandelslogistik, was die Raumoptimierung zu einer absoluten Priorität macht. Infolgedessen planen 40 % der Unternehmen, in Automatisierung zu investieren, um dieser Nachfrage gerecht zu werden.
Drittens agieren Unternehmen in einem zunehmend angespannten Arbeitsmarkt. Steigende Arbeitskosten und ein akuter Mangel an verfügbaren Arbeitskräften für repetitive und körperlich anstrengende Lagertätigkeiten stellen eine erhebliche operative Hürde dar. Fast 60 % der Lagerbetreiber planen daher in den nächsten zwei Jahren gezielte Investitionen in Automatisierungstechnologien wie AS/RS und Robotik, um die Produktivität zu steigern und die Abhängigkeit von einem schrumpfenden Arbeitskräftepool zu verringern.
Schließlich hat die COVID-19-Pandemie die Fragilität globaler Lieferketten offengelegt und die Notwendigkeit von Resilienz in den Vordergrund gerückt. Unternehmen erkennen, dass Automatisierung ein Schlüsselfaktor zur Stärkung ihrer Lieferketten ist. Sie reduziert die Anfälligkeit gegenüber Arbeitskräfteausfällen und ermöglicht eine schnelle Anpassung an unvorhersehbare Nachfrageschwankungen, wie sie während der Pandemie zu beobachten waren.
Diese vier Kräfte – Marktwachstum, E-Commerce-Komplexität, Arbeitskräftemangel und der Ruf nach Resilienz – bilden eine “operative Zange”, die manuelle Prozesse zunehmend unhaltbar macht. Die Automatisierung durch AS/RS ist somit keine optionale Effizienzmaßnahme mehr, sondern eine strategische Notwendigkeit, um die operative Handlungsfähigkeit zu sichern und im Wettbewerb zu bestehen. Die Investition wandelt sich von einer reinen Kostensenkungsmaßnahme zu einem entscheidenden Wegbereiter für Geschäftswachstum und Kundenzufriedenheit.
Was genau ist ein Automatisiertes Lager- und Bereitstellungssystem (AS/RS) und welche fundamentalen Vorteile verspricht es?
Ein Automatisiertes Lager- und Bereitstellungssystem, kurz AS/RS, ist ein computergesteuertes System, das die Ein- und Auslagerung von Waren mit minimalem menschlichen Eingriff durchführt. Es stellt eine hochentwickelte Kombination aus Hardware und Software dar. Die Hardware umfasst typischerweise Regalstrukturen, Regalbediengeräte (RBGs), Shuttles, Roboter und Fördertechnik, während die Software aus Lagersteuerungs- (WCS), Lager-Ausführungs- (WES) und Lagerverwaltungssystemen (WMS) besteht, die alle Aktivitäten koordinieren.
Die fundamentalen Vorteile eines AS/RS lassen sich in mehreren Schlüsselbereichen zusammenfassen, die weit über eine einfache Effizienzsteigerung hinausgehen:
- Effektive Raumnutzung: Der vielleicht offensichtlichste Vorteil ist die drastische Verbesserung der Lagerdichte. Durch die Nutzung der vertikalen Höhe eines Gebäudes maximieren AS/RS die Lagerkapazität auf einer gegebenen Grundfläche. Dies reduziert den Bedarf an teuren Gebäudeerweiterungen oder zusätzlichen Standorten.
- Erhöhte Durchsatzleistung: Durch die Automatisierung der Ein- und Auslagerungsprozesse können AS/RS ein deutlich höheres Volumen an Waren pro Stunde bewegen als manuelle Systeme. Dies ist entscheidend, um Spitzenlasten abzufedern und schnelle Lieferzeiten zu gewährleisten.
- Verbesserte Kommissioniergenauigkeit: Menschliche Fehler bei der Kommissionierung sind eine der Hauptursachen für Kosten und Kundenunzufriedenheit. AS/RS arbeiten mit computergesteuerter Präzision, was zu einer nahezu fehlerfreien Auftragszusammenstellung führt.
- Verbesserte Ergonomie und Sicherheit: AS/RS übernehmen körperlich anstrengende, repetitive und potenziell gefährliche Aufgaben wie das Heben schwerer Lasten oder das Arbeiten in großen Höhen. Dies reduziert das Risiko von Arbeitsunfällen und verbessert die Arbeitsbedingungen für die Mitarbeiter erheblich.
- Gesteigerte Produktsicherheit und Bestandskontrolle: Die Systeme bieten einen kontrollierten Zugriff auf die Waren und eine exakte, softwaregestützte Nachverfolgung jeder einzelnen Lagerbewegung. Dies minimiert das Risiko von Diebstahl, Beschädigung und Bestandsdifferenzen.
- Reduzierte Arbeitskosten und -engpässe: Durch die Automatisierung wird die Abhängigkeit von manueller Arbeit signifikant verringert, was nicht nur die direkten Lohnkosten senkt, sondern auch die Anfälligkeit gegenüber Arbeitskräftemangel reduziert.
Diese Vorteile führen zu einem fundamentalen Paradigmenwechsel im Lagerbetrieb. Das traditionelle “Person-zur-Ware”-Prinzip, bei dem Mitarbeiter weite Strecken im Lager zurücklegen, um Artikel zu kommissionieren, wird durch das “Ware-zur-Person”-Prinzip (Goods-to-Person) ersetzt. In diesem Modell bringt das AS/RS die benötigten Artikel direkt zu einem stationären, ergonomisch optimierten Arbeitsplatz. Da die Laufwege der Mitarbeiter bis zu 50 % ihrer Arbeitszeit ausmachen können, führt diese Umstellung zu einer dramatischen Produktivitätssteigerung. Die Einführung eines AS/RS ist daher mehr als nur ein Technologie-Upgrade; es ist ein Katalysator, der eine vollständige Neugestaltung und Standardisierung der Lagerprozesse erzwingt und dadurch ein völlig neues Effizienzniveau ermöglicht.
Können diese versprochenen Vorteile mit konkreten Daten untermauert werden? Welche quantitativen Leistungsverbesserungen kann ein Unternehmen realistischerweise erwarten?
Ja, die qualitativen Versprechen der AS/RS-Technologie werden durch eine beeindruckende Reihe von quantitativen Leistungsdaten gestützt, die in zahlreichen Implementierungen nachgewiesen wurden. Diese Zahlen bilden die Grundlage für jeden soliden Business Case.
Platzersparnis & Dichte: AS/RS können die Lagerkapazität durch die optimale Nutzung der vertikalen Raumhöhe um 40 % bis 80 % steigern. In einigen Konfigurationen, insbesondere bei hochdichten Systemen, kann die Lagerdichte im Vergleich zu traditionellen Regalsystemen um bis zu 85 % erhöht werden. Dies bedeutet, dass auf derselben Grundfläche fast doppelt so viele Waren gelagert werden können.
Genauigkeit: Die Präzision computergesteuerter Systeme ermöglicht eine Kommissioniergenauigkeit von 99,9 % oder sogar höher. Dieser Wert ist nicht nur eine operative Kennzahl, sondern hat tiefgreifende finanzielle Auswirkungen. Eine Reduzierung der Fehlerrate von beispielsweise 2 % (typisch für manuelle Systeme) auf 0,1 % bedeutet eine 20-fache Verringerung von kostspieligen Retouren, Nachlieferungen und unzufriedenen Kunden.
Durchsatz & Geschwindigkeit: Die Automatisierung der Ein- und Auslagerungsprozesse führt zu bis zu dreimal schnelleren Auftragsbearbeitungszeiten. Dies ermöglicht es Unternehmen, spätere Annahmeschlusszeiten für Bestellungen anzubieten (Cut-off-Zeiten), was im E-Commerce einen erheblichen Wettbewerbsvorteil darstellt.
Arbeitskosten und Produktivität: Die Reduzierung der Abhängigkeit von manueller Arbeit führt zu einer Senkung der Arbeitskosten um 40 % bis 70 %. Gleichzeitig werden Produktivitätssteigerungen von 30 % bis 50 % realisiert, da die verbleibenden Mitarbeiter an hocheffizienten “Ware-zur-Person”-Arbeitsplätzen tätig sind.
Sicherheit: Durch die Minimierung der manuellen Handhabung und der Interaktion von Menschen mit Gabelstaplern in den Gängen können Sicherheitsvorfälle und Arbeitsunfälle um bis zu 50 % reduziert werden.
Betriebszeit: AS/RS sind für den Dauerbetrieb ausgelegt und ermöglichen einen 24/7-Betrieb ohne Pausen oder Schichtwechsel, was die Auslastung des investierten Kapitals maximiert.
Return on Investment (ROI): Aufgrund dieser erheblichen Einsparungen und Leistungssteigerungen erzielen Unternehmen, die in AS/RS investieren, oft einen Return on Investment innerhalb von nur 1 bis 3 Jahren. In einem dokumentierten Fall wurde sogar ein ROI von 204 % bei einer Amortisationszeit von nur 6 Monaten erreicht.
Diese quantitativen Vorteile sind nicht isoliert zu betrachten, sondern erzeugen einen positiven Rückkopplungseffekt. Höhere Genauigkeit senkt die Kosten für die Fehlerbehebung und erhöht die Kundentreue. Ein höherer Durchsatz ermöglicht mehr Umsatzvolumen mit derselben Infrastruktur und Belegschaft. Die Kombination dieser Effekte führt nicht nur zu einem schnellen ROI, sondern schafft auch einen nachhaltigen, schwer zu kopierenden Wettbewerbsvorteil. Das Lager wird von einer reinen Notwendigkeit zu einem Motor für Rentabilität und Wachstum.
Quantifizierbare Leistungsversprechen von AS/RS-Systemen: Welche realistischen Verbesserungen sind belegbar?
Quantifizierbare Leistungsversprechen von AS/RS-Systemen: Welche realistischen Verbesserungen sind belegbar? – Bild: Xpert.Digital
Automatisierte Lagersysteme (AS/RS) bieten beeindruckende Leistungsverbesserungen in verschiedenen Unternehmensbereichen. Die Analyse der Schlüsselleistungsindikatoren (KPIs) zeigt signifikante Vorteile: In der Raumnutzung können Unternehmen die Lagerdichte um bis zu 85 % steigern und die Lagerkapazität um 40 bis 80 % erhöhen. Hinsichtlich der Effizienz ermöglichen diese Systeme eine bis zu dreifach schnellere Bearbeitungszeit und steigern die Produktivität um 30 bis 50 %.
Ein weiterer entscheidender Vorteil ist der Potenzial für einen 24/7-Betrieb, der die Durchgängigkeit der Lagerprozesse maximiert. Die Kommissioniergenauigkeit erreicht beeindruckende 99,9 % und übertrifft damit manuelle Prozesse deutlich. Kostenoptimierung ist ebenfalls ein Schlüsselaspekt: Die Arbeitskosten können um 40 bis 70 % reduziert werden. Zusätzlich verbessern AS/RS-Systeme die Arbeitssicherheit durch eine Reduktion von Sicherheitsvorfällen um bis zu 50 %.
Finanziell betrachtet liegt der typische Return on Investment (ROI) zwischen ein und drei Jahren, was die langfristige wirtschaftliche Attraktivität dieser Technologie unterstreicht.
Xpert Partner in der Lagerplanung und -bau
Technologie-Upgrade: Die smarten Systeme hinter effizienter Lagerhaltung
Ein technischer Einblick: Die Anatomie moderner AS/RS-Lösungen
Was sind die primären Typen von AS/RS, und für welche spezifischen operativen Szenarien ist jeder Typ am besten geeignet?
Die Welt der Automatisierten Lager- und Bereitstellungssysteme ist vielfältig, und die Wahl des richtigen Systems hängt entscheidend von den spezifischen Anforderungen eines Betriebs ab. Es gibt kein universell “bestes” System; vielmehr stellt jede Technologie einen optimierten Kompromiss zwischen Lagerdichte, Durchsatz und Flexibilität dar. Die primären Typen lassen sich wie folgt kategorisieren:
Unit-Load AS/RS (Paletten-AKL)
Dies ist die klassische Form des AS/RS, konzipiert für die Handhabung großer und schwerer Ladeeinheiten wie Paletten oder Gitterboxen. Regalbediengeräte (RBGs) bewegen sich in schmalen Gängen und lagern die Paletten in hohen Regalen ein und aus. Dieses System ist ideal für Pufferlager in der Produktion, die Lagerung von Rohmaterialien oder die Konsolidierung von Fertigwaren, also Szenarien mit relativ wenigen Artikelvarianten (SKUs), aber hohem Volumen pro SKU.
Mini-Load AS/RS (Behälter-AKL)
Als Pendant zum Unit-Load-System ist das Mini-Load-System für die Handhabung kleiner bis mittelgroßer Artikel in standardisierten Behältern, Kartons oder auf Tablaren ausgelegt. Es ist das Rückgrat vieler “Ware-zur-Person”-Kommissionierlösungen und eignet sich hervorragend für Anwendungen mit einer sehr hohen SKU-Vielfalt und hohen Anforderungen an die Genauigkeit, wie sie im E-Commerce, in der Pharmaindustrie oder in der Ersatzteillogistik typisch sind.
Shuttle-Systeme
Diese Technologie stellt eine Weiterentwicklung des Mini-Load-Prinzips dar und bietet ein Höchstmaß an Flexibilität und Skalierbarkeit. Autonome Shuttles bewegen sich unabhängig auf jeder Ebene eines Regalsystems, während separate Lifte den vertikalen Transport übernehmen. Diese Entkopplung von horizontaler und vertikaler Bewegung ermöglicht extrem hohe Durchsatzraten. Shuttle-Systeme sind prädestiniert für hochdynamische E-Commerce-Operationen mit stark schwankenden Auftragsvolumina, da die Leistung durch einfaches Hinzufügen oder Entfernen von Shuttles angepasst werden kann. Einige Systeme bieten eine Skalierbarkeit von 100 %.
Vertikale Liftsysteme (VLM) & Karusselle
Dies sind hochdichte, gekapselte Lagerlösungen. VLMs funktionieren wie ein Schrank mit zwei Reihen von Tablaren und einem Extraktor in der Mitte, der das angeforderte Tablar zu einer ergonomischen Öffnung bringt. Karusselle rotieren entweder horizontal oder vertikal, um die gelagerten Waren zum Bediener zu bringen. Sie sind ideal für die Lagerung von Kleinteilen auf sehr begrenztem Raum, beispielsweise direkt in der Produktionslinie, in Werkstätten oder für Service-Teile.
Kubische Lagersysteme (z.B. AutoStore)
Diese Architektur bietet die höchstmögliche Lagerdichte. Roboter fahren auf einem Gitter (Grid) über einem Block aus direkt aufeinander gestapelten Behältern. Sie heben Behälter an und graben sich bei Bedarf zu tiefer liegenden Behältern durch (“Dig-Out”). Da keine Gänge benötigt werden, ist die Raumnutzung unübertroffen. Dieses System eignet sich perfekt für Anwendungen, bei denen die Maximierung der Lagerkapazität auf einer begrenzten Grundfläche oberste Priorität hat und ein mittlerer bis hoher Durchsatz gefordert ist.
Die Wahl des Systems ist eine tiefgreifende strategische Entscheidung. Sie spiegelt die Erwartungen eines Unternehmens an sein zukünftiges Geschäftsvolumen und seine Volatilität wider. Ein stabiles Produktionsumfeld könnte mit einem robusten Unit-Load-System gut bedient sein. Ein schnell wachsendes E-Commerce-Unternehmen, das sich auf unvorhersehbare Nachfragespitzen einstellen muss, wird die Skalierbarkeit und den Durchsatz eines Shuttle-Systems oder die Dichte eines kubischen Systems bevorzugen. Die Evolution dieser Systeme zeigt einen klaren Trend: weg von monolithischen, zentralisierten Architekturen (ein RBG pro Gang) hin zu dezentralisierten, resilienten und granular skalierbaren Systemen (Flotten von Shuttles oder Robotern), die besser auf die Unsicherheiten der modernen Wirtschaft vorbereitet sind.
Wenn wir tiefer in die Technologie eintauchen, wie funktionieren die mechanischen Kernkomponenten von Regalbediengeräten (in Unit-Load-Systemen) und Shuttles tatsächlich?
Um die Leistungsfähigkeit und die Limitierungen der verschiedenen AS/RS-Typen zu verstehen, ist ein Blick auf ihre mechanischen Kernkomponenten unerlässlich. Die Designphilosophien von Regalbediengeräten und Shuttles unterscheiden sich fundamental.
Regalbediengeräte (RBGs / Stacker Cranes)
RBGs sind die Arbeitspferde der traditionellen Paletten- und Behälter-AS/RS. Ihr Funktionsprinzip ist monolithisch und integriert.
Grundprinzip und Bewegungsachsen: Ein RBG ist ein hohes Mastfahrzeug, das auf einer einzelnen Schiene am Boden und oft mit einer oberen Führungsschiene am Regaldach entlang eines schmalen Ganges verfährt. Seine Bewegung erfolgt simultan in zwei Hauptachsen: horizontal entlang des Ganges (Fahrachse) und vertikal entlang des Mastes durch einen Hubschlitten (Hubachse). Die Fähigkeit, beide Bewegungen gleichzeitig auszuführen (diagonale Fahrt), ist entscheidend für die Minimierung der Zykluszeit.
Lastaufnahmemittel (LAM): Am Hubschlitten ist das LAM befestigt, das die eigentliche Ein- und Auslagerung vornimmt. Bei Palettensystemen sind dies typischerweise Teleskopgabeln, die sich einfach oder doppelt tief in die Regalfächer ausfahren, die Palette anheben und zurückziehen. Bei Mini-Load-Systemen können dies Greifer, Sauger oder kleine Teleskoptische für Behälter sein.
Mast-Design: Das Design des Mastes ist ein kritischer Faktor für die Stabilität und Leistung. Einmast-RBGs sind leichter und potenziell energieeffizienter, aber anfälliger für Schwingungen bei hohen Geschwindigkeiten oder großen Höhen, was die Positioniergenauigkeit beeinträchtigen kann. Hier ist eine ausgefeilte Steuerungstechnik zur Schwingungsdämpfung erforderlich.
Zweimast-RBGs bieten eine deutlich höhere Steifigkeit und Stabilität, was sie zur bevorzugten Wahl für sehr hohe Anwendungen (über 40 Meter) oder sehr schwere Lasten macht. Diese Stabilität wird jedoch mit einem höheren Eigengewicht und somit einem höheren Energieverbrauch für Beschleunigung und Abbremsen erkauft.
Shuttle-Fahrzeuge
Shuttle-Systeme basieren auf dem Prinzip der Dezentralisierung und der Entkopplung der Bewegungsachsen, was ihnen eine höhere Dynamik und Flexibilität verleiht.
Entkoppeltes Prinzip: Im Gegensatz zum RBG, das Fahren und Heben in einer Maschine vereint, trennt das Shuttle-System diese Funktionen.
Horizontale Bewegung: Das Shuttle selbst ist ein flaches, batteriebetriebenes und autonomes Fahrzeug. Es operiert auf Schienen innerhalb einer einzigen Ebene des Regalsystems und ist ausschließlich für die schnelle horizontale Bewegung zuständig, um Behälter oder Kartons aus den Regalfächern zu holen und an den Gang-Anfang zu bringen.
Vertikale Bewegung: Am Kopfende jedes Ganges befindet sich ein oder mehrere Hochleistungslifte. Diese nehmen ein Shuttle (oft bereits mit einem Behälter beladen) auf und transportieren es extrem schnell zwischen den verschiedenen Regalebenen und zur Anbindung an die Vorzonen-Fördertechnik, wo die Behälter an die Kommissionierplätze übergeben werden.
Diese unterschiedlichen mechanischen Ansätze haben tiefgreifende Konsequenzen. Der Engpass in einem RBG-System ist das RBG selbst; seine Zykluszeit diktiert die Leistung des gesamten Ganges. In einem Shuttle-System ist der Lift der potenzielle Engpass. Das Systemdesign zielt darauf ab, diesen Engpass optimal auszulasten, indem mehrere Shuttles den Lift quasi “füttern”. Dies macht das System nicht nur leistungsfähiger, sondern auch granular skalierbar: Benötigt man mehr Durchsatz, fügt man weitere Shuttles hinzu, bis die Kapazität des Lifts erreicht ist. Dies bietet eine Flexibilität, die ein monolithisches RBG-System nicht leisten kann.
Shuttle vs. Roboter: Welches Lagersystem wird die Industrie dominieren?
Wie schneiden die führenden Systemarchitekturen – RBG-basiert, Shuttle-basiert und kubische Lagerung – im Vergleich bei kritischen Kennzahlen wie Durchsatz, Lagerdichte und Flexibilität ab?
Die Entscheidung für eine spezifische AS/RS-Architektur erfordert eine sorgfältige Abwägung der drei zentralen Leistungsparameter: Lagerdichte, Durchsatz und Flexibilität. Jede Technologie hat hier ihre spezifischen Stärken und Schwächen.
Lagerdichte
Die Dichte gibt an, wie viele Artikel auf einer bestimmten Grundfläche gelagert werden können.
Kubische Systeme (z.B. AutoStore): Sie bieten die unangefochten höchste Lagerdichte, insbesondere in Gebäuden mit begrenzter Deckenhöhe (unter 12 Metern bzw. 40 Fuß). Da sie komplett auf Gänge verzichten und die Behälter direkt übereinander stapeln, wird praktisch kein Raum verschwendet. Sie können die Lagerkapazität im Vergleich zu manuellen Regalsystemen um das Vierfache erhöhen.
Shuttle- und RBG-Systeme: Diese Systeme erzielen ihre hohe Dichte durch extrem schmale Gänge und die Fähigkeit, die volle Gebäudehöhe (oft bis zu 25 Meter oder mehr) auszunutzen. In sehr hohen Gebäuden (über 12-15 Meter) können sie eine höhere Dichte als kubische Systeme erreichen, da letztere die vertikale Dimension nicht vollständig ausnutzen können. Die Dichte kann durch doppel- oder mehrfachtiefe Lagerung weiter erhöht werden, was jedoch den direkten Zugriff auf jeden einzelnen Artikel einschränkt und den Verwaltungsaufwand erhöht.
Durchsatz
Der Durchsatz misst die Anzahl der Ein- und Auslagerungen pro Zeiteinheit.
Shuttle-Systeme: Sie gelten als die Könige des Durchsatzes. Durch die Entkopplung der Bewegungsachsen und den parallelen Einsatz vieler Fahrzeuge erreichen sie die höchsten Leistungsraten. Sie sind die bevorzugte Wahl für “sehr hohe oder ultra-hohe” Durchsatzanforderungen, wie sie im dynamischen E-Commerce-Fulfillment an der Tagesordnung sind. Ein einzelner Lift kann bis zu 400 Behälter pro Stunde bewegen.
RBG-Systeme: Bieten einen soliden, hohen und sehr konstanten Durchsatz. Die Leistung ist jedoch durch die physikalischen Grenzen des einen Regalbediengeräts pro Gang limitiert. Ein typisches Paletten-RBG schafft etwa 40 Ein- und Auslagerungen pro Stunde. Sie eignen sich gut für stabile Prozesse mit planbar hohem Volumen.
Kubische Systeme: Erzielen einen mittleren bis hohen Durchsatz. Die Leistung ist hier sehr gut skalierbar, indem einfach mehr Roboter auf dem Grid eingesetzt und zusätzliche Kommissionier-Ports installiert werden. Ein limitierender Faktor kann die Notwendigkeit sein, obere Behälter wegzuräumen, um an tiefer gelegene zu gelangen (“Dig-Out”), was die Zykluszeit für bestimmte Aufträge verlängern kann.
Flexibilität & Skalierbarkeit
Diese Dimension beschreibt die Fähigkeit des Systems, sich an veränderte Geschäftsanforderungen anzupassen.
Shuttle- und Kubische Systeme: Bieten maximale Flexibilität. Die Durchsatzleistung kann dynamisch an das Geschäftswachstum angepasst werden, indem weitere Fahrzeuge (Shuttles oder Roboter) zur Flotte hinzugefügt werden, ohne die grundlegende Regal- oder Gitterstruktur verändern zu müssen. Dies ermöglicht eine “Pay-as-you-grow”-Investitionsstrategie.
RBG-Systeme: Sind in ihrer Skalierbarkeit deutlich eingeschränkter. Die Leistung ist fest an die Anzahl der Gänge gekoppelt. Eine signifikante Leistungssteigerung erfordert in der Regel den Bau komplett neuer Gänge, was eine große, sprunghafte Investition darstellt.
Ein entscheidender Faktor, der diese drei Dimensionen verbindet, ist die Gebäudeinfrastruktur. Die Wahl der Technologie und die Immobilienstrategie sind untrennbar miteinander verknüpft. Ein Unternehmen, das ein bestehendes Lager mit niedriger Decke nachrüsten möchte, wird wahrscheinlich die unübertroffene Dichte eines kubischen Systems bevorzugen. Ein Unternehmen, das hingegen einen Neubau auf einem teuren Grundstück plant, könnte eine extrem hohe Halle errichten, um die Grundfläche zu minimieren, und ein Shuttle-System installieren, um maximalen Durchsatz und Höhennutzung zu kombinieren.
Systemvergleich zur Flexibilität & Skalierbarkeit: Welche Lagertechnologie passt sich am besten an Wachstum und Veränderungen an?
Systemvergleich zur Flexibilität & Skalierbarkeit: Welche Lagertechnologie passt sich am besten an Wachstum und Veränderungen an? – Bild: Xpert.Digital
In der Logistik und Lagertechnologie gibt es verschiedene Systemlösungen, die sich in Flexibilität und Skalierbarkeit unterscheiden. Ein detaillierter Vergleich zeigt die Vor- und Nachteile verschiedener Lagertechnologien.
Das RBG-System (Regalbediengerät) zeichnet sich durch eine hohe Lagerdichte aus, die durch schmale Gänge und optimale Höhennutzung erreicht wird. Mit einer Höhe von bis zu 40 Metern bietet es direkten Zugriff auf jede Palette. Allerdings ist seine Skalierbarkeit begrenzt und ein Systemausfall stoppt sofort den gesamten Gang.
Shuttle-Systeme überzeugen durch sehr hohe Durchsatzraten und eine hervorragende Skalierbarkeit. Durch parallelen Betrieb mehrerer Shuttles können sie flexibel auf Veränderungen reagieren. Sie erreichen Höhen bis zu 25 Metern und bieten hohe Fehlertoleranz.
Kubische Systeme wie AutoStore sind ideal für platzbeschränkte Standorte. Sie erreichen eine extrem hohe Lagerdichte ohne Gänge und ermöglichen eine sehr hohe Skalierbarkeit durch Hinzufügen von Robotern. Die Fehlertoleranz ist sehr hoch, da ein Roboterausfall von anderen kompensiert werden kann.
Vertikale Lagersysteme (VLM) oder Karussells eignen sich besonders für Kleinteilelagerung und Produktionsinseln. Sie nutzen die volle Modulhöhe, haben aber eine niedrigere Durchsatzrate und begrenzte Skalierbarkeit.
Die Wahl des richtigen Systems hängt von spezifischen Anforderungen wie Auftragsvolumen, Platzbedarf, Prozessstabilität und Flexibilität ab.
Welche Sensortechnologien bilden das “Nervensystem” eines AS/RS, und wie gewährleisten sie das erforderliche Maß an Präzision, Sicherheit und Effizienz?
Moderne AS/RS und die mit ihnen interagierenden autonomen Roboter sind komplexe mechatronische Systeme, deren Funktion von einem ausgeklügelten “Nervensystem” aus verschiedenen Sensortechnologien abhängt. Diese Sensoren liefern die Daten, die für präzise Bewegungen, die Sicherheit von Personal und Material sowie die allgemeine Systemeffizienz unerlässlich sind.
Positionssensoren
Sie sind das Fundament für die präzise Steuerung. Ihre Aufgabe ist es, die exakte Position der beweglichen Komponenten – wie des Regalbediengeräts im Gang, des Hubschlittens am Mast oder des Shuttles auf seiner Ebene – kontinuierlich zu erfassen. Realisiert wird dies durch Technologien wie Laser-Distanzsensoren, die den Abstand zum Gangende messen, Seilzug-Encoder, die die Abwicklung eines Seils messen, oder hochpräzise lineare Messsysteme, die ein am Regal montiertes Barcode-Band ablesen. Ohne diese Millimetergenauigkeit wäre ein sicheres Anfahren der Lagerplätze unmöglich.
Distanz- und photoelektrische Sensoren
Diese Gruppe von Sensoren übernimmt eine Vielzahl von Überwachungs- und Kontrollaufgaben. Sie funktionieren wie die “Augen und Ohren” des Systems auf kurze Distanz.
Fach-Belegt-Kontrolle: Bevor eine Ladeeinheit eingelagert wird, prüft ein Sensor, ob der Zielplatz tatsächlich frei ist, um Kollisionen und Fehlbuchungen zu vermeiden.
Anwesenheitskontrolle: Sensoren an der Fördertechnik oder am Lastaufnahmemittel selbst detektieren, ob ein Behälter oder eine Palette korrekt aufgenommen wurde und vorhanden ist.
Überstandskontrolle: Eine der wichtigsten Sicherheitsfunktionen. Photoelektrische Sensoren (Lichtschranken) erzeugen einen virtuellen “Rahmen” um die Ladeeinheit. Ragt ein Teil der Ladung über diesen Rahmen hinaus, wird die Bewegung gestoppt, um eine Kollision mit der Regalstruktur zu verhindern.
Vision-Sensoren (Computer Vision)
Kamerasysteme, oft in Verbindung mit KI-Algorithmen, verleihen dem AS/RS eine Form von “Sehvermögen”. Sie gehen über die reine Anwesenheitserkennung hinaus und ermöglichen komplexere Aufgaben wie die Identifizierung von Objekten, die Überprüfung von Barcodes oder QR-Codes zur Verifizierung, die Qualitätskontrolle (z.B. Erkennung beschädigter Verpackungen) und die hochpräzise Feinpositionierung beim Anfahren eines Lagerplatzes.
LiDAR (Light Detection and Ranging)
Diese Technologie ist weniger in den schienengebundenen AS/RS selbst, aber umso mehr in den frei navigierenden Autonomen Mobilen Robotern (AMRs) zu finden, die Waren zum oder vom AS/RS transportieren. LiDAR-Sensoren scannen die Umgebung mit Laserpulsen und erstellen aus der Laufzeit des reflektierten Lichts eine präzise 2D- oder 3D-Punktwolkenkarte. Diese Karte dient dem AMR zur Navigation und zur Erkennung von Hindernissen in Echtzeit.
SLAM (Simultaneous Localization and Mapping)
SLAM ist kein Sensor, sondern ein entscheidender Algorithmus, der die Daten der Sensoren (wie LiDAR oder Kameras) verarbeitet. Er löst das “Henne-Ei-Problem” der autonomen Navigation: Um sich auf einer Karte zu lokalisieren, braucht ein Roboter eine Karte. Um eine Karte zu erstellen, muss er wissen, wo er ist. SLAM ermöglicht es dem Roboter, beides gleichzeitig zu tun – eine Karte einer unbekannten Umgebung zu erstellen und seine eigene Position innerhalb dieser Karte kontinuierlich zu verfolgen.
Die wahre Stärke moderner autonomer Systeme liegt in der Sensorfusion. Anstatt sich auf eine einzige Technologie zu verlassen, kombinieren fortschrittliche AMRs die Daten verschiedener Sensoren. Sie fusionieren beispielsweise die hochpräzisen Distanzmessungen von LiDAR (gut für die Kartierung von Wänden und großen Objekten) mit den hochauflösenden Bilddaten von Kameras (gut für die Erkennung kleiner, flacher Hindernisse oder das Lesen von Schildern). Dieser Ansatz schafft ein redundantes und weitaus robusteres Verständnis der Umgebung, was die Sicherheit und Zuverlässigkeit in dynamischen Lagerhallen, in denen Menschen und Maschinen denselben Raum teilen, dramatisch erhöht. Die Evolution der Sensortechnik von einfachen Positionssensoren hin zu komplexer, fusionierter Umfelderkennung ist ein Spiegelbild der Evolution der Lagerautomatisierung selbst – von starren, isolierten Systemen hin zu flexiblen, kollaborativen Ökosystemen.
Ihr globaler Marketing und Business Development Partner
☑️ Unsere Geschäftssprache ist Englisch oder Deutsch
☑️ NEU: Schriftverkehr in Ihrer Landessprache!
Gerne stehe ich Ihnen und mein Team als persönlicher Berater zur Verfügung.
Sie können mit mir Kontakt aufnehmen, indem Sie hier das Kontaktformular ausfüllen oder rufen Sie mich einfach unter +49 89 89 674 804 (München) an. Meine E-Mail Adresse lautet: wolfenstein∂xpert.digital
Ich freue mich auf unser gemeinsames Projekt.